Palabora’s vent shaft a 'triumph of collaboration’ and remarkable safety performance
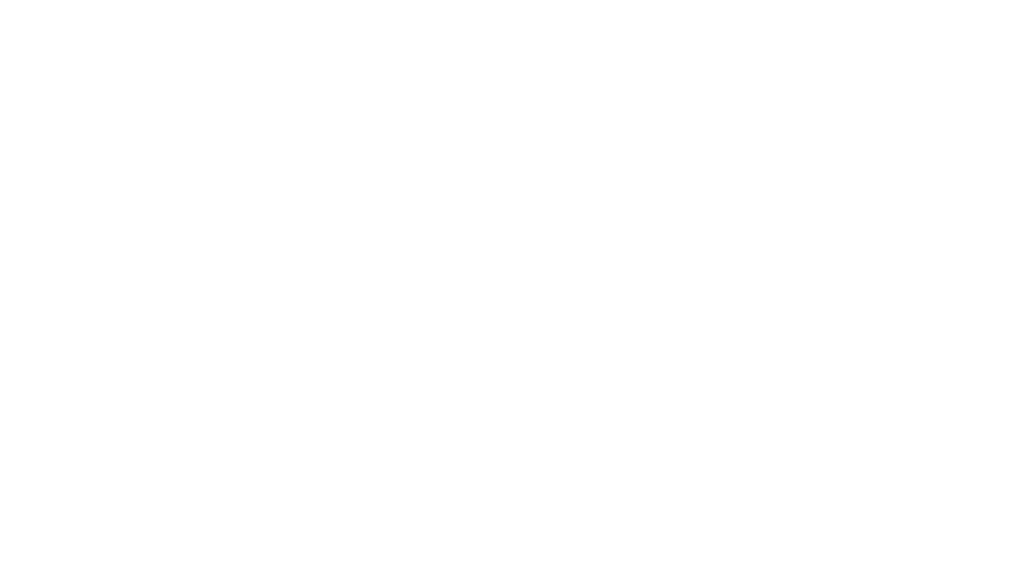
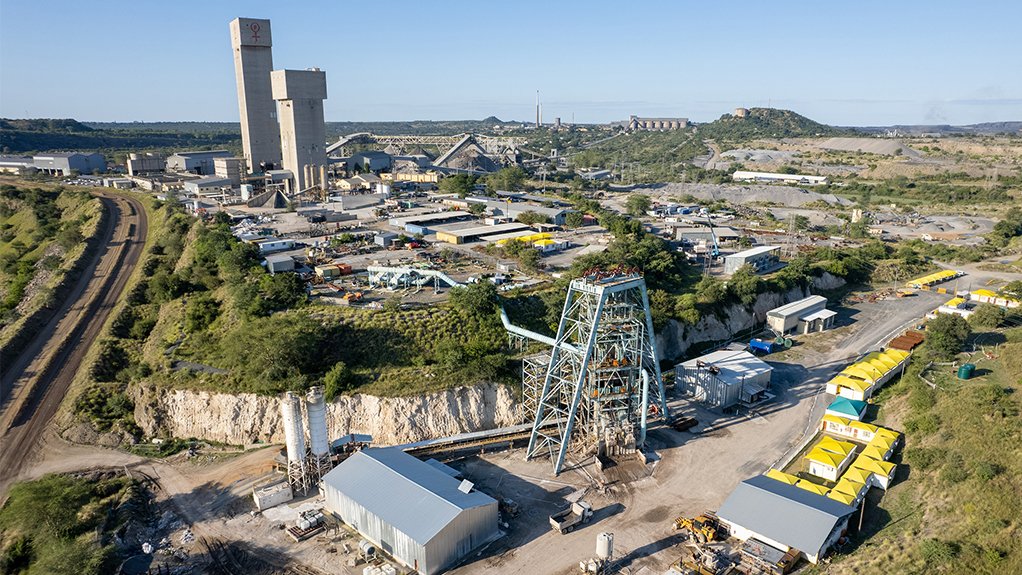
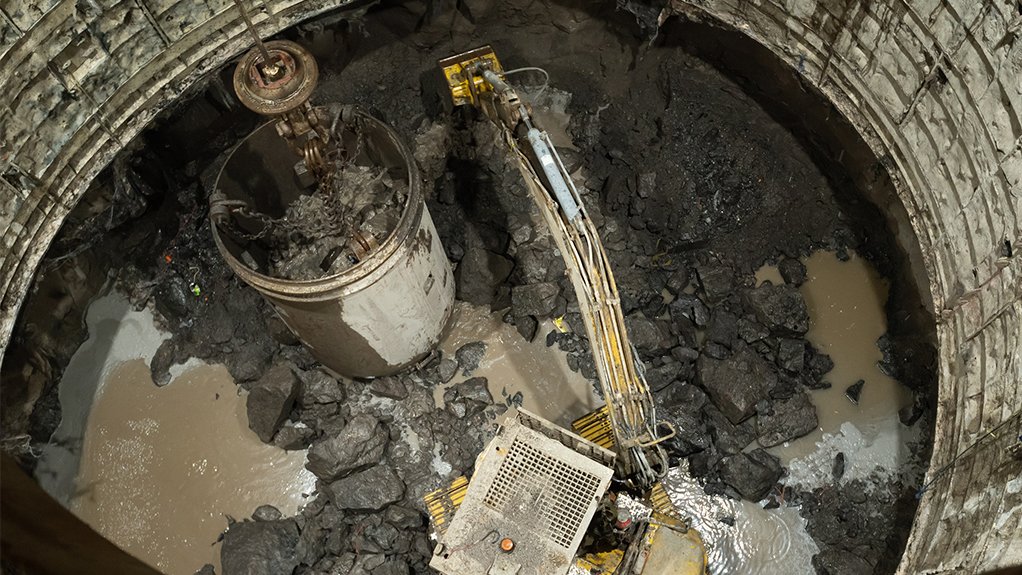
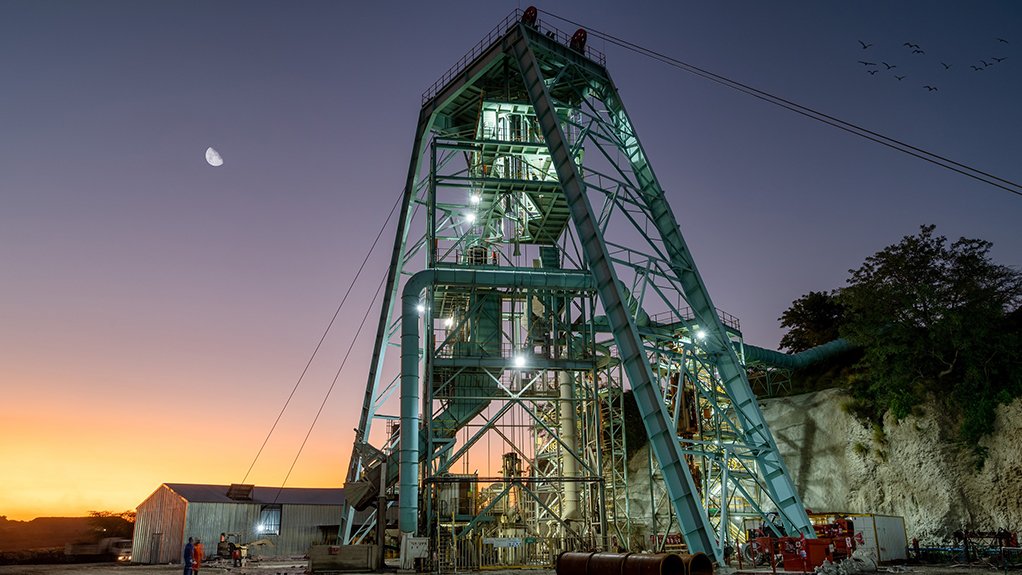

The PMC Lift 2 expansion project is expected to extend the life-of-mine to at least 2038
An excavator busy lashing at the shaft bottom with shaft lining being carried out on the face
Murray & Roberts Cementation was awarded the contract to sink and line a ventilation shaft at PMC
PMC took a deliberate decision to prioritise safety in the sinking of the ventilation shaft
The sinking of a 1 200 m ventilation shaft as part of copper miner Palabora Mining Company’s (PMC’s) Lift 2 expansion is proving to be a partnership success story, based on an unshakeable commitment to safety, Murray & Roberts Cementation states.
PMC commissioned the new ventilation shaft – which measures 8.5 m in diameter – to service its Lift 2 block cave, awarding the project to South African consultants Murray & Roberts Cementation in February 2019.
Now in its final phases, the project has an impeccable safety record. It has remained fatality-free and, last year, achieved 574 days without a lost-time injury.
“Feasibility studies indicated that a blind sink was the optimal method, despite its higher cost and longer timeframe,” says Murray & Roberts Cementation project manager Jas Malherbe.
“Ground conditions were among the reasons why raiseboring was not an option, as the side walls needed immediate support to prevent scaling,” he points out.
Traditionally, the shaft would be lined to within 12 m to 18 m of the shaft bottom, with the sidewalls being temporarily supported with split sets and mesh. However, the difficult ground conditions led to high levels of scaling that made this practice unviable.
“With ground conditions being such a key challenge on the project, we responded in an innovative way by taking the shaft lining right down to the blasted face,” he says.
“The shaft sinking methodology in this project is therefore based on the Canadian shaft sinking method pioneered by Murray & Roberts Cementation – but has been adapted to ‘the PMC way’. This has involved lining the shaft to within 1.5 m of the shaft bottom, after mucking out the waste,” Malherbe says.
Murray & Roberts Cementation uses a specialised concrete mix for rapid setting and early strength, which hardens to 3 MPa within four hours. This is in place for at least eight hours before blasting.
This solution requires that the blast is conducted while the shutters are still in place – so the shutters are strengthened and a toe is added to better handle the blast.
The exposed concrete above the shutter is able to withstand the blast, as it has already cured for 48 hours.
