Medupi units 1 to 3 at full load, Eskom to bring damaged unit 4 online in August 2024
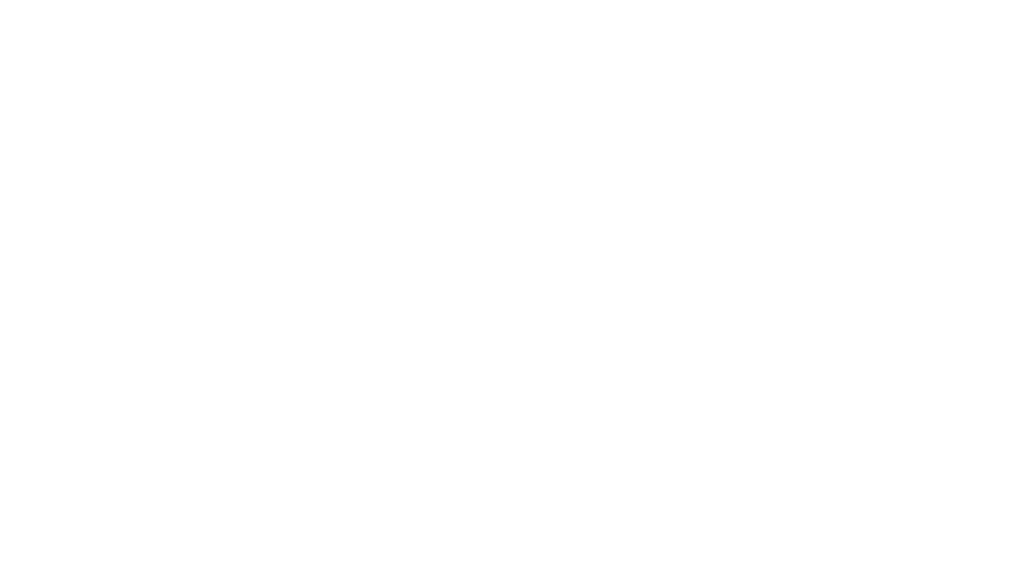
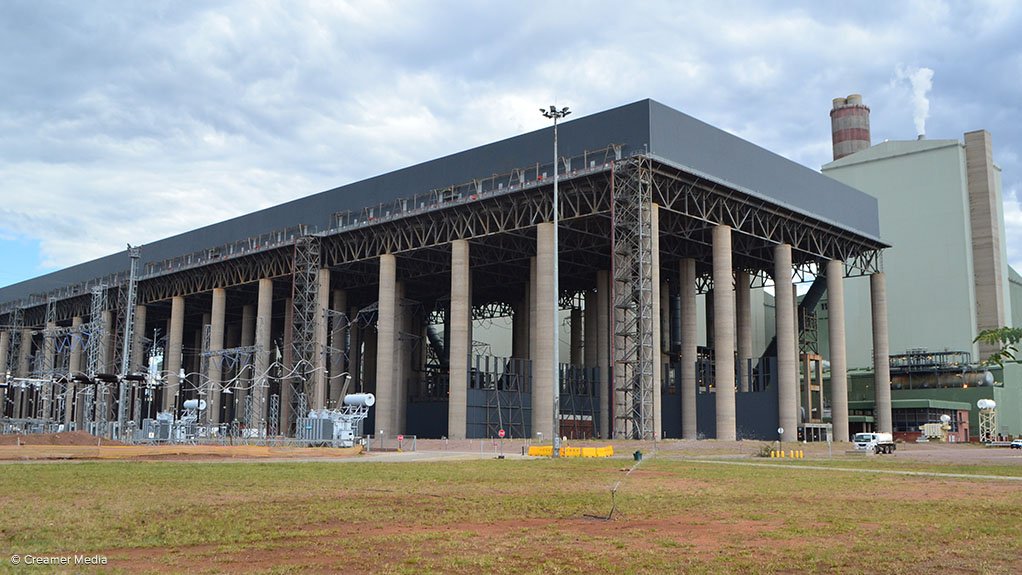
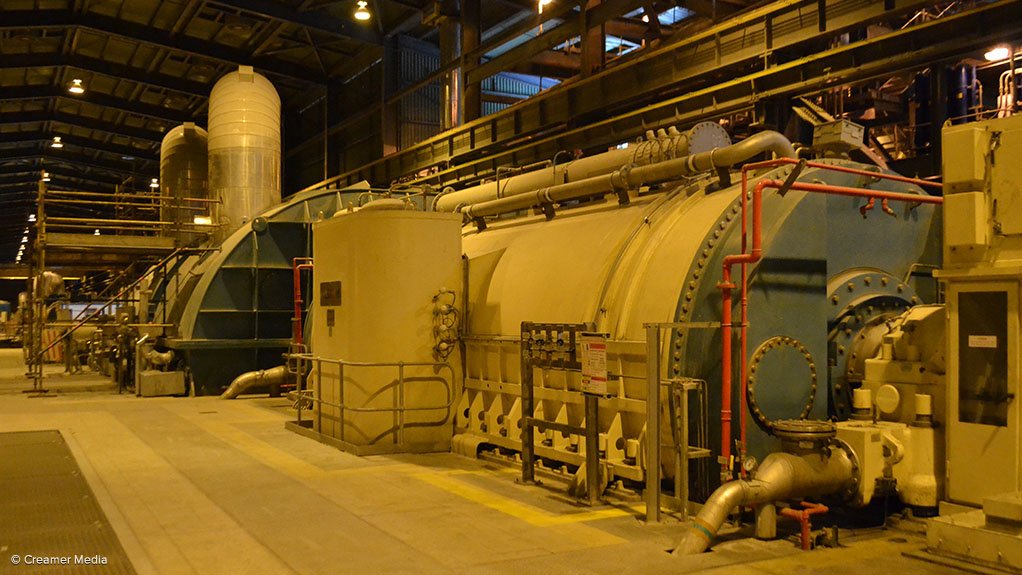
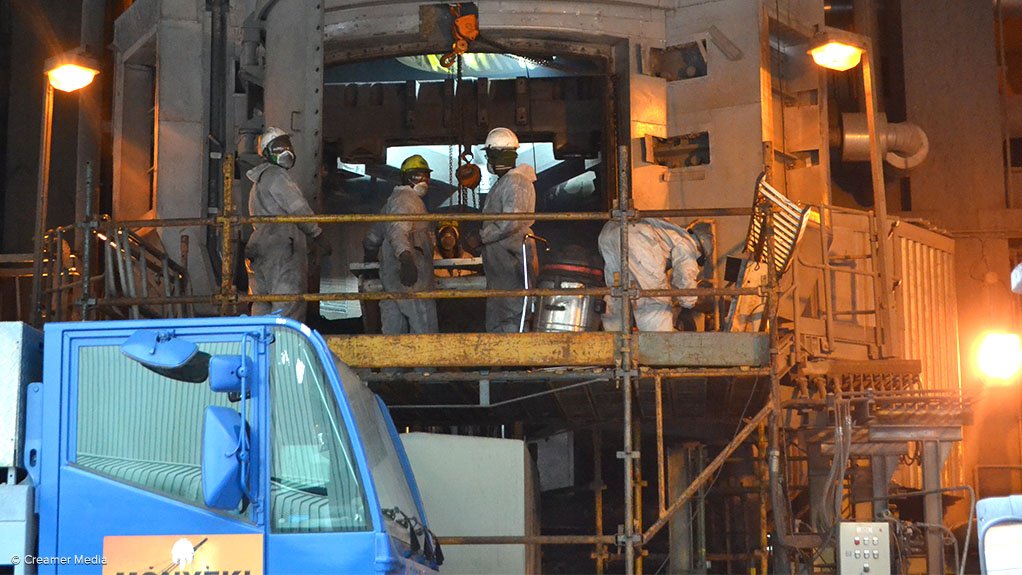
The Medupi power station
Photo by Creamer Media's Schalk Burger
Medupi Unit 3
Photo by Creamer Media's Schalk Burger
Mill work at Medupi
Photo by Creamer Media's Schalk Burger
State-owned power utility Eskom this week revealed that it had implemented repairs and fixes to generation units 1 to 3 at the Medupi power station, and that the units are operating at full load, producing 720 MW of electricity each.
Unit 4, which was damaged in a generator explosion, after hydrogen (used to cool the shaft) mixed with air instead of carbon dioxide during a purging process, will be brought online in August 2024.
Eskom would implement fixes to design flaws as it undertakes repairs of the unit, the utility said during a media site visit on May 19.
Meanwhile, units 5 and 6 at the power station are operating at partial loads to ensure they meet emissions licence requirements.
Eskom would implement fixes and repairs to these units during routine maintenance shutdowns in future to bring them to full load.
Medupi acting power station manager Zweli Witbooi said the company had experienced challenges in relation to equipment not performing to design specifications, including boiler tubes, boiler air and gas ducting, the pulse jet fabric filter plants, the gas air heaters and the reheater spray.
The company was working with original-equipment manufacturers to fix the defects that were contributing to the plant having much lower availability than the targeted 92% availability, he said.
However, over the past year, the Medupi team has maintained units 1 to 3 above 85% availability, with Unit 1 exceeding the objective 92% availability and Unit 6 achieving 74.6% availability.
The key issues with the boiler plants include that the reheater spray flows exceed the boiler contractual requirements owing to poor evaporator heat absorbance, which results in a high furnace exit gas temperature.
"We have issues with high-temperature gas from a design perspective, which contributes to trips. The automatic protection control system shuts down the system when encountering temperatures outside parameters, which causes unavailability and is a serious problem," Witbooi explained.
