3D printing has huge potential to help decarbonise manufacturing
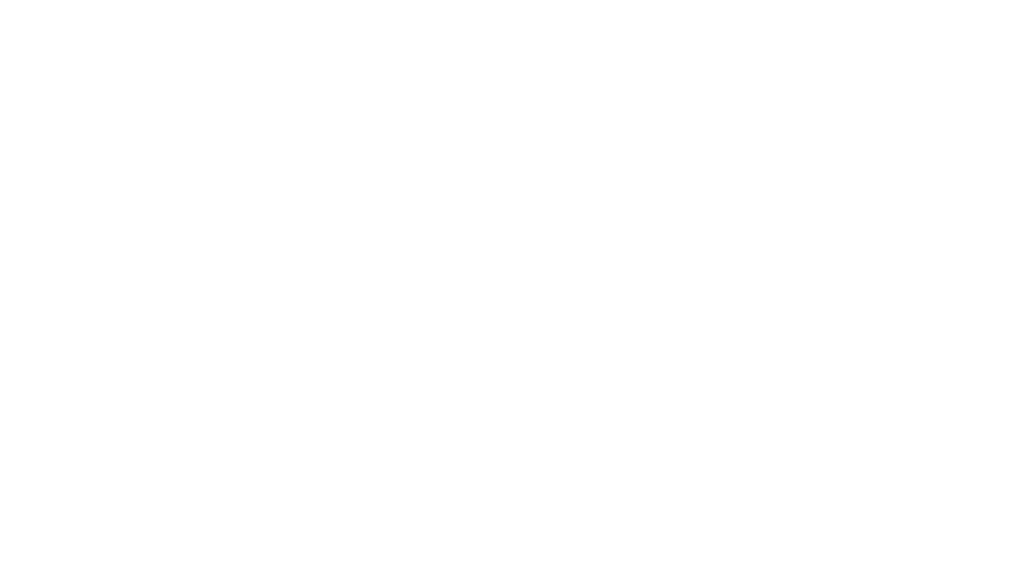
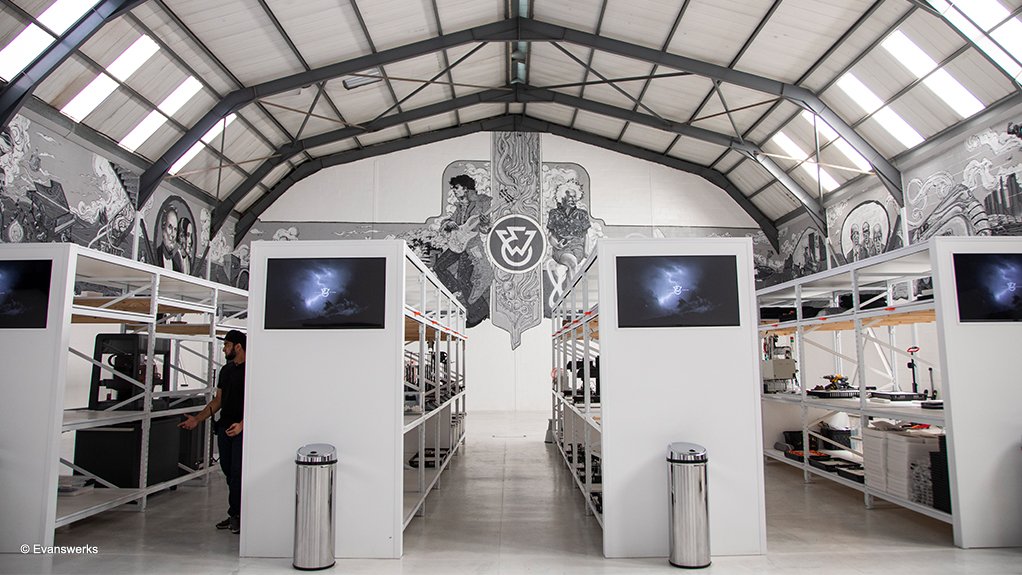
A 21st century green factory: inside the Evanswerks Labs production facility
Photo by Evanswerk Labs
Additive manufacturing (AM), popularly called three-dimensional (3D) printing, has an important role to play in greatly reducing the global manufacturing industry’s carbon emissions, Cape Town-based Evanswerks Labs co-founder and CEO Justin Evans tells Engineering News & Mining Weekly.
“3D printing is not zero-carbon but it produces a lot less carbon emissions than conventional manufacturing,” he points out.
