Screw splicing a reliable alternative to conventional belt repairs
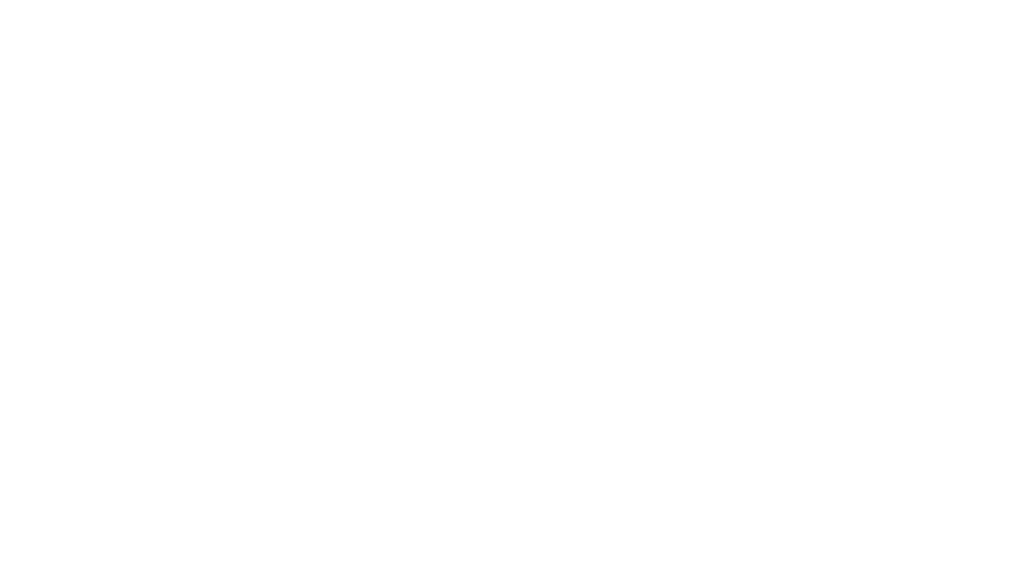
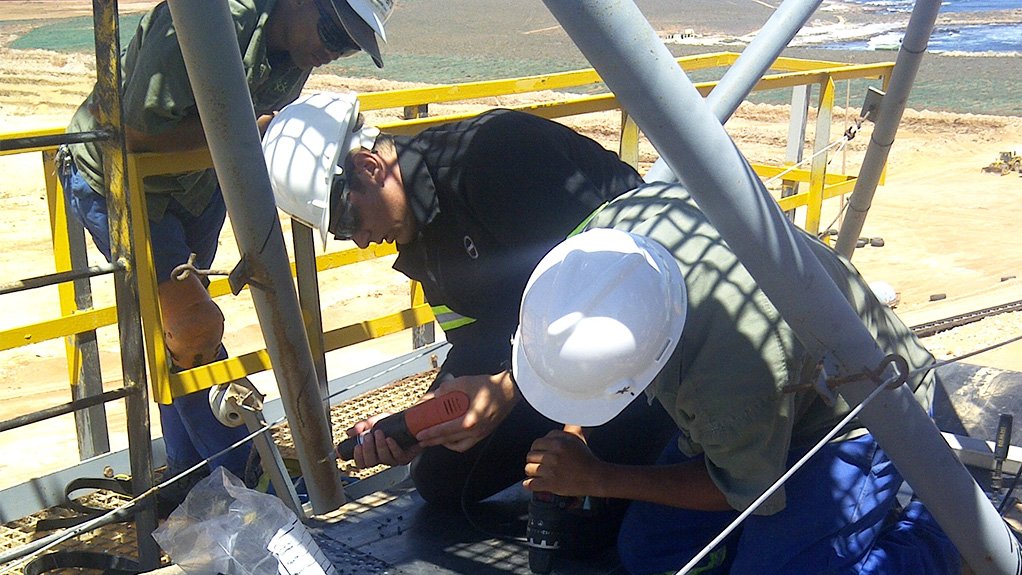
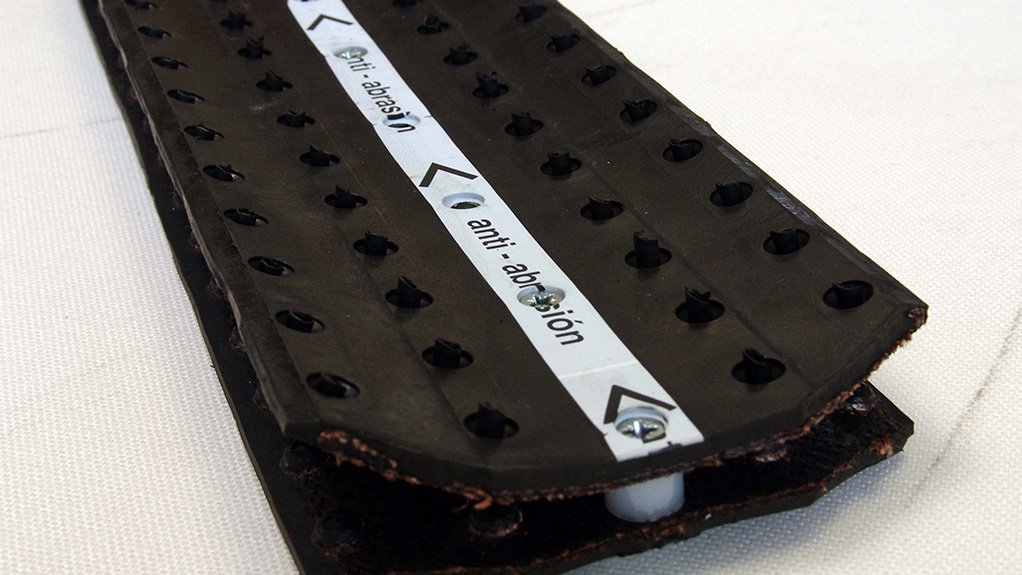
VERSATILE USE Super-Screw splices can be installed as temporary or permanent solutions regardless of the conveyor belt configuration, accessibility and the weather
RESISTANCE STRENGTH The Super-Screw splicing material is abrasion-, heat-, fire- and oil-resistant, as well as heat retardant, as it can withstand temperatures of up to 200 °C
Engineering company Bearing Man Group’s (BMG’s) efficient belt fastener system – the Super-Screw splice – which was originally used as a temporary alternative to conventional hot and cold splicing, has proven to be significantly reliable as a permanent splice for certain conveyor belts.
The high-strength splicing system includes a flexible rubber splice, which uses self-tapping screws that enable Super-Screw to be installed regardless of the configuration of the conveyor belt, accessibility and the weather.
“Super-Screw splices have lasted as long as hot and cold splices in the same application,” says BMG bulk materials handling divisional manager Donovan Scott. He adds that, depending on the application, the product can be used as a per- manent or temporary solution.
He further stresses the importance of the reduced production costs enabled by the Super-Screw. “While production costs are high, downtime can cost a business a lot of money and the Super-Screw mitigates this through its ease and speed of installation. Further, stock can be kept on site and fitted by the end-user’s employees.”
Meanwhile, Scott points out that demand for the Super-Screw has increased exponentially – by more than 25% in the past year – as more users adopt the product. He adds that BMG sells hundreds of metres of the splicing material yearly.
He also emphasises the product’s versatility, which allows for temporary repair, subsequently enhancing production time until a planned hot or cold splice can be completed. “It has been used to great effect as a longitudinal rip repair option, as the product is flexible enough to get around head, tail or snub pulleys without much of a problem.”
The product has been fitted successfully at steel producer ArcelorMittal South Africa’s operations, in Newcastle, KwaZulu-Natal; at copper miner Palaborwa Copper’s operations, in Limpopo; at Richards Bay Minerals’ operations, in KwaZulu-Natal, owned by diversified miner Rio Tinto; and at diversified miner BHP Billiton’s Wessels mine, near Hotazel, in the Northern Cape, and its Hillside operation, in Richards Bay. “These include temporary and permanent installations. However, belt classes, plies and widths have varied,” Scott adds.
