Water treatment prevents boiler damage
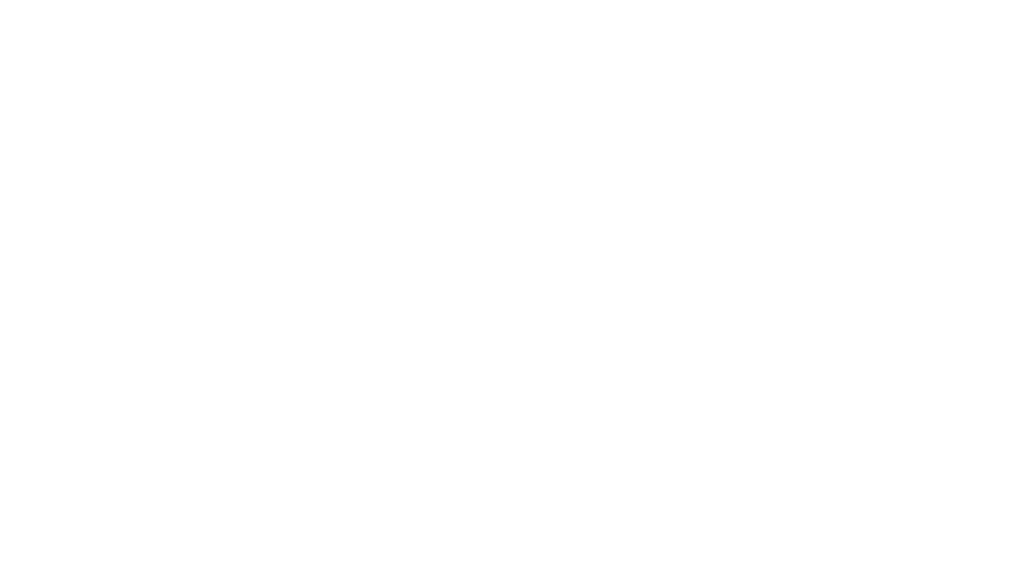
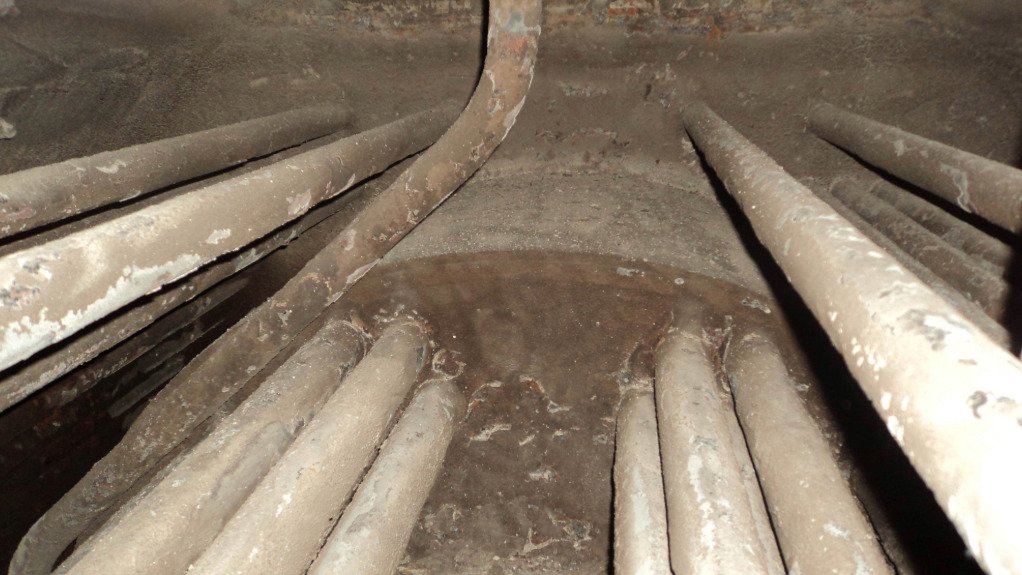
SCALED UP RISKS Increased scale build-up can contribute to increased fuel consumption and reduced boiler lifespan
Many companies often forgo water treatment when maintaining boilers to reduce their operating costs and meet production demands, but ignoring water treatment can contribute to boiler failure, resulting in boiler downtime and costly repairs, says boiler manufacturer Allmech MD Lionel Maasdorp.
By law, boilers should be serviced yearly, with a full-service inspection completed every three years, depending on the Act and other regulatory requirements governing the industry for which the boiler was installed.
“The problem is that the process is time consuming and, therefore, many companies [authorise] a full service only when they have to, which means they could run for months or even years with an inefficient boiler,” he adds.
Further, Maasdorp point out that, while the Department of Employment and Labour has inspectors for manufacturing plants, some offices are not as “proactive” as they could be.
He notes that a comprehensive boiler maintenance programme that includes water treatment can result in lower maintenance costs and downtime in the long term, consequently ensuring that boilers operate reliably, along with improved equipment longevity and safety.
“If one considers the yearly cost of water treatment chemicals and services on industrial boilers, such a programme would account for only a small percentage of the equipment costs,” Maasdorp elaborates.
