Sustainable construction ethos prioritised by manufacturer
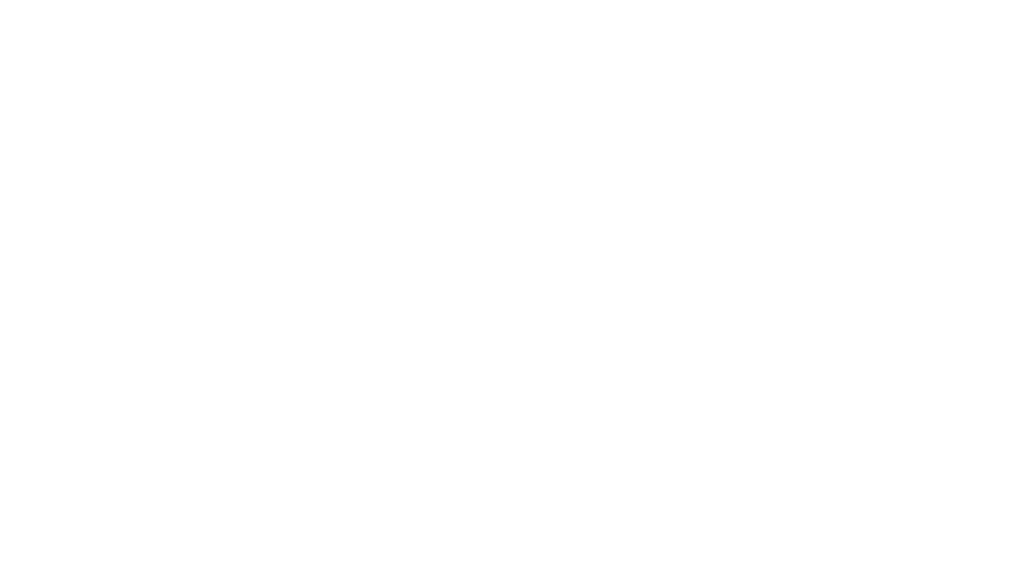
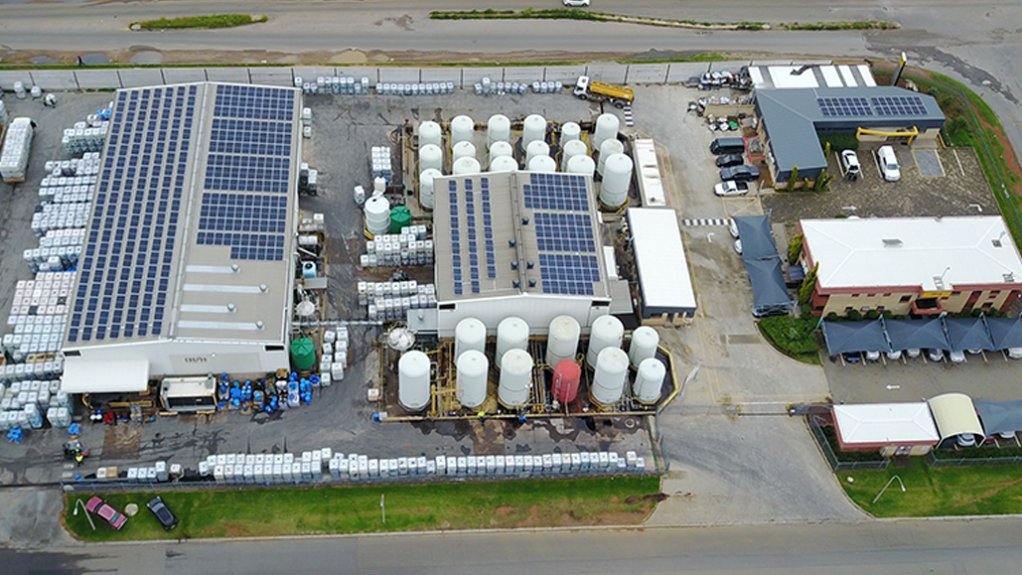
ENERGY EFFICIENCY The solar installation provides about 70% of the facility’s energy requirement
Cement additive manufacturing company CHRYSO Southern Africa has installed a solar electricity generating system at its Jet Park manufacturing facility, in Gauteng; this forms part of the company’s efforts to lower its carbon footprint.
The installation was completed in January and consists of 393 solar panels with a capacity of 400 W each. The panels can collectively generate 157 kWp through five 27.6 K inverters.
CHRYSO Southern Africa CEO Norman Seymore tells Engineering News that the estimated yearly energy output of the system is 239.13 MWh, providing about 70% of the company’s historical energy requirement. The remaining 30% will continue to be sourced from the grid.
Previously, the company implemented a series of wastewater treatment systems to recycle and, thereby, reduce the amount of wastewater produced at the plant. Several wastewater catchment areas were also constructed to ensure that wastewater is treated to an acceptable standard before being discharged.
Seymore explains that these measures are not strictly mandated according to municipal or government regulations, but CHRYSO Southern Africa has implemented them in accordance with the company’s global efforts to contribute to a more sustainable construction sector.
