Hybrid future in sight
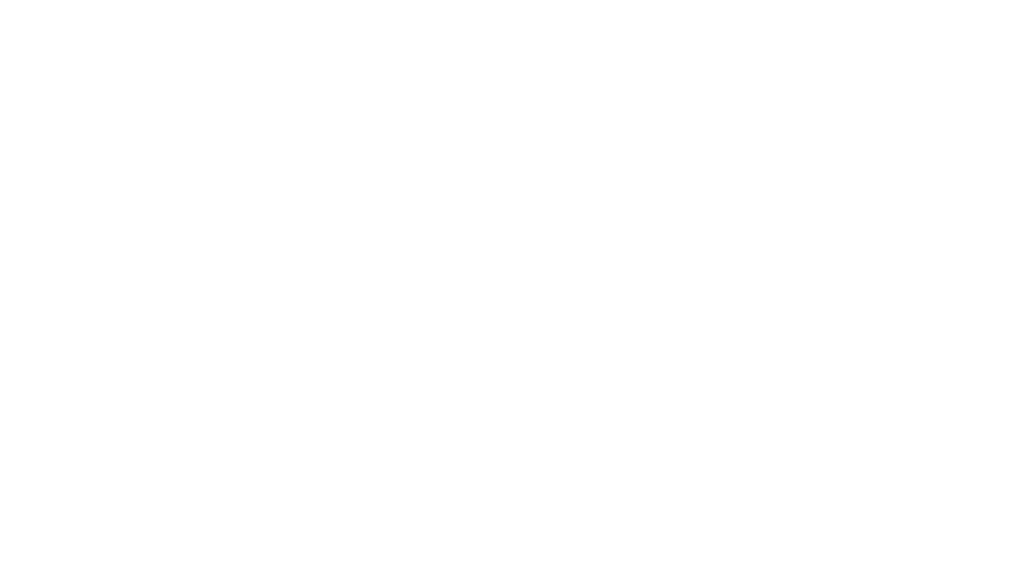
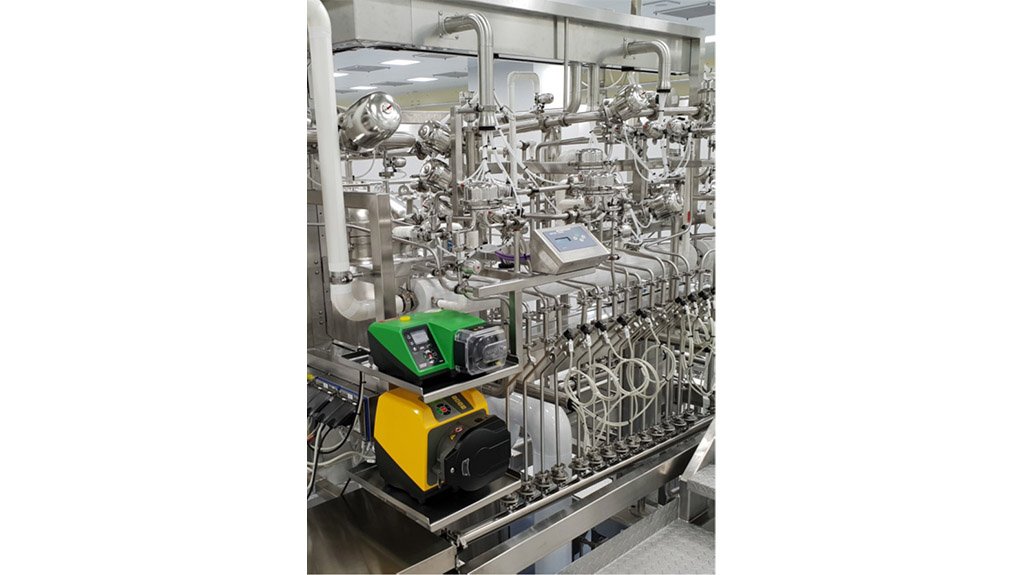
TECHNOLOGY SHAKE UP Stainless steel is not dead nor dying, but the emergence of new technology continues to shake up the biopharmaceutical industry
Global engineering company Watson-Marlow Fluid Technology Group (WMFTG) predicts a hybrid bioprocessing future, where tried and trusted stainless steel systems are seamlessly integrated with single-use technology.
This flexible approach will enable contract manufacturing organisations (CMOs) and biopharmaceuticals alike to find the ideal solution for their therapeutics in the best of both worlds, say sustainable engineering, architecture, construction and consulting solutions provider CRB director Marc Pelletier and Mark Embury of specialist valve manufacturer for bioprocessing applications ASEPCO, part of WMFTG, in an article titled ‘ Watson-Marlow on the Future of Stainless Steel in Bioprocessing’.
“We see this already in sampling systems, where a customer may use single-use sampling bags with a stainless steel valve. The customer reduces the cost of the single-use sampling system, which might only service five sampling bags, by using a semi-permanent one.”
