Komatsu centre leveraging data to improve mining equipment performance on-site
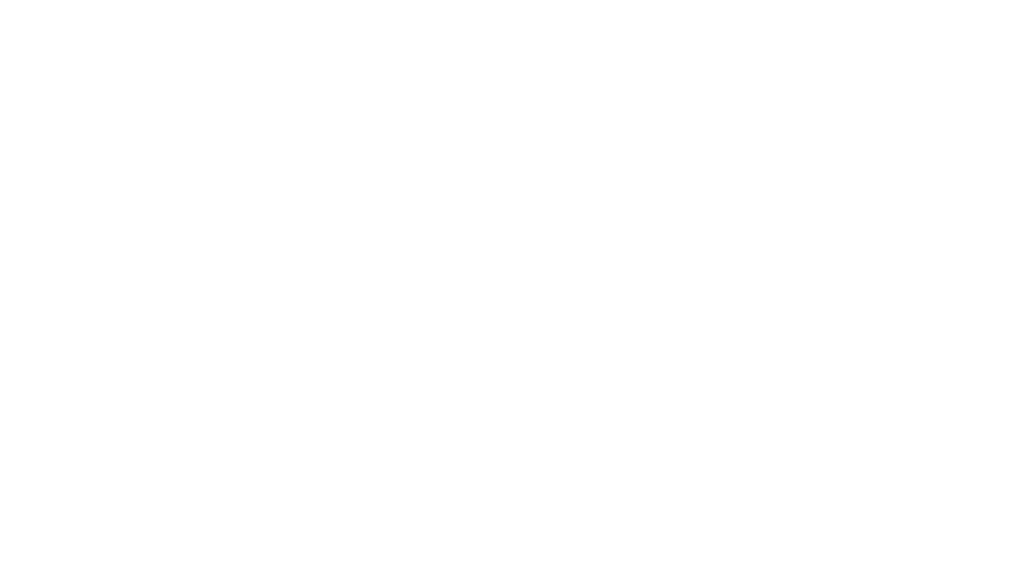
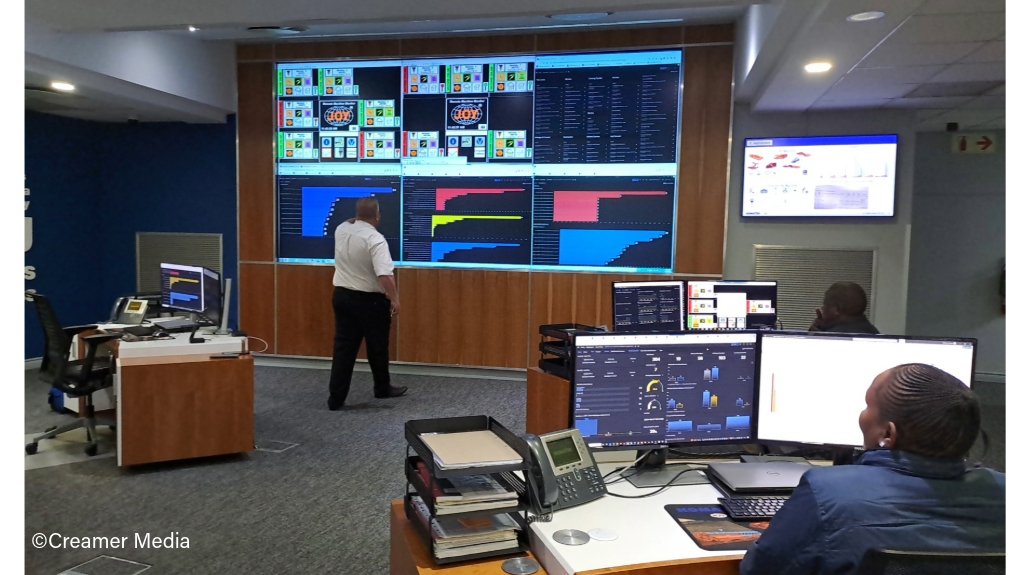
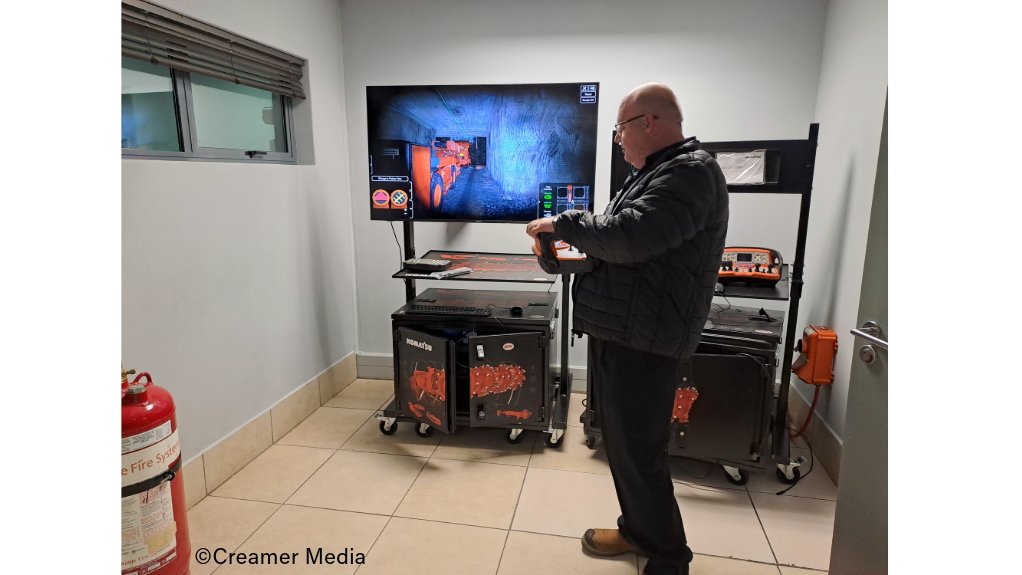
Data monitoring and analysis
Photo by Creamer Media's Tasneem Bulbulia
Training simulator
Photo by Creamer Media's Tasneem Bulbulia
Mining and industrial machinery developer and manufacturer Komatsu’s Smart Services Centre, in eMalahleni, is capitalising on data to assist coal mining companies to optimise productivity, ensure reliable equipment and strive for zero harm at the lowest possible costs, the company says.
Speaking to Engineering News during a recent site visit to the centre, Komatsu Sales and Services manager Leon Papenfus explained that the centre was a centralised hub for Komatsu’s services.
It brought together the company’s old traditional services of field service support and the like, as well as new data-driven services, he pointed out, noting that this was achieved through a trifold approach, namely, equipment data and information, equipment and reliability, and skills development.
EQUIPMENT DATA AND INFORMATION
The centre provides support for coal mining operations in the area. Using data obtained from its sensors on machines at underground operations; it discerns how these are operated, what their performance is and then provides customers with the requisite recommendations for optimisation – with 24/7 support available.
Customers buy original equipment from Komatsu as a baseline capital asset. The customer owns the equipment, but, from a services side, Komatsu looks after it in the field, as well as how to drive that equipment to perform to the utmost.
This is part of the company’s push to move away from the traditional reactive approach of supporting the asset in the field and intervening only when there is a need.
Instead, it is striving to be more proactive, using available technologies.
This would enable reduced downtime or eliminate it completely, so that the asset could continue to produce, the company noted.
To ensure mines are connected and that data can be collected, Komatsu collaborates with customers to implement the requisite infrastructure at the operations – from the onset with greenfield operations, or advising existing customers on technology advancements.
Also, all of Komatsu’s equipment is equipped with smart sensors.
The data that is received from underground mining operations is sent to the company’s cloud facility. Algorithms are used to analyse the data to then provide information to the customer in terms of safety and production.
The centre is currently monitoring about 124 machines, of which 90 are continuous miners, across nine mines, with data gleaned from about 260 sensors. The majority of the mines are from the surrounding area, but the centre also has the capability to monitor further afield, evidenced by it currently assisting customers in Botswana and India.
Papenfus averred that what differentiated Komatsu from its competitors was that it gleaned data, understood it and then actioned it.
“By leveraging data effectively, companies not only improve their current operations, but also innovate and adapt to future challenges. As the landscape of business continues to evolve, the role of data analysis in decision-making will undoubtedly grow, paving the way for new levels of success and discovery,” he said.
