Locally manufactured vacuums offer cost-effective solution
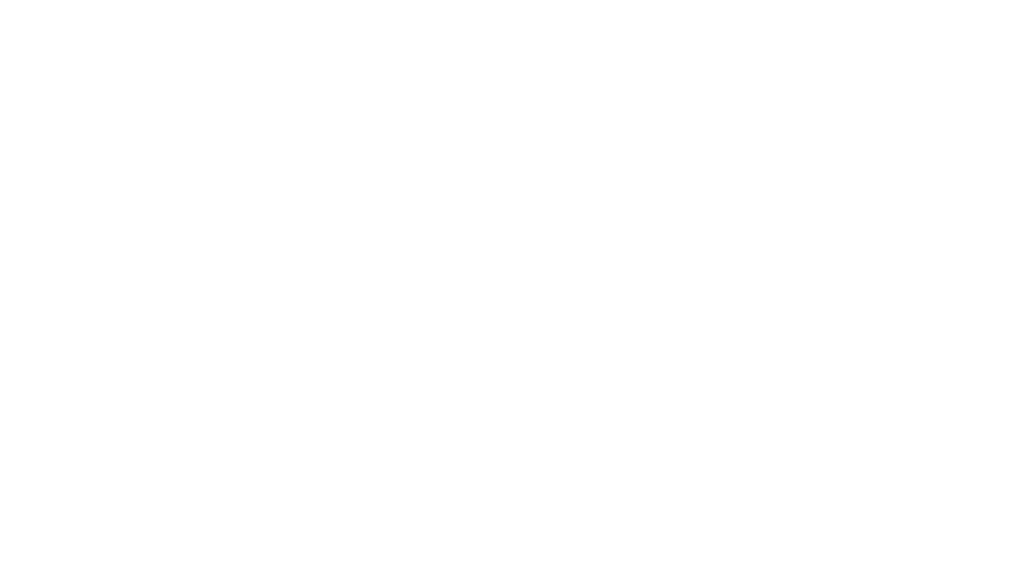
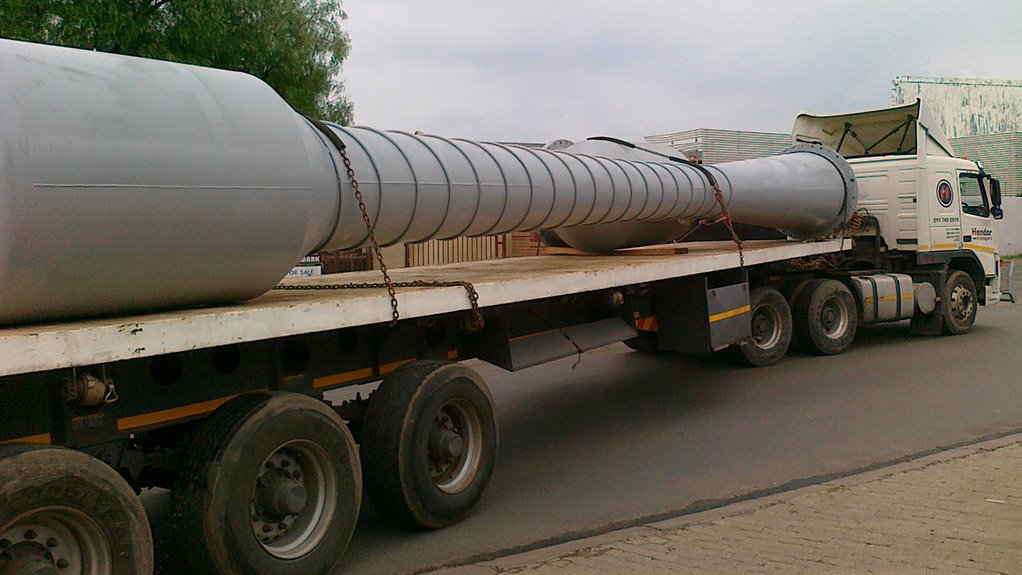
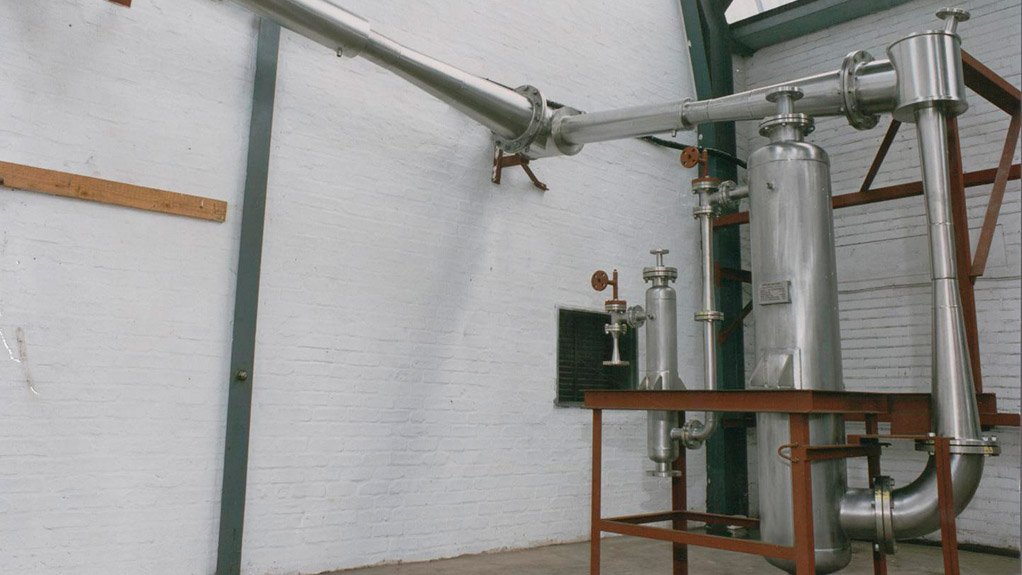
MINIMAL MAINTENANCE REQUIRED Applied Vacuum recently sold spare parts to an edible-oil distillery for the first time since the company bought the ejector 12 years ago
LOCAL CAPABILITIES Applied Vacuum is the only South African manufacturer of steam ejectors
Steam-powered and high-pressure water-powered ejectors do not require maintenance and regular replacement, compared with regular vacuum pumps and, therefore, save clients time and money that could have been lost as downtime, says local vacuums manufacturer Applied Vacuum MD Geoff Levy.