Stainless steel is not dead nor dying, but the emergence of new technology continues to shake up the industry, calling on engineers to be more creative, to pave the way for smarter, more personalised manufacturing techniques and, above all, to develop more effective and inexpensive therapies.
In the past 15 years, the biopharmaceutical industry has seen a steady uptake in the use of single-use technology in bioprocessing, say Pelletier and Embury.
A recent report by biotechnology, pharmaceutical and healthcare publishing and market information service provider BioPlan Associates on biopharmaceutical manufacturing relayed that the most critical reasons for using single-use technology were to eliminate cleaning requirements, reduce capital investment in facility and equipment, avoid costs associated with system redesign and modifications, and decrease the risk of product crosscontamination.
“Clearly, single-use technology is the ideal choice for specific applications, some of which are setting the theme for the future of biopharmaceutical production. In recent years, we have seen huge growth in small-scale manufacturing processes, such as advanced therapy medicinal products.
“The success of therapies, such as [chimeric antigen receptor T-cell therapy], will surely attract greater attention and investment in these types of manufacturing processes, and where manufacturers are designing systems to be taken out in the field, in war zones or in disaster areas, a closed, wholly disposable system is essential,” state Pelletier and Embury.
Single-use technology is being developed for applications from upstream mixing and bioreaction to downstream perfusion and chromatography and is hailed as the only way to achieve personalised medicine and continuous processing.
Pelletier and Embury note that single-use technology has been viewed by many as the holy grail of manufacturing, promising fast process setup, low upfront capital investment, reduced maintenance costs, more flexible manufacturing layouts and a reduction in validation times.
“For CMOs, single-use systems are particularly appealing as clients often demand fast setup and an even faster production rate. By throwing out the previous system and replacing [it with a new one] for each client, CMOs can give assurance that there will be no cross-contamination, even when timescales are tight.”
However, an indication emerged in the BioPlan Associates report that might signal a shifting view towards single-use technology.
Between 2016 and 2018, a 13% decline was noted in ‘reducing capital investment in facility and equipment’ as a reason for using single-use technology.
“This hints at a potential problem with single-use equipment. Although this technology may have a lower initial capital cost, it can often have a much higher operational cost. You might remove a large portion of your cleaning and validation budget, but you’ll be signing up to an ongoing consumables plan that will tie you to an individual supplier,” explain Pelletier and Embury.
Surety of supply is a critical consideration. Can a secure and steady feed of consumables be guaranteed when needed? If a single-source supplier was to cease trading, could the transfer to an alternative system be undertaken without risking the product or critical deadlines?
Single-use technology is still a new industry, state Pelletier and Embury.
“Chromatography and perfusion stages are still widely dominated by stainless-steel equipment and although there are innovative new products being released regularly, some stages of bioprocessing simply cannot be carried out as effectively as they can with a stainless-steel system. In fact, in conversations with our clients, we find that downstream processing is much less likely to be provided by single-use technology for that very reason.”
But this is also evident in upstream processing.
Single-use bioreactor bags are only available up to 4 000 ℓ. Anything more than that, and stainless steel is the only way to go, say Pelletier and Embury.
Comments
Press Office
Announcements
What's On
Subscribe to improve your user experience...
Option 1 (equivalent of R125 a month):
Receive a weekly copy of Creamer Media's Engineering News & Mining Weekly magazine
(print copy for those in South Africa and e-magazine for those outside of South Africa)
Receive daily email newsletters
Access to full search results
Access archive of magazine back copies
Access to Projects in Progress
Access to ONE Research Report of your choice in PDF format
Option 2 (equivalent of R375 a month):
All benefits from Option 1
PLUS
Access to Creamer Media's Research Channel Africa for ALL Research Reports, in PDF format, on various industrial and mining sectors
including Electricity; Water; Energy Transition; Hydrogen; Roads, Rail and Ports; Coal; Gold; Platinum; Battery Metals; etc.
Already a subscriber?
Forgotten your password?
Receive weekly copy of Creamer Media's Engineering News & Mining Weekly magazine (print copy for those in South Africa and e-magazine for those outside of South Africa)
➕
Recieve daily email newsletters
➕
Access to full search results
➕
Access archive of magazine back copies
➕
Access to Projects in Progress
➕
Access to ONE Research Report of your choice in PDF format
RESEARCH CHANNEL AFRICA
R4500 (equivalent of R375 a month)
SUBSCRIBEAll benefits from Option 1
➕
Access to Creamer Media's Research Channel Africa for ALL Research Reports on various industrial and mining sectors, in PDF format, including on:
Electricity
➕
Water
➕
Energy Transition
➕
Hydrogen
➕
Roads, Rail and Ports
➕
Coal
➕
Gold
➕
Platinum
➕
Battery Metals
➕
etc.
Receive all benefits from Option 1 or Option 2 delivered to numerous people at your company
➕
Multiple User names and Passwords for simultaneous log-ins
➕
Intranet integration access to all in your organisation