Metso Megaliner improves safety, reduces downtime
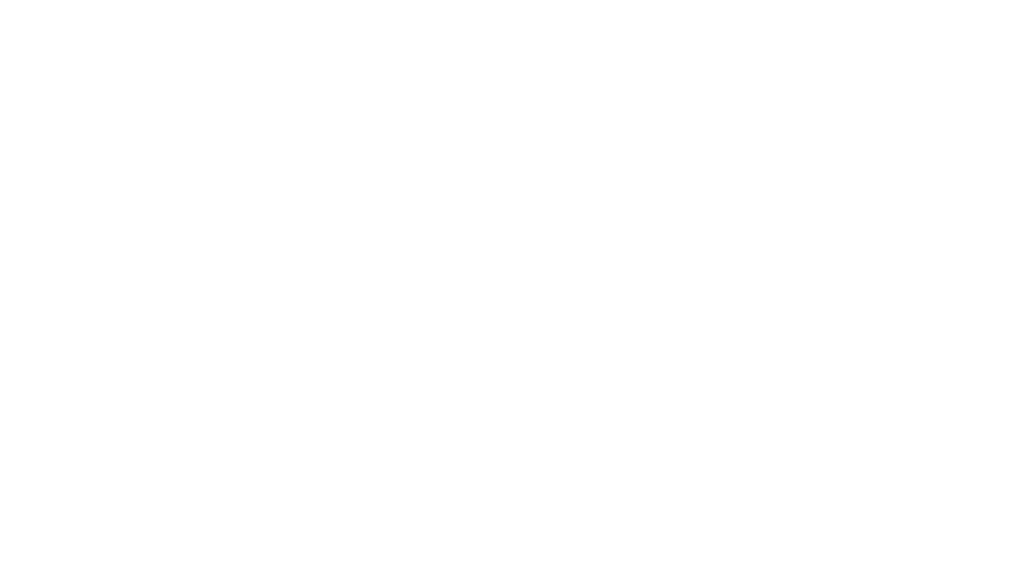
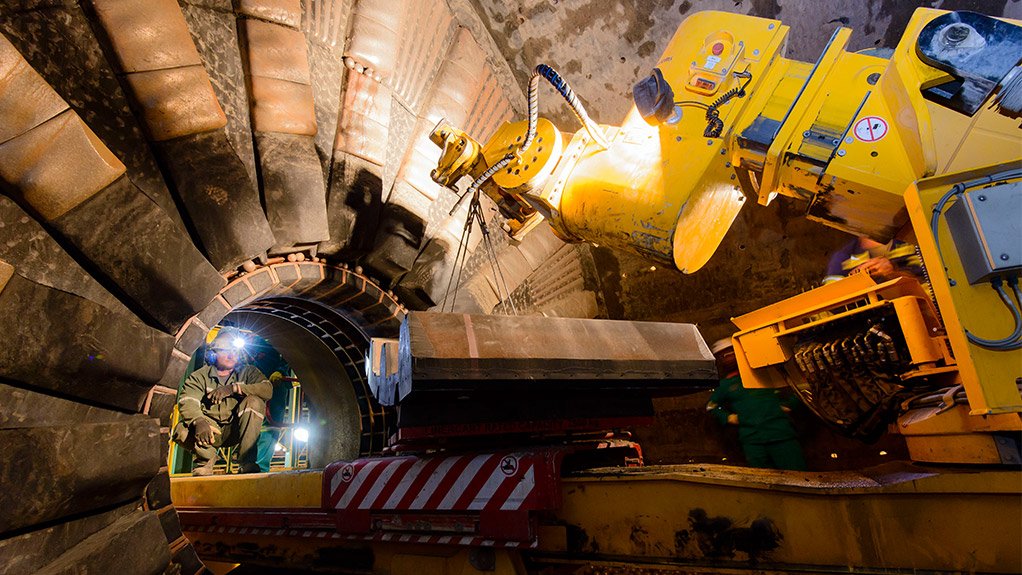
FAST AND EFFECTIVE Megaliner uses fewer and larger parts improving safety, with faster installations
Global industrial equipment and services offering company Metso has proven that its Megaliner mill lining system can result in a drastic reduction in downtime and improved safety in mining operations.
