Manufacturer installs ultrafiltration technology, significantly improves quality of wastewater
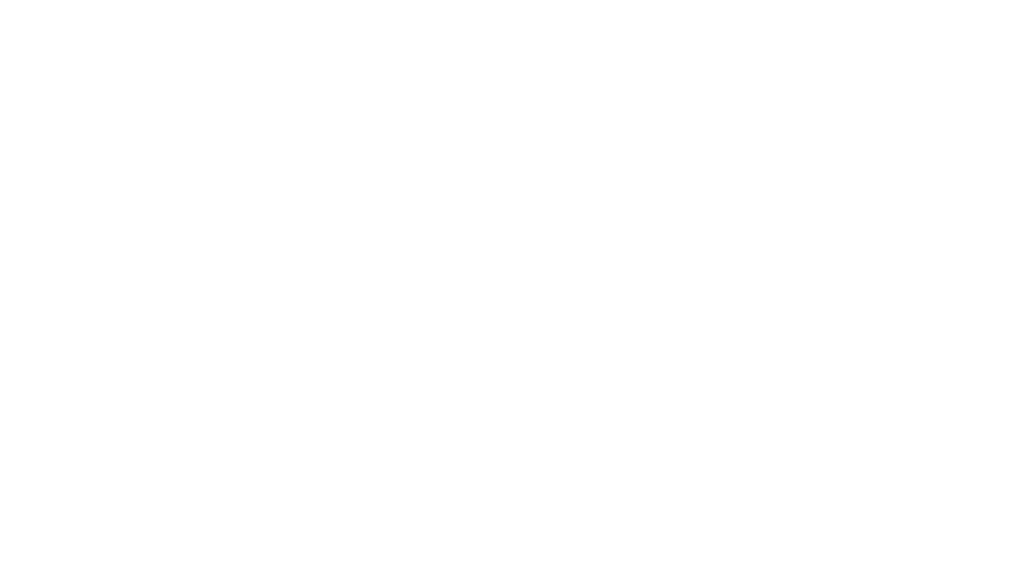
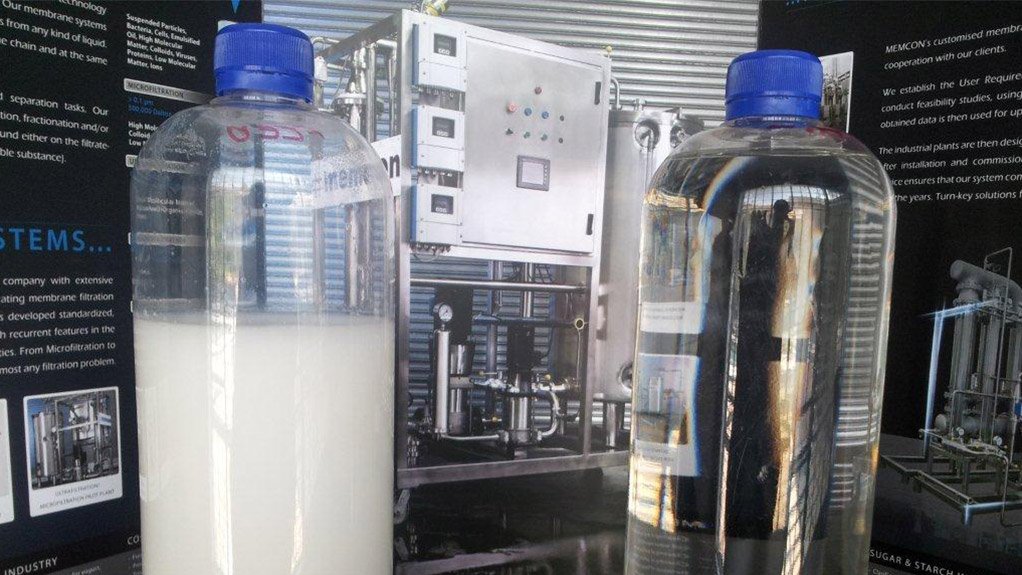
Henkel adhesives technologies operations GM Manie Botha speaks about the company’s newly-installed ultrafiltration plant. Camerawork: Nicholas Boyd. Editing: Shane Williams.
BETTER THAN MUNICIPAL STANDARDS Installed by membrane filtration technology specialist Memcon, Henkel SA’s new R2-million effluent plant has significantly improved the effluent water’s chemical composition
Adhesive technologies specialist and product manufacturer Henkel South Africa has set a benchmark in sustainability for the global Henkel brand by replacing its old chemical treatment plant with a new R2-million effluent plant that uses ultrafiltration technology in ceramic filters to treat the liquid waste from its factory.
The company’s adhesives technologies operations GM Manie Botha tells Engineering News that Henkel South Africa’s factory produces about 1 000 kℓ of wastewater every month – effluent which used to be chemically treated before it was released into the sewerage system.
