Equipment design vital for sugar industry
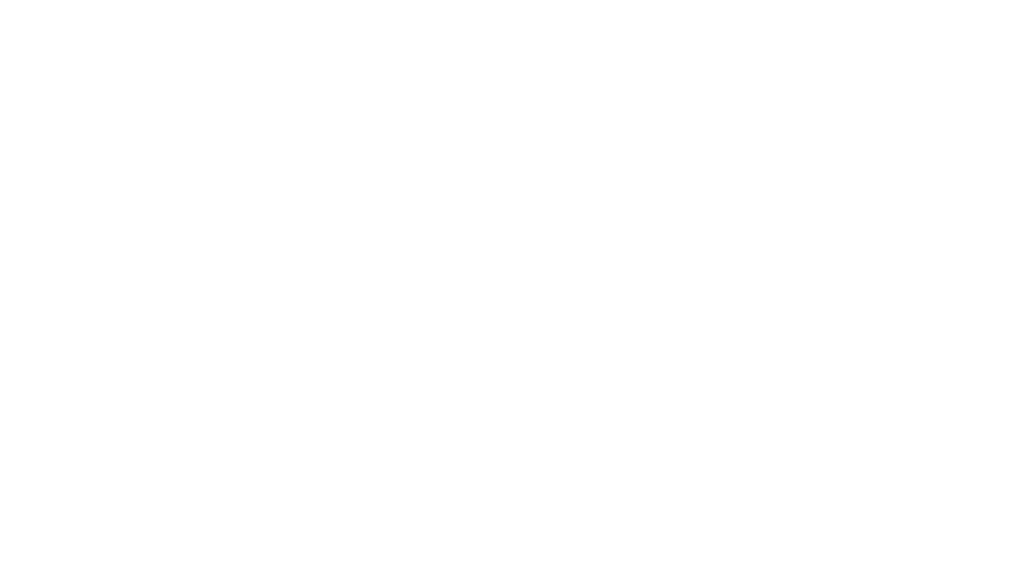
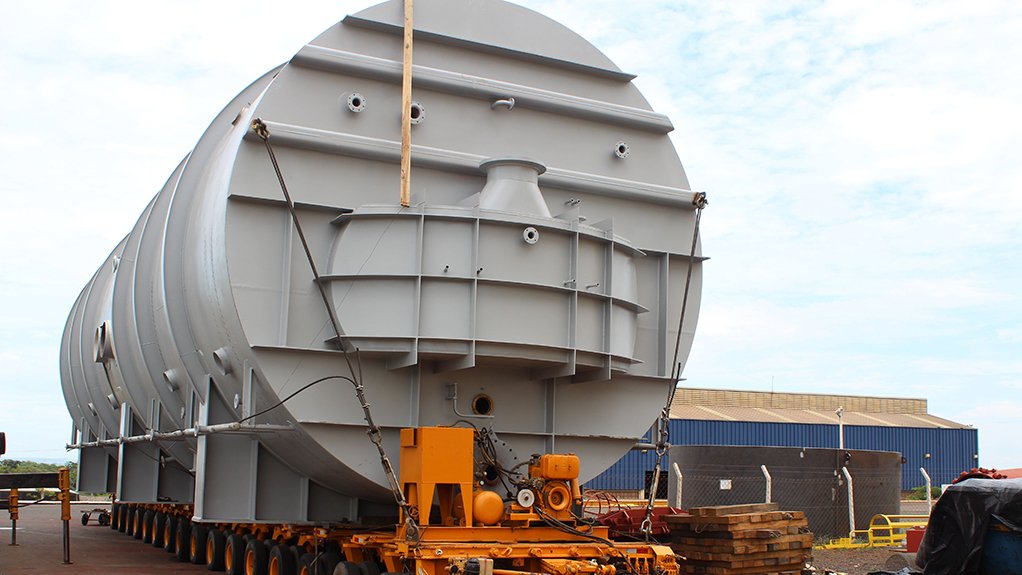
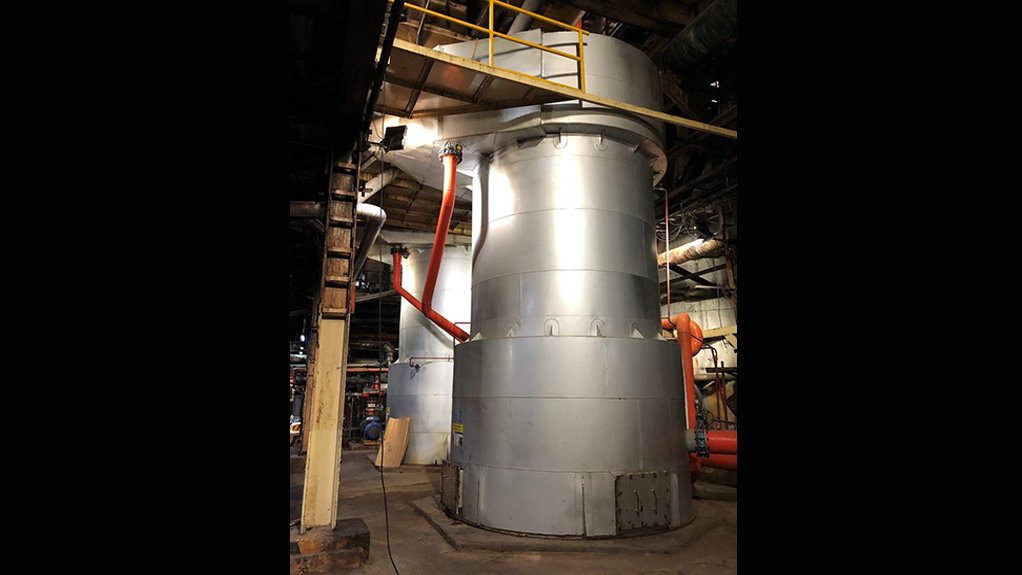
DIVERSE OFFERING For the sugar industry, Bosch Projects provides front-end cane offloading, cane preparation, juice extraction, sugar processing, sugar drying and refining equipment
SO, SO ADVANTAGEOUS The major advantage of the vertical reheater design (pictured above) is that massecuite rises as it is heated, therefore following natural convection tendencies
A critical aspect of servicing the sugar industry is equipment design, says integrated engineering technology and project management company Bosch Projects sugar sector director Steve Rosettenstein.
Bosch Projects, a member of multidisciplinary consulting engineering holding company Bosch Holdings group, provides tailored solutions for diverse industries.
Bosch Projects, which has served the global sugar industry for almost 59 years, offers “a comprehensive service to customers”, encompassing strategic planning and feasibility studies, sugar technology selection, project structuring and funding, design and engineering, project delivery, as well as operational support and training.
Rosettenstein says the company’s research and development team works closely with associate sugar consultants and technologists globally to develop high-performance equipment, with every system designed to meet client requirements for cost efficiency and improved productivity.
“Although new equipment is designed – combining the latest technologies and advanced manufacturing trends – Bosch Projects also incorporates tried and tested technologies favoured by clients into new designs.”
Further, over the past 20 years, the company’s equipment division has developed an extensive range of sugar-processing equipment, which includes the patented Bosch Projects chainless diffuser and continuous vacuum pan (CVP).
Bosch Projects’ other best-selling equipment includes rotary juice screens, juice heaters and clarifiers, cane preparation equipment, long-tube evaporators and entrainment separators.
The company has also sold sugar dryers, refined-sugar conditioning silos, continuous vertical massecuite reheaters, vertical continuous crystallisers and batch pans.
The CVP design has become “the preferred system” of many of the world’s largest sugar-processing groups, says Bosch Projects sugar equipment sector manager Neil du Plessis.
“When supplying a CVP for C boilings, we recommend to clients that we provide the full C station, which includes the CVP, the continuous vertical crystalliser and the continuous massecuite reheater.”
The company’s offering of the entire system, he says, guarantees optimum performance of the total C station exhaustion.
