Extrusion press concept for aluminium sector developed
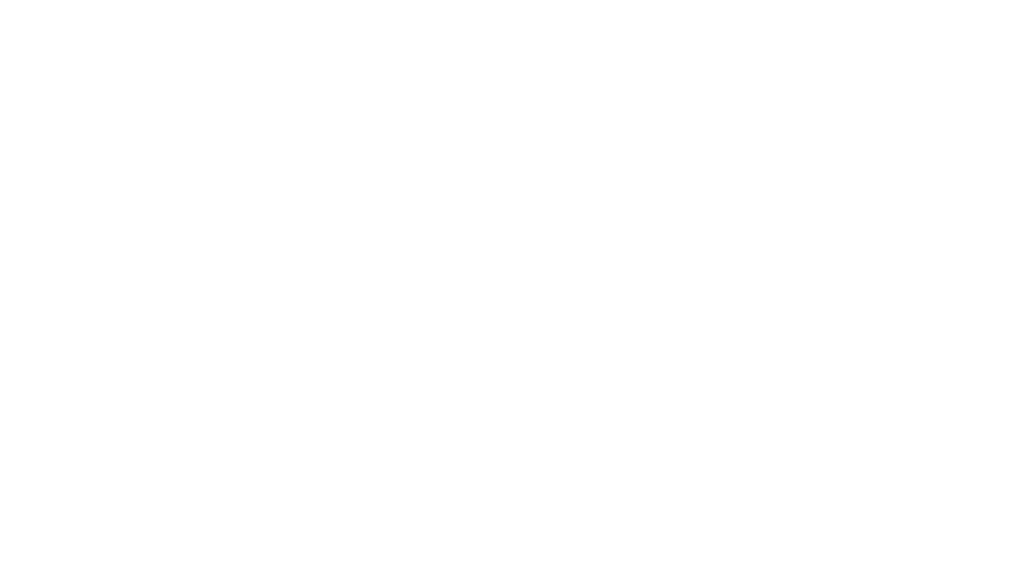
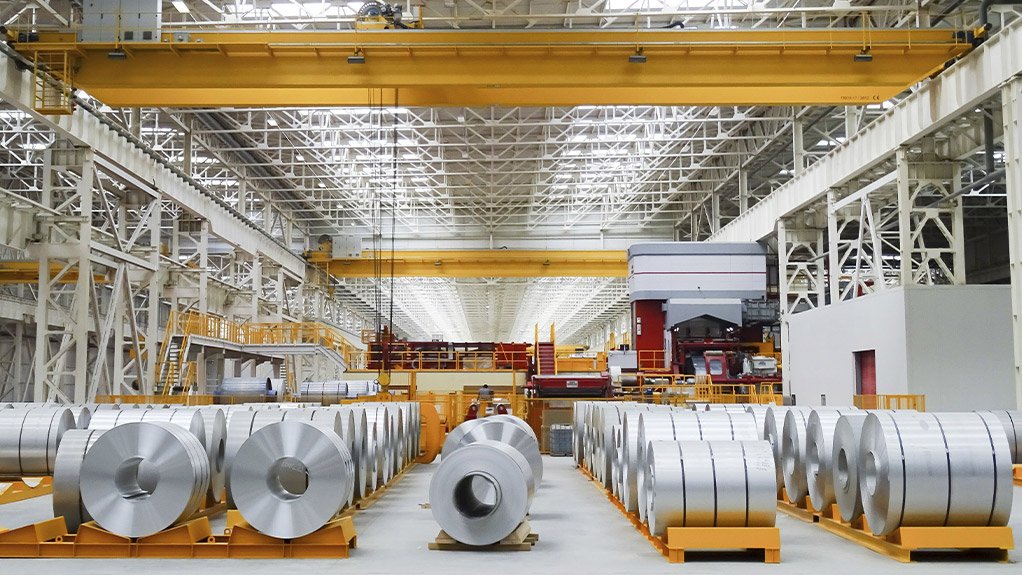
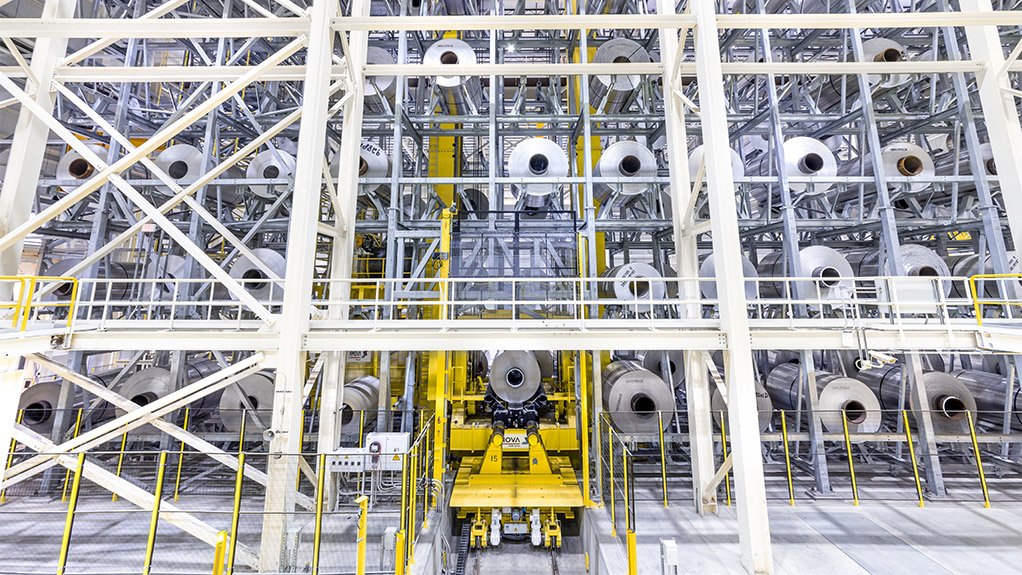
KEEP ROLLING ROLLING ROLLING A cold rolling production line supplied to an international client by SMS group
ALUMINIUM STORE A high bay storage system for aluminium coils also supplied by SMS group
As a global service partner for clients, metallurgical industry plant and integrated systems provider SMS group has developed a concept for extrusion presses offering significant flexibility and efficiency for the steel and aluminium industries.
“SMS group service technicians are specifically trained for extrusion presses and are exclusively responsible for them and, incidentally, also for the plants of third-party producers, which makes us unique,” explains SMS group MD Pieter Bezuidenhout.
The service solution is not only precisely and individually customisable but also simple and entirely practice-orientated.
This service concept from SMS group focuses on quality, productivity and production reliability to sustainably ensure the successful operation and competitiveness of plant operators.
SMS group service experts provide technical advice if needed, considering the prevailing framework conditions. The concept is not rigid, which means that SMS group can react to changed circumstances at any time.
The service for extrusion presses depends on the client’s production planning and customised services are coordinated accordingly. Therefore, taking into consideration scheduled production downtimes, the services are freely combinable with regard to the order, frequency and timeframe.
Moreover, Bezuidenhout points out that a high level of client satisfaction indicates that this concept has proven to be very successful in practice. “Our newest clients of a service contract include metals supplier HMT Höfer Metall Technik, in Hettstedt, Germany.”
