Modular installation systems fitted in abattoir
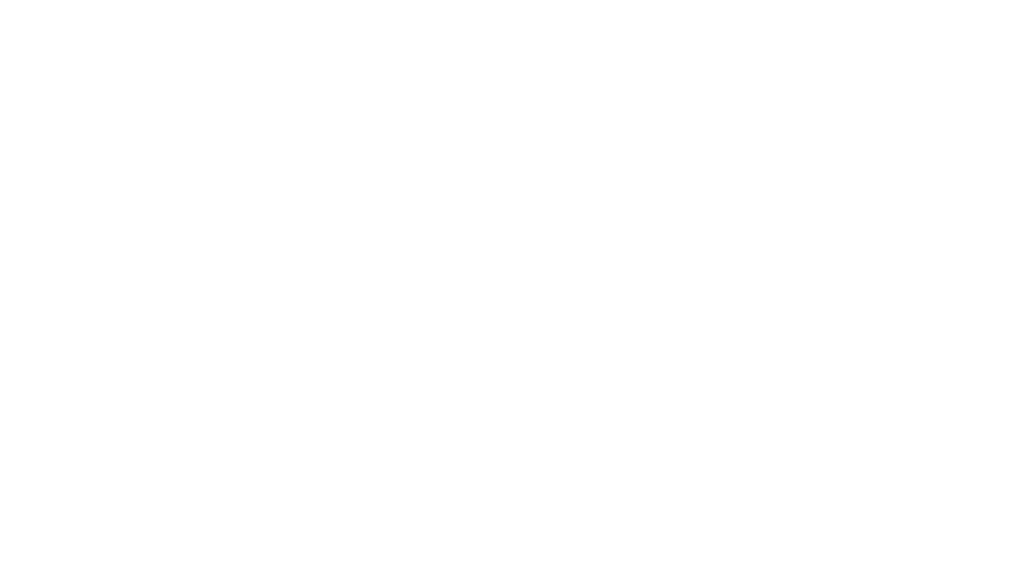
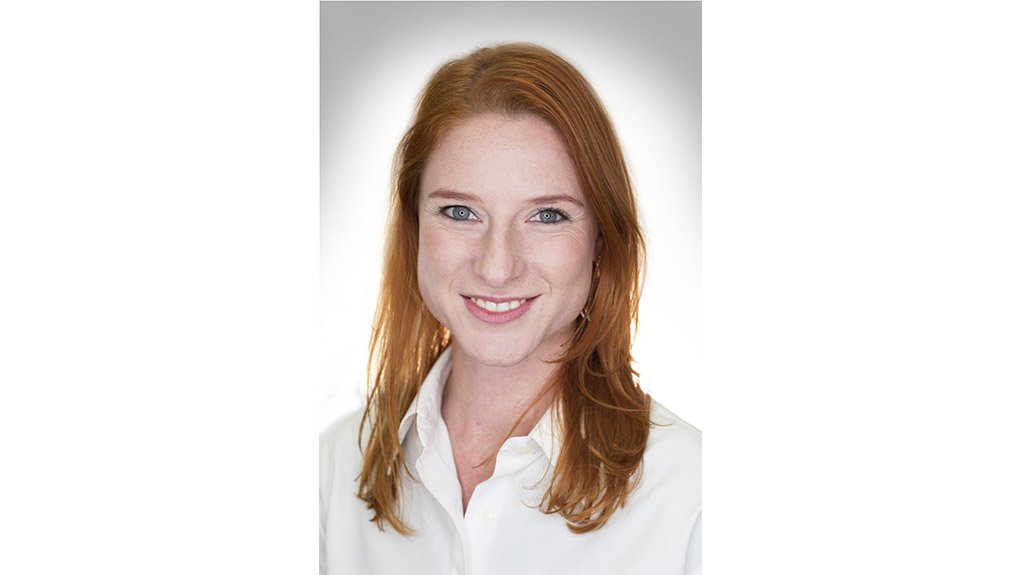
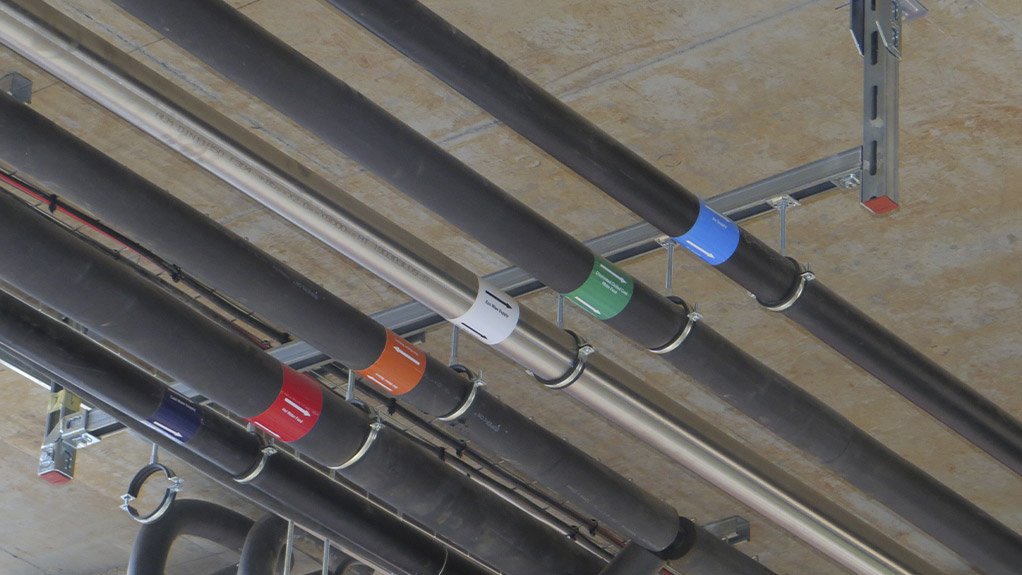
CRIZETTE VAN DEN BERGH The modular installation system is beneficial in terms of maintenance because of reduced downtime
FIRM GRIP The modular installation system requires no welding or drilling
Multinational construction services company Hilti designed and supplied the modular installation systems to support wet services for chicken producer Early Bird Farms, in Olifantsfontein.