The Megaliner was developed by Metso in 2012 and expanded in 2013 to include a liner positioning system to reduce the inevitable downtime that occurs during liner replacement. The system also provides a significant improvement in operator safety, notes Metso mill lining support specialist Marcel Bode.
The conventional practice of replacing a liner involves installing many pieces using bolts that need to be inserted from the inside of the mill, which is a time- consuming process that has been identified as a potentially hazardous work for the liner replacement crew.
The Megaliner design, however, uses fewer and larger parts and has a ‘unique’ attachment system, improving safety, with faster installations. The parts are also designed for easy replacement. The bolts used to attach the liners used in the Megaliner concept are secured from the outside of the mill, eliminating the risk of having people in the danger zone inside the mill.
Bode further explains that the liner handler operator can put the liners in place without assistance from other workers while the liner positioning system provides remote guidance using cameras for the operator during the process.
“The large mills of today have changed the game. It is the new bigger mills that enable ten to fifteen times higher production. This reduces the significant loss in production caused by downtime,” says Metso key account manager David Maritz.
Metso’s Megaliner is designed with this in mind, he notes, adding that one Megaliner combines several lifter bars and plates into one component.
Maritz says many mines in South Africa are becoming more aware about mill availability and safe installations and are, therefore, interested in using Metso’s innovative Megaliner concept.
South Africa-based platinum group metals and chrome producer Tharisa Minerals’ mine in Marikana, near Rustenburg, in the North West, was the first South African mine to adopt and implement the Megaliner concept in December 2017.
The mine was concerned about major downtime that occurred on average every nine months, which involved the replacement of linings in the primary ball mill – a process that took about 48 h. The primary ball mill, like many others of its type, can process 250 t/h of ore 24/7, which amounted to a significant disruption in production.
Metso regional product support manager Duane Mathers says the primary ball mill was originally equipped with 180 liners that had to be removed individually, which was a time-consuming process. “Replacing them with Metso’s Megaliner, however, was a different story. Owing to the simplicity of the design, we required only 30 modules to reline the mill interior,” he explains.
Mathers says, despite a few “first-time niggles”, the process took only 38 h, reducing planned downtime by ten h.
He says the company expects that this will bring the total time taken to replace liners to less than 24 h, reducing downtime by about 50% at the next reline.
Metso also offers after-sales service to clients, as well as process and wear monitoring, which helps the company to fine-tune the design.
“From the client’s perspective, the Megaliner presents a tried and tested improvement in technology, providing an accessible and credible competitive advantage,” Mathers concludes.
Comments
Press Office
Announcements
What's On
Subscribe to improve your user experience...
Option 1 (equivalent of R125 a month):
Receive a weekly copy of Creamer Media's Engineering News & Mining Weekly magazine
(print copy for those in South Africa and e-magazine for those outside of South Africa)
Receive daily email newsletters
Access to full search results
Access archive of magazine back copies
Access to Projects in Progress
Access to ONE Research Report of your choice in PDF format
Option 2 (equivalent of R375 a month):
All benefits from Option 1
PLUS
Access to Creamer Media's Research Channel Africa for ALL Research Reports, in PDF format, on various industrial and mining sectors
including Electricity; Water; Energy Transition; Hydrogen; Roads, Rail and Ports; Coal; Gold; Platinum; Battery Metals; etc.
Already a subscriber?
Forgotten your password?
Receive weekly copy of Creamer Media's Engineering News & Mining Weekly magazine (print copy for those in South Africa and e-magazine for those outside of South Africa)
➕
Recieve daily email newsletters
➕
Access to full search results
➕
Access archive of magazine back copies
➕
Access to Projects in Progress
➕
Access to ONE Research Report of your choice in PDF format
RESEARCH CHANNEL AFRICA
R4500 (equivalent of R375 a month)
SUBSCRIBEAll benefits from Option 1
➕
Access to Creamer Media's Research Channel Africa for ALL Research Reports on various industrial and mining sectors, in PDF format, including on:
Electricity
➕
Water
➕
Energy Transition
➕
Hydrogen
➕
Roads, Rail and Ports
➕
Coal
➕
Gold
➕
Platinum
➕
Battery Metals
➕
etc.
Receive all benefits from Option 1 or Option 2 delivered to numerous people at your company
➕
Multiple User names and Passwords for simultaneous log-ins
➕
Intranet integration access to all in your organisation