‘Dry’ flue-gas desulphurisation possible on combustion installations
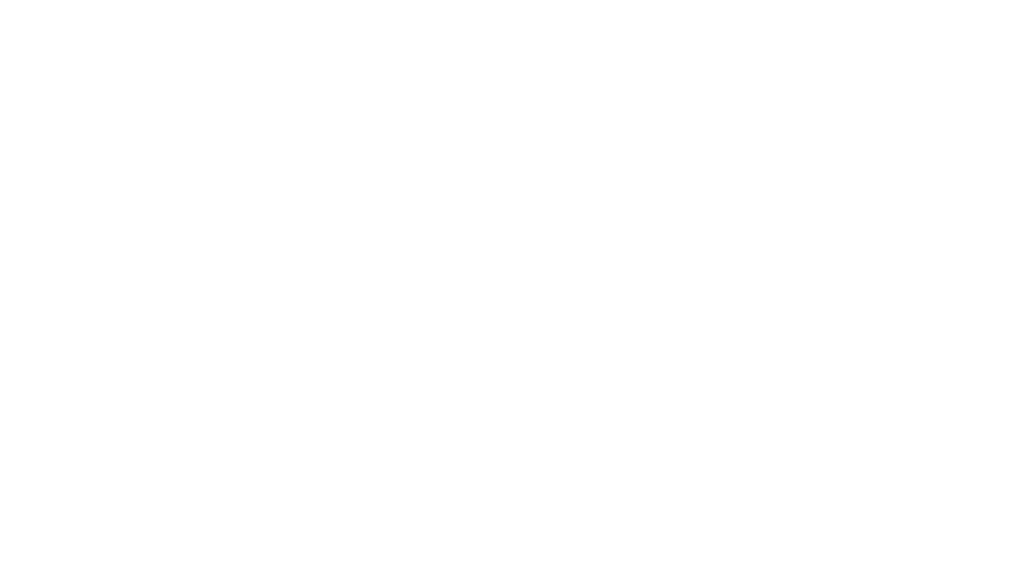
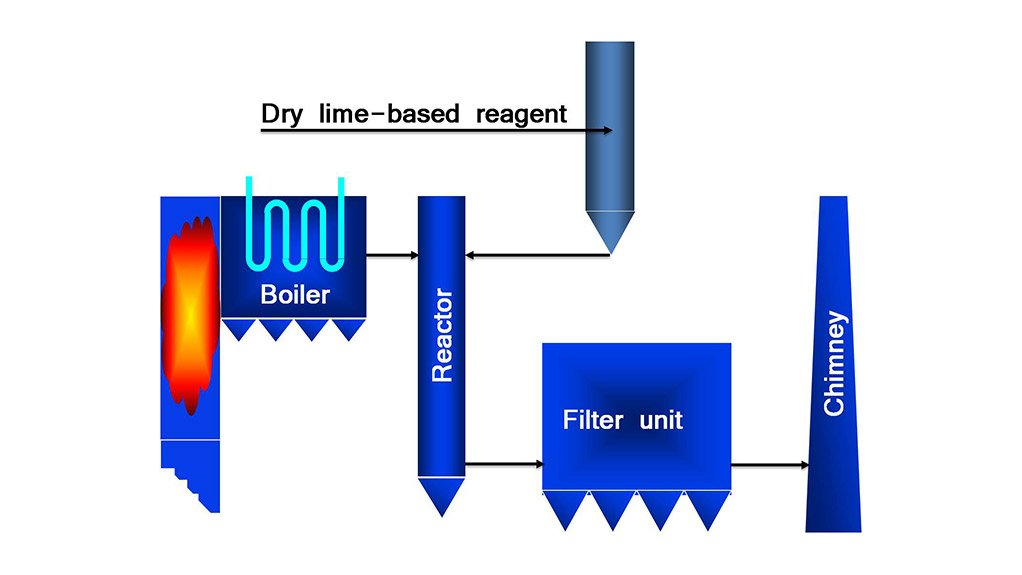
DRY FLUE-GAS DESULPHURISATION Slaked lime is injected as a dry powder into the boiler at high temperatures or at a lower temperature into a simple reactor along the flue gas duct to capture SOx pollutants
Adry flue-gas desulphurisation (dry FGD) system uses a lime-based reagent to remove sulphur oxides (SOx) from the flue gases of any combustion installation without using water, says gas and energy specialist engineering company Tractebel Engineering South Africa business development manager Yves Grofils.
