Compressor control solutions offer optimisation, increased efficiency
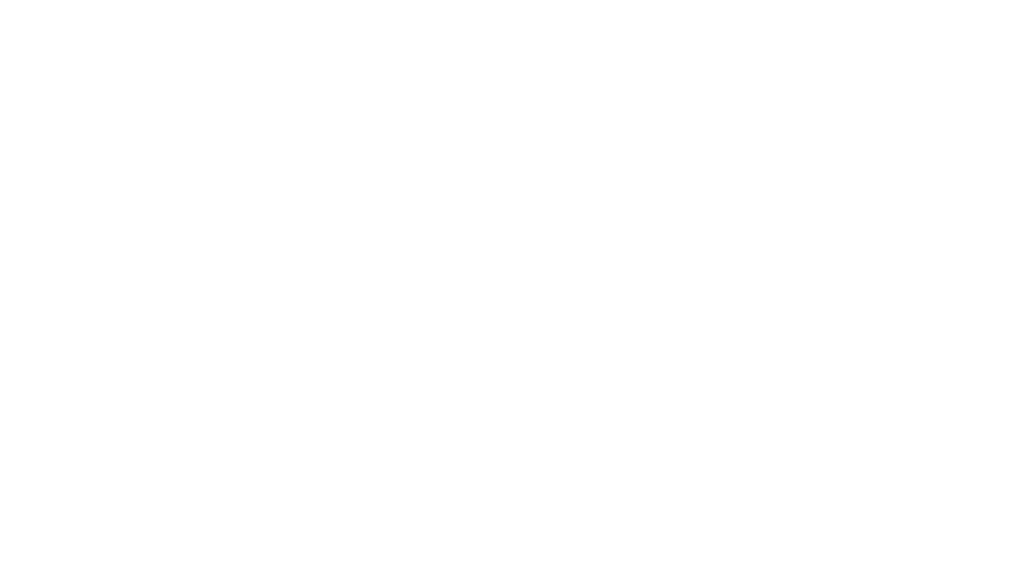
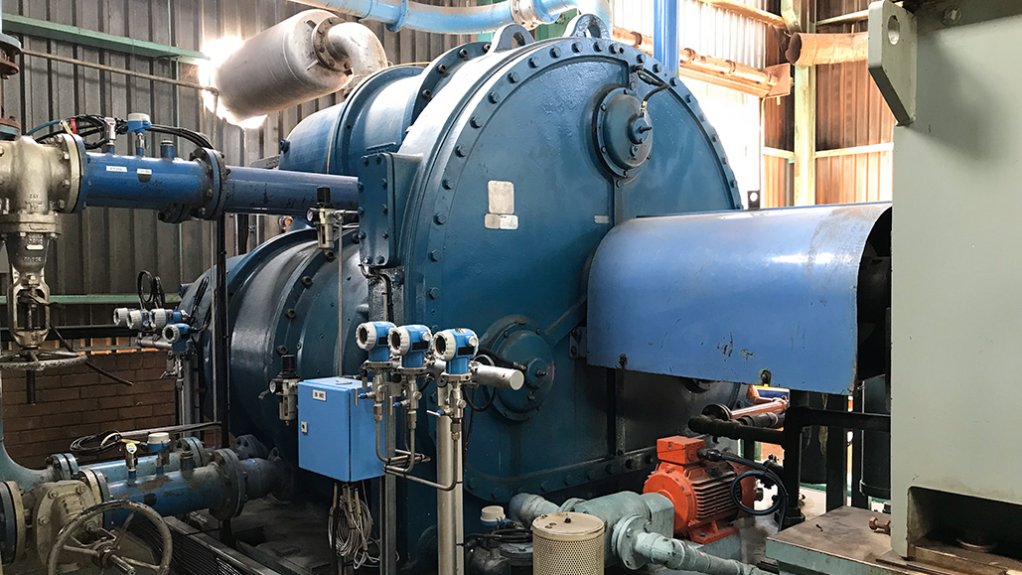
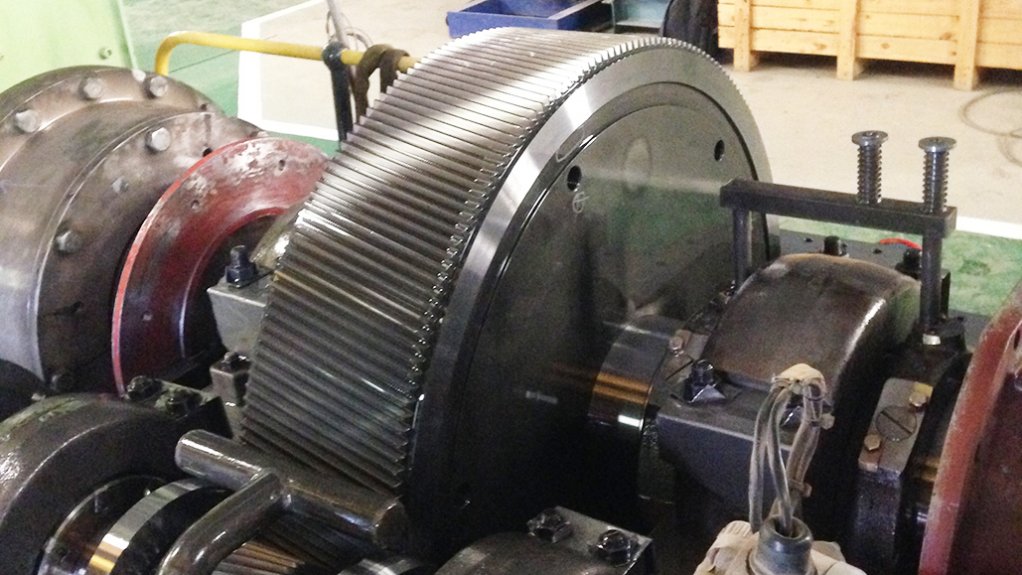
INCREASED EFFICIENCY The master control solution can provide up to 10% in energy savings
BEYOND THE BOX Rockwell Automation's solutions focus on controlling and protecting compressors enabling efficiency
Automation technology and solutions specialist Rockwell Automation offers solutions for controlling and protecting compressors; these solutions improve energy efficiency, optimise machine performance and allow for making data-driven decisions that enable efficient and effective operations.
The solutions include hardware and software, with application-focused programming required to provide a complete solution, consequently enabling customers to efficiently manage the machine during operational times, says Rockwell Automation compressor specialist Andries Kruger.
A key focus of the company’s solutions is energy efficiency, which is a significant factor in various industries that use compressors, particularly the mining industry.
“Ensuring adequate compressed air and ventilation in mining is one of the biggest power consumers by a big margin. The efficient optimisation of compressors, both as individual units and as a fleet of machines is a big market driver,” Kruger adds.
Rockwell Automation offers clients the solution in two phases – advanced compressor control and then supervisory master control.
The advanced compressor control system is applied to specific individual compressors, while the supervisory master control enables customers to control an entire fleet of compressors.
An important aspect of the advanced control per compressor is the system’s anti-surge control functionality, particularly for dynamic-type compressors. Operating the machine close to the surge line is important for efficiency. However, it is crucial to prevent the compressor from going into a surge condition, as frequent surges can cause significant damage.
Regarding the master control phase, most customers do not have the same pressure requirements every hour of the day, and this control enables them to change compressor discharge pressures based on production requirements and according to a stipulated pressure set point profile.
Kruger explains that energy saving is the key benefit of the master control solution as customers can save significant amounts of energy if they reduce the output of their fleet of compressors by stopping or idling a few machines during specific times when production shift changes occur and ventilation in specific areas is not required.
Based on results from Rockwell Automation’s installed projects, the master control solution can provide up to 10% in energy savings.
