Newest firefighting technology delivered to South Africa
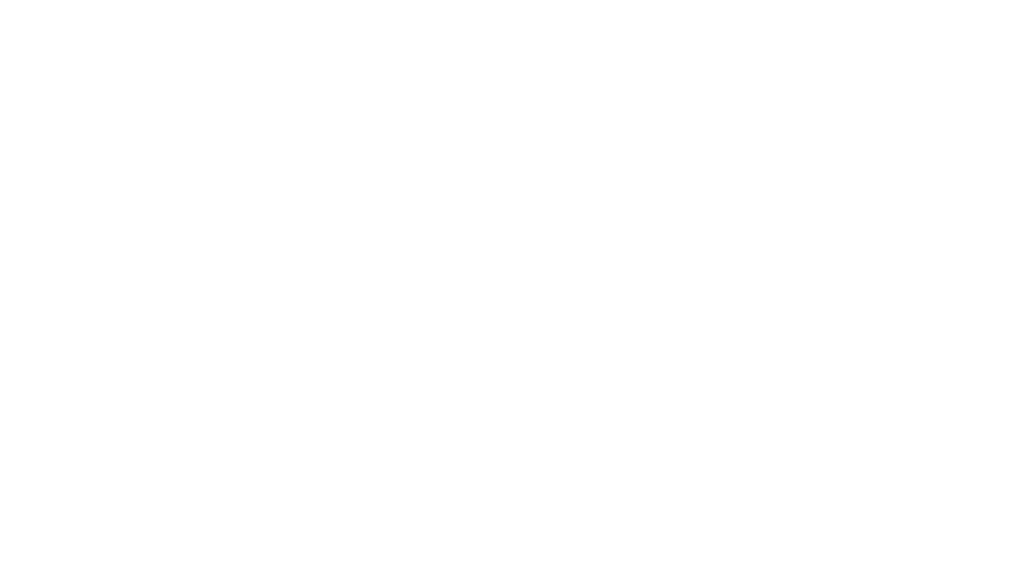
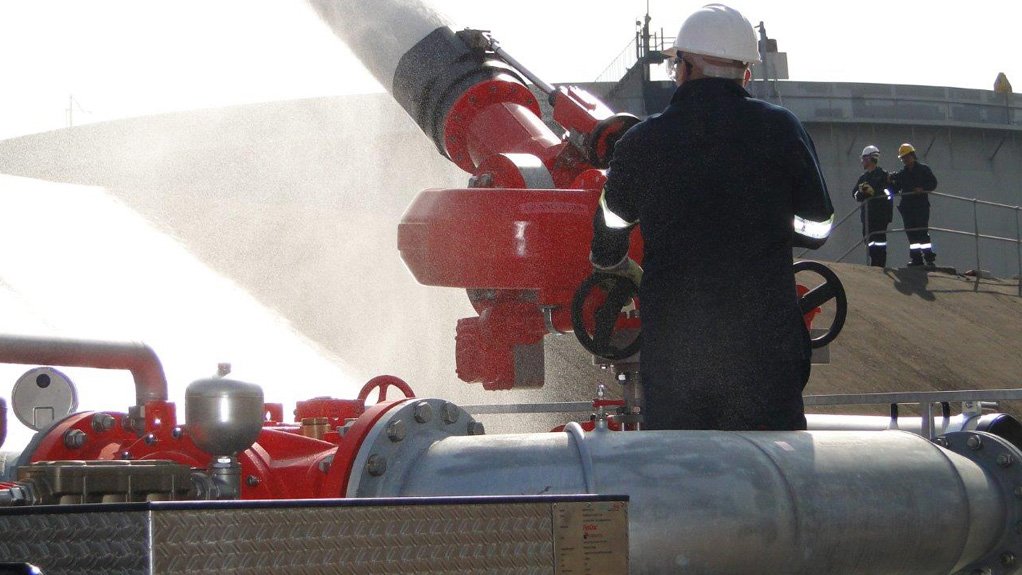
GERMAN ENGINEERING The FTM units are manufactured by DoseTech partner and German fire-safety product manufacturer FireDos
Fire protection technology provider DoseTech is promoting the concept of firefighting trailer-mounted (FTM) units in the sub-Saharan Africa oil industry, and has concluded the delivery of the first system to the South African market. Further, the company is in discussions with a South African refinery for the possible supply of a unit.
DoseTech MD Mike Feldon says the concept has gained traction in the South African oil industry, after DoseTech supplied an FTM unit – for quick and effective knock-down in the event of fire – to a South Africa-based crude oil storage depot in July.
The portable unit requires no external power source and is capable of delivering between 5 000 ℓ/min and 22 000 ℓ/min of fire-suppressing foam and water up to 120 m away.
The design comprises a special FireDos foam and water monitor, combined with a FireDos foam dosing proportioner unit to ensure that the precise proportion of suppression foam to water – 3% in this case – is maintained regardless of the volume flow rate selected on the adjustable flow setting. This allows the operator to adjust the unit according to the severity of the fire.