Malherbe explains that drilling is undertaken by two twin-boom electro-hydraulic jumbo drill rigs. These are slung down the shaft from surface and nested in the four-deck stage for drilling the shaft bottom, a procedure which is repeated for each 48-hour blast-to-blast cycle.
Waste rock is lashed using an excavator with a 0.36 m2 bucket, which is lowered from surface through the stage to shaft bottom.
After blasting, an excavator is used for loading rock from the shaft bottom, which is safer than the conventional cactus grab. Ground conditions lend themselves to the generation of large rocks during blasting, which can be difficult to handle.
These are broken up using an hydraulic breaker, which can be coupled to the excavator. An 11 t kibble transports the waste rock to surface.
“Lashing a shaft with an excavator is not a new idea, but it is usually a back-up method to the cactus grab,” he says.
“In this project, we decided that the excavator would be the primary lashing method, to further enhance safety on site.”
Steps have also been taken towards automating the headgear, to avoid the safety hazards of manually hooking the kibble to tip out the waste rock. This includes the winding engine driver being able to use a camera to check for correct hooking.
“We also opted to use electric actuators in this project, rather than the traditional pneumatic and hydraulic cylinders on equipment such as the bank doors, swing chutes and tipping chutes,” Malherbe elaborates.
“This has allowed us to mitigate the risks such as hearing loss from the noise of certain actuators, and contamination from oil leaks.”
PMC package manager on the project Sechaba Letaba, meanwhile, says the copper miner took a deliberate decision to prioritise safety in the sinking of this ventilation shaft.
“By taking the PMC way, we have accepted that the pace of sinking would have to be compromised.
“This has proved to be a positive approach, as we have an outstanding safety record on the project. This is in stark contrast to the history of shaft sinking, which would often claim lives and cause injuries. We are therefore very proud of what we have achieved to date,” says Letaba.
Letaba highlights the pivotal roles played by PMC operation and Lift 2 project senior manager Sam Ngidi and PMC construction senior project manager Aidan Schoonbee in driving the project and ensuring its success.
Meanwhile, Murray & Roberts Cementation senior project manager Fred Durand points out that unexpected challenges tend to have an impact on scheduling, so the strong relationship of trust with PMC was vital to solving any issues as they arose.
“Our approach has always been to work closely with customers on solutions, and to ensure they are regularly updated on progress,” says Durand.
“As a team, for instance, we decided that the rock breaker was the right solution for the issue of oversized rocks, and it was accepted that this would have an impact on the cycle times.”
Similarly, encountering more challenging ground conditions than expected required a significant mindset change about how the team approached the project.
“With the supportive relationship between PMC and Murray & Roberts Cementation, we were able to agree on the necessary remedies and adjust the timeframe to suit our priority – which was safety,” he says.
Letaba emphasises that relationships between the client, the contractor, suppliers, employees and surrounding communities are vital to success. This project is testament to this fact, he says, and to the professionalism of Murray & Roberts Cementation.
“It is a pleasure to be serviced by a company like this, who proactively put world-class safety measures in place,” he says. “We look forward to completing the final phases of the shaft in the same safe manner.”
Malherbe concludes that, for Murray & Roberts Cementation, the lessons learnt on this project have shown the industry a viable alternative method of shaft sinking that takes safety to a new level.
Comments
Announcements
What's On
Subscribe to improve your user experience...
Option 1 (equivalent of R125 a month):
Receive a weekly copy of Creamer Media's Engineering News & Mining Weekly magazine
(print copy for those in South Africa and e-magazine for those outside of South Africa)
Receive daily email newsletters
Access to full search results
Access archive of magazine back copies
Access to Projects in Progress
Access to ONE Research Report of your choice in PDF format
Option 2 (equivalent of R375 a month):
All benefits from Option 1
PLUS
Access to Creamer Media's Research Channel Africa for ALL Research Reports, in PDF format, on various industrial and mining sectors
including Electricity; Water; Energy Transition; Hydrogen; Roads, Rail and Ports; Coal; Gold; Platinum; Battery Metals; etc.
Already a subscriber?
Forgotten your password?
Receive weekly copy of Creamer Media's Engineering News & Mining Weekly magazine (print copy for those in South Africa and e-magazine for those outside of South Africa)
➕
Recieve daily email newsletters
➕
Access to full search results
➕
Access archive of magazine back copies
➕
Access to Projects in Progress
➕
Access to ONE Research Report of your choice in PDF format
RESEARCH CHANNEL AFRICA
R4500 (equivalent of R375 a month)
SUBSCRIBEAll benefits from Option 1
➕
Access to Creamer Media's Research Channel Africa for ALL Research Reports on various industrial and mining sectors, in PDF format, including on:
Electricity
➕
Water
➕
Energy Transition
➕
Hydrogen
➕
Roads, Rail and Ports
➕
Coal
➕
Gold
➕
Platinum
➕
Battery Metals
➕
etc.
Receive all benefits from Option 1 or Option 2 delivered to numerous people at your company
➕
Multiple User names and Passwords for simultaneous log-ins
➕
Intranet integration access to all in your organisation