Slogging hammer, wheel slogger upgrades offer safer maintenance
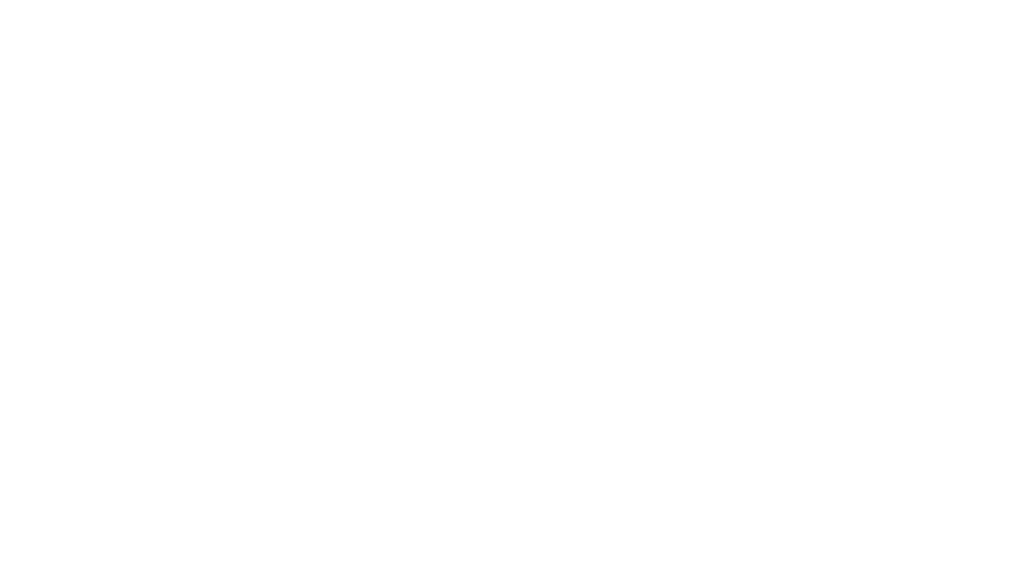
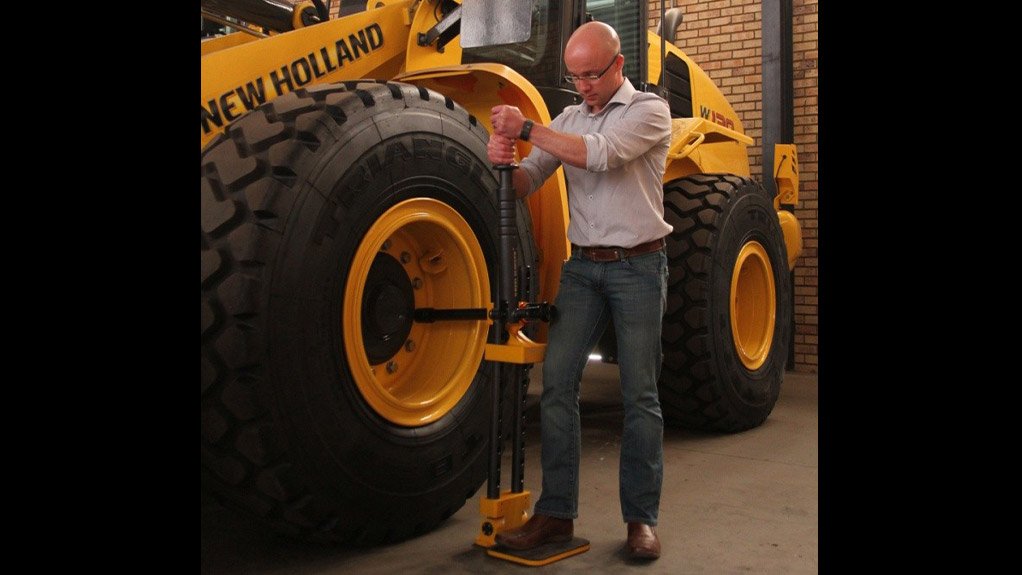
SIMPLER SETTINGS The clip on the wheel slogger enables the user to leave the tool attached to a wheel while selecting different torque settings
The slogging hammer and wheel slogger from tools and equipment supplier BMG have been upgraded to provide operators with greater efficiency and improved safety when loosening and tightening bolts and nuts during maintenance on mining equipment.
Productivity is significantly improved through the controlled and effective impact between the hammer and the spanner, resulting in minimal downtime when compared with other conventional methods, says BMG tools and equipment business unit manager Andrew Johns.
