Growth in laser gas noted by company
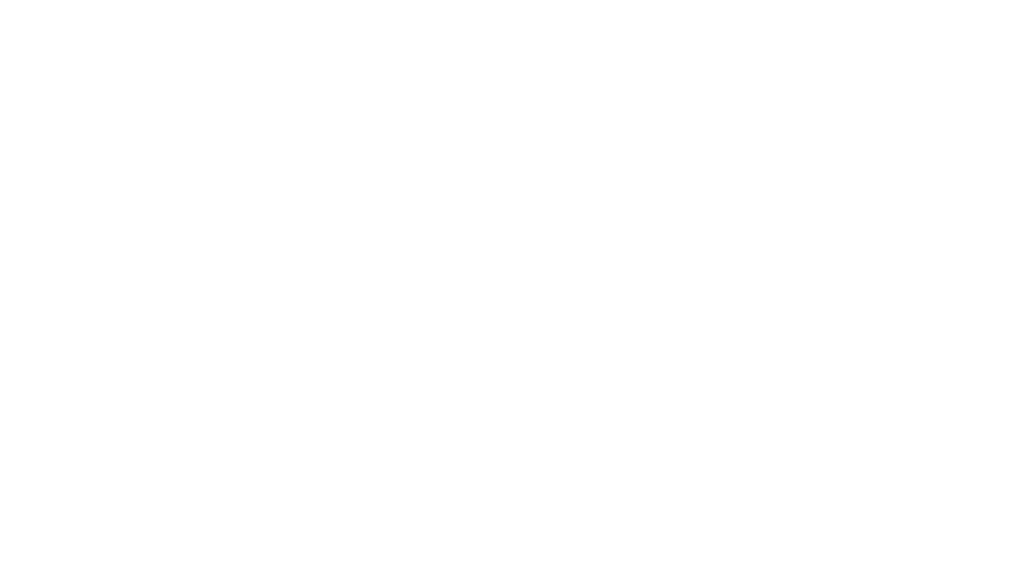
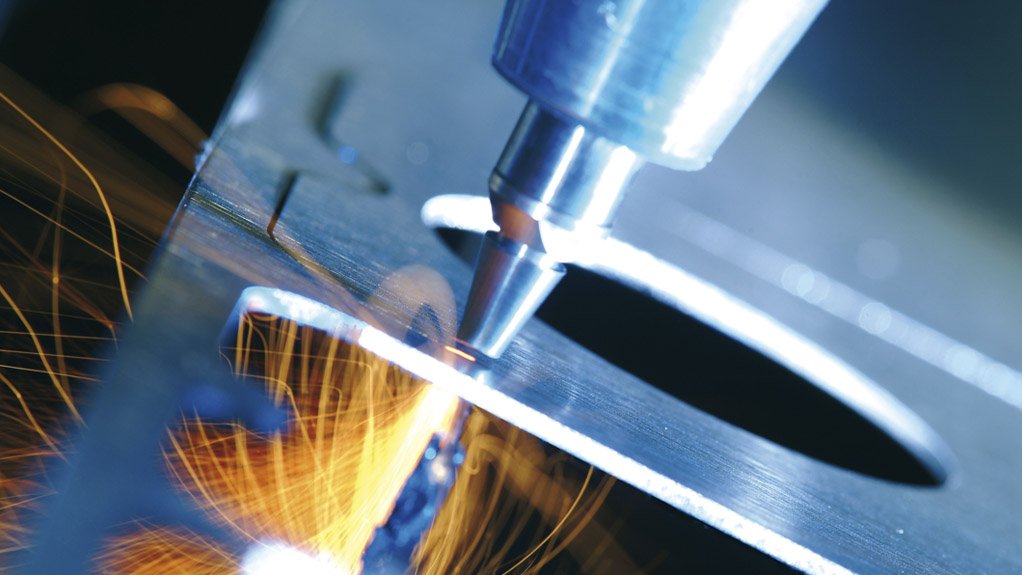
CUTTING EDGE Afrox started penetrating the laser cutting market around 2005 and its growth in this field and of the market share for laser cutting has dramatically increased since then
Laser application technology has seen substantial progress and development since the invention of the laser in the 1960s, and gases and welding products supplier African Oxygen (Afrox) has experienced market growth over the years owing to its development of laser gases for different applications in the market.
“Our specialist expertise enables Afrox to advise on every aspect of laser use, whether it is assist gases, supply mode or laser mixed gases and supply,” says Afrox cutting, heating and safety application development manager Hennie van Rhyn.
