OMRON is shaping traceability in food and beverage packaging
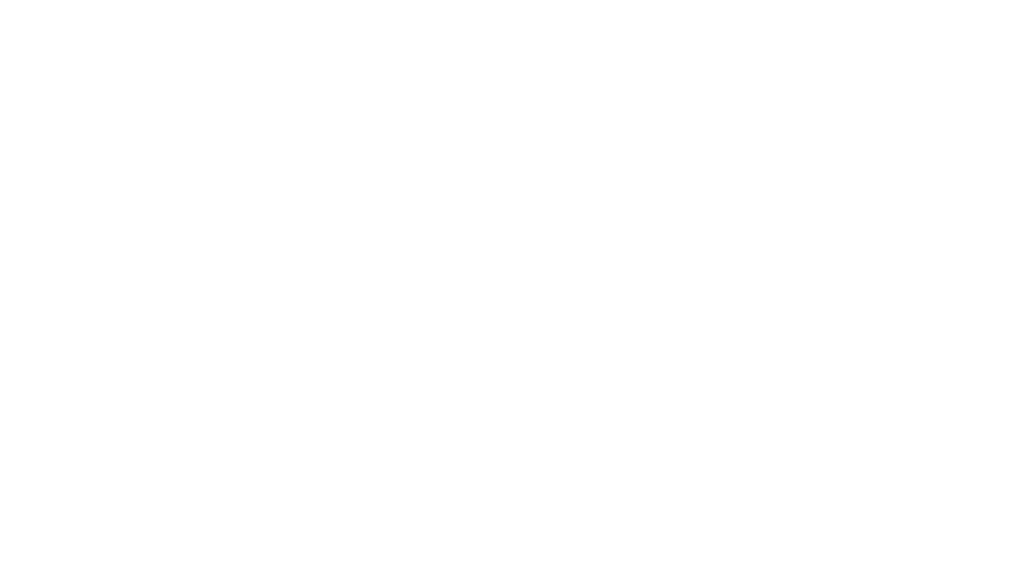
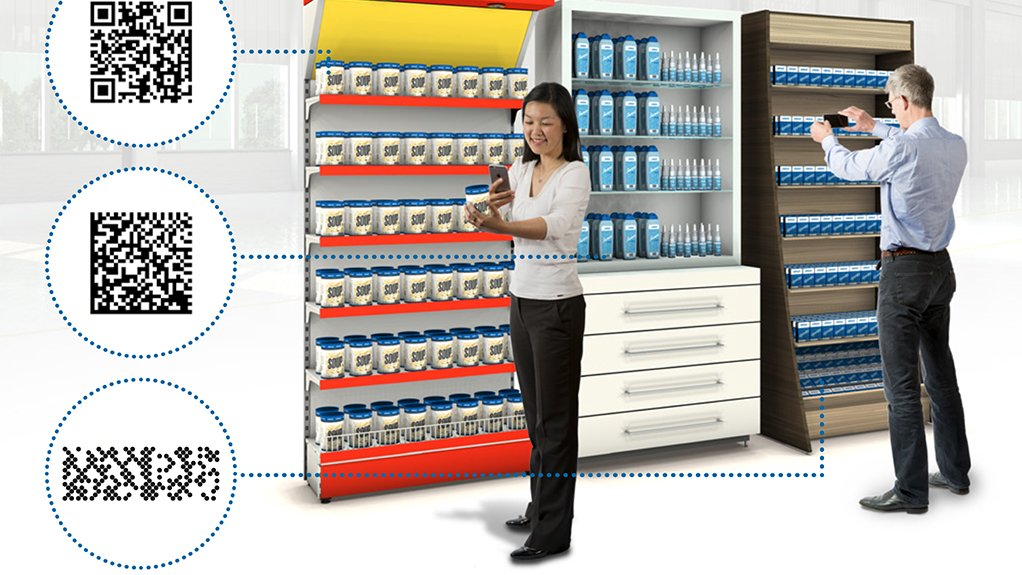
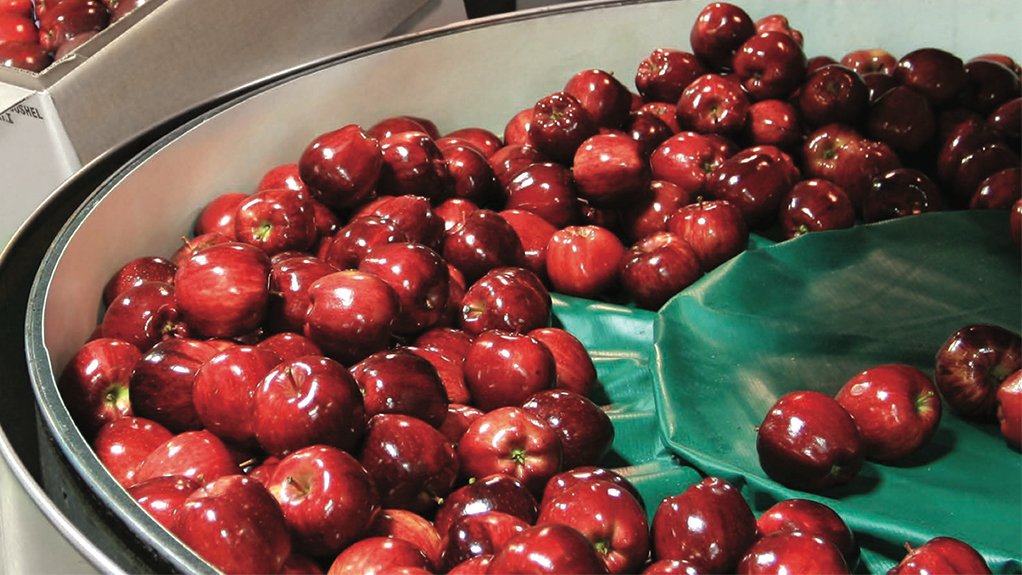
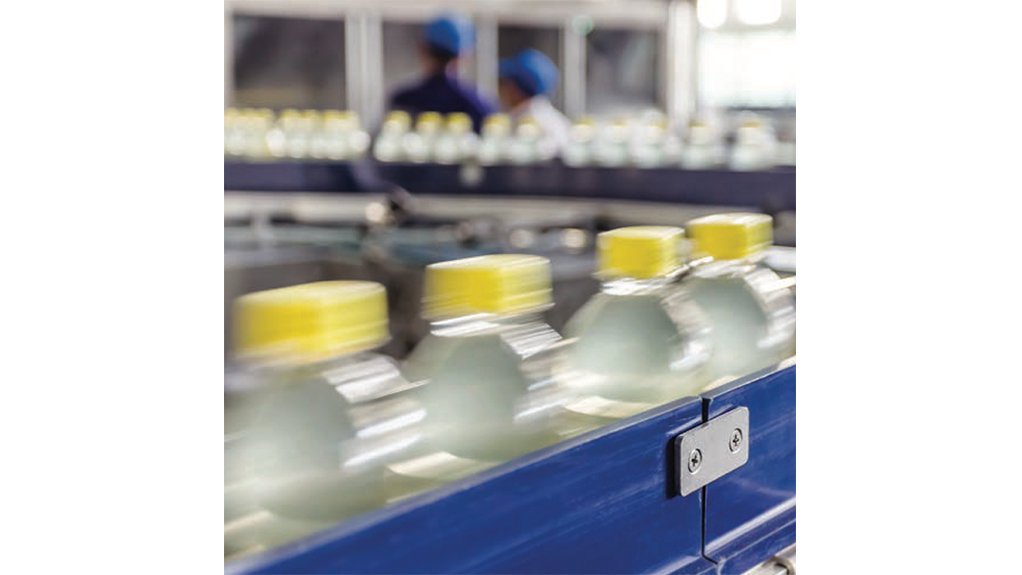
VISIONARY Omron strives to make traceability as easy as possible, just as it strives to make its machine vision technology intuitive enough for the average operator to use
NEW RULES The South African government has created a regulatory framework and related instruments for food safety and traceability
STANDARD PROCEDURE Larger South African retailers are adopting international trade standards and/or defining their standards
In the food and beverage packaging industry, authenticity is essential. Consumers need to know that the foods they are purchasing consist of the things listed on their labels, because food allergies and expired foods can cause serious illness and possibly death.