To counteract this, Eskom reduced the number of tubes in reheater one from 13 tubes per layer to 12 and in reheater two by three layers.
"This solution was implemented on two units. However, the solution worked only to a limited extent under steady-state conditions. When the units are under load, but under low-load and transient conditions, the solution remains problematic," he said.
A basic design to solve the challenges under low-load and transient conditions had been completed and implementation was expected to be done between June 2023 and December 2024, depending on outage availability, said Witbooi.
Further, the milling plants do not meet Eskom’s performance, availability or maintenance duration requirements, and issues with a number of components have been identified.
"We will upgrade the equipment with a new design dam ring and throat, vulcanised feeder rollers, differential pressure measurements, upgraded scrapers, stationary plenum cowls, mill reject box valves, loading system ball carrier, enlarged reject box grid, duplex hydraulic filter housing and split labyrinth seals," he said.
All five generating units, barring the damaged Unit 4, will have their mills upgraded this year, starting in May, with the final Unit 6 mill expected to return to service in September.
Additionally, the pulse jet fabric filter plant does not meet the Eskom performance, maintenance or bag life requirements, largely owing to the pulsing system and flue gas flow entry.
The high-temperature bags should have 28 000 operating hours, or 42 months, at the contracted availability of 92%, but instead last only 12 months currently.
The pressure of the flue gas from the boiler is too high and the fabric filter plant is not performing according to specifications, said Witbooi.
The solution was to redirect the flow into the fabric filter plant from a side inlet. In typical pulse jet fabric filter plants, the airflow must approach from the bottom, which was not the case at the Medupi filter plants. The solution has been implemented and is providing benefits, but the engineering team wants to improve the performance further, he noted.
Further, the gas air heater does not meet Eskom requirements in terms of the temperature gradient, erosion, fouling and ash carryover to the clean air side.
To solve these challenges, the company installed seal strips and split-pin racks on the gas air heaters. This provided an adequate seal between the flue gas and the clean air. The company also installed wear protection and new measuring ports to understand fully what the gas flows were and what the conditions within the gas air heaters were, said Witbooi.
"We also had numerous areas in the primary air, secondary air and burner ducting that experienced excessive erosion due to ash entrainment, as well as erosion within the flue gas ducting due to ineffective erosion protection. We have implemented various protection measures to overcome this. We are making progress in repairing the defects on the boilers," he said.
The costs to repair defects are estimated at R300-million a unit. The estimates to repair the damaged Unit 4 is R2.5-billion.
Meanwhile, Eskom suspended nine employees, four at senior level and five at managerial level, for the incident and explosion that damaged Unit 4. The incident seems to indicate procedural non-compliance and management failures including in terms of oversight and supervision, the utility said.
It concluded its investigations and was undertaking disciplinary actions on the grounds of neglect or omission or acting in such a manner that an asset or plant was harmed. The disciplinary actions were expected to be concluded by the end of May, said Witbooi.
Comments
Press Office
Announcements
What's On
Subscribe to improve your user experience...
Option 1 (equivalent of R125 a month):
Receive a weekly copy of Creamer Media's Engineering News & Mining Weekly magazine
(print copy for those in South Africa and e-magazine for those outside of South Africa)
Receive daily email newsletters
Access to full search results
Access archive of magazine back copies
Access to Projects in Progress
Access to ONE Research Report of your choice in PDF format
Option 2 (equivalent of R375 a month):
All benefits from Option 1
PLUS
Access to Creamer Media's Research Channel Africa for ALL Research Reports, in PDF format, on various industrial and mining sectors
including Electricity; Water; Energy Transition; Hydrogen; Roads, Rail and Ports; Coal; Gold; Platinum; Battery Metals; etc.
Already a subscriber?
Forgotten your password?
Receive weekly copy of Creamer Media's Engineering News & Mining Weekly magazine (print copy for those in South Africa and e-magazine for those outside of South Africa)
➕
Recieve daily email newsletters
➕
Access to full search results
➕
Access archive of magazine back copies
➕
Access to Projects in Progress
➕
Access to ONE Research Report of your choice in PDF format
RESEARCH CHANNEL AFRICA
R4500 (equivalent of R375 a month)
SUBSCRIBEAll benefits from Option 1
➕
Access to Creamer Media's Research Channel Africa for ALL Research Reports on various industrial and mining sectors, in PDF format, including on:
Electricity
➕
Water
➕
Energy Transition
➕
Hydrogen
➕
Roads, Rail and Ports
➕
Coal
➕
Gold
➕
Platinum
➕
Battery Metals
➕
etc.
Receive all benefits from Option 1 or Option 2 delivered to numerous people at your company
➕
Multiple User names and Passwords for simultaneous log-ins
➕
Intranet integration access to all in your organisation