Afrox, a member of The Linde Group, started penetrating the laser cutting market around 2005 and the company’s growth in this field and of the market share for laser cutting has dramatically increased since then. Afrox has the latest high-quality laboratory with highly skilled operators to mix any lasermix requirement to meet required tolerances for any original-equipment manufacturer-supplied laser machine.
This includes four part mixes for new 6 kW high-powered carbon dioxide (CO2) lasers in South Africa. Afrox is licensed to sell five-part mixed laser gases in South Africa, which are competitively priced, says Van Rhyn.
The recovery period after the global economic downturn in 2008 witnessed a step-change in laser technology for laser cutting and welding: the fibre and fibre-delivered laser. It was evidenced that laser and fibre technology originally developed for telecoms applications was able to handle the high power needed for cutting and welding. The advance of these lasers for metal fabrication was driven by the development of cost-effective, reliable high-power diode lasers needed to ‘pump’ fibre lasers.
The gap in investment in new equipment by industry during 2008/9 provided the window for the fibre-delivered laser manufacturers to enter the market with new, attractive lasers showing rapid growth in uptake and even replacing old CO2 laser machines for cutting, and especially welding.
Fibre-delivered lasers have a much shorter wavelength than CO2 lasers and, apart from the major advantage that this wavelength can be transmitted by optical fibre, there is also another significant difference, caused by the wavelength, in how these two types of lasers interact with metal, both for cutting and welding.
At the shorter wavelength of the fibre-delivered laser, steel has a much smaller so-called Brewster angle than the CO2 laser. The consequence of this is that, when cutting thin steel sheet with nitrogen, the radiation of the fibre-delivered laser is used much more efficiently than the radiation of a CO2 laser.
Therefore, a fibre-delivered laser cuts thin sheet up to three times faster than a CO2 laser of the same power.
However, in order to remove the molten metal effectively at this very high cutting speed, a higher nitrogen pressure is required. Moreover, as a consequence of the smaller Brewster angle, the cut front is less steeply inclined and therefore a slightly larger nozzle must be used. The result of these two factors is that nitrogen consumption per hour is higher, but nitrogen consumption per metre of cut length is very similar.
Although not available yet in South Africa, an investment programme over the last three years has seen the introduction of 300 bar nitrogen cylinder bundles in the industrial hubs of Pune and Bangalore, in India. Compared with a 200 bar bundle, the 300 bar bundle holds 50% more nitrogen.
Further, when the 200 bundle has reached a pressure of 40 bar, it needs to be replaced with a full one, leaving 20% of the nitrogen unused.
Comments
Press Office
Announcements
What's On
Subscribe to improve your user experience...
Option 1 (equivalent of R125 a month):
Receive a weekly copy of Creamer Media's Engineering News & Mining Weekly magazine
(print copy for those in South Africa and e-magazine for those outside of South Africa)
Receive daily email newsletters
Access to full search results
Access archive of magazine back copies
Access to Projects in Progress
Access to ONE Research Report of your choice in PDF format
Option 2 (equivalent of R375 a month):
All benefits from Option 1
PLUS
Access to Creamer Media's Research Channel Africa for ALL Research Reports, in PDF format, on various industrial and mining sectors
including Electricity; Water; Energy Transition; Hydrogen; Roads, Rail and Ports; Coal; Gold; Platinum; Battery Metals; etc.
Already a subscriber?
Forgotten your password?
Receive weekly copy of Creamer Media's Engineering News & Mining Weekly magazine (print copy for those in South Africa and e-magazine for those outside of South Africa)
➕
Recieve daily email newsletters
➕
Access to full search results
➕
Access archive of magazine back copies
➕
Access to Projects in Progress
➕
Access to ONE Research Report of your choice in PDF format
RESEARCH CHANNEL AFRICA
R4500 (equivalent of R375 a month)
SUBSCRIBEAll benefits from Option 1
➕
Access to Creamer Media's Research Channel Africa for ALL Research Reports on various industrial and mining sectors, in PDF format, including on:
Electricity
➕
Water
➕
Energy Transition
➕
Hydrogen
➕
Roads, Rail and Ports
➕
Coal
➕
Gold
➕
Platinum
➕
Battery Metals
➕
etc.
Receive all benefits from Option 1 or Option 2 delivered to numerous people at your company
➕
Multiple User names and Passwords for simultaneous log-ins
➕
Intranet integration access to all in your organisation