Since both public health and consumer satisfaction depend so heavily on product integrity, the food and beverage packaging industry is highly regulated.
One of the main things mandated by food and beverage regulation is traceability – the practice of maintaining thorough records of the origins and whereabouts of products and raw materials by scanning printed barcodes, direct part marks or radio frequency identification tags throughout the production process and the supply chain.
From the raw materials supplier to the production line to the supermarket and then to the customer, the creation and distribution of a particular food item should be as transparent as possible.
Food and beverage manufacturers also benefit directly from traceability protocols that minimise the occurrence and effect of costly issues, such as product recalls, by providing real-time data on supplier materials, processes and machinery involved in the production.
These protocols can significantly reduce the cost of a recall by isolating tainted items and making it unnecessary to pull large amounts of non-tainted products off the shelves.
To meet the requirements of the European Union regulations, South Africa promulgated Standards Regarding Food Hygiene and Food Safety of Regulated Agricultural Food Products of Plant Origin for Export.
These are collectively referred to as SA-GAP. SA-GAP is often used as the basic standard for inspections of produce destined for the local market.
SA-GAP standards require that food products are handled under hygienic conditions through all stages of the supply chain, good record keeping and that food business operators (FBOs) can withdraw or recall products that pose a risk to human health from anywhere in the trade chain.
The South African government has created a regulatory framework and related instruments for food safety and traceability.
The Department of Health and the Department of Agriculture, Land Reform and Rural Development (DALRRD) have responsibilities relating to the safety of food locally and meeting the requirements of international markets. DALRRD Inspection Services ensures compliance with phytosanitary agreements.
Government assignees assure compliance of products in different sectors, for example, the Perishable Products Export Control Board (PPECB) is responsible for assuring that exports of fresh and processed products of plant origin meet the requirements of the South African Agricultural Products Standards Act [Act 119 of 1990].
Similarly, the Department of Agriculture, Forestry and Fisheries assures that fish products comply with regulations, and the Wine & Spirits Board assures compliance of wine and spirits processes and products.
The Meat Safety Act, 2000 – Act 40 of 2000 – provides for measures to promote meat safety and the safety of animal products, establishes and maintains essential national standards in respect of abattoirs, regulates the import and export of meat, and establishes meat safety schemes.
The national Food Safety and Maximum Residue Levels is chaired by DALRRD’s Directorate: Food Safety and Quality Assurance. The forum publishes hazard profiles, food safety checklists, and compliance criteria for different types of FBOs.
Separate operating procedures and guidelines may be provided, for example, for residue sampling and traceability. PPECB inspectors use the checklists during food safety export compliance audits.
A Food Safety Forum Technical Working Group updates the documents from time to time.
Further documents are under review or in the process of being prepared.
Companies handling products of plant origin that are destined for export markets are required to register with DALRRD as FBOs. Producers who supply local fresh produce markets will in the future also register as FBOs.
An FBO must adhere to good handling practices and traceability, keep adequate records and be able to withdraw implicated products from the market should there be a serious problem. An approach to responding to product alerts, withdrawals and recalls is provided in the Traceability Standard Operating Procedure.
Larger South African retailers are adopting international trade standards and/or defining their standards. This has a domino effect and backs up the fresh produce chain, and producers and processors who are unable to provide evidence of adhering to good practices may be locked out of storage and processing facilities.
