Bright future for multifaceted foundry industry, despite decline
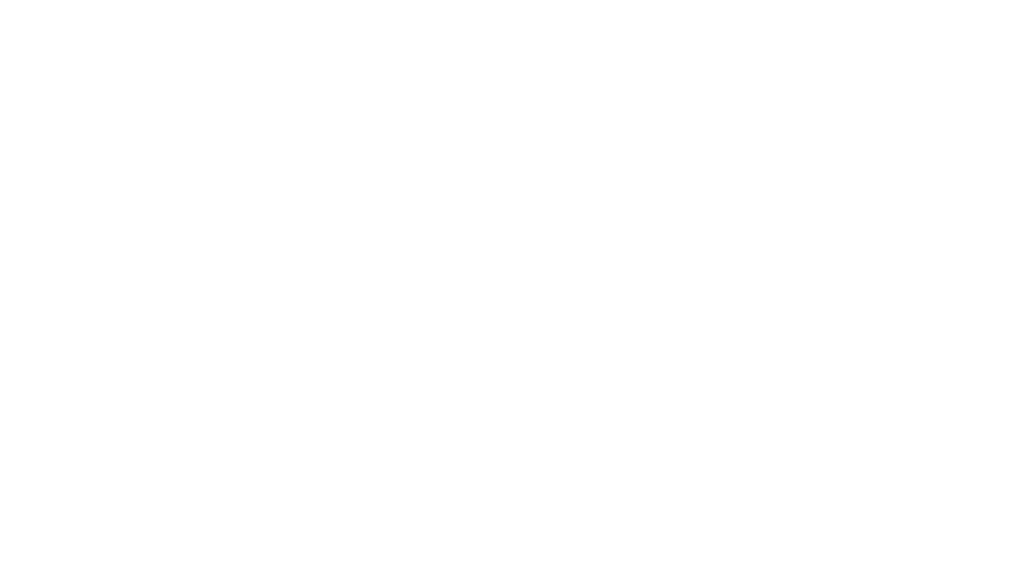
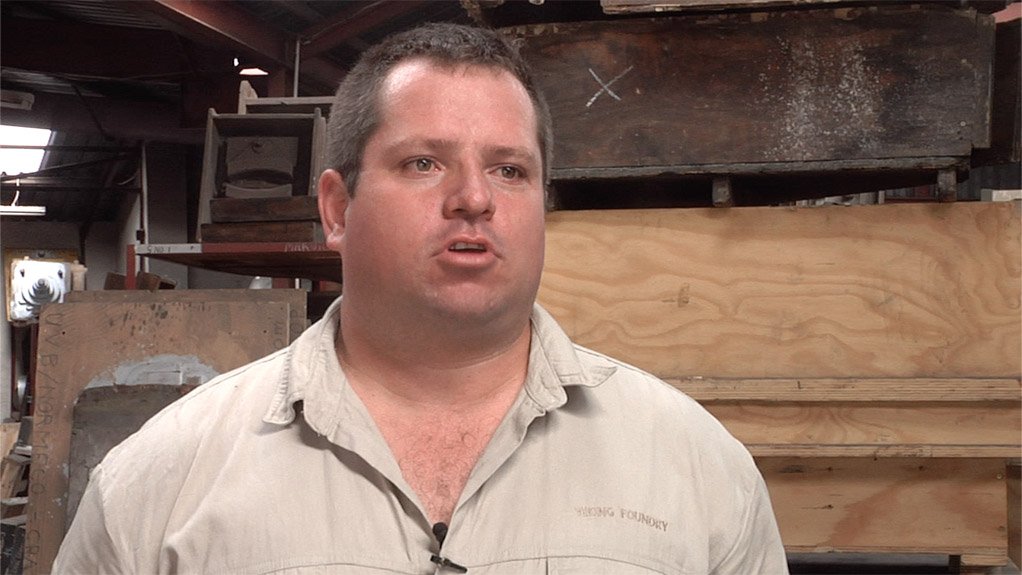
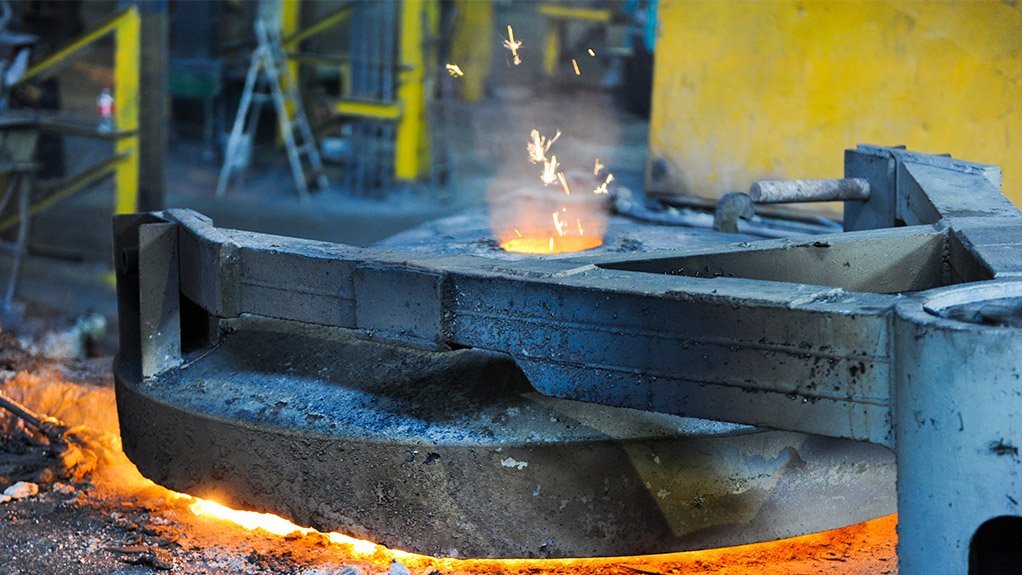
SAIF CEO John Davies discusses tackling the forging industry’s challenges and Viking Foundry operations manager Greg Estman discusses the foundry.
PROMISING FUTURE Local foundries have been preparing for the increased volumes
The metal-casting industry has experienced a period of decline, with several closures of foundries in recent years. However, the recent signs of economic recovery in Europe and North America, the continued strong growth of the African continent’s economy and the weakening of the rand are all encouraging signs that a more stable period for foundries is on the horizon, says the South African Institute of Foundrymen (SAIF) CEO John Davies.
He explains that there is some buoyancy in the industry amid government’s infrastructural reconstruction and development plan, the mid- to long-term aims of the automotive industry to manufacture 1.2-million vehicles by 2020 and government’s commitment to what will soon be the sixth iteration of the Industrial Policy Action Plan.
Further, owing to continued support for local supply chain development from the National Foundry Technology Network (NFTN) and government-driven localisation programmes, the Manufacturing Competitiveness Enhancement Programme (MCEP) and the capital assistance scheme, the future looks encouraging for the foundry industry.
Challenges
Davies says that the lack of a firm, long-term order book and the continuing threat of manufactured imports, arising from global sourcing policies and lower-cost manufacturing zones, are challenges for the industry.
Further, the rapid rise in energy costs, the dependence on world market prices for metal scrap and other input materials, the underdeveloped skills, training and education of the workforce, as well as the associated resistance to adopting new technologies by industry, also present challenges.
The cost of compliance with the recently implemented legislation concerning both air emissions and waste disposal, as well as the declining level of activity in the South African mining industry, have also affected the foundry industry, says Davies, as manufacturing processes have had to be changed.
He notes that the shift in focus of the automotive industry, from local supplier development to the global sourcing of drivetrain and chassis components, also does not bode well for the industry, as it increases cheaper imports and reduces exports from South Africa.
South African Institute of Foundrymen president Enno Krueger says that, unfortunately, South Africa currently imports large amounts of castings for the rail, automotive and mining industries, among others.
However, the foundry industry has severely underused capacity. Bringing these volumes back to the local foundries will have a significant impact on their production costs, making them competitive.
