Simpler aeration pump design reduces maintenance requirements
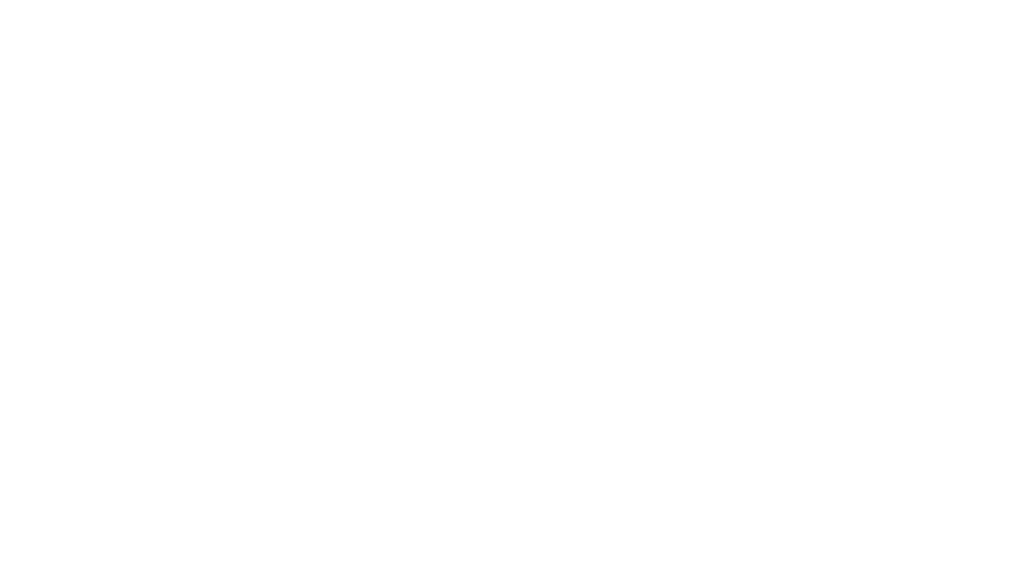
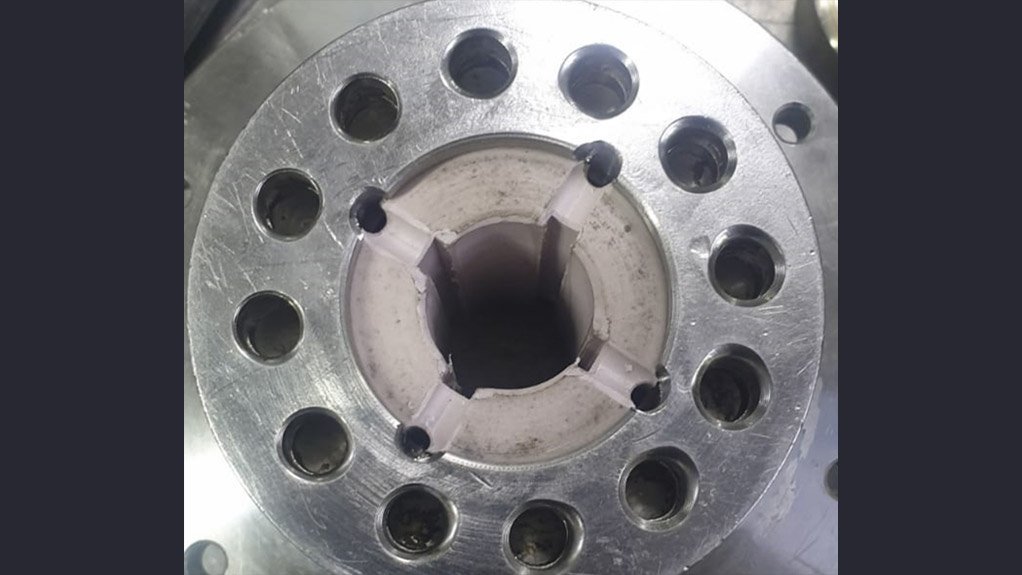
The much simpler bearing-component pump design includes Vesconite Bearings’ premier bearing material known as Vesconite Superlube
This article has been supplied.
There are times when a simple pump design and less maintenance are preferred by pump users, especially in messy dirty wastewater applications.
Such was the case with one wastewater plant operator in South Africa, which was being called in every couple of weeks to remove, disassemble and clean wastewater pumps at one or other of the facilities that the company maintains.
Aeration pumps float on wastewater treatment dams and ensure that chemical decomposition of the dirty water occurs before the wastewater gets treated further. The pumps ensure that the water remains oxygenated and that there is aerobic decomposition rather than anaerobic decomposition, which usually results in volatile and poisonous gases such as methane.
The pump design that was in place was a standard vertical shaft pump design with an output of between 5 kW and 10 kW.
However, the bearing design was complex and prone to failure before the introduction of Vesconite materials.
The main shaft bearing design consisted of a ball bearing with carbon mechanical seals on either side of it and the ball bearing was lubricated by oil that was pressure fed into the system so the pressure of the oil was higher than the pressure of the water on either side of the carbon seals, describes Vesconite Bearings engineer Petrus Fourie.
The main problem was that the carbon seals would pick up the dirt and grime that was in the naturally abrasive water and would erode. The seals would then fail and the wastewater would enter into the ball bearing.
“Anyone who has worked with ball bearings would know that ball bearings and water are not friends,” describes Fourie.
“If you get water anywhere near them they corrode very fast, especially if it is abrasive water,” he says.
It is this problem that resulted in the pumps seizing or shutting down because the ball bearings failed, and this resulted in the aerator pump company being called out every two to three weeks for pump maintenance.