Papenfus stated that the company listened to the customer, understood their needs and expectations and used the centre to enhance the customer’s systems to achieve their objectives.
Komatsu is also using the data it obtains to innovate.
One such innovation that it has been testing is its continuous miner assistant programme, which helps operators with the cutting cycle, and functions similarly to cruise control on a vehicle.
This programme reduced the number of inputs required from the operator, in turn reducing fatigue and ensuring greater efficiency, Papenfus pointed out.
Consequently, the operator can instead focus on safety, better control and observing the overall mining process.
This promotes safety, a predictable cutting cycle, even surfaces and efficient cutting shuttle car loading.
This programme forms part of Komatsu’s drive for full automation, which will eventually remove the operator entirely out of the hazardous area.
For the second innovation, Komatsu is using GPS to track machine routes underground, with the data used to determine whether the correct mining sequence is being followed.
Management can use this information to intervene if the correct sequence is not being followed or if the conditions require changes to the pre-determined cutting sequence.
This innovation is currently in the development stage, with Komatsu rolling it out to one of its customers.
EQUIPMENT AND RELIABILITY
To ensure equipment is performing correctly and reliably, the centre undertakes remote health monitoring and has a lab that undertakes condition-based monitoring.
The company makes use of vibration analysis, infrared thermography and oil analysis technologies for condition monitoring.
Oil analysis, a proactive monitoring technology, is done to find out about mechanical wear, find out about contamination in oil and to find out if oil chemistry has changed.
It can effectively forecast the impending failure of mechanical and electrical systems through which the oil flows.
Papenfus explained that this was part of Komatsu’s drive of ensuring the lowest total cost of ownership of the equipment.
SKILL DEVELOPMENT
The centre provides both technical and operational skills development.
As part of its data-centric approach, it has pivoted to now providing a complete digitalised training solution (DTS).
It undertakes a training programme, which analyses a current customer’s benchmark on skills development, and uses data and smart services to pinpoint their specific training needs.
This new strategy moves away from the old, traditional way of lecture-based training.
The first phase of DTS is a confidence evaluation, designed to determine the level of knowledge students currently have on a certain topic.
Phase two is small and medium enterprise-led training, with media used to conduct interactive classes.
Phase three is on-the-job training, which takes place on operator and technical simulators, or a relevant machine.
Phase four is classroom presentation, which entails cross-pollination and experience-sharing to enable complete knowledge retention.
DTS aims to raise team morale without compromising on safety.
Comments
Press Office
Announcements
What's On
Subscribe to improve your user experience...
Option 1 (equivalent of R125 a month):
Receive a weekly copy of Creamer Media's Engineering News & Mining Weekly magazine
(print copy for those in South Africa and e-magazine for those outside of South Africa)
Receive daily email newsletters
Access to full search results
Access archive of magazine back copies
Access to Projects in Progress
Access to ONE Research Report of your choice in PDF format
Option 2 (equivalent of R375 a month):
All benefits from Option 1
PLUS
Access to Creamer Media's Research Channel Africa for ALL Research Reports, in PDF format, on various industrial and mining sectors
including Electricity; Water; Energy Transition; Hydrogen; Roads, Rail and Ports; Coal; Gold; Platinum; Battery Metals; etc.
Already a subscriber?
Forgotten your password?
Receive weekly copy of Creamer Media's Engineering News & Mining Weekly magazine (print copy for those in South Africa and e-magazine for those outside of South Africa)
➕
Recieve daily email newsletters
➕
Access to full search results
➕
Access archive of magazine back copies
➕
Access to Projects in Progress
➕
Access to ONE Research Report of your choice in PDF format
RESEARCH CHANNEL AFRICA
R4500 (equivalent of R375 a month)
SUBSCRIBEAll benefits from Option 1
➕
Access to Creamer Media's Research Channel Africa for ALL Research Reports on various industrial and mining sectors, in PDF format, including on:
Electricity
➕
Water
➕
Energy Transition
➕
Hydrogen
➕
Roads, Rail and Ports
➕
Coal
➕
Gold
➕
Platinum
➕
Battery Metals
➕
etc.
Receive all benefits from Option 1 or Option 2 delivered to numerous people at your company
➕
Multiple User names and Passwords for simultaneous log-ins
➕
Intranet integration access to all in your organisation