Manufacturer offers solutions for energy efficiency
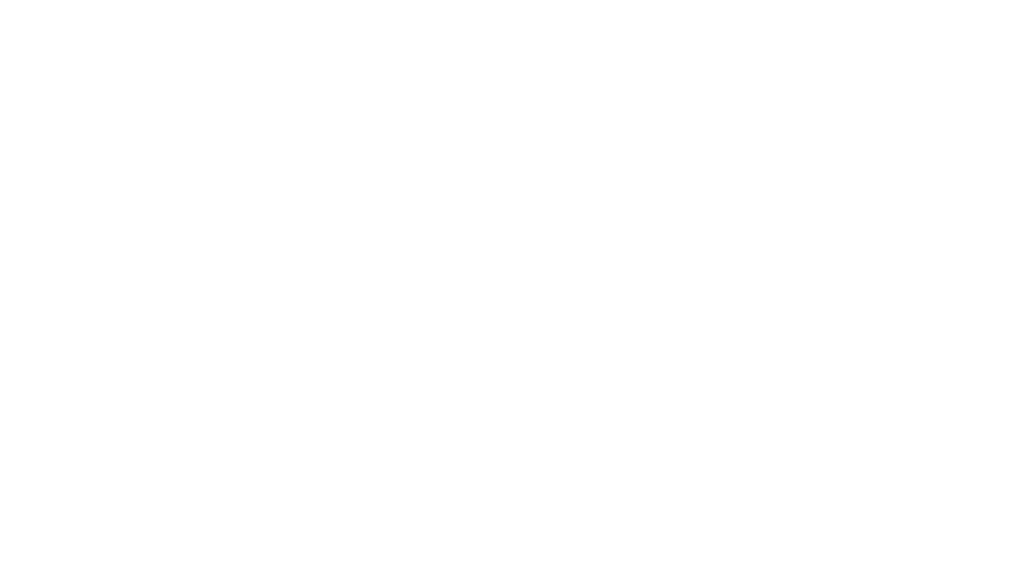
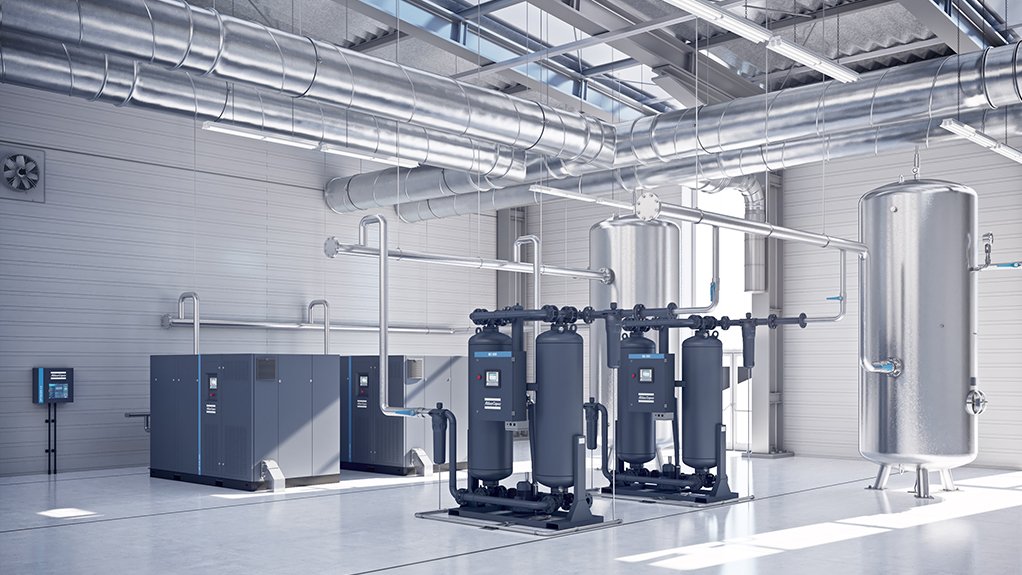
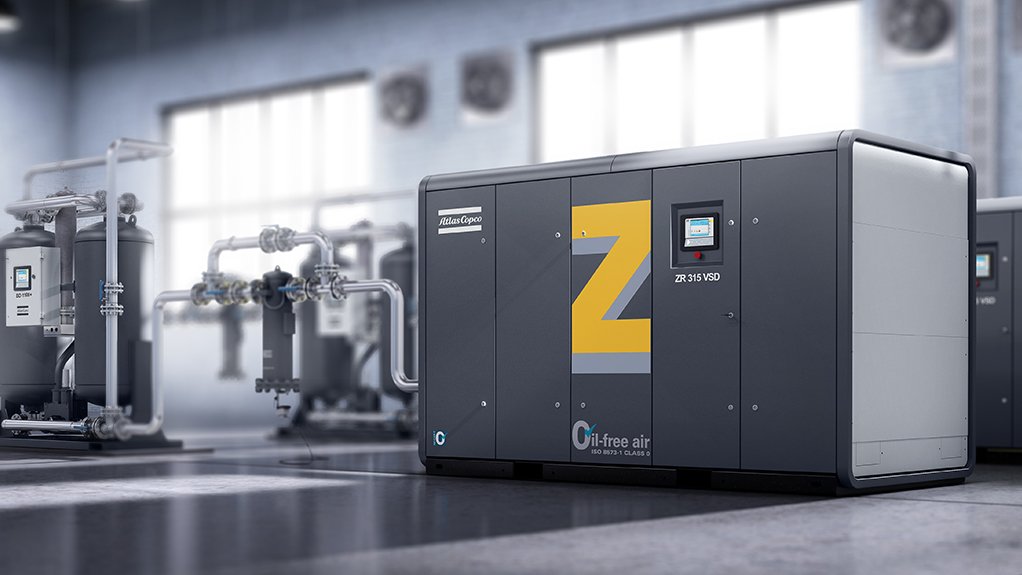
ELECTRIC ENERGY Electricity is the most prevalent energy source for industrial compressed-air production and accounts for up to 80% of the life-cycle cost of a compressor
GREAT RETURN Atlas Copco offers a range of products and technologies that offer customers a great return on investment through cost savings in energy
With a concentrated effort and focus on improving energy efficiency, industrial equipment manufacturer Atlas Copco offers a variety of compressed-air solutions.
“Electricity is the most prevalent energy source for industrial compressed-air production and accounts for up to 80% of the life-cycle cost of a compressor, with the remainder of the cost shared between initial investment and maintenance costs,” highlights Atlas Copco business line manager Wayne Jacobs.
Moreover, the generation of compressed air can account for more than 40% of a plant’s total electricity bill.
Owing to pressure drops, air leaks, loss of heat energy and its inefficient use, besides others, compressed air has been one of the least efficient forms of energy.
“Our offering ranges from compressed-air audits using our AIRScan audit service, control systems using central controls and equipment technology, such as variable-speed drive (VSD) technology, to energy recycling with the Atlas Copco Energy Recovery control unit and data monitoring using smart link.”
Owing to the use of a superior screw element and a high efficiency motor, customers can reduce the life-cycle costs of the plant as the superior screw element provides the optimum combination of maximum free air delivery and low energy consumption, while the high efficiency motors use less electricity, run cooler, and often last longer. This together with Atlas Copco’s VSD technology reduces energy costs by 35% on average.
The technology closely follows the air demand from the compressor by automatically adjusting the motor speed, consequently resulting in VSDs running only at the required speed. The life-cycle cost of a compressor can be reduced by an average of 22%, says Jacobs.
Lowered system pressure using VSD technology also reduces energy use across production significantly – which is why adjusting the motor speed is important as the air demand fluctuates in almost every production environment.
Another solution that Atlas Copco offers is energy reuse. Jacobs explains that air compression generates a lot of heat and, thus by recovering the heat, the company can use it to create thermal energy, which has been a proven method to improve plants’ overall energy efficiency.