Dealing with the Challenges
Local foundries have been preparing for the increased volumes arising from localisation and infrastructure spend, highlights Davies.
The Gauteng Foundry Training Centre, in KwaThema, was launched in September 2013 and the first intake of apprentices are receiving training in specific foundry skills. The centre was established with the help of the NFTN, the Gauteng Department of Economic Development and further education and training institution Ekurhuleni East College, as well as with SAIF resources.
This followed the successful completion of a pilot learnership programme at the end of 2013, resulting in 14 learners obtaining their National Qualifications Framework Level 4 qualification in melting, moulding and patternmaking, as well as becoming available for placement in the industry.
Further, government has introduced a price preference policy for metal scrap to lower input costs. The industry has been active in the designation process for valves, which is now in effect and which will lead to greater casting demands, explains Davies.
Several other initiatives, driven by the SAIF and the NFTN, in collaboration with the industry, have been implemented to address these challenges in some way, he adds. Skills development and training and education programmes have been implemented to improve the knowledge of the workforce.
They are offered as generic courses and customised for in-house presentations to existing employees in the industry.
Trends in Industry
Besides the continued drive for greater mechanisation, automation and robot use in foundry design to ensure quality consistence, the industry is leaning towards more rapid product development cycles, shorter lead times, leaner sections with increased strengths, and the well-established thrust for lighter metals in automotive applications, says Davies.
“Additive manufacturing, or the three- dimensional printing of polymers, metals and ceramics, such as sand, will transform the low-volume end of the market and the rapid prototyping technologies,” he adds.
Several of the country’s technology universities have courses directed at the metallurgical industries, in general, or the metal casting industry, in particular, so a thin stream of engineers is being absorbed by the industry on a yearly basis.
“More needs to be done to encourage the uptake of technicians and engineers in our industry. Research is carried out at South Africa’s four technical universities, which provide valuable assistance to the industry in applying the latest technologies in our foundries,” notes Davies.
He says the biggest potential for growth in the industry lies in the localisation programmes for the 18 Strategic Infrastructural Projects making up the R847-billion spend over the medium term announced in the Finance Minister’s Budget speech, resurrecting the local supply chain for the supply of drivetrain components to the automotive industry and exploiting the capital goods and consumable markets in the African mining industry.
Comments
Press Office
Announcements
What's On
Subscribe to improve your user experience...
Option 1 (equivalent of R125 a month):
Receive a weekly copy of Creamer Media's Engineering News & Mining Weekly magazine
(print copy for those in South Africa and e-magazine for those outside of South Africa)
Receive daily email newsletters
Access to full search results
Access archive of magazine back copies
Access to Projects in Progress
Access to ONE Research Report of your choice in PDF format
Option 2 (equivalent of R375 a month):
All benefits from Option 1
PLUS
Access to Creamer Media's Research Channel Africa for ALL Research Reports, in PDF format, on various industrial and mining sectors
including Electricity; Water; Energy Transition; Hydrogen; Roads, Rail and Ports; Coal; Gold; Platinum; Battery Metals; etc.
Already a subscriber?
Forgotten your password?
Receive weekly copy of Creamer Media's Engineering News & Mining Weekly magazine (print copy for those in South Africa and e-magazine for those outside of South Africa)
➕
Recieve daily email newsletters
➕
Access to full search results
➕
Access archive of magazine back copies
➕
Access to Projects in Progress
➕
Access to ONE Research Report of your choice in PDF format
RESEARCH CHANNEL AFRICA
R4500 (equivalent of R375 a month)
SUBSCRIBEAll benefits from Option 1
➕
Access to Creamer Media's Research Channel Africa for ALL Research Reports on various industrial and mining sectors, in PDF format, including on:
Electricity
➕
Water
➕
Energy Transition
➕
Hydrogen
➕
Roads, Rail and Ports
➕
Coal
➕
Gold
➕
Platinum
➕
Battery Metals
➕
etc.
Receive all benefits from Option 1 or Option 2 delivered to numerous people at your company
➕
Multiple User names and Passwords for simultaneous log-ins
➕
Intranet integration access to all in your organisation