Mines urged to fill renewables gaps with green electrons from on-site waste heat
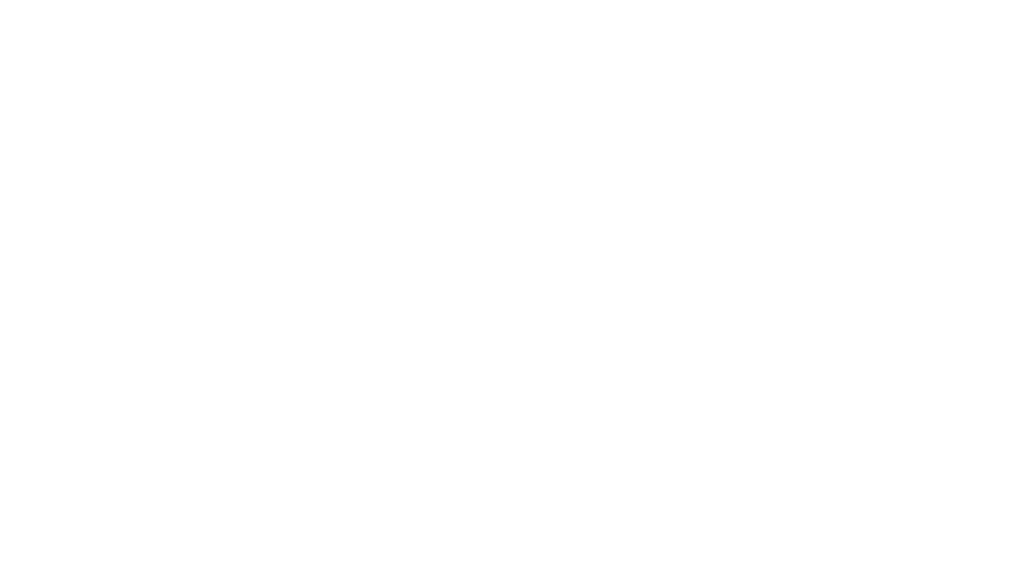
Kraftblock's Martin Schichtel interviewed by Mining Weekly's Martin Creamer. Video: Darlene Creamer.
JOHANNESBURG (miningweekly.com) – Mines using renewable energy are being encouraged to harvest and store heat wasted during minerals processing and to then use its green electrons to close renewables intermittency gaps that come about when the sun isn’t shining and the wind isn’t blowing.
Implementing systems to do this also come with considerable economic benefit, Kraftblock co-founder and CEO Dr Martin Schichtel outlined to Mining Weekly in a Zoom interview. (Also watch attached Creamer Media video.)
Kraftblock, a high-temperature thermal energy storage system for process heat recall, augments decarbonisation by decoupling renewable-energy generation from energy demand and then discharging stored green electrons to where they are needed, when they are needed.
Rethinking heat can take mining operations to the next level of greenness, says Schichtel, whose main takeaway is that there are now options in the market to make processes even cleaner through high-temperature processing elevation.
“All those options, especially high-temperature energy storage, which were not that well known in the market, are here today, and we can use them now to make things better,” he says about turning renewable electricity into usable heat as well as reusing waste heat from high-temperature processes.
As mining scales up production of critical minerals for clean energy technologies, storing clean heat from electrification for discharge during intermittency is seen as having the wherewithal to enable mining companies to also offset declining ore grade quality.
The mining industry is very much involved in the energy transition itself. Just think about the raw materials for PV solar, wind turbines, the transmission grid and the many other aspects of the energy transition requiring green electrons and increased energy efficiency that need to be ecologically positive in the fight against climate change.
Mining Weekly: What becomes of the surplus heat if it is not recovered and stored?
Schichtel: That's the crazy part of this story. Usually, where you operate an oven, a furnace, a kiln, a calciner, what we call waste heat is generated and sometimes, in the more modern industries, that waste heat is partially reused in the process, but not all of it, and usually there’s a good opportunity to utilise what remains to increase efficiency. Otherwise, it just goes into the atmosphere as lost energy.
How does storage ensure that the intermittent renewable energy gap is filled?
Thermal storage involves storing heat and the stored heat is nothing but a buffer, which means you can decouple energy generation from energy demand. The perfect use case is as intermittent energy, especially to buffer renewable electricity, be it from solar PV or wind energy, because there are a lot of fluctuations. The stored energy can be discharged to whenever it's needed to make mining greener.
Where have you succeeded in using thermal heat to decarbonise operations?
Our earliest project began five years ago in the ceramics industry, where we installed the system to harvest the thermal energy by preventing it from going into the atmosphere and by putting it to our storage device. Then, when the next batch gets heated up, the stored heat is released back to the furnace, increasing the warmth from room temperature to 400 oC when the gas burners start firing, which reduces emissions, saves energy and improves the quality of the ceramic material.
How long do these systems take to pay for themselves?
Systems in waste heat recovery have payback times of between one-and-a-half years and three years maximum. Electrification of heat might be a bit different, because it depends on the price difference between gas and green electrons. But renewables in locations such as Spain, California in the US, southern Europe, and Australia, are so cheap that they easily compete against gas, with payback times of between three and maybe six years.
LOWERING EMISSIONS
The metal and mining sector has two big jobs. The one is to dig out the raw materials needed for many low-carbon technologies that help to combat climate change and the other is to minimise the generation of harmful emissions during minerals production and processing. Solar energy and wind power generation need a lot of aluminium and copper; wind and geothermal power generation need zinc and titanium; storage needs graphite and lithium.
The upshot is that technologies have to be deployed to keep in check the considerable energy demands of high-temperature smelting and refining and high-temperature energy storage is one of those technologies now on offer to take processing to the next level of greenness.
Comments
Press Office
Announcements
What's On
Subscribe to improve your user experience...
Option 1 (equivalent of R125 a month):
Receive a weekly copy of Creamer Media's Engineering News & Mining Weekly magazine
(print copy for those in South Africa and e-magazine for those outside of South Africa)
Receive daily email newsletters
Access to full search results
Access archive of magazine back copies
Access to Projects in Progress
Access to ONE Research Report of your choice in PDF format
Option 2 (equivalent of R375 a month):
All benefits from Option 1
PLUS
Access to Creamer Media's Research Channel Africa for ALL Research Reports, in PDF format, on various industrial and mining sectors
including Electricity; Water; Energy Transition; Hydrogen; Roads, Rail and Ports; Coal; Gold; Platinum; Battery Metals; etc.
Already a subscriber?
Forgotten your password?
Receive weekly copy of Creamer Media's Engineering News & Mining Weekly magazine (print copy for those in South Africa and e-magazine for those outside of South Africa)
➕
Recieve daily email newsletters
➕
Access to full search results
➕
Access archive of magazine back copies
➕
Access to Projects in Progress
➕
Access to ONE Research Report of your choice in PDF format
RESEARCH CHANNEL AFRICA
R4500 (equivalent of R375 a month)
SUBSCRIBEAll benefits from Option 1
➕
Access to Creamer Media's Research Channel Africa for ALL Research Reports on various industrial and mining sectors, in PDF format, including on:
Electricity
➕
Water
➕
Energy Transition
➕
Hydrogen
➕
Roads, Rail and Ports
➕
Coal
➕
Gold
➕
Platinum
➕
Battery Metals
➕
etc.
Receive all benefits from Option 1 or Option 2 delivered to numerous people at your company
➕
Multiple User names and Passwords for simultaneous log-ins
➕
Intranet integration access to all in your organisation