Today, 3D printing can be done with metals, composites, polymers, ceramics and even biological materials. Regarding metals, a wide range can now be used – aluminium, cobalt chrome, copper, low-alloy steel, nickel-based superalloys, stainless steel and tool steel.
AM is massively more efficient than conventional manufacturing. Often, conventional manufacturing involves machining, in which time and energy are wasted in removing material to create the desired shape, a process which can also produce a lot of waste. Complex components often have to be assembled from a number of separate subcomponents. With 3D printing, all the energy goes into creating the component, which can usually be done as a single unit. This significantly reduces the energy required to manufacture something.
“The top five global industrial economies have a total gross domestic product of about $120-trillion,” he highlights. “Of this, 3D printing accounts for only 0.001%. The potential is huge. AM is part of decarbonising industry.”
The demand is certainly there. “We have so many customers that, after just over a month, we’re already at break-even,” he reports. “We’ll be profitable within another 45 days.”
However, he cautions that maximum effect requires a lot more than just adopting a technology.
“The mistake people make is they think that 3D printing alone is the answer. It isn’t. It’s the whole system around 3D printing, such as robotics, artificial intelligence, the people, and the implementation of kaizen principles. Kaizen is central to everything Evanswerks does.”
Kaizen is the philosophy that continuous small improvements in a process can lead to significant efficiencies. The concept is especially associated with Japanese companies (kaizen is a Japanese word), because they have been major adopters and successful appliers of the concept (which was actually developed in the US, but largely ignored there, at least until recently).
“Using kaizen, we have developed easy ways to deal with complex processes,” he stresses. “Also, kaizen processes mean that all tools are clearly labelled and kept in one place. We put kaizen notes on everything: what something is, what it does, where it is stored. Tools that are commonly used are duplicated. “The protective glasses used with our laser machines are kept alongside each laser machine, as are the other tools used with them. We make it look easy because of how hard our staff work on kaizen!” In just five weeks of operation, some 30 kaizen improvements have been made at the facility.
Evanswerks Labs’ Cape Town factory gets its energy from solar power, with lithium-ion battery backup, as 3D printing requires continuous power. The facility’s solar array has a capacity of about 60 kW/h, while the facility itself needs around 20 kW/h, of electricity. For a month it has been independent from national electricity utility Eskom and the power cuts it imposes on the country, called loadshedding.
Currently, the company cannot sell its surplus electricity to Cape Town, because, although its inverter is from an approved manufacturer, the model selected by Evanswerks is so new that it is not yet on the approved list. Once it is approved, the company will be able to feed electricity back into the grid.
Comments
Press Office
Announcements
What's On
Subscribe to improve your user experience...
Option 1 (equivalent of R125 a month):
Receive a weekly copy of Creamer Media's Engineering News & Mining Weekly magazine
(print copy for those in South Africa and e-magazine for those outside of South Africa)
Receive daily email newsletters
Access to full search results
Access archive of magazine back copies
Access to Projects in Progress
Access to ONE Research Report of your choice in PDF format
Option 2 (equivalent of R375 a month):
All benefits from Option 1
PLUS
Access to Creamer Media's Research Channel Africa for ALL Research Reports, in PDF format, on various industrial and mining sectors
including Electricity; Water; Energy Transition; Hydrogen; Roads, Rail and Ports; Coal; Gold; Platinum; Battery Metals; etc.
Already a subscriber?
Forgotten your password?
Receive weekly copy of Creamer Media's Engineering News & Mining Weekly magazine (print copy for those in South Africa and e-magazine for those outside of South Africa)
➕
Recieve daily email newsletters
➕
Access to full search results
➕
Access archive of magazine back copies
➕
Access to Projects in Progress
➕
Access to ONE Research Report of your choice in PDF format
RESEARCH CHANNEL AFRICA
R4500 (equivalent of R375 a month)
SUBSCRIBEAll benefits from Option 1
➕
Access to Creamer Media's Research Channel Africa for ALL Research Reports on various industrial and mining sectors, in PDF format, including on:
Electricity
➕
Water
➕
Energy Transition
➕
Hydrogen
➕
Roads, Rail and Ports
➕
Coal
➕
Gold
➕
Platinum
➕
Battery Metals
➕
etc.
Receive all benefits from Option 1 or Option 2 delivered to numerous people at your company
➕
Multiple User names and Passwords for simultaneous log-ins
➕
Intranet integration access to all in your organisation