Cutting corners to cost mines in long run
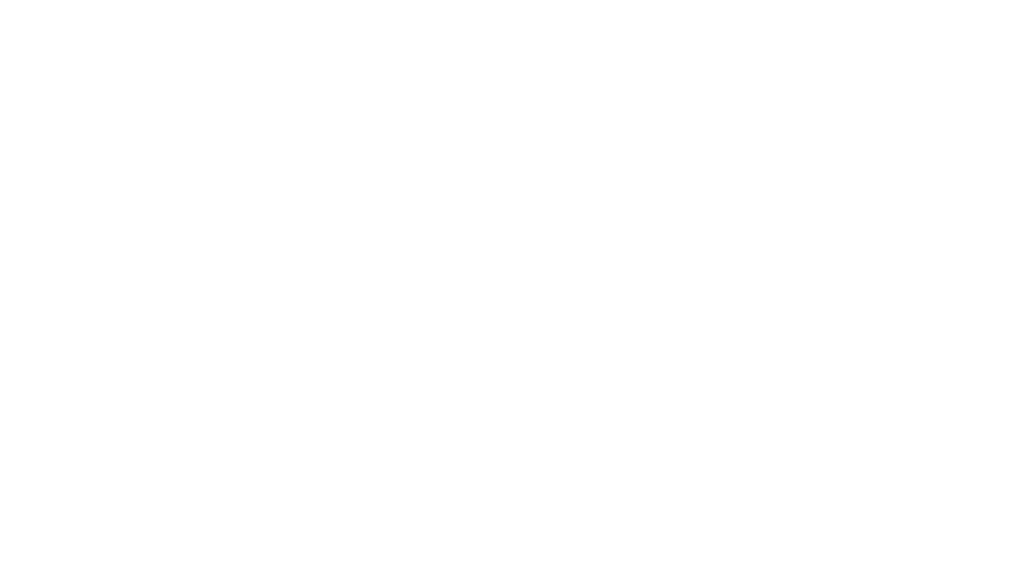
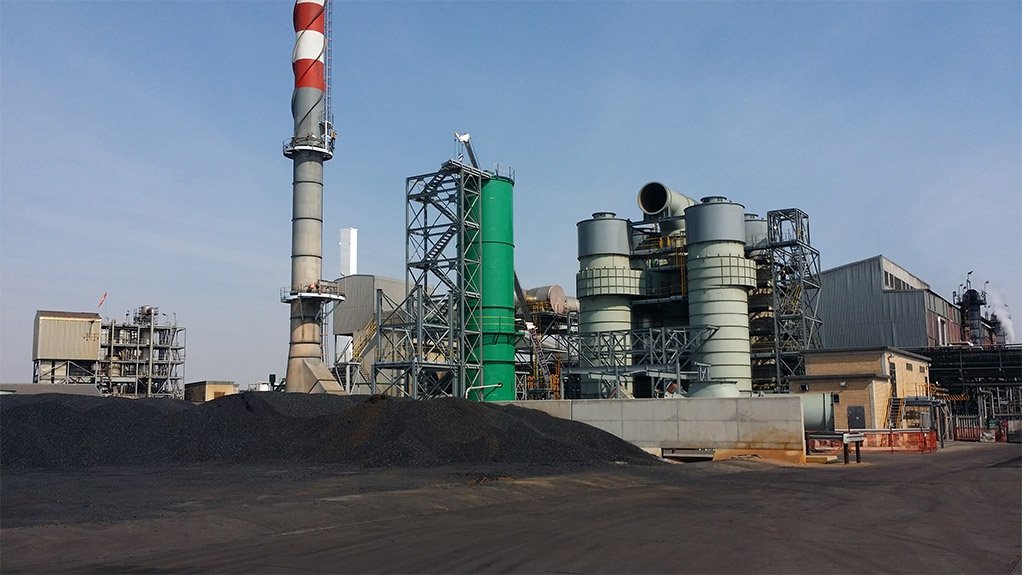
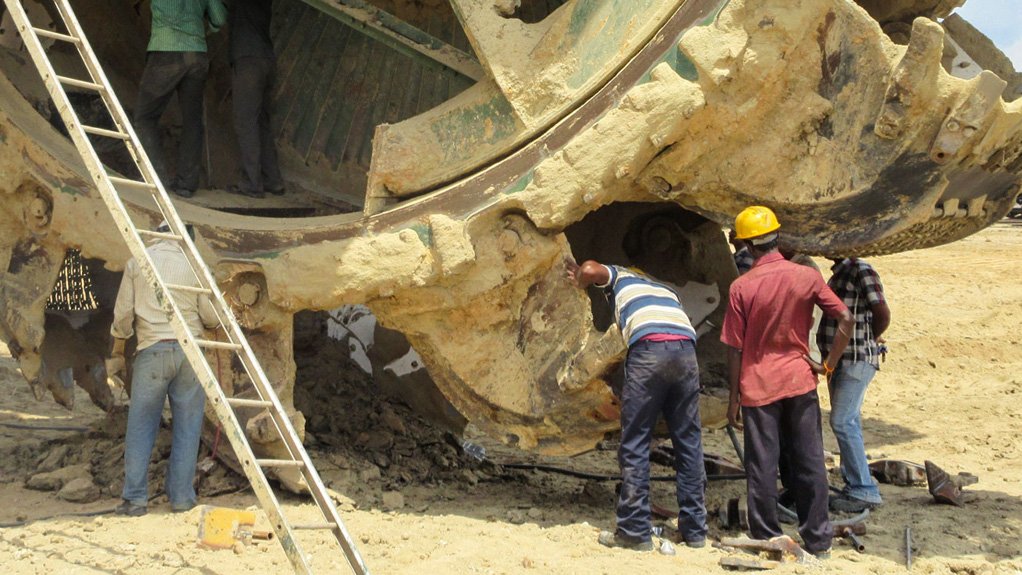
INCREASED NEED With the rapid uptake of mechanisation and automation in the mining industry, greater emphasis has been placed on the need for maintenance in the last 20 years
QUALITY ENSURES SAFETY Not using original-equipment manufacturer parts to maintain equipment could lead to unsafe working conditions at mining sites
Many sites are trying to cut costs by moving away from using original- equipment-manufacturer (OEM) spares and components when undertaking maintenance, says technologies, products and engineering services provider Tenova Takraf Africa aftermarket GM Paul Davies.