Early Bird Farms has been refurbishing and refitting its operations as part of Project Phoenix, which includes the expansion of its existing abattoir facilities.
The wet services installation section of the project was completed in August by contractor Sebenza Sanitary Engineering.
The project included wet services, such as plumbing and related piping, and was time sensitive from the start, says Hilti field engineer Crizette van den Bergh.
Sebenza Sanitary Engineering subsequently used Hilti’s modular installation systems because the contractor was familiar with the systems’ design, assembly and quick installation procedures, owing to recent project designs and system demonstrations.
Upon receiving the request from Sebenza Sanitary Engineering, Hilti’s local design team performed a preliminary design, which was reviewed by the project engineer.
Thereafter, a fully detailed design was completed by the Hilti design team in Dubai, in the United Arab Emirates, along with technical submissions for approval by the project structural engineer, who, in turn, granted final approval less than two weeks after the initial request had been received.
Consequently, 103 brackets were installed in about two weeks, including the pipes, says Sebenza Sanitary Engineering contracts manager Gustav Beukes.
Sebenza Sanitary Engineering director Dale Hawkins adds that Hilti’s modular installation system for the nine-pipe bank was prefabricated to save time.
“The modular nature of the system meant that the installation was a simple and quick task,” he adds.
Van den Bergh explains that conventional bracketing systems are typically made from angle iron. This requires it being cut to the required size, then drilled for bolting and then welded together. The angle iron bracket also needs to be painted or galvanised for rust protection before it can be installed.
The Hilti modular installation system, by comparison, requires only cutting to size before assembly and installation. The steel components are already galvanised or made from stainless steel, and no welding or drilling is required. Final in- place adjustments and alignment are made possible by the serrated channel lip and fitting components to assure precision work before final tightening.
A test conducted by Hilti showed that one conventional bracket made from angle iron would require about two hours and 15 minutes to complete. The Hilti modular installation system, by comparison, took only about 35 minutes.
Van den Bergh notes that the absence of hot works from the installation process translates to improved safety on site, as well as lower costs because legislated hot works safety precautions and site adjustments need not be implemented.
Further, there is no need to employ specialised hot works skills such as welding, for example.
The modular nature of the installation system also means that future extensions and adjust ments can be made with comparatively little effort and reduced shutdown time.
For further ease of implementation, Hilti has developed the Profis Installation building information modelling software. It is geared specifically for the design and planning of the modular bracketing systems and allows for the creation of two- or three-dimensional (3D) drawings.
This is further supported through Hilti’s field engineering services, which include technical calculations and design support, as well as detailed assembly drawings.
Further, the software is freely available and can be downloaded at no cost from the company’s website. Hilti offers a variety of such software applications bespoke for different products.
The modular installation system is available in several sizes for a variety of applications.
The MM series is aimed at smaller, lighter channel installations and is suitable for most light mechanical and electrical support systems. It can include ventilation duct and electrical cable tray supports.
The MQ and MI series are modular 3D systems that allow for an unlimited number of connections.
While the MQ series is best suited to medium-duty channel installations, and can support most mechanical and electrical support applications, the larger units of the MI series are geared towards industrial applications and can support heavy-duty pipes, cable trays and raised flooring applications.
The MI series is about 50% lighter than standard bracketing systems, which translates to less weight being placed on ceiling or wall structures.
Van den Bergh notes that, while the MI series has been used quite extensively in industrial applications, an uptick in the MQ series – in wet works and plant room applications, such as at Early Bird Farms – has occurred only recently.
Comments
Press Office
Announcements
What's On
Subscribe to improve your user experience...
Option 1 (equivalent of R125 a month):
Receive a weekly copy of Creamer Media's Engineering News & Mining Weekly magazine
(print copy for those in South Africa and e-magazine for those outside of South Africa)
Receive daily email newsletters
Access to full search results
Access archive of magazine back copies
Access to Projects in Progress
Access to ONE Research Report of your choice in PDF format
Option 2 (equivalent of R375 a month):
All benefits from Option 1
PLUS
Access to Creamer Media's Research Channel Africa for ALL Research Reports, in PDF format, on various industrial and mining sectors
including Electricity; Water; Energy Transition; Hydrogen; Roads, Rail and Ports; Coal; Gold; Platinum; Battery Metals; etc.
Already a subscriber?
Forgotten your password?
Receive weekly copy of Creamer Media's Engineering News & Mining Weekly magazine (print copy for those in South Africa and e-magazine for those outside of South Africa)
➕
Recieve daily email newsletters
➕
Access to full search results
➕
Access archive of magazine back copies
➕
Access to Projects in Progress
➕
Access to ONE Research Report of your choice in PDF format
RESEARCH CHANNEL AFRICA
R4500 (equivalent of R375 a month)
SUBSCRIBEAll benefits from Option 1
➕
Access to Creamer Media's Research Channel Africa for ALL Research Reports on various industrial and mining sectors, in PDF format, including on:
Electricity
➕
Water
➕
Energy Transition
➕
Hydrogen
➕
Roads, Rail and Ports
➕
Coal
➕
Gold
➕
Platinum
➕
Battery Metals
➕
etc.
Receive all benefits from Option 1 or Option 2 delivered to numerous people at your company
➕
Multiple User names and Passwords for simultaneous log-ins
➕
Intranet integration access to all in your organisation