Energy consumption reduced with new pumps
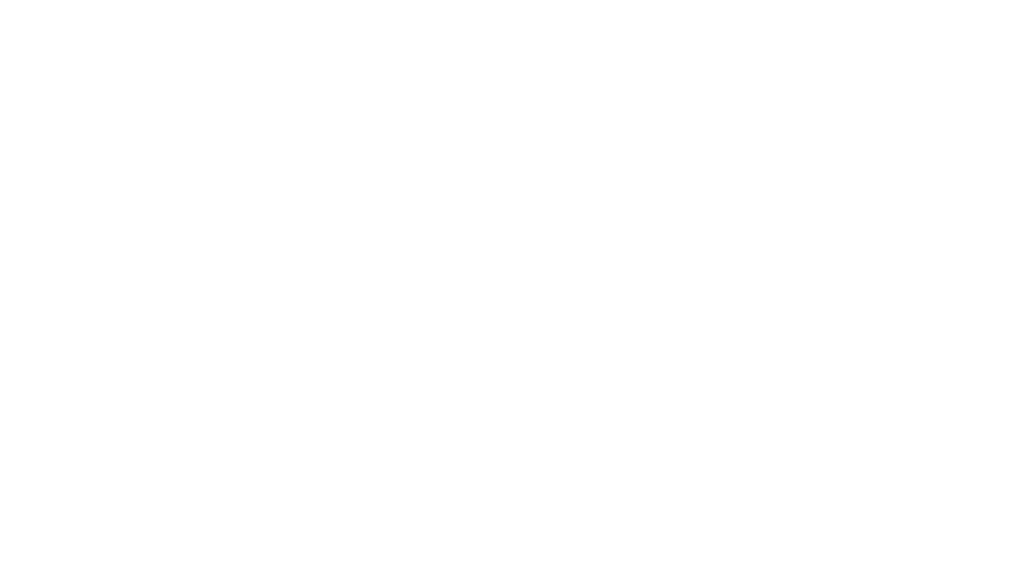
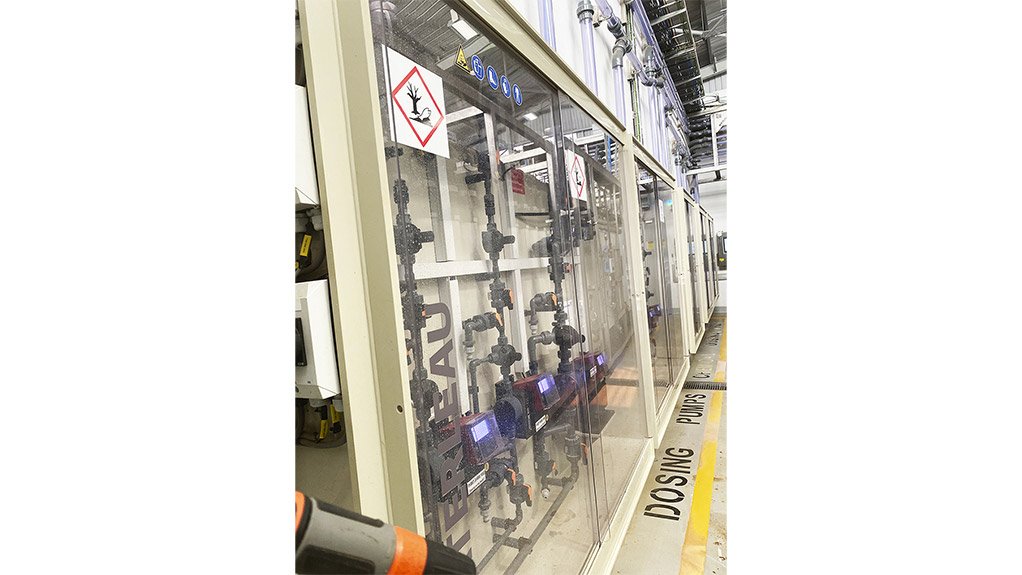
BEER MADE SUSTAINABLY Grundfos dosing skids installed at a brewery water recovery plant
The installation of pumps manufacturer and supplier Grundfos pumps and related equipment as part of an international beer brewer’s expansion in Gauteng highlights a common commitment to water and energy efficiency.
A range of Grundfos submersible pumps, smart digital pumps and vertical multistage centrifugal pumps are installed at this Sedibeng-based brewery’s wastewater plant and its water treatment plant.
The installation, which is in line with the brewer’s commitment to conserve water as a precious resource, included the installation of a water recovery plant, allowing the operation to further optimise water use within its facility.
The expansion also saw the upgrading of the water treatment plant, where clean, ‘raw’ water from the municipality is further purified for brewing purposes. After the beer is produced, beer residues and water used for pipe cleaning is treated to meet regulated environmental discharge limits. This can also be reused for cleaning, reducing the need to draw on the municipal supply.