The ability to show evidence of due diligence and compliance with a standard would depend on the records available about a specific product or process at each point in the chain.
Using Traceability to Analyse and Optimise Productivity
In addition to helping companies avoid recalls and other disruptions to their profitability, traceability systems are also a great way to optimise processes and evaluate overall equipment effectiveness.
By collecting and analysing operational data, manufacturers can figure out which machines are underperforming and pinpoint precisely where bottlenecks are occurring in production.
To gather this data, manufacturers need to set up numerous barcode reading stations at various points across the production line. Barcoding helps track vital productivity information, such as throughput and quality based on package type, machine, shift and product.
In many cases, this means that barcode readers need to be embedded within machinery. This poses a challenge since most manufacturing equipment is designed to take up as little space as possible and, therefore, doesn’t have much extra room for barcode readers. This creates the need for ultra-compact readers, such as Omron’s MicroHAWK readers.
The MicroHAWK industrial barcode readers and smart cameras are designed to be highly flexible and configurable within an exceptionally compact casing. This means that they can be easily embedded within machinery while still providing a fast and accurate reading.
Thanks to their liquid lens autofocus technology, the MicroHAWK readers eliminate constraints on camera positioning. The same MicroHAWK camera can be used for machine vision inspection, enabling the expansion of automation as a facility’s needs evolve without investment in new hardware.
Once traceability data is gathered using the barcode readers, it needs to be communicated to the rest of the system. This poses a new challenge – that of using this data without hampering control performance.
When traditional controllers are tasked with processing large amounts of traceability data, they are liable to slow down the production cycle time.
Omron addressed this issue by developing controllers that can maintain high-speed control while handling all the information a traceability system provides.
For example, the NX1 controller can be used for a packaging machine with the capability of handling 1 000 products per minute and can collect all traceability data in synchronisation with the production cycle while performing motion control.
This means that traceability doesn’t need to slow down other aspects of production while fulfilling the purpose of collecting important data.
MicroHAWK barcode readers provide direct connectivity via Ethernet/IP to Omron’s NX1 controllers, making it simple to integrate traceability data into the automated system.
When it comes to using traceability information, data collection is one challenge. It is another matter altogether to transfer that data to the business and enterprise systems that store and use the data.
“Our controllers make this easy thanks to the seamless incorporation of SQL and OPC-UA.”
Embracing Vision Systems for Complete Product Compatibility
Machine vision technology has been taking on an increasingly important role in traceability because it is an extremely effective way to maintain complete product integrity.
Vision inspection includes a wide variety of functionality, such as detecting defective products in real-time and performing both optical character recognition and optical character verification to verify that the data on labels and packages adds up.
By functioning as a complete solution for ensuring that non-conforming products do not go out into the market, vision systems are vital for brand protection.
The hurdle that manufacturers face in implementing a machine vision system is twofold. Such systems are often expensive to implement, and the complexity of the technology can overwhelm operators.
Many applications require special programming. However, these challenges are offset by the fact that a single product recall or fine for a tainted product – preventable by a vision system – could cost more than the vision system itself.
Omron puts ease of use at the core of its machine vision technology so that manufacturers do not need to rely on experts to get things up and running.
The HAWK MV-4000 smart camera is a perfect example of machine vision made easy. It has two separate user interfaces to satisfy both novices and experienced vision professionals alike.
Operators who are new to machine vision can benefit from the intuitive AutoVISION interface, whereas the experts can gain access to the smart camera’s full potential with the Visionscape FrontRunner interface.
The HAWK MV-4000 is also extremely powerful. As a standalone smart camera, it can reach processing speeds almost as high as a PC-based system of multiple cameras.
With a complete vision, code reading and code verification toolset in combination with full industrial connectivity, it is an excellent choice for manufacturers seeking to take their traceability systems to a new level.
