Explosives firm assists with disposal of used oil
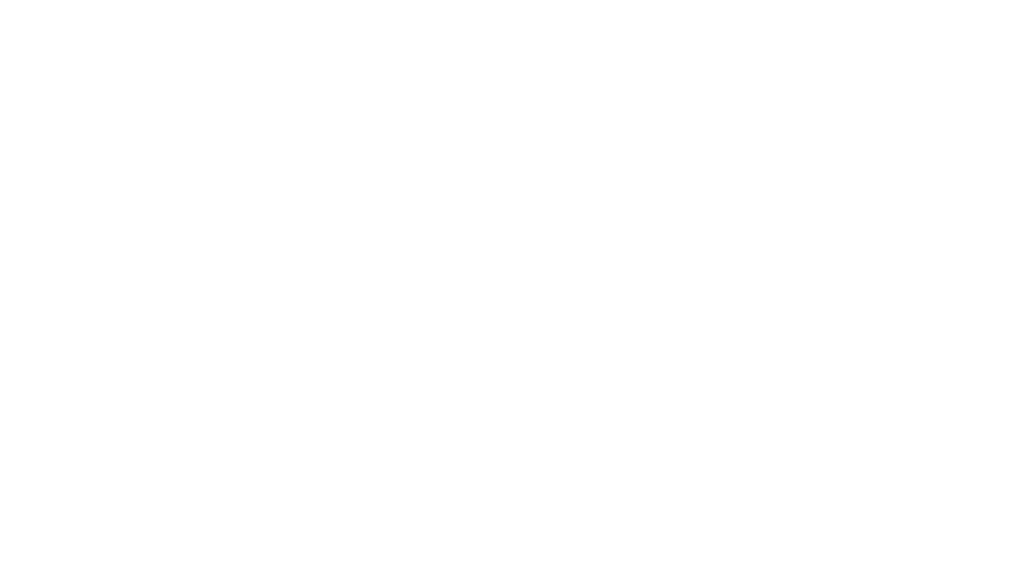
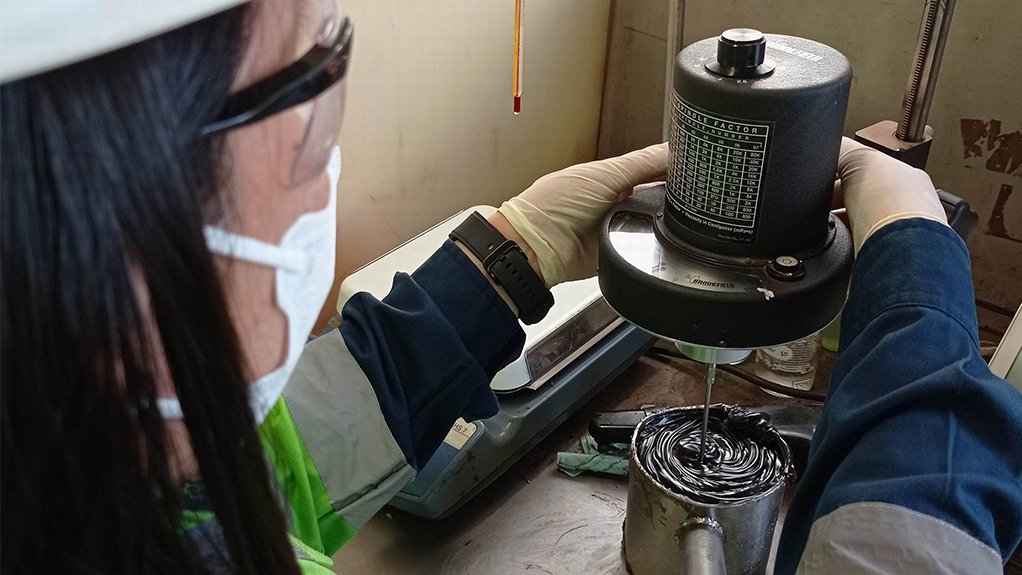
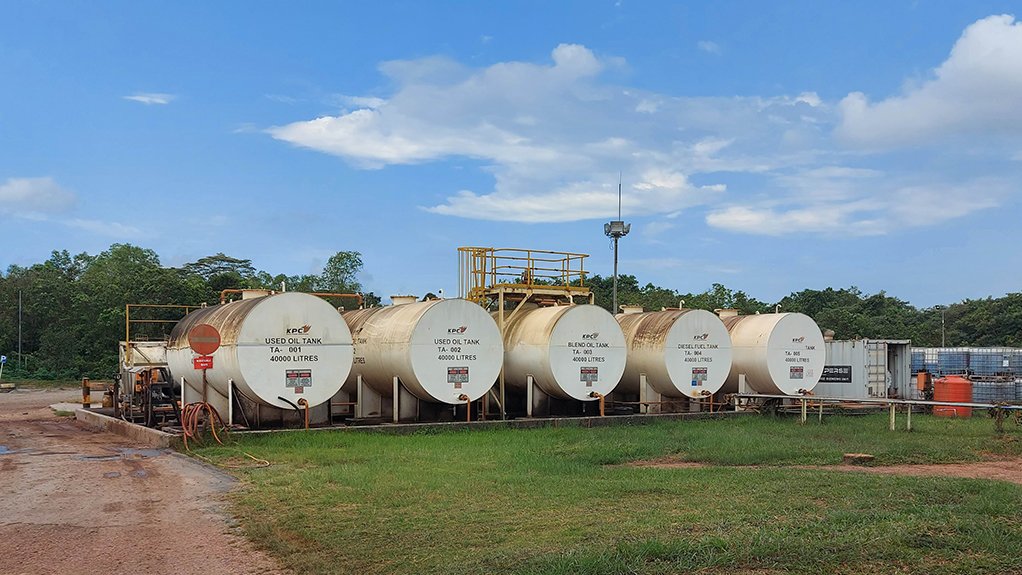
TESTING The recovered used oil from a given workshop facility or source is delivered to a specific settling tank where the used oil is allowed to settle for a number of days
USED OIL STORAGE KPC’s mining activity generated over 8-million litres of used oil a year from 2010 to 2021
Major openpit coal mining company PT Kaltim Prima Coal (KPC), which operates in the regions of Sangatta and Bengalon, in East Kalimantan, Indonesia, manages one of the largest openpit mines in the world which produces about 60-million tons of run-of-mine coal a year.
The truck and excavator method is used across multiple pits, which are managed by two divisions: mine-owner division and contract mining division (CMD). Chemicals group AECI Mining Explosives operates within the CMD area.
KPC mines over 450-million bank cubic metre (BCM) of overburden material a year.
In 2021, KPC mined 453-million BCM of overburden by consuming 85 000 t of bulk explosives to produce 56.4-million tons of coal.
KPC’s mining activity generated over 8-million litres of used oil a year from 2010 to 2021. Prior to 2011, used oil in explosives was only used for ammonium nitrate fuel oil while the remaining oil was shipped to a local licensed waste processor.
Business Challenges
The required volume of bulk explosives at KPC ranges from 80 000 t to 100 000 t a year, and 65% of that requirement is supplied by AECI Mining Explosives at the CMD operations.
KPC has identified that fuel and explosives consumption represent two of the main operating costs for the mine. Consequently, KPC is actively and constantly identifying and implementing more efficient and safe blasting processes to reduce consumables costs, including the saving on diesel for emulsion manufacturing.
To support this, KPC obtained a permit in 2016 to introduce and use used oil to replace diesel by up to 80% in the emulsion formulation and in conformance with the local standard Standar Nasional Indonesia 7642:2010, followed by an upgrade to 100% replacement in 2017.
Used oil is known to contain elements that are harmful to the environment and handling this waste stream in a cost effective and environmentally responsible way is challenging.
To categorise the used oil as a reusable resource and not a hazardous waste material, a strict specification for the quality of the used oil is necessary.
Recovered used oil from a given workshop facility or source is delivered to a specific settling tank where the used oil is allowed to settle for several days.
