Strategic approach enables effective dewatering
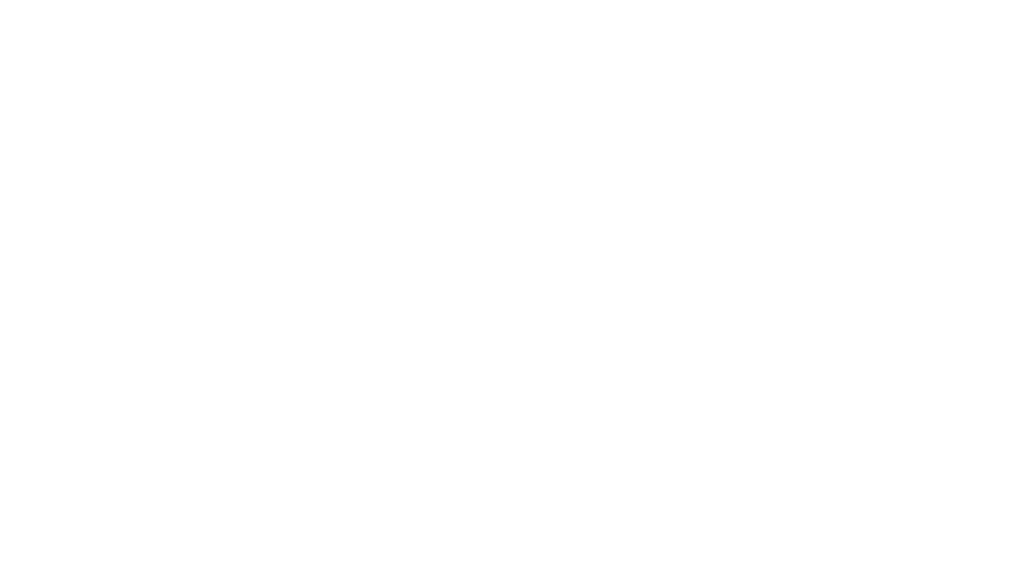
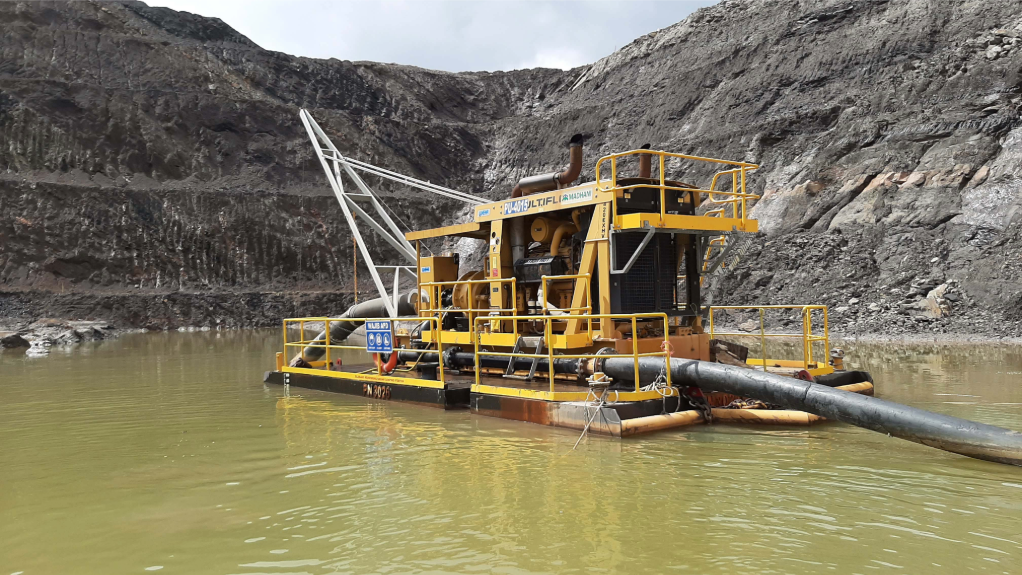
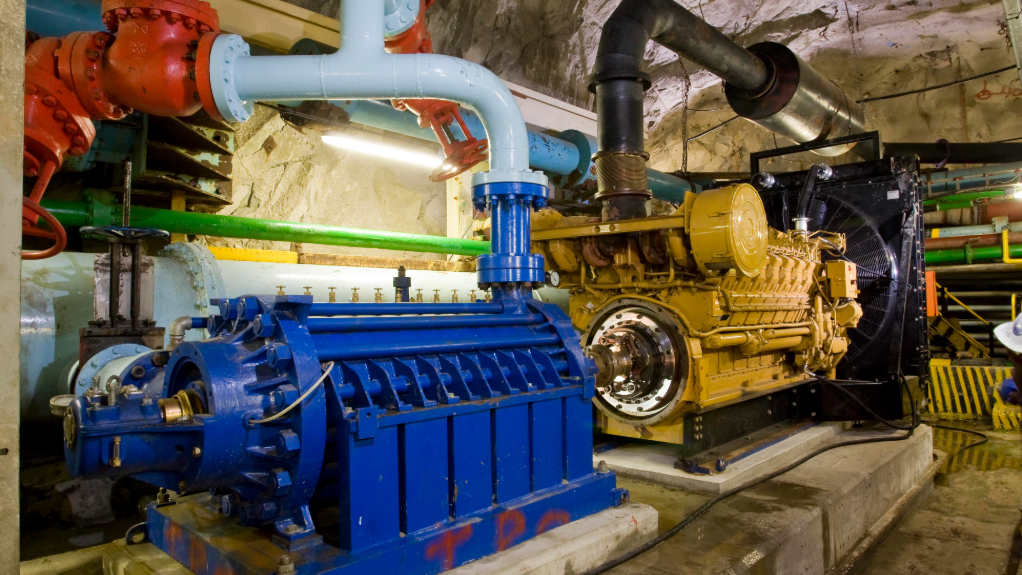
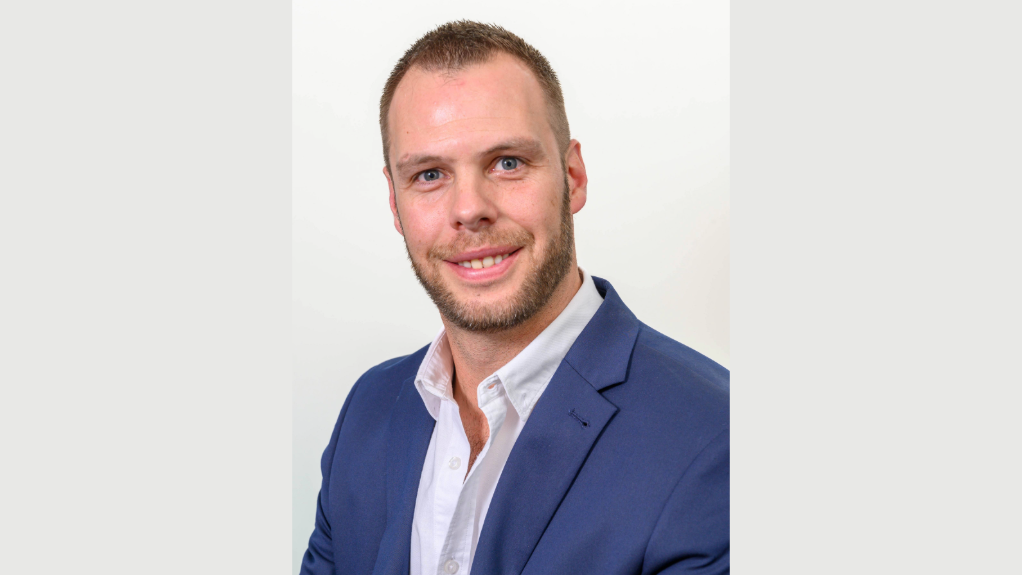
FLEXIBLE SOLUTION The Multiflo diesel driven pontoon offers a flexible, mobile dewatering solution
IDEAL DEWATERING SOLUTION Weir’s Envirotech multistage dewatering pump is ideal for dewatering underground site requirements
MARNUS KOORTS Improper planning often leads to a situation where the cost of peripheral equipment can far exceed the cost of the pump itself
A key challenge in dewatering operations that are electrically operated lies within the interfacing, particularly when dealing with pumps at remote mining operations. This challenge involves the design of a flexible electrical power distribution network, within an active mining operation, that can accommodate the changing landscape, owing to the extraction of the orebody.
These requirements add both complexity and cost to the system.
Mining technology and original-equipment manufacturer Weir pumps GM for Africa Marnus Koorts explains that improper planning in this regard often leads to a situation where the cost of peripheral equipment, such as transformers, cables and other electrical infrastructure, can far exceed the cost of the pump itself.
To mitigate this, it is often required to consider these solutions when designing the original plant. One way that Weir works around this, is to offer diesel-powered pumps as an alternative, providing mobility and flexibility. However, Koorts cautions that diesel systems come with their own costs and maintenance requirements.
For dewatering solutions to be truly effective, he stresses the importance of understanding the specific needs of each mine. For example, some mines benefit from continuously operating pumps, while others use intermittent systems that activate only during periods of heavy rainfall.
Another key point emphasised by Koorts is that dewatering is often treated as an afterthought by mining operations.
“People don’t think about it, and then you wake up one day, and your pits have become flooded, halting mining operations. Reactive dewatering, rather than proactive planning, leads to hastily implemented solutions that may not be the most efficient or cost-effective,” he adds.
The lack of planning, Koorts explains, results in mines reverse-engineering dewatering systems into existing infrastructure – a process that can be both difficult and expensive.
Without proper foresight, mines often have to deploy temporary solutions to address flooding, only to replace them with more suitable systems later. This piecemeal approach not only incurs additional costs but also leads to inefficiencies that can hamper the overall operation.