He tells Mining Weekly that this is due to the recent tougher global economic conditions facing the mining industry, with many mines opting for pirate parts to reduce maintenance costs.
However, Davies advises against this, as long-term maintenance costs will increase if OEM components are not used in the maintenance of major equipment.
Further, undertaking maintenance perfunctorily could lead to unsafe working conditions at mines. Davies explains that, in terms of Tenova Takraf Africa’s client support services, it is well accepted that “only properly maintained equipment is safe equipment”.
When training technical and operating personnel, the company focuses on safety; therefore, its artisans can be used as safety supervisors when undertaking shutdowns. This saves mines the additional fee that is often uncured when contracting third-party labour to ensure that shutdowns are done safely.
Meanwhile, rapid mechanisation and automation in the mining industry have resulted in greater emphasis being placed on mine maintenance over the past 20 years, Davies states. “The capital outlay and cost of ownership related to mining equipment and its importance to production require that it is maintained in good condition to ensure the most effective performance at the highest safety levels.”
Although the depressed mining market has caused capital constraints, it has, in turn, placed greater emphasis on the importance of maintenance and refurbishment, as clients want to make the most of their assets, he notes.
However, in some instances, mines are skipping the required routine maintenance, which is often the case with junior mining companies, as their available capital is limited and cannot deal with the necessary mine site and equipment maintenance, Davies elaborates.
“The degeneration of skills and training, not only in South Africa but also worldwide, also puts Tenova Takraf in a position to provide the skills needed to better maintain equipment.”
Training is as important as regular maintenance, states Davies, adding that the company offers training for technical and operating staff during the commissioning phase and plant handover, and as part of its aftermarket client support services.
The company further hosts technology days, participates in roadshows in the areas where its equipment is installed and hosts local technical meetings with engineers who regularly use the equipment. Davies states that, through all these initiatives, Tenova Takraf aims to not only maintain close business relationships with its clients but also transfer technical expertise to partners and clients of the company.
Tenova Takraf’s client support services are a crucial element of the company’s total service delivery, he highlights. The services aim to provide comprehensive aftermarket support, including the sourcing and supply of spares, refurbishments and the upgrading of machines.
Davies states that Tenova Takraf’s field-inspection service adds much value, as it identifies which of a client’s machines are in poor condition. The company then provides further assistance by identifying and supplying the required and/or critical spares, auditing on-site or available inventory and replacing components.
Tenova Takraf has met many demanding deadlines on big projects. For example, the refurbishment of a rapid train load-out system for a Mpumalanga-based coal producer was completed within four months, says Davies: “The scope of work covered the design, construction and commissioning of a new control system, as well the recertification of the weigh flask system, without incurring any production loss.”
Comments
Press Office
Announcements
What's On
Subscribe to improve your user experience...
Option 1 (equivalent of R125 a month):
Receive a weekly copy of Creamer Media's Engineering News & Mining Weekly magazine
(print copy for those in South Africa and e-magazine for those outside of South Africa)
Receive daily email newsletters
Access to full search results
Access archive of magazine back copies
Access to Projects in Progress
Access to ONE Research Report of your choice in PDF format
Option 2 (equivalent of R375 a month):
All benefits from Option 1
PLUS
Access to Creamer Media's Research Channel Africa for ALL Research Reports, in PDF format, on various industrial and mining sectors
including Electricity; Water; Energy Transition; Hydrogen; Roads, Rail and Ports; Coal; Gold; Platinum; Battery Metals; etc.
Already a subscriber?
Forgotten your password?
Receive weekly copy of Creamer Media's Engineering News & Mining Weekly magazine (print copy for those in South Africa and e-magazine for those outside of South Africa)
➕
Recieve daily email newsletters
➕
Access to full search results
➕
Access archive of magazine back copies
➕
Access to Projects in Progress
➕
Access to ONE Research Report of your choice in PDF format
RESEARCH CHANNEL AFRICA
R4500 (equivalent of R375 a month)
SUBSCRIBEAll benefits from Option 1
➕
Access to Creamer Media's Research Channel Africa for ALL Research Reports on various industrial and mining sectors, in PDF format, including on:
Electricity
➕
Water
➕
Energy Transition
➕
Hydrogen
➕
Roads, Rail and Ports
➕
Coal
➕
Gold
➕
Platinum
➕
Battery Metals
➕
etc.
Receive all benefits from Option 1 or Option 2 delivered to numerous people at your company
➕
Multiple User names and Passwords for simultaneous log-ins
➕
Intranet integration access to all in your organisation