Atlas Copco’s energy recovery solution allows for thermal energy to be reused in other industrial processes that require heat or steam.
“The solution lowers a plant’s overall energy consumption and enables the user to save costs while reducing the environmental impact. A staggering 94% of the energy that an air compressor uses, is converted into heat.”
Jacobs notes that without the Atlas Copco Energy Recovery system, costly thermal energy vanishes into the atmosphere through the cooling system and radiation.
He adds that the actual savings then depends on the compressor installation, air system and waste heat applications.
Meanwhile, the AIRScan is a comprehensive audit of the entire compressed air installation, including its energy input, air flow demand, system pressure, air quality, and pressure drops over a period.
The software offers users the opportunity to reduce the energy consumption of the compressor by identifying tangible measures that result in energy savings of between 25% and 30%.
“Our unique audit software can simulate various configurations of a compressed-air installation, enabling us to provide realistic projections on potential energy savings, as well as environmental and financial benefits.”
Further, a new device of Atlas Copco, called the Optimiser 4.0, optimises the operation of the compressed air and blower system while set pressure and flow are being met.
It increases energy savings and assists in keeping the units in a good operating condition, with a proactive approach to maintenance through online monitoring, adds Jacobs. The central controller of the device is ready for Industry 4.0.
The optimizer is a state of the art module, boasting latest electronic design with a smart algorithm controlling users’ compressed air equipment. “It is like having a permanent operator in your compressor room,” he remarks.
“The Optimizer 4.0 not only ensures efficiency and reliability of your compressed air network, but with its advanced connectivity options it captures and records all information enabling the client to analyse the data and to make smart decisions – data available on your fingertips – any time, anywhere.”
Monitoring a compressed-air installation enables users to have remote insight into the air system, and “to detect problems, identify potential improvements and even follow up on actual savings”.
Investing in the latest generation of equipment ensures that customers have the most effective and reliable technology, he adds.
“With new technology comes various savings, and lower energy use and maintenance costs due to extended maintenance intervals, connectivity and monitoring. Customers benefit from not only the return on investment over a short period but also the continuous savings going forward,” Jacobs concludes.
Comments
Press Office
Announcements
What's On
Subscribe to improve your user experience...
Option 1 (equivalent of R125 a month):
Receive a weekly copy of Creamer Media's Engineering News & Mining Weekly magazine
(print copy for those in South Africa and e-magazine for those outside of South Africa)
Receive daily email newsletters
Access to full search results
Access archive of magazine back copies
Access to Projects in Progress
Access to ONE Research Report of your choice in PDF format
Option 2 (equivalent of R375 a month):
All benefits from Option 1
PLUS
Access to Creamer Media's Research Channel Africa for ALL Research Reports, in PDF format, on various industrial and mining sectors
including Electricity; Water; Energy Transition; Hydrogen; Roads, Rail and Ports; Coal; Gold; Platinum; Battery Metals; etc.
Already a subscriber?
Forgotten your password?
Receive weekly copy of Creamer Media's Engineering News & Mining Weekly magazine (print copy for those in South Africa and e-magazine for those outside of South Africa)
➕
Recieve daily email newsletters
➕
Access to full search results
➕
Access archive of magazine back copies
➕
Access to Projects in Progress
➕
Access to ONE Research Report of your choice in PDF format
RESEARCH CHANNEL AFRICA
R4500 (equivalent of R375 a month)
SUBSCRIBEAll benefits from Option 1
➕
Access to Creamer Media's Research Channel Africa for ALL Research Reports on various industrial and mining sectors, in PDF format, including on:
Electricity
➕
Water
➕
Energy Transition
➕
Hydrogen
➕
Roads, Rail and Ports
➕
Coal
➕
Gold
➕
Platinum
➕
Battery Metals
➕
etc.
Receive all benefits from Option 1 or Option 2 delivered to numerous people at your company
➕
Multiple User names and Passwords for simultaneous log-ins
➕
Intranet integration access to all in your organisation