The maintenance then required fishing the pump out of the wastewater; opening it up; cleaning out all the water and dirt that was trapped inside; and replacing the ball bearings.
The aeration pump company then approached Vesconite Bearings in search of a solution and Vesconite Bearings and the pump original equipment manufacturer (OEM) went through several design iterations before an appropriate and effective design was finalised.
The first design involved the replacement of the ball bearing, two carbon seals and the lubrication system with a no-swell wear-resistant Vesconite Hilube bushing in the existing housing.
The design was a combined thrust bearing and radial guide bearing — a combined main shaft bearing and thrust bearing so it has both axial and radial running faces.
“We proposed a flange bearing design where basically a step on the shaft would sit on the flange,” states Fourie.
“The vertical shaft would sit on top of the flange to absorb the vertical forces, the axial forces, and then you would have the bushing that would absorb lateral forces, or radial forces,” he says.
“In a pump that uses plain bearings from the start, you have a separate thrust washer or wear ring and a main shaft bearing,” Fourie notes.
“But here we hybridised the two parts,” he says noting that, because the ball bearings absorbed the axial force, Vesconite Bearings designed a plain bushing also to take on the axial force.
However, the first design proved inadequate in testing on a test bench with dirty water in the OEM company’s workshop.
None of the water that followed through the pump got to the flange face and this resulted in that particular face overhearing and melting.
“I suggested that the pump company cut some grooves on the flange face to allow the water to flush through,” notes Fourie.
“I also suggested that they add a stainless steel collar to the shaft, which would increase the area on to which the axial force applied,” he says, adding that, if you increase the area, you would decreasing the pressure and decrease the overall load on the bearing so it is less likely that it would overheat.
This second design worked better, but a couple of the grooves got blocked up on the axial face because of the dirty water and, again, that resulted in the bearing overheating.
Fourie further altered the design and suggested that the pump OEM switch its bearing material to Vesconite Bearings’ highest-grade bearing material, Vesconite Superlube, which is known for its ultra-low friction and extreme wear resistance.
His design also included additional grooves, increased groove sizes and holes through the stainless steel flange that rests on the axial face of the bearing to allow more water flow through the bearing.
The third design iteration has proven to be a charm and the South African wastewater company is happy with its pump’s performance.
The exact lifetime improvement has yet to be quantified, as the pumps that were installed with the latest bearing design are still operating, having been installed in October 2022.
Other advantages include that the company has reduced oil lubrication which, prior to the introduction of Vesconite Superlube, took place every four to six weeks depending on the water quality and currently takes place between four to six months with Vesconite Superlube, says the wastewater company’s operations director, who adds that the company is still deciding on a final acceptable maintenance schedule for the Vesconite Superlube application.
In addition, Vesconite Bearings’ solution resulted in the elimination of the carbon seals and the ball bearings, making the system much less complex and allowing for fewer problem areas while making the bearing system cheaper due to the reduction in the number of components.
The wastewater company’s operations director notes that he estimates that the Vesconite Superlube solution costs two third’s the cost of the replaced bearings and seals, with additional savings for the end user since they have reduced down time, labour and service costs.
The company increased the bearing lifetime and decreased its running costs. The company has also indicated it is easier to do maintenance because it is simpler to replace a plain bushing than to replace the carbon seals and ball bearings that were present in the earlier design.
“There are much fewer places for the dirt to accumulate so the engineer’s job is a little bit less messy,” states Fourie.
Vesconite’s premier bearing material, Vesconite Superlube, is a niche product which is made for niche applications such as this one, which is characterised by extremely abrasive and dirty water.
The material’s low friction, which is lower than virgin PTFE , is directly proportional to the material’s low wear rate.
“The low friction also has the advantage that it generates less heat,” describes Fourie.
“If you have any application that has a tendency to overheat and is wearing too fast, Vesconite Superlube is the ideal replacement because it generates less heat and it wears less quickly,” he adds.
Comments
Press Office
Announcements
What's On
Subscribe to improve your user experience...
Option 1 (equivalent of R125 a month):
Receive a weekly copy of Creamer Media's Engineering News & Mining Weekly magazine
(print copy for those in South Africa and e-magazine for those outside of South Africa)
Receive daily email newsletters
Access to full search results
Access archive of magazine back copies
Access to Projects in Progress
Access to ONE Research Report of your choice in PDF format
Option 2 (equivalent of R375 a month):
All benefits from Option 1
PLUS
Access to Creamer Media's Research Channel Africa for ALL Research Reports, in PDF format, on various industrial and mining sectors
including Electricity; Water; Energy Transition; Hydrogen; Roads, Rail and Ports; Coal; Gold; Platinum; Battery Metals; etc.
Already a subscriber?
Forgotten your password?
Receive weekly copy of Creamer Media's Engineering News & Mining Weekly magazine (print copy for those in South Africa and e-magazine for those outside of South Africa)
➕
Recieve daily email newsletters
➕
Access to full search results
➕
Access archive of magazine back copies
➕
Access to Projects in Progress
➕
Access to ONE Research Report of your choice in PDF format
RESEARCH CHANNEL AFRICA
R4500 (equivalent of R375 a month)
SUBSCRIBEAll benefits from Option 1
➕
Access to Creamer Media's Research Channel Africa for ALL Research Reports on various industrial and mining sectors, in PDF format, including on:
Electricity
➕
Water
➕
Energy Transition
➕
Hydrogen
➕
Roads, Rail and Ports
➕
Coal
➕
Gold
➕
Platinum
➕
Battery Metals
➕
etc.
Receive all benefits from Option 1 or Option 2 delivered to numerous people at your company
➕
Multiple User names and Passwords for simultaneous log-ins
➕
Intranet integration access to all in your organisation