Upgrade Drive
In conjunction with the South African Bureau of Standards, BMG has used various belt classes and widths to test the Super-Screw in different applications over the past three years.
Further, tension tests are being conducted by the Council for Scientific and Industrial Research on various splice types and wider 500 mm belts.
The aim of the tests is to fully understand the maximum and minimum tension levels, and to provide users with peace of mind when using the product, Scott explains. He adds that the joining is tested against SANS-accredited spliced belts.
Scott further tells Engineering News that the strength rating for the Super-Screw has been increased for higher-class belts, enabled by internal fabric reinforcement. Future enhancements of the Super-Screw may include aramid or carbon-strength members, he adds.
“Steel cord is also going to be an area of focus, as the product is currently geared more towards plied belting,” he says.
Moreover, field tests indicate that the Super-Screw is the quickest way to repair a conveyor belt in any emergency situation, thereby significantly reducing downtime, says Scott.
“Trials, during which the same belt width of 600 mm is being used, demonstrate that a conventional hot splice takes seven hours, while a cold splice takes more than eight hours, which includes curing the Super-Screw takes less than one hour to install,” he highlights.
This leak-proof system can be used to join a belt, or repair a longitudinal rip or puncture in a belt. The Super-Screw splice is compatible with small pulley diameters, is suitable for pipe conveyors and is conveyor scraper and V-plough friendly. The flexible splicing system can also be used to insert new belting into old conveyor belt systems.
The screws are self-drilling and self-tapping, spreading the carcass threads without cutting them. No predrilling is required.
Meanwhile, Scott points out that the current trend in the materials handling industry is to avoid using hazardous substances when possible. Trichloroethylene, a solvent used in conventional hot and cold splicing procedures, can now be replaced by the Super-Screw system as a safe splicing alternative, notes Scott.
He adds that trichloroethylene is deemed hazardous by the Department of Mineral Resources (DMR). Limited exposure to this solvent has been advised by the DMR as it can be absorbed through the skin. Scott believes, therefore, that other plants and factories will embrace this risk-mitigation strategy as they aim to put the health of their employees and contractors first.
Comments
Press Office
Announcements
What's On
Subscribe to improve your user experience...
Option 1 (equivalent of R125 a month):
Receive a weekly copy of Creamer Media's Engineering News & Mining Weekly magazine
(print copy for those in South Africa and e-magazine for those outside of South Africa)
Receive daily email newsletters
Access to full search results
Access archive of magazine back copies
Access to Projects in Progress
Access to ONE Research Report of your choice in PDF format
Option 2 (equivalent of R375 a month):
All benefits from Option 1
PLUS
Access to Creamer Media's Research Channel Africa for ALL Research Reports, in PDF format, on various industrial and mining sectors
including Electricity; Water; Energy Transition; Hydrogen; Roads, Rail and Ports; Coal; Gold; Platinum; Battery Metals; etc.
Already a subscriber?
Forgotten your password?
Receive weekly copy of Creamer Media's Engineering News & Mining Weekly magazine (print copy for those in South Africa and e-magazine for those outside of South Africa)
➕
Recieve daily email newsletters
➕
Access to full search results
➕
Access archive of magazine back copies
➕
Access to Projects in Progress
➕
Access to ONE Research Report of your choice in PDF format
RESEARCH CHANNEL AFRICA
R4500 (equivalent of R375 a month)
SUBSCRIBEAll benefits from Option 1
➕
Access to Creamer Media's Research Channel Africa for ALL Research Reports on various industrial and mining sectors, in PDF format, including on:
Electricity
➕
Water
➕
Energy Transition
➕
Hydrogen
➕
Roads, Rail and Ports
➕
Coal
➕
Gold
➕
Platinum
➕
Battery Metals
➕
etc.
Receive all benefits from Option 1 or Option 2 delivered to numerous people at your company
➕
Multiple User names and Passwords for simultaneous log-ins
➕
Intranet integration access to all in your organisation