The process uses calcium hydroxide, or Ca(OH)2 – a lime-based reagent with a large surface area – that is injected as a dry powder into the boiler at high temperatures or at a lower temperature into a simple reactor along the flue gas duct. The fine powder’s reactivity enables it to react more effectively with pollutants than conventional small surface area lime or crushed limestone, capturing up to 99% of sulphurous gas pollutants.
The dry FGD system does not require water to capture sulphurous gas emissions. The reaction forms gypsum (CaSO4 • 2H2O). The flue gases then pass through a conventional filtration process to remove particles before being sent to the chimney. The gypsum is removed along with the ash and dust.
The reagent is pneumatically transferred to injection lances as a powder and can be injected into the boiler or the reactor. The system can be designed to meet the process requirements of each combustion plant and can also accommodate multiple injection points – in the boiler and the reactor.
Using high surface area lime as a substitute to Ca(OH)2 enables significant reduction (up to 50%) of lime consumption for an identical result. This offsets the higher cost of the Ca(OH)2 reagent. An additional benefit is the significant reduction of the gypsum by-product to be disposed of after filtration, says Grofils.
“No major modifications to the existing flue gas ducts are required. This makes the dry FGD ideal to include in existing boiler retrofit programme. Further, the system can be trialled on a full-scale industrial basis before an investment decision needs to be made,” he avers.
South Africa is experiencing an electrical power crunch and many old power plants’ operations may be extended through refurbishment to reduce the possibility of rolling blackouts.
However, most coal-fired boilers and power plants were designed prior to modern air pollution control regulations and do not have adequate systems to reduce or eliminate pollutants from their emissions to comply with forthcoming legislation, says Grofils.
These plants often operate in areas where water is scarce or must be preserved for use by people or agriculture. Dry FGD process does not require water and does not require capital-intensive equipment investment, while the production loss during installation is minimal and maintenance costs low, making it a suitable technology for existing plants with an extended or uncertain operational life span, explains Grofils.
New environmental air pollution regulations should be promulgated during next year and brought into force by 2015. Most large combustion installations in South Africa do not comply with these regulations and will require upgrades to continue to operate lawfully, or be granted exemptions.
“Pollution has significant effects on human and animal health. Air pollution has been shown to exacerbate and increase respiratory diseases, while water pollution affects all animals and people living along watercourses. SOx reacts with moisture in the atmosphere to form acid rains that impact on agricultural and urban regions in South Africa,” notes Grofils.
Estimates show that there is not enough limestone in South Africa to treat the flue gases of the existing large combustion installations of the country. High specific surface area lime is a solution to avoid imports of limestone and, if there is sufficient demand in South Africa, the high surface area reagent can be produced locally, creating jobs and access to a new technology, he concludes.
Comments
Announcements
What's On
Subscribe to improve your user experience...
Option 1 (equivalent of R125 a month):
Receive a weekly copy of Creamer Media's Engineering News & Mining Weekly magazine
(print copy for those in South Africa and e-magazine for those outside of South Africa)
Receive daily email newsletters
Access to full search results
Access archive of magazine back copies
Access to Projects in Progress
Access to ONE Research Report of your choice in PDF format
Option 2 (equivalent of R375 a month):
All benefits from Option 1
PLUS
Access to Creamer Media's Research Channel Africa for ALL Research Reports, in PDF format, on various industrial and mining sectors
including Electricity; Water; Energy Transition; Hydrogen; Roads, Rail and Ports; Coal; Gold; Platinum; Battery Metals; etc.
Already a subscriber?
Forgotten your password?
Receive weekly copy of Creamer Media's Engineering News & Mining Weekly magazine (print copy for those in South Africa and e-magazine for those outside of South Africa)
➕
Recieve daily email newsletters
➕
Access to full search results
➕
Access archive of magazine back copies
➕
Access to Projects in Progress
➕
Access to ONE Research Report of your choice in PDF format
RESEARCH CHANNEL AFRICA
R4500 (equivalent of R375 a month)
SUBSCRIBEAll benefits from Option 1
➕
Access to Creamer Media's Research Channel Africa for ALL Research Reports on various industrial and mining sectors, in PDF format, including on:
Electricity
➕
Water
➕
Energy Transition
➕
Hydrogen
➕
Roads, Rail and Ports
➕
Coal
➕
Gold
➕
Platinum
➕
Battery Metals
➕
etc.
Receive all benefits from Option 1 or Option 2 delivered to numerous people at your company
➕
Multiple User names and Passwords for simultaneous log-ins
➕
Intranet integration access to all in your organisation