Du Plessis advances that another system that has been well received by the sugar industry is Bosch Projects’ vertically orientated reheater, with significant performance benefits over conventional massecuite reheaters that are horizontally orientated.
He explains that the major advantage of the vertical reheater design is that massecuite rises as it is heated, therefore following natural convection tendencies.
This, ultimately, results in favourable plug flow through the heater, which minimises the purity rise across the unit.
“Horizontal reheaters tend to have overheated channels of massecuite near the top of the vessel and static cool areas at the bottom. This causes the short-circuiting of massecuite inside the reheater, reducing the unit’s efficiency,” he points out.
Consequently, the company has supplied and commissioned six vertical massecuite reheaters globally in the last 12 months and has submitted proposals for another four units to clients who are looking to upgrade reheaters.
These units are fabricated from stainless steel, which minimises maintenance costs and reduces the probability of having to treat the heating water.
Clients can choose from either a full turnkey installation or standalone equipment, the company says.
Integrated Solutions
Added to that, the company has also developed the Lamella clarifier especially for the sugar industry to satisfy demand for short retention clarification.
Although various Lamella clarifier systems are well established in water treatment applications, this technology is new in sugar processing, and is especially effective for juice, syrup and refinery phosphotation clarification.
This clarifier system, which uses a series of inclined plates for fast, effective particle separation and settling, is much smaller than conventional clarifiers and reduces liquor retention times substantially.
“The design of this new settling Lamella clarifier reduces the size and footprint of conventional juice clarifiers by about 30%, significantly lowering capital investment costs.
“Important features include short residence times, reduced sucrose degradation and improved turbidity removal. This highly efficient system, which operates with minimal moving parts, requires low maintenance,” notes Du Plessis.
The syrup Lamella clarifier is similar in design to the juice Lamella version, except that it operates as a flotation, as opposed to a settling, clarifier. This system can be switched on and off as required when syrup qualities are low, and can be easily installed inside an existing factory, owing to its compact size.
The company’s team also works closely with its technology partners and fabricators globally to ensure that the manufacturing of all equipment adheres to stringent international quality standards and exact design specifications.
Bosch Projects has an extensive network of offices in Africa, South and Central America, as well as the UK, with technology partners in the South-East Asia region and the US.
Comments
Press Office
Announcements
What's On
Subscribe to improve your user experience...
Option 1 (equivalent of R125 a month):
Receive a weekly copy of Creamer Media's Engineering News & Mining Weekly magazine
(print copy for those in South Africa and e-magazine for those outside of South Africa)
Receive daily email newsletters
Access to full search results
Access archive of magazine back copies
Access to Projects in Progress
Access to ONE Research Report of your choice in PDF format
Option 2 (equivalent of R375 a month):
All benefits from Option 1
PLUS
Access to Creamer Media's Research Channel Africa for ALL Research Reports, in PDF format, on various industrial and mining sectors
including Electricity; Water; Energy Transition; Hydrogen; Roads, Rail and Ports; Coal; Gold; Platinum; Battery Metals; etc.
Already a subscriber?
Forgotten your password?
Receive weekly copy of Creamer Media's Engineering News & Mining Weekly magazine (print copy for those in South Africa and e-magazine for those outside of South Africa)
➕
Recieve daily email newsletters
➕
Access to full search results
➕
Access archive of magazine back copies
➕
Access to Projects in Progress
➕
Access to ONE Research Report of your choice in PDF format
RESEARCH CHANNEL AFRICA
R4500 (equivalent of R375 a month)
SUBSCRIBEAll benefits from Option 1
➕
Access to Creamer Media's Research Channel Africa for ALL Research Reports on various industrial and mining sectors, in PDF format, including on:
Electricity
➕
Water
➕
Energy Transition
➕
Hydrogen
➕
Roads, Rail and Ports
➕
Coal
➕
Gold
➕
Platinum
➕
Battery Metals
➕
etc.
Receive all benefits from Option 1 or Option 2 delivered to numerous people at your company
➕
Multiple User names and Passwords for simultaneous log-ins
➕
Intranet integration access to all in your organisation