He tells Engineering News that most of the steam ejectors supplied by the company to installations worldwide have been running for more than 20 years.
“The advantage of a steam ejector is that it has no moving parts, so it does not need maintenance,” says Levy, adding, however, that the ejector’s components might need to be replaced over time.
He cites the company’s recent selling of spare parts to a Cape Town-based edible-oil distillery for the first time since the company bought the steam ejector 12 years ago as an example.
Levy adds that Applied Vacuum designs and manufactures the steam ejectors at its factory, in Johannesburg, and parts and complete systems are sent to clients worldwide who require new ejectors or replacement parts.
The company has a staff complement of 13, comprising ten tradesmen working in the factory and three on the engineering side of the business.
Levy says Applied Vacuum is the only company that designs and manufactures steam ejectors in South Africa, thereby enabling the company to offer customised products to customers’ specifications as well as swiftly supplied bespoke replacement parts whenever needed.
How Steam Ejectors Work
Steam ejectors use high-pressure steam to compress low-pressure vapours or gases for pumping purposes. They can be used in various applications, including the evaporation of phosphoric acid, fruit-juice concentration, black liquor and metallurgical applications, the manufacture of sodium hyperchlorite and soap-drying processes, as well as the evaporation of molasses, sweet liquors and syrups.
Steam ejectors can also be used in edible-oil refining processes; for filtration in the refining of precious metals; in the distillation of fatty acids, petrochemicals, lubrication oil, furfural and furfural alcohol and hydrogen peroxide solutions; in the power generation sector for condensing steam turbines; and in air ejection.
“Steam ejectors are effective in environments with highly corrosive vapours and fluids. They are available in any size and can operate safely under the most hazardous conditions,” highlights Levy, adding that they can be fabricated using a variety of materials.
The ejector sets operate in a range of suction pressures down to 0.3 mbar absolute, and carry loads of up to 1 000 kg/h.
High-Pressure Water Vacuum
Levy tells Engineering News that Applied Vacuum is testing a newly designed and manufactured high-pressure water-powered vacuum system, in collaboration with KwaZulu-Natal-based vacuum pumps company Pumpsmith.
“As with the steam ejector, the main difference between this vacuum system and the traditional vacuum pump is in the maintenance. Maintaining vacuum pumps is very expensive and we have found that maintaining a recirculation pump is cheaper. We, therefore, opted to use them instead,” he says.
About Applied Vacuum
Applied Vacuum has agents in Europe, Australia, Israel, Indonesia, Central America and Pakistan, through which it has sold its South Africa-manufactured steam ejectors. The company’s services include the design, fabricating and commissioning multistage ejector sets. It also designs replacement parts for these products to meet clients’ specifications.
The company’s multistage ejector sets are fabricated in carbon steel, stainless steel, titanium, polytetrafluoroethylene and carbon. Its fabrication workshop is a 4 000 m2 floor space with a 5 m column and boom submerged arc welding system; two 5 t welding manipulators; a 10 t overhead crane; three welding turntables; ten conventional centre lathes; three computer numerical control (CNC) lathes; five conventional milling machines; two CNC milling machines; six metal inert welding machines; five tungsten inert welding machines and six shielded metal arc welding machines.
Comments
Press Office
Announcements
What's On
Subscribe to improve your user experience...
Option 1 (equivalent of R125 a month):
Receive a weekly copy of Creamer Media's Engineering News & Mining Weekly magazine
(print copy for those in South Africa and e-magazine for those outside of South Africa)
Receive daily email newsletters
Access to full search results
Access archive of magazine back copies
Access to Projects in Progress
Access to ONE Research Report of your choice in PDF format
Option 2 (equivalent of R375 a month):
All benefits from Option 1
PLUS
Access to Creamer Media's Research Channel Africa for ALL Research Reports, in PDF format, on various industrial and mining sectors
including Electricity; Water; Energy Transition; Hydrogen; Roads, Rail and Ports; Coal; Gold; Platinum; Battery Metals; etc.
Already a subscriber?
Forgotten your password?
Receive weekly copy of Creamer Media's Engineering News & Mining Weekly magazine (print copy for those in South Africa and e-magazine for those outside of South Africa)
➕
Recieve daily email newsletters
➕
Access to full search results
➕
Access archive of magazine back copies
➕
Access to Projects in Progress
➕
Access to ONE Research Report of your choice in PDF format
RESEARCH CHANNEL AFRICA
R4500 (equivalent of R375 a month)
SUBSCRIBEAll benefits from Option 1
➕
Access to Creamer Media's Research Channel Africa for ALL Research Reports on various industrial and mining sectors, in PDF format, including on:
Electricity
➕
Water
➕
Energy Transition
➕
Hydrogen
➕
Roads, Rail and Ports
➕
Coal
➕
Gold
➕
Platinum
➕
Battery Metals
➕
etc.
Receive all benefits from Option 1 or Option 2 delivered to numerous people at your company
➕
Multiple User names and Passwords for simultaneous log-ins
➕
Intranet integration access to all in your organisation