Therefore, when Henkel’s previous effluent plant reached a 15-year milestone in 2011, the company decided to re-engineer its effluent process and replace the old technology with an environment-friendly option.
The ultrafiltration technology, often used in the mining industry, uses ceramic filters with microsized pores that allow for filtration.
Having had previous experience with ceramic filter technology, Botha believed it would work for the company and approached membrane filtration technology specialist Memcon to partner with Henkel for the possible installation of a new effluent plant.
“After 18 months of trials, we registered impressive results and decided to install an ultrafiltration plant, which was fully operational by March,” says Botha. It took four months to install and commission the plant, with Memcon on site for the duration of the project to ensure that the process ran smoothly.
The new plant, which is more compact than the previous one and features 54 ceramic filters, contained in two steel modules, has significantly improved the effluent water’s chemical composition, which is currently up to 1 000 times better than the municipality’s standard for treated effluent.
“The plant also functions automatically, eliminating the need for maintenance and human involvement,” says Botha, explaining that the plant runs the cleaning cycles with a programmable logic controller (PLC), which ultimately adds to the cost benefits of the plant.
He adds that Henkel’s maintenance department has ownership of the plant and will monitor the PLC logs to ensure that everything runs accordingly.
Further, as it is encased in stainless steel, Henkel’s new effluent plant has an indefinite life span, though the filters last a minimum of five years, after which they need to be replaced.
“Moreover, having cost R2-million to manu- facture and install, the new effluent plant allows for a two-and-a-half-year payback period, which is unattainable in some projects. It’s a good deal,” says Botha, adding that, at first, Henkel employees were hesitant to employ the new technology, as applying ultrafiltration technology to a manufacturing facility’s effluent plant is perceived by some to be too costly.
“We had to get everybody to understand that this technology would do the job, and since there was no precedent for an effluent plant technology like this in a manufacturing environment, we did take a risk in deciding to implement it,” he adds.
Meanwhile, one of the primary benefits of Henkel’s new environment-friendly effluent plant is that it helped the company reach its global 2030 sustainability target for waste in less than a year.
“All of the sustainability strategies that we’ve rolled out in the last 12 months are aimed at reducing our use of resources by at least 30%, compared with Henkel’s 2012 results. This includes the reduction of water and energy use,” explains Botha.
Henkel’s global sustainability strategy is based on the philosophy of achieving more with less, thereby creating more value for the company, consumers, customers and communities while reducing its ecological footprint.
Meanwhile, the company’s long-term plans are to become a zero-effluent plant, with plans already under way to attach a reverse-osmosis (RO) plant to the back end of the new effluent plant to recycle the company’s wastewater for use in the manufacturing process.
Once Henkel installs the RO plant, the water used in the manufacturing process will be 100% recycled and the company’s environmental footprint for waste will be minimal, says Botha.
He further points out that the new plant also subscribes to the company’s value for innovation.
He concedes that it was a significant risk for Henkel South Africa to apply the new technology but maintains that, without risk, there can be no innovation.
“Innovation requires a paradigm shift and it is refreshing to work for a company that embraces new ideas. We have been using the ceramic filters for three months and can definitely say that the results are already exceeding our expectations,” he says.
Comments
Press Office
Announcements
What's On
Subscribe to improve your user experience...
Option 1 (equivalent of R125 a month):
Receive a weekly copy of Creamer Media's Engineering News & Mining Weekly magazine
(print copy for those in South Africa and e-magazine for those outside of South Africa)
Receive daily email newsletters
Access to full search results
Access archive of magazine back copies
Access to Projects in Progress
Access to ONE Research Report of your choice in PDF format
Option 2 (equivalent of R375 a month):
All benefits from Option 1
PLUS
Access to Creamer Media's Research Channel Africa for ALL Research Reports, in PDF format, on various industrial and mining sectors
including Electricity; Water; Energy Transition; Hydrogen; Roads, Rail and Ports; Coal; Gold; Platinum; Battery Metals; etc.
Already a subscriber?
Forgotten your password?
Receive weekly copy of Creamer Media's Engineering News & Mining Weekly magazine (print copy for those in South Africa and e-magazine for those outside of South Africa)
➕
Recieve daily email newsletters
➕
Access to full search results
➕
Access archive of magazine back copies
➕
Access to Projects in Progress
➕
Access to ONE Research Report of your choice in PDF format
RESEARCH CHANNEL AFRICA
R4500 (equivalent of R375 a month)
SUBSCRIBEAll benefits from Option 1
➕
Access to Creamer Media's Research Channel Africa for ALL Research Reports on various industrial and mining sectors, in PDF format, including on:
Electricity
➕
Water
➕
Energy Transition
➕
Hydrogen
➕
Roads, Rail and Ports
➕
Coal
➕
Gold
➕
Platinum
➕
Battery Metals
➕
etc.
Receive all benefits from Option 1 or Option 2 delivered to numerous people at your company
➕
Multiple User names and Passwords for simultaneous log-ins
➕
Intranet integration access to all in your organisation