New ball mill offers junior miners energy, cost savings
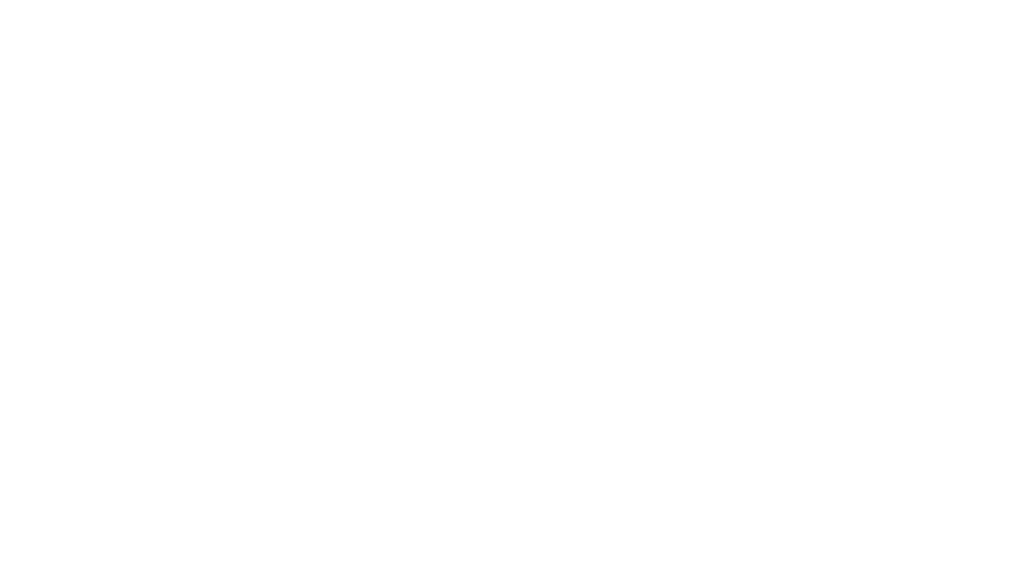
Gold Rock Projects founder and head of sales Mike Marsay discusses the company’s new cost effective mill
Crushing solutions company Gold Rock Projects is developing a new, more cost-effective and energy efficient ball mill, designed to enable gold producers, particularly entry-level and junior operations, to process ore with greater flexibility and lower operating costs.
The most expensive and complex section of gold mining is typically the mill, owing to heavy machinery being employed, a high energy demand, extensive maintenance and sophisticated process control adding to its operational costs, says Gold Rock Projects founder and head of sales Mike Marsay.
The new mill directly addresses these issues with a reduction in plant size, lower power requirements and a less complicated structure, while retaining its ability to efficiently break down ore, he posits.
Gold Rock is currently finalising the new mill’s design.
“We’ve completed the design process and we’re now preparing to construct a prototype for testing. The concept isn’t a dramatic departure from conventional mill design; instead, we’re focusing on reducing excess mass and power consumption while retaining functionality,” says Marsay.
Gold Rock’s new mill is not meant to replace conventional mills used by large, established mines, but rather to enable growing operations to raise their processing capacity to a commercial standard without needing significant capital investment.
“ . . . while we do not anticipate its delivering a service life [exceeding] . . . five or six years, it’s designed to enable companies to grow their operations and generate revenue in a cost-effective way,” he adds.
If properly maintained, the new mill can operate for a “number of years”, but Marsay says the mill “is not a 20-year solution”.
Although many mining companies, especially in developing jurisdictions or more remote locations, cannot justify a multimillion-rand investment in standard mill equipment, Gold Rock’s mill offers a realistic way forward, says Gold Rock technical sales executive Bennie Botha.
“Our aim is to enable producers to process their ore without needing to make that heavy investment. We’re looking at delivering this mill at roughly a third of the price of a conventional mill, while [it] retains functionality, robustness and operational stability,” he adds.
Under Development
The Gold Rock team expects to have its first prototype ready by the end of this year or by mid-2026, depending on funding and operational schedules.
The company is in discussion with a company in Zimbabwe, which is eager to trial the new mill at its processing plant once it is operational.
There is a strong industry interest in this kind of solution, especially from companies that need something more flexible, less heavy and less power-intensive, highlights Marsay.
“We’re looking forward to putting it into action and demonstrating its ability to make a measurable financial and operational difference for gold producers,” he says.
Marsay adds that the company’s innovations form a key piece in a larger industry-wide drive towards more sustainable and cost-effective operations, as gold mines are under growing pressure to reduce their energy use and carbon emissions.
“With the new mill, you’re looking at a significant drop in power consumption per tonne of ore processed. Some modern crushers have been able to halve their power usage, dropping from 200 kW down to 110 kW, without affecting production. This directly reduces . . . energy costs and the carbon footprint of gold mines, which is a major step forward for the industry,” says Marsay.
This forms a crucial part of a much broader movement, whereby some mines are increasingly commissioning renewable- energy power plants, installing water treatment plants and employing more energy-intensive technology, while Gold Rock is focusing on reducing energy use directly at the point of ore processing, he concludes.
Comments
Press Office
Announcements
What's On
Subscribe to improve your user experience...
Option 1 (equivalent of R125 a month):
Receive a weekly copy of Creamer Media's Engineering News & Mining Weekly magazine
(print copy for those in South Africa and e-magazine for those outside of South Africa)
Receive daily email newsletters
Access to full search results
Access archive of magazine back copies
Access to Projects in Progress
Access to ONE Research Report of your choice in PDF format
Option 2 (equivalent of R375 a month):
All benefits from Option 1
PLUS
Access to Creamer Media's Research Channel Africa for ALL Research Reports, in PDF format, on various industrial and mining sectors
including Electricity; Water; Energy Transition; Hydrogen; Roads, Rail and Ports; Coal; Gold; Platinum; Battery Metals; etc.
Already a subscriber?
Forgotten your password?
Receive weekly copy of Creamer Media's Engineering News & Mining Weekly magazine (print copy for those in South Africa and e-magazine for those outside of South Africa)
➕
Recieve daily email newsletters
➕
Access to full search results
➕
Access archive of magazine back copies
➕
Access to Projects in Progress
➕
Access to ONE Research Report of your choice in PDF format
RESEARCH CHANNEL AFRICA
R4500 (equivalent of R375 a month)
SUBSCRIBEAll benefits from Option 1
➕
Access to Creamer Media's Research Channel Africa for ALL Research Reports on various industrial and mining sectors, in PDF format, including on:
Electricity
➕
Water
➕
Energy Transition
➕
Hydrogen
➕
Roads, Rail and Ports
➕
Coal
➕
Gold
➕
Platinum
➕
Battery Metals
➕
etc.
Receive all benefits from Option 1 or Option 2 delivered to numerous people at your company
➕
Multiple User names and Passwords for simultaneous log-ins
➕
Intranet integration access to all in your organisation