According to Grundfos associate sales engineer Raymond Makgoga, three Grundfos submersible wastewater pumps were provided to transfer water from the brewery to the water recovery plant. After the sedimentation process, water is pumped to the reclamation plant for final treatment. In this circuit, about 6 000 m3 of water is pumped daily, with the pumps being driven by 15 kW high-efficiency motors with International Efficiency 3 (IE3) rating.
Accurate Dosing
In the water treatment plant, a number of Grundfos Smart Digital S and Smart Digital XL pumps are installed, mounted on dosing skids, says Makgoga.
“These must accommodate a range of chemicals from sodium hydroxide and sodium hypochlorite in the reverse osmosis circuit, to citric acid and antiscalant in the ultrafiltration circuit.”
Makgoga illustrates that this function is a critical part of the brewery’s operation, and comments on the value of Grundfos control systems.
“These systems give a high level of control, communicating vital data between the pump and the programme logic controller (PLC) so that chemical dosing is accurate and appropriate. “This eliminates over-dosing and ensures that chemicals are not wasted; the Grundfos pumps are able to measure the volumes of water flow and then dose in proportion.”
The dosing pumps were supplied with the complete package, including Grundfos’ CIU 500 interface. The CIU 500 is a standard interface for data transmission between an industrial Ethernet network and a Grundfos pump or controller, making data exchange possible between Grundfos pumping systems and a PLC or super- visory control and data acquisition system.
Other accessories in the package were pressure relief valves, pressure loading valves for maintaining pressure on the discharge line, and pulsation dampeners to ensure smooth dosing flow.
Saving Energy
Energy efficiency is also an important factor, considering the significant energy consumed by wastewater treatment plants. Some 28% of the Sedibeng facility’s energy is consumed by utilities, which are the first port of call for energy saving efforts.
Large pumps in the system transfer about 1 750 m3 of water per hour around the brewery, for instance, pumping for 24 hours a day. To monitor and conserve energy, he says the company uses a utilities benchmark model which compares the electricity used with the kilograms of water treated and chemical oxygen demand (COD).
The use of IE3 energy efficient motors in the Grundfos pump installations has assisted in reducing energy consumption to about 13 kW/kg COD treated, from a level of over 1.9 kW/kg COD treated, previously. These statistics are tracked daily, and the new equipment helps to facilitate this data tracking as the operation works towards even more demanding energy saving targets.
According to Grundfos service salesperson Nancy Khumalo, energy savings can be modelled in advance to indicate how Grundfos pump installations can improve energy consumption.
“This allows our customers to consider how the Grundfos pumps could contribute to reducing their carbon footprint and their actual electricity costs. “We are also able to provide an estimation of the capital payback period based on these savings,” says Khumalo.
As part of the package, Grundfos provided training and support to operator-level employees at the brewery. This allowed the plant staff to ‘take ownership’ of the equipment and understand more about its functioning.
“Grundfos has been proactive in embracing our sustainability vision, and is now guided by our Grundfos Strategy 2025. “Focusing on people and water, we share the same passion as our customers to impact positively on our global future through high-value, technology-driven solutions.
Comments
Press Office
Announcements
What's On
Subscribe to improve your user experience...
Option 1 (equivalent of R125 a month):
Receive a weekly copy of Creamer Media's Engineering News & Mining Weekly magazine
(print copy for those in South Africa and e-magazine for those outside of South Africa)
Receive daily email newsletters
Access to full search results
Access archive of magazine back copies
Access to Projects in Progress
Access to ONE Research Report of your choice in PDF format
Option 2 (equivalent of R375 a month):
All benefits from Option 1
PLUS
Access to Creamer Media's Research Channel Africa for ALL Research Reports, in PDF format, on various industrial and mining sectors
including Electricity; Water; Energy Transition; Hydrogen; Roads, Rail and Ports; Coal; Gold; Platinum; Battery Metals; etc.
Already a subscriber?
Forgotten your password?
Receive weekly copy of Creamer Media's Engineering News & Mining Weekly magazine (print copy for those in South Africa and e-magazine for those outside of South Africa)
➕
Recieve daily email newsletters
➕
Access to full search results
➕
Access archive of magazine back copies
➕
Access to Projects in Progress
➕
Access to ONE Research Report of your choice in PDF format
RESEARCH CHANNEL AFRICA
R4500 (equivalent of R375 a month)
SUBSCRIBEAll benefits from Option 1
➕
Access to Creamer Media's Research Channel Africa for ALL Research Reports on various industrial and mining sectors, in PDF format, including on:
Electricity
➕
Water
➕
Energy Transition
➕
Hydrogen
➕
Roads, Rail and Ports
➕
Coal
➕
Gold
➕
Platinum
➕
Battery Metals
➕
etc.
Receive all benefits from Option 1 or Option 2 delivered to numerous people at your company
➕
Multiple User names and Passwords for simultaneous log-ins
➕
Intranet integration access to all in your organisation