Beyond the Black Box
Kruger says there is growing interest in increasing customers’ understanding of machines, owing to their wanting to find out which machines are most efficient, and, therefore, most beneficial.
A drawback associated with legacy systems and legacy compressor controls is black box solutions, which comprise a piece of hardware that customers cannot access. While it is working, customers cannot see what is happening inside of it, visualise its process or configure it.
In response to this, Rockwell Automation’s solutions do not use a black box, with all processes linked to configurable controllers as one fully integrated system. Customers have full visualisation of what is happening within the controller and can make a variety of changes to suit their particular requirements.
In-Depth Reporting Driving Digitalisation
Kruger says a key consideration for many customers is an efficient machine with enhanced availability that allows frequent use.
A significant aspect of the company’s solutions is the reporting options it provides. It seamlessly integrates into the Industrial Internet of Things (IIoT) platforms that are available from Rockwell Automation.
The IIoT solution chosen by the customer can be scalable, from a few focused reports to an entire digital mining solution that is vendor agnostic and integrates all aspects of the entire mining business. This compressor solution is an ideal building block for the digitalisation journey of mining companies.
Rockwell Automation has developed several tools to provide in-depth analytics that enable customers to evaluate efficiency and assist with predictive maintenance.
The reporting tools provide as much information about predictive maintenance as possible, including reports on water and oil flows, vibration and temperature.
The resulting reports can be accessed through a dashboard that contains information. The reports can be accessed without physically going to the machinery, allowing for convenient access to information.
The reporting tools provide different reports for different levels of management or different departments within the business.
For example, the production and efficiency report provides an idea of the efficiency of the machine, taking into account if any downtime occurred and the reasons for the downtime. Meanwhile, the condition report provides an overview of all the instrumentation and includes key performance indicators for every specific set of instrumentation.
These reports enable management to make data-driven decisions, at the right level, at the right time, based on relevant, accurate machine information, concludes Rockwell Automation engineering manager Johan Buckle.
The company aims to eventually integrate artificial intelligence into its reporting tools, which would assist in the predictive management of the compressor fleet.
Comments
Press Office
Announcements
What's On
Subscribe to improve your user experience...
Option 1 (equivalent of R125 a month):
Receive a weekly copy of Creamer Media's Engineering News & Mining Weekly magazine
(print copy for those in South Africa and e-magazine for those outside of South Africa)
Receive daily email newsletters
Access to full search results
Access archive of magazine back copies
Access to Projects in Progress
Access to ONE Research Report of your choice in PDF format
Option 2 (equivalent of R375 a month):
All benefits from Option 1
PLUS
Access to Creamer Media's Research Channel Africa for ALL Research Reports, in PDF format, on various industrial and mining sectors
including Electricity; Water; Energy Transition; Hydrogen; Roads, Rail and Ports; Coal; Gold; Platinum; Battery Metals; etc.
Already a subscriber?
Forgotten your password?
Receive weekly copy of Creamer Media's Engineering News & Mining Weekly magazine (print copy for those in South Africa and e-magazine for those outside of South Africa)
➕
Recieve daily email newsletters
➕
Access to full search results
➕
Access archive of magazine back copies
➕
Access to Projects in Progress
➕
Access to ONE Research Report of your choice in PDF format
RESEARCH CHANNEL AFRICA
R4500 (equivalent of R375 a month)
SUBSCRIBEAll benefits from Option 1
➕
Access to Creamer Media's Research Channel Africa for ALL Research Reports on various industrial and mining sectors, in PDF format, including on:
Electricity
➕
Water
➕
Energy Transition
➕
Hydrogen
➕
Roads, Rail and Ports
➕
Coal
➕
Gold
➕
Platinum
➕
Battery Metals
➕
etc.
Receive all benefits from Option 1 or Option 2 delivered to numerous people at your company
➕
Multiple User names and Passwords for simultaneous log-ins
➕
Intranet integration access to all in your organisation