Innovation, resilience key features in process control – company
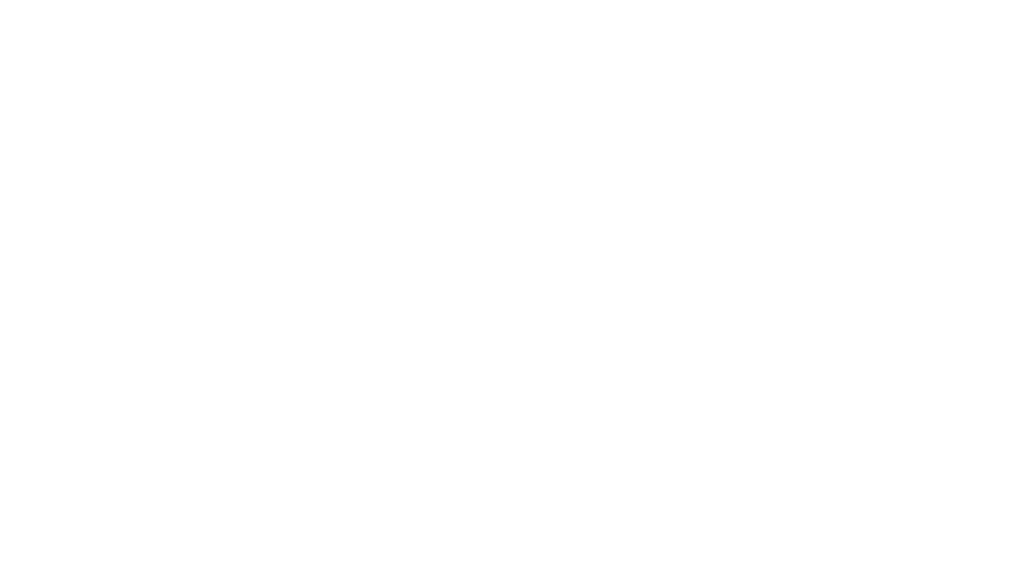
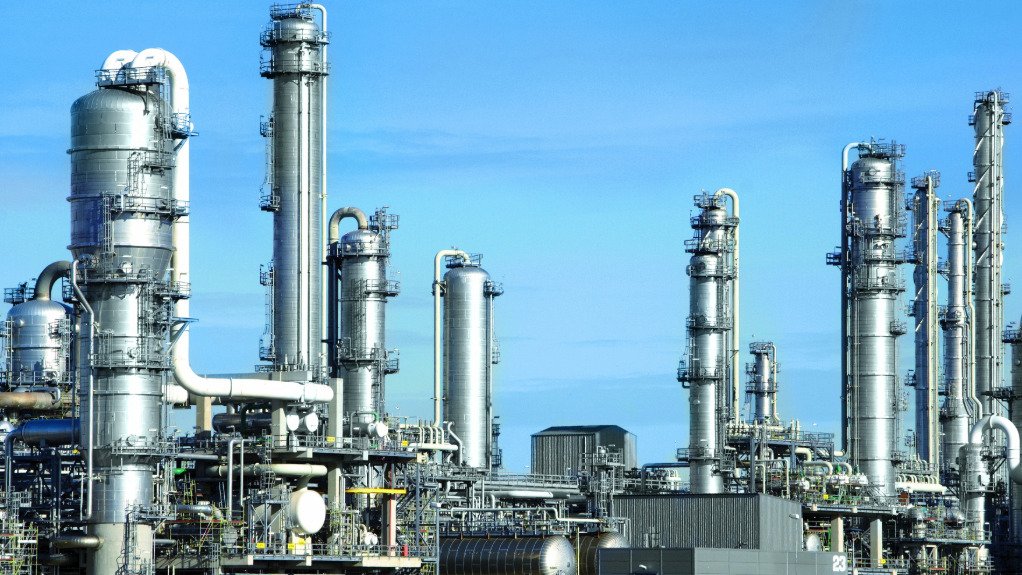
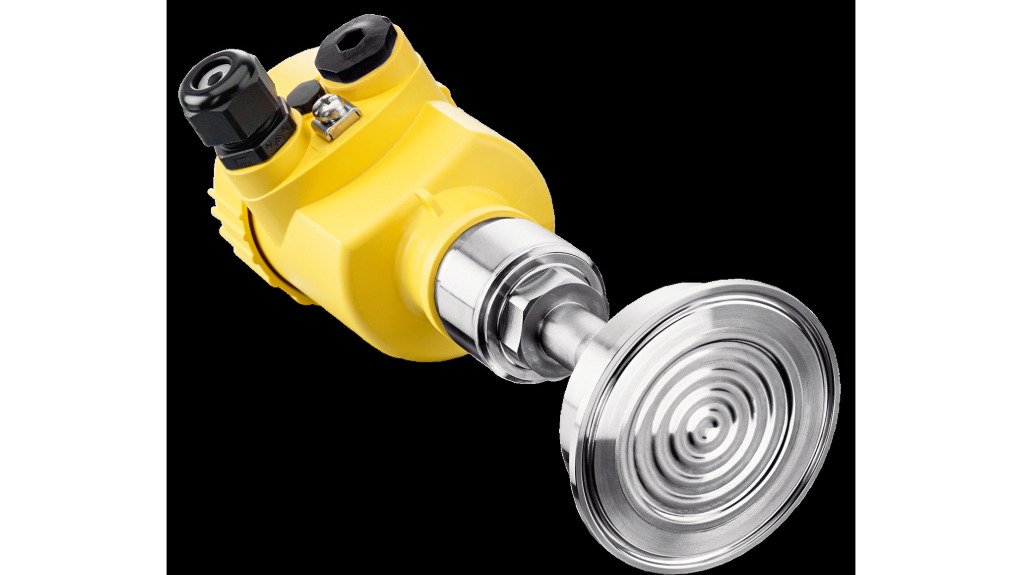
PRODUCT DURABILITY Technology and innovation are at the forefront of Vega's pressure sensors, thereby ensuring maximum efficiency and resilience
EFFICIENCY AND RELIABILITY Vega harnesses technology to improve its pressure sensors for a variety of applications within the chemical industry
Pressure sensors with ceramic CERTEC measuring cells have proven to be the preferred technology in not only the chemicals industry but also in industries where reliability and stability are key features in process control, says German instrumentation and control company Vega technical product specialist Clint Viviers.
Vega places great emphasis on the use of its VEGABAR 82 pressure sensor, with its dry ceramic measuring cell. The cell uses a capacitive measuring principle to accurately measure process pressure relative to atmosphere, absolute pressure and hydrostatic pressure.
Viviers asserts that the VEGABAR 82 ceramic cell has a high chemical resistance to roughly 80% of all chemicals. With process fitting options of stainless steel, polyvinylidene fluoride and various metals, this product can be applied to “almost all” applications in the chemicals industry, with different process seals made of different polymers also available to suit high-demand applications.
“After the birth of ceramic technology, it became apparent that some high-demand applications needed some enhanced features on the VEGABAR 82. Vega did not hesitate to engineer and improve features that allowed for fewer failures, promoting a longer life span,” he adds.
Viviers elaborates, using the example of processes during which there are fast temperature fluctuations. Owing to the expansion coefficients of different materials, including metal body and ceramic cells, pressure drifts occurred within shorter periods.
Accurate and fast temperature compensation, therefore, became a necessity, and a temperature sensor was introduced behind the diaphragm of the ceramic cell.
Consequently, temperature compensation can occur rapidly, while the process temperature can also be measured and separately communicated to the programmable logic controller or distributed control system, the company contends.
Metallic Alternative
Vega highlights that sensors equipped with ceramic measuring cells are a ‘proven’ alternative to metallic diaphragm sensors as they offer high safety, long-term stability and reliability.
The company notes that metallic-based sensors were integral to pressure measurement technology in chemicals processes, as their robust design made them suitable for applications with high-pressures and extreme temperatures. Many different designs and measuring techniques were developed over the years, owing to the diverse process and installation conditions in the chemicals industry.