Water, solids and oil sludge are drained off the bottom of the tanks at regular intervals until the stored used oil is approved for use in the fuel blend component of the emulsion for the manufacture of the final S300 Eco-emulsion.
The S300 Eco series is designed to incorporate used oil with the aim of protecting the environment and reducing the carbon footprint. AECI Mining Explosives is one of the pioneers in the use and application of used oil as a replacement for diesel in emulsion manufacturing.
Advanced emulsifier technology, combined with high-quality used oil, has allowed for the successful replacement of diesel in the manufacture of bulk emulsion explosives.
The development of suitable emulsifiers has enabled AECI Mining Explosives to replace diesel up to 100% without reducing bulk explosives performance.
Energy and performance have, in fact, increased through the combination of these technologies, and AECI Mining Explosives states that it is quite possibly producing the best emulsion explosives in the world today.
In January 2011, AECI Mining Explosives started trials at KPC with 10% replacement of virgin oil, ramping up to 100% in 2017, a testament to the two companies’ relentless drive for continuous improvement.
Outcome
The performance of the S300 Eco Series bulk explosive products has been consistent with all levels of used oil replacement and is monitored regularly on the bench by conducting regular velocity of detonation tests. The product has proved to be stable and performed within its specification, with excellent blast results achieved.
Since the time of introducing used oil for emulsion manufacturing, the saving in diesel consumption for the period 2011 to 2021 has been approximately 25.5-million litres or a yearly average saving of 2.3-million litres.
“The KPC Drill and Blast department is committed to adhering to the country’s stringent environmental regulations. In realising this with our commitment to greener operations, the team understands that there is an opportunity to reduce the proliferation of used oils, which is categorised as a hazardous pollutant. “Part of the synergies explored with AECI Mining Explosives is to ensure that used oils from the mine’s production processes are absorbed as part of AECI’s explosive formulations.
“This opportunity for improvement will not only significantly reduce the blasting cost, but also assist KPC with managing the used oil produced from its operations. “The group expects that AECI Mining Explosives Indonesia will maintain, and where possible, improve on the current excellent emulsion technology and also continue bringing new improvement ideas to KPC,” concluded KPC’s Sasongko Nurwendo.
Comments
Announcements
What's On
Subscribe to improve your user experience...
Option 1 (equivalent of R125 a month):
Receive a weekly copy of Creamer Media's Engineering News & Mining Weekly magazine
(print copy for those in South Africa and e-magazine for those outside of South Africa)
Receive daily email newsletters
Access to full search results
Access archive of magazine back copies
Access to Projects in Progress
Access to ONE Research Report of your choice in PDF format
Option 2 (equivalent of R375 a month):
All benefits from Option 1
PLUS
Access to Creamer Media's Research Channel Africa for ALL Research Reports, in PDF format, on various industrial and mining sectors
including Electricity; Water; Energy Transition; Hydrogen; Roads, Rail and Ports; Coal; Gold; Platinum; Battery Metals; etc.
Already a subscriber?
Forgotten your password?
Receive weekly copy of Creamer Media's Engineering News & Mining Weekly magazine (print copy for those in South Africa and e-magazine for those outside of South Africa)
➕
Recieve daily email newsletters
➕
Access to full search results
➕
Access archive of magazine back copies
➕
Access to Projects in Progress
➕
Access to ONE Research Report of your choice in PDF format
RESEARCH CHANNEL AFRICA
R4500 (equivalent of R375 a month)
SUBSCRIBEAll benefits from Option 1
➕
Access to Creamer Media's Research Channel Africa for ALL Research Reports on various industrial and mining sectors, in PDF format, including on:
Electricity
➕
Water
➕
Energy Transition
➕
Hydrogen
➕
Roads, Rail and Ports
➕
Coal
➕
Gold
➕
Platinum
➕
Battery Metals
➕
etc.
Receive all benefits from Option 1 or Option 2 delivered to numerous people at your company
➕
Multiple User names and Passwords for simultaneous log-ins
➕
Intranet integration access to all in your organisation