“We are also aiming to ensure that our packaging materials and containers are recyclable and reusable. We deliver much of our products in bulk, but where we deliver 1 000 𝓵 containers or 200 𝓵 drums, for example, we make use of recyclable materials,” he says.
Sustainable Trend
Seymore says the company’s efforts to reduce its manufacturing footprint is tied to its chemicals additive product offering, which supports the construction industry’s demand for sustainable construction materials.
CHRYSO’s products serve to reduce carbon emissions downstream by improving cement and concrete performance, thereby reducing energy consumption in cement manufacture.
For example, the company’s newly patented Innovative Cement Activation and Rheology Enhancement (ICare) strength enhancement technology is designed with this in mind. The ICare technology is being subjected to several long-term trials in South Africa.
“Covid-19 delayed the rollout of the ICare product on a large scale, but the interest in the product has been significant. We believe the penetration of the product into the market will accelerate quickly,” Seymore says.
The technology provides extra activation for cements manufactured from challenging process (CP) configurations and in vertical roller mills (VRMs), which are specific processes where the performance of conventional strength enhancers is limited.
Seymore explains that the ICare technology empowers cement reactivity by creating a synergistic effect between chemical and mechanical activation to further increase cement strength at all ages while optimising the clinker factor.
As such, the technology has been developed into two ranges – the ICare CP and the ICare VRM.
The ICare VRM additive range enables cement manufacturers to achieve higher cement compressive strengths by overtaking process limitations inherent in VRMs.
“Using conventional high-performance strength enhancers can lead to process limitations. These side effects are often controlled by reducing the dosing rate of cement additive. However, this leads to a lack of grinding aid in cement to achieve all the benefits from the chemicals,” explained CHRYSO cement technical director Laurent Guillot in a statement issued in September last year.
He said such limitations were further emphasised with strength enhancers that were used for their combined properties as process improvers and chemical activators to boost cement strengths.
“In such a situation, the appropriate balance between process sensitivity – especially with process differential pressures – and cement reactivity can be difficult, if not impossible, to achieve,” he added.
The ICare VRM product allows for the full optimisation of mill stability by reducing pressure changes and vibrations in the process.
Moreover, it causes an improvement of cement reactivity by reducing water injection while causing an overall increase of cement compressive strengths at all ages to significantly reduce the clinker factor.
A reduction in clinker content needed in cement translates to an upstream reduction in clinker manufacture, which, in turn, lowers emissions.
“The cement manufacturing industry is strongly motivated to reduce carbon emissions, owing to the carbon tax levied by government,” says Seymore.
He adds that there is an increasingly strong influence from consulting engineers and architects towards more sustainable construction; “therefore, we are seeing a growing market for our chemical additive products, which allow for cement and concrete to be more sustainable”.
The ICare CP overtakes process limitations to maximise cement activation potential, resulting in an improved cement fineness and particle-size distribution.
Seymore explains that, at different stages of the ball mill process, a significant increase in productivity is achieved.
“Better cement powder transport properties enable the plant to maintain high productivity while reducing maintenance costs,” he says.
Using chemical additives actually reduces the cost of cement – despite the additive being an additional input cost – because it enables manufacturers to use less cementitious material to achieve the desired strength or performance, Seymore concludes.
Comments
Press Office
Announcements
What's On
Subscribe to improve your user experience...
Option 1 (equivalent of R125 a month):
Receive a weekly copy of Creamer Media's Engineering News & Mining Weekly magazine
(print copy for those in South Africa and e-magazine for those outside of South Africa)
Receive daily email newsletters
Access to full search results
Access archive of magazine back copies
Access to Projects in Progress
Access to ONE Research Report of your choice in PDF format
Option 2 (equivalent of R375 a month):
All benefits from Option 1
PLUS
Access to Creamer Media's Research Channel Africa for ALL Research Reports, in PDF format, on various industrial and mining sectors
including Electricity; Water; Energy Transition; Hydrogen; Roads, Rail and Ports; Coal; Gold; Platinum; Battery Metals; etc.
Already a subscriber?
Forgotten your password?
Receive weekly copy of Creamer Media's Engineering News & Mining Weekly magazine (print copy for those in South Africa and e-magazine for those outside of South Africa)
➕
Recieve daily email newsletters
➕
Access to full search results
➕
Access archive of magazine back copies
➕
Access to Projects in Progress
➕
Access to ONE Research Report of your choice in PDF format
RESEARCH CHANNEL AFRICA
R4500 (equivalent of R375 a month)
SUBSCRIBEAll benefits from Option 1
➕
Access to Creamer Media's Research Channel Africa for ALL Research Reports on various industrial and mining sectors, in PDF format, including on:
Electricity
➕
Water
➕
Energy Transition
➕
Hydrogen
➕
Roads, Rail and Ports
➕
Coal
➕
Gold
➕
Platinum
➕
Battery Metals
➕
etc.
Receive all benefits from Option 1 or Option 2 delivered to numerous people at your company
➕
Multiple User names and Passwords for simultaneous log-ins
➕
Intranet integration access to all in your organisation