Feldon explains that the foam concentrate is specified by the customer and forms part of a detailed analysis of the actual safety requirements. Foam is available in various concentrations, such as 1%, 3% and 6%. “Once the foam has been selected, the FireDos foam-dosing pump is designed to ensure that the amount of foam concentrate added to the water flow remains proportional throughout the operation.”
Maintaining this constant foam-water flow ensures that fire hazards are successfully dealt with, significantly reducing the cost when providing correct volume of foam concentrate, he adds. “Additionally, this ensures effective planning in terms of foam stock.
“The FireDos foam addition dosing pump is designed and tested to meet exacting requirements and forms part of the total system, which includes the FireDos water cannon, also known as a monitor,” Feldon states.
The innovative oval-flat design of the monitor ensures that, unlike competitors’ products, the reactive forces are practically eliminated; therefore, no additional ballast is required to keep the unit stable during operation. The monitor has 360° of horizontal movement and between –90° and +120°in the vertical plane; it is fitted with a combined fog and stream nozzle for either cooling or vapour-suppression applications. A removable foam aspiration tube is available as an option.
“The FireDos proportioner is driven solely by the extinguishing water flow. No emergency electrical energy or engine-driven prime mover is required. The purely mechanical system is highly reliable,” explains Feldon.
The water motor and proportioning pump are connected with each other through a coupling, and therefore operate at the same speed. The system regulates itself automatically; therefore, as more water flows through the water motor, more foam is added. The proportioning rate selected by the user always remains constant.
He comments that a portion of the pressure in the extinguishing water line is used as an energy source to drive the water motor, which is substantially lower than that of other systems available. “While hydrant pressures of10 bar are usual, the unit can safely accommodate a maximum water pressure of 16 bar and higher, if required.” Further, the self-priming proportioning pump can deliver fluorine-free viscous and/or alcohol-resistant foam agents without requiring additional modification.
The FTM unit incorporates water and foam agent manifolds that allow for connection to multiple hydrants through a standard-size fire hose, while the foam-agent manifold permits the coupling of more than one foam-agent tank, which is necessary during prolonged operation and prevents downtime during foam tanker changeover.
Specifically designed for the protection of fuel storage tanks, the FTM unit is one of the most advanced firefighting products available and the first of its kind on the continent, according to Feldon.
“The FireDos unit is built to last, as it is constructed from high-quality polytetrafluoro- ethylene-coated metal components and materials. All pressurised cast parts are designed for a test pressure of 64 bar and, although the unit has a mass of 4 t, it can easily be pulled by the average 1 t pick-up truck,” he adds.
The FTM units are custom-designed and manufactured by German fire-safety product manufacturer FireDos and supported and serviced by their business partner, DoseTech. Prior to delivery, the units are factory-tested in Germany to ensure that they meet the customer-specific performance and quality assurance requirements.
The units meet European and international fire-safety standards. They also comply with requirements set out by third-party testing and certification organisation FM Approvals, independent German fire protection and safety organisation Vertrauen durch Sicherheit, and European Union directive ATEX95, which outlines requirements for equipment and protective systems for use in potentially explosive atmospheres.
Feldon explains that the unit supplied to the local South African storage facility is unique; the units are built according to customer and application requirements, as they vary depending on the location, type and layout of the refinery or storage facility, and national or international product and safety standards.
As the units are individually designed and factory-tested, the company has a degree of flexibility. Therefore, future FTM units will have similar characteristics and be suited to similar applications.
Comments
Press Office
Announcements
What's On
Subscribe to improve your user experience...
Option 1 (equivalent of R125 a month):
Receive a weekly copy of Creamer Media's Engineering News & Mining Weekly magazine
(print copy for those in South Africa and e-magazine for those outside of South Africa)
Receive daily email newsletters
Access to full search results
Access archive of magazine back copies
Access to Projects in Progress
Access to ONE Research Report of your choice in PDF format
Option 2 (equivalent of R375 a month):
All benefits from Option 1
PLUS
Access to Creamer Media's Research Channel Africa for ALL Research Reports, in PDF format, on various industrial and mining sectors
including Electricity; Water; Energy Transition; Hydrogen; Roads, Rail and Ports; Coal; Gold; Platinum; Battery Metals; etc.
Already a subscriber?
Forgotten your password?
Receive weekly copy of Creamer Media's Engineering News & Mining Weekly magazine (print copy for those in South Africa and e-magazine for those outside of South Africa)
➕
Recieve daily email newsletters
➕
Access to full search results
➕
Access archive of magazine back copies
➕
Access to Projects in Progress
➕
Access to ONE Research Report of your choice in PDF format
RESEARCH CHANNEL AFRICA
R4500 (equivalent of R375 a month)
SUBSCRIBEAll benefits from Option 1
➕
Access to Creamer Media's Research Channel Africa for ALL Research Reports on various industrial and mining sectors, in PDF format, including on:
Electricity
➕
Water
➕
Energy Transition
➕
Hydrogen
➕
Roads, Rail and Ports
➕
Coal
➕
Gold
➕
Platinum
➕
Battery Metals
➕
etc.
Receive all benefits from Option 1 or Option 2 delivered to numerous people at your company
➕
Multiple User names and Passwords for simultaneous log-ins
➕
Intranet integration access to all in your organisation