Given that unexpected water ingress is a significant challenge in mining operations, it often brings production to a complete halt. This issue is especially pronounced in regions such as West Africa, where rainfall is frequently excessive.
Consequently, Weir provides a variety of bespoke solutions tailored to the unique challenges faced by different mining operations, he tells Engineering News.
He highlights the company’s pontoon- based pump system designed for opencast mines.
The pontoon floats on water, and the pump activates automatically when it starts to rise with increasing water levels. This allows for an efficient, low-maintenance solution that only operates when needed, reducing wear and energy consumption.
Pontoons are particularly effective in areas where water tends to accumulate at the lowest points of the mine, making them ideal for managing varying water levels, Koorts notes.
In underground mining operations, pontoons and automated systems are equally valuable.
Shafts often include designated water- holding areas, where pontoons can be deployed to manage the accumulated water more effectively than fixed-position pumps.
However, while the correct pumping application is crucial, Koorts emphasises that planning is equally critical, especially as mines expand over time.
“What we often find is that one pump might be the best solution today, but in two or three years, the requirements will change,” he says.
To accommodate this, Weir works closely with clients to forecast their future needs and plan dewatering systems that can scale with the mine’s growth.
Bespoke Solutions
Weir has developed customised solutions for specific industries and regions, including diamond and copper producers in West and Central Africa. In some regions, dewatering systems need to account for complex pit structures, where water may need to be moved across rolling hills and varying elevations. In other areas, mines face chronic water surpluses that demand continuous, high-capacity dewatering.
Koorts describes a solution Weir implemented for a diamond producer, where multiple booster stations were strategically placed to move water across challenging terrain.
In contrast, a copper mine in Central Africa faced constant flooding owing to the region’s water surplus. Weir developed a phased solution that included pontoons and booster pumps to transfer water out of the mine in a responsible manner.
He adds that, while opencast mines face flooding from heavy rain, underground mines have their own persistent challenges.
Continuous water seepage into underground operations requires dedicated dewatering solutions to prevent mining tunnels from filling with water, even in the absence of rainfall.
Koorts highlights the importance of backup power systems to ensure dewatering pumps continue to function during power outages.
Experience and Expertise
One of the key advantages that Weir brings to the table is its deep experience in designing and implementing dewatering solutions, Koorts states – “you pay for experience”. He adds that, while the pumps themselves are relatively inexpensive, the knowledge required to properly integrate them into a mining operation is invaluable.
For example, incorrectly placing a pontoon can lead to additional costs for walkways and other infrastructure, which can exceed the cost of the pump.
Weir’s team has developed systems that allow for easy maintenance of pontoons in remote locations, where cranes or other heavy equipment may not be available. These solutions, developed through years of trial and error, offer clients the assurance that their dewatering systems will continue to operate smoothly, even in the most challenging environments.
Effective dewatering through proper pumping systems is therefore essential for the success of mining operations.
With proper planning, tailored solutions and expert implementation, Weir helps its clients maintain operational continuity and avoid the costly consequences of unplanned water ingress, Koorts concludes.
Comments
Announcements
What's On
Subscribe to improve your user experience...
Option 1 (equivalent of R125 a month):
Receive a weekly copy of Creamer Media's Engineering News & Mining Weekly magazine
(print copy for those in South Africa and e-magazine for those outside of South Africa)
Receive daily email newsletters
Access to full search results
Access archive of magazine back copies
Access to Projects in Progress
Access to ONE Research Report of your choice in PDF format
Option 2 (equivalent of R375 a month):
All benefits from Option 1
PLUS
Access to Creamer Media's Research Channel Africa for ALL Research Reports, in PDF format, on various industrial and mining sectors
including Electricity; Water; Energy Transition; Hydrogen; Roads, Rail and Ports; Coal; Gold; Platinum; Battery Metals; etc.
Already a subscriber?
Forgotten your password?
Receive weekly copy of Creamer Media's Engineering News & Mining Weekly magazine (print copy for those in South Africa and e-magazine for those outside of South Africa)
➕
Recieve daily email newsletters
➕
Access to full search results
➕
Access archive of magazine back copies
➕
Access to Projects in Progress
➕
Access to ONE Research Report of your choice in PDF format
RESEARCH CHANNEL AFRICA
R4500 (equivalent of R375 a month)
SUBSCRIBEAll benefits from Option 1
➕
Access to Creamer Media's Research Channel Africa for ALL Research Reports on various industrial and mining sectors, in PDF format, including on:
Electricity
➕
Water
➕
Energy Transition
➕
Hydrogen
➕
Roads, Rail and Ports
➕
Coal
➕
Gold
➕
Platinum
➕
Battery Metals
➕
etc.
Receive all benefits from Option 1 or Option 2 delivered to numerous people at your company
➕
Multiple User names and Passwords for simultaneous log-ins
➕
Intranet integration access to all in your organisation