In addition to high-performance smart cameras, Omron also has high-end, full-vision systems with the same focus on ease of use.
The FH Series enables high-speed, high-accuracy inspection and measurement functionality designed to meet or exceed the need for rapidly growing automation and higher performance requirements in industries, such as food and beverage packaging.
FH Series machine vision systems employ sophisticated lighting that clearly shows defects by flexibly changing illumination colours and angles. Multiple cameras can be hooked up to enable panoramic shooting and expand the field of view by combining images at high speeds.
Transitioning from Manual Record-keeping to Fully Automated Traceability
The avoidance of unwanted complexity is not just a deterrent to using machine vision – it is often a reason manufacturers forego upgrading their traceability systems in any way.
Because implementing a new system seems inordinately complex, many manufacturers prefer to stick with cumbersome and error-prone record-keeping methods that rely on manual processes.
Understandably, companies want traceability to be easy. However, failing to upgrade the system with automation leads to more work in the long run.
Manual record-keeping is far more widespread in the food and beverage packaging industry than it should be, especially when one considers the huge costs associated with certain types of mistakes.
Unfortunately, not all companies have the budget to invest in good traceability software. Budgetary constraints and the fact that traceability solutions need to be scalable are major barriers to automating systems.
Omron strives to make traceability as easy as possible, just as it strives to make its machine vision technology intuitive enough for the average operator to use.
Its MicroHAWK barcode readers keep things simple by working right out of the box – in fact, the browser-based Weblink interface allows manufacturers to start using the readers without needing to install any software whatsoever.
Omron also has extensive knowledge of how traceability works in a variety of industries, and its focus on providing comprehensive solutions with complete line integration lets companies rest assured that the upgraded system will “just work”.
Although often perceived to be challenging and somewhat expensive at the outset, a robust traceability system is the single most important means of complying with industry regulations and reducing the incidence and cost of recalls.
Omron’s traceability solutions address various pain points that manufacturers face in the food and beverage packaging industry so that real-time, automated traceability is within the reach of any company that needs to comply with requirements from the South African Bureau of Standards and SA-GAP to mention a few.
Comments
Press Office
Announcements
What's On
Subscribe to improve your user experience...
Option 1 (equivalent of R125 a month):
Receive a weekly copy of Creamer Media's Engineering News & Mining Weekly magazine
(print copy for those in South Africa and e-magazine for those outside of South Africa)
Receive daily email newsletters
Access to full search results
Access archive of magazine back copies
Access to Projects in Progress
Access to ONE Research Report of your choice in PDF format
Option 2 (equivalent of R375 a month):
All benefits from Option 1
PLUS
Access to Creamer Media's Research Channel Africa for ALL Research Reports, in PDF format, on various industrial and mining sectors
including Electricity; Water; Energy Transition; Hydrogen; Roads, Rail and Ports; Coal; Gold; Platinum; Battery Metals; etc.
Already a subscriber?
Forgotten your password?
Receive weekly copy of Creamer Media's Engineering News & Mining Weekly magazine (print copy for those in South Africa and e-magazine for those outside of South Africa)
➕
Recieve daily email newsletters
➕
Access to full search results
➕
Access archive of magazine back copies
➕
Access to Projects in Progress
➕
Access to ONE Research Report of your choice in PDF format
RESEARCH CHANNEL AFRICA
R4500 (equivalent of R375 a month)
SUBSCRIBEAll benefits from Option 1
➕
Access to Creamer Media's Research Channel Africa for ALL Research Reports on various industrial and mining sectors, in PDF format, including on:
Electricity
➕
Water
➕
Energy Transition
➕
Hydrogen
➕
Roads, Rail and Ports
➕
Coal
➕
Gold
➕
Platinum
➕
Battery Metals
➕
etc.
Receive all benefits from Option 1 or Option 2 delivered to numerous people at your company
➕
Multiple User names and Passwords for simultaneous log-ins
➕
Intranet integration access to all in your organisation