Preventable Wear
A significant result of not prioritising water treatment is increased scale build-up, which can contribute to increased fuel consumption and reduced boiler lifespan.
Scale is calcium or magnesium detectable as a dissolved mineral in the water. When these minerals come into contact with a hot surface, they adhere to the hot surface and ‘coat’ it.
Scale build-up then acts as an insulator on the surface, resulting in heat not being transferred to the water or product efficiently. Consequently, the boiler must produce more heat to heat a product to the required temperature, which, in turn, requires more fuel, adds Maasdorp.
“As a rule of thumb, 1 mm of scale build-up can increase fuel consumption by 2%. If you have 5 mm of scale build-up on the boiler tubes, you might be paying an extra 10% on your monthly fuel bills.”
Well-maintained boilers, therefore, require less energy to operate, resulting in significant cost savings.
“In extreme cases, when the scale prevents the heat from being dissipated into the water, the resulting excessive heat can cause mechanical failures, such as bent tubes or even a melted flue,” he adds.
Further, significant scale build-up increases the risk of under-deposit pitting. This refers to a small crater that forms under the scale, which reduces boiler lifespan.
To prevent scale formation, companies should firstly evaluate the water composition of the feeding system. Depending on the result, companies will filter and/or pre-soften the water – in the case of ‘hard’ water, which has a high concentration of calcium carbonate and other ions – before feeding it to the boiler to eliminate not only scale formation but also chemical scale inhibitors inside the boiler.
Maasdorp suggests chemical cleaning and neutralisers to dissolve the scale and clean the tubes. However, a boiler’s service must be more comprehensive if there is excessive scale presence, even if chemical cleaners are used, and can increase the cost of the service.
When boilers function with precautions to limit additional scale build-up, the scale will dissolve slowly under the correct pH conditions.
Proper water treatment can also mitigate boiler corrosion, and while this cannot be prevented, mitigation can slow the corrosion rate, he adds.
Corrosion refers to the degradation of the material, resulting in its becoming thinner and, therefore, weaker over time. This poses a risk, as the boiler could rupture if the material becomes too thin.
It is caused by the interaction of water chemistry, the environment of the facility, operational procedures and the materials used in the construction of the system. Dissolved gases in the boiler, such as oxygen, carbon dioxide and ammonia, will aggravate corrosion.
Oxygen is the most “aggressive” gas in a boiler, but internal water treatment using chemicals in the feed water and raising the temperature can remove the oxygen, Maasdorp explains.
Effective Prevention
Key indicators of a boiler’s water treatment programme being ineffective include water hardness and pH abnormalities, Maasdorp says.
Water treatment strategies do not have to be changed often, unless there are abnormalities in production hours. Changes, such as additional shifts, could require a review of the softener size, while a change in hardness in the feed water, owing to a change in the supply line, requires that the softener size or the required settings be reviewed.
Maasdorp emphasises that companies should inform their supplier of changes that could affect equipment.
He recommends that Runxin valves, manufactured by equipment manufacturer Wenzhou Runxin Manufacturing Machine, be used as softener, filter and ball valves.
Maasdorp says the range is “reliable, easy to maintain and cost effective to repair” adding that, if properly maintained, these control valves on the softener, can be the “most effective portion of the treatment process”.
“At times a duplex softener with a Runxin automatic control valve will negate [having] to replace any equipment, especially if the abnormalities are short in duration,” he concludes.
Comments
Press Office
Announcements
What's On
Subscribe to improve your user experience...
Option 1 (equivalent of R125 a month):
Receive a weekly copy of Creamer Media's Engineering News & Mining Weekly magazine
(print copy for those in South Africa and e-magazine for those outside of South Africa)
Receive daily email newsletters
Access to full search results
Access archive of magazine back copies
Access to Projects in Progress
Access to ONE Research Report of your choice in PDF format
Option 2 (equivalent of R375 a month):
All benefits from Option 1
PLUS
Access to Creamer Media's Research Channel Africa for ALL Research Reports, in PDF format, on various industrial and mining sectors
including Electricity; Water; Energy Transition; Hydrogen; Roads, Rail and Ports; Coal; Gold; Platinum; Battery Metals; etc.
Already a subscriber?
Forgotten your password?
Receive weekly copy of Creamer Media's Engineering News & Mining Weekly magazine (print copy for those in South Africa and e-magazine for those outside of South Africa)
➕
Recieve daily email newsletters
➕
Access to full search results
➕
Access archive of magazine back copies
➕
Access to Projects in Progress
➕
Access to ONE Research Report of your choice in PDF format
RESEARCH CHANNEL AFRICA
R4500 (equivalent of R375 a month)
SUBSCRIBEAll benefits from Option 1
➕
Access to Creamer Media's Research Channel Africa for ALL Research Reports on various industrial and mining sectors, in PDF format, including on:
Electricity
➕
Water
➕
Energy Transition
➕
Hydrogen
➕
Roads, Rail and Ports
➕
Coal
➕
Gold
➕
Platinum
➕
Battery Metals
➕
etc.
Receive all benefits from Option 1 or Option 2 delivered to numerous people at your company
➕
Multiple User names and Passwords for simultaneous log-ins
➕
Intranet integration access to all in your organisation