While the main advantage of metallic sensors is their ability to withstand extreme conditions, their disadvantages include their susceptibility to corrosion, which in turn, leads to the inevitable ageing of the metal. This results in the sensor requiring regular recalibration to maintain accuracy over the long term.
On the other hand, ceramic-engineered pressure sensors are characterised by their corrosion resistance, long-term stability and minimal drift, thereby providing a reliable measurement over a long period.
Ceramic sensors can also be used for pressure measurement in about 60% to 70% of all chemical applications. Further, ceramic measuring cells have a significantly higher overload resistance than metallic cells. Where metal diaphragms deform irreversibly when exposed to very high pressure, a ceramic diaphragm simply deflects, sits against the base body and then returns to its original position.
Additionally, while metallic measuring cells operate with oil as a transmission medium, which can leak into the process in the event of a diaphragm rupture, ceramic measuring cells are completely dry and function similar to a capacitator. Pressure on a ceramic diaphragm causes a minute amount of deflection, which changes a capacitance value. The pressure can then be calculated from the factory-calibrated capacitance value.
Efficiency Underscored
Vega highlights that optimising processes for maximum efficiency can be achieved only by using technology that withstands the challenges in the chemicals manufacturing industry. For this reason, the company notes that level and pressure sensors have been improved to suit high-demand applications.
“Radar level transmitters have been a key success for Vega, where the wetted parts, or process fittings, have been developed to have high chemical resistance . . . To apply the correct sensor to the application, chemical resistance charts have been developed to ensure the selection process is done correctly,” Viviers explains.
Further, overload resistance is a key feature of the ceramic measuring cell. In some applications, the process flow is not always optimised, and high-pressure shocks can be created during pump operation and valve changeovers.
Vega also highlights that the development of product technologies ultimately depends on customer demands.
The motivation driving the introduction of ceramic technology was to improve the pressure sensor market to ensure that end-users have peace of mind and there is less downtime.
Known for developing pressure sensor technology for high- and low-demand applications, Vega prides itself on the improvements in its radar technology and follows the demands of manufacturing processes to increase the life span of critical measuring elements as part of the automation process for all manufacturing companies.
“Vega has been thought of only as a level sensor company, but we understand pressure sensors. Being a market leader in radar level, Vega aims to map the same success for pressure sensors,” Viviers concludes.
Comments
Announcements
What's On
Subscribe to improve your user experience...
Option 1 (equivalent of R125 a month):
Receive a weekly copy of Creamer Media's Engineering News & Mining Weekly magazine
(print copy for those in South Africa and e-magazine for those outside of South Africa)
Receive daily email newsletters
Access to full search results
Access archive of magazine back copies
Access to Projects in Progress
Access to ONE Research Report of your choice in PDF format
Option 2 (equivalent of R375 a month):
All benefits from Option 1
PLUS
Access to Creamer Media's Research Channel Africa for ALL Research Reports, in PDF format, on various industrial and mining sectors
including Electricity; Water; Energy Transition; Hydrogen; Roads, Rail and Ports; Coal; Gold; Platinum; Battery Metals; etc.
Already a subscriber?
Forgotten your password?
Receive weekly copy of Creamer Media's Engineering News & Mining Weekly magazine (print copy for those in South Africa and e-magazine for those outside of South Africa)
➕
Recieve daily email newsletters
➕
Access to full search results
➕
Access archive of magazine back copies
➕
Access to Projects in Progress
➕
Access to ONE Research Report of your choice in PDF format
RESEARCH CHANNEL AFRICA
R4500 (equivalent of R375 a month)
SUBSCRIBEAll benefits from Option 1
➕
Access to Creamer Media's Research Channel Africa for ALL Research Reports on various industrial and mining sectors, in PDF format, including on:
Electricity
➕
Water
➕
Energy Transition
➕
Hydrogen
➕
Roads, Rail and Ports
➕
Coal
➕
Gold
➕
Platinum
➕
Battery Metals
➕
etc.
Receive all benefits from Option 1 or Option 2 delivered to numerous people at your company
➕
Multiple User names and Passwords for simultaneous log-ins
➕
Intranet integration access to all in your organisation