While maintaining the same level of performance, compared with that of previous versions, the new tools offer reduced downtime during maintenance and cost savings through single-operator deployment and the need for calibration has been removed on the wheel slogger.
Locally produced by precision engineering and tooling specialist Slogging International, the upgraded tools have been on the market since April this year, states Johns.
Advancements to the tools include a combination of two sizes, a new safety clip on the slogging hammer that prevents the shaft from sliding out when the tool is not in operation and an all-in-one torqueing clip on the wheel slogger.
The clip on the wheel slogger enables the user to leave the tool attached to a wheel while selecting different torque settings – from 450 Nm to 650 Nm. Previously torque settings were specific to a particular clip. Custom torque ranges of up to 1 000 Nm can be accommodated on request.
“The operator can be confident that when the required torque for the application, as prescribed by the original-equipment manufacturer, has been applied through the wheel slogger with its new torque clip, the installed torque will be within a 5% accuracy of a torque wrench applied to the same joint. This system mitigates the risk of damage to wheel studs through over-tightening,” explains Johns.
He adds that safety is the key focus with the slogging hammer and wheel slogger.
The slogging hammer was originally developed to overcome the hazards associated with the traditional hammer and slogging spanner method and to improve operator safety. This tool can also be used for pin extractions and, with an adaptor, it can be used with standard impact sockets and tyre bead breakers, as well as the removal of coal picks and other custom chisels.
Safety features of the slogging hammer include a built-in hand-grip, which eliminates the need for the operator’s hand to be near the impact zone, and an eye-bolt, which prevents accidents in overhead working conditions. No heavy lifting is necessary, as only the shaft weight needs to be managed.
This tool is easy to use in confined spaces and in areas that are difficult to access. It also provides greater direct impact, ensuring that the job is completed quickly and safely, as fewer blows are required, compared with conventional methods, says BMG.
The slogging hammer is available in four size configurations, from M16 to M76, and in models specifically suited to open-air, underground, spark-free and underwater environments. The open-air range is constructed with an aluminium tube and steel impact head, while the spark-free design uses a copper impact head.
The underground range is available as standard with a stainless steel tube and steel impact head, and also as spark-free, with a copper impact head, ensuring a safe solution for use in potentially explosive areas in underground mining.
When the slogging hammer is used in combination with the wheel slogger, applications are extended, says BMG, emphasising that this enables a single operator to safely and effortlessly loosen, tighten and torque nuts and bolts for the quick release and replacement of a damaged tyre on transportation, earthmoving and military equipment.
“Conventional hammer and slogger spanner systems require two operators to tighten and loosen nuts and bolts. This method is not only dangerous when the working area is cramped and there are other people in the vicinity but is also unsafe for the operator holding and guiding the slogging spanner. The operator is then at risk of shrapnel and is effectively at the mercy of the operator swinging the hammer,” concludes Johns.
Comments
Announcements
What's On
Subscribe to improve your user experience...
Option 1 (equivalent of R125 a month):
Receive a weekly copy of Creamer Media's Engineering News & Mining Weekly magazine
(print copy for those in South Africa and e-magazine for those outside of South Africa)
Receive daily email newsletters
Access to full search results
Access archive of magazine back copies
Access to Projects in Progress
Access to ONE Research Report of your choice in PDF format
Option 2 (equivalent of R375 a month):
All benefits from Option 1
PLUS
Access to Creamer Media's Research Channel Africa for ALL Research Reports, in PDF format, on various industrial and mining sectors
including Electricity; Water; Energy Transition; Hydrogen; Roads, Rail and Ports; Coal; Gold; Platinum; Battery Metals; etc.
Already a subscriber?
Forgotten your password?
Receive weekly copy of Creamer Media's Engineering News & Mining Weekly magazine (print copy for those in South Africa and e-magazine for those outside of South Africa)
➕
Recieve daily email newsletters
➕
Access to full search results
➕
Access archive of magazine back copies
➕
Access to Projects in Progress
➕
Access to ONE Research Report of your choice in PDF format
RESEARCH CHANNEL AFRICA
R4500 (equivalent of R375 a month)
SUBSCRIBEAll benefits from Option 1
➕
Access to Creamer Media's Research Channel Africa for ALL Research Reports on various industrial and mining sectors, in PDF format, including on:
Electricity
➕
Water
➕
Energy Transition
➕
Hydrogen
➕
Roads, Rail and Ports
➕
Coal
➕
Gold
➕
Platinum
➕
Battery Metals
➕
etc.
Receive all benefits from Option 1 or Option 2 delivered to numerous people at your company
➕
Multiple User names and Passwords for simultaneous log-ins
➕
Intranet integration access to all in your organisation