HMT Höfer Metall Technik GM Christian Schwarz says about the cooperation with SMS group: “The workflows in our maintenance department are focused on product quality, productivity and production reliability. To achieve this, we have developed a customised service concept, together with SMS group, which is a perfect partner for us, owing to its technical expertise. SMS group also supports us in planning and implementing the measures.”
One of SMS group’s technical services’ long-established clients includes metals processing company Nedal Aluminium, which also opted for the complete service package from SMS group.
The Dutch producers have relied on the support from SMS group for the past ten years, says Bezuidenhout.
“The service experts from SMS group have the know-how and experience to recognise changes in the plants early and rectify them promptly. We were able to measurably improve the availability of our extrusion presses with extrusion forces from 25 MN to 55 MN,” says Nedal technical director Rob van der Meij.
Bezuidenhout adds, “there are only a few specialists in the market, but SMS group has experts particularly trained in the fields of mechanics, hydraulics and control technology for extrusion presses”.
Looking Ahead
SMS group technical service is also prepared for the new challenges of the digital age and Industry 4.0 regarding extrusion presses, says SMS group key account manager Anish James. The latest developments include the electronic parts catalogue (eDoc), as well as training courses using virtual reality (VR) and augmented reality (AR) for maintenance and servicing staff.
With eDoc, the SMS group technical service offers a completely new digital system portraying the technical plant documentation with new convenient functions in a cloud solution. The data is based on bills of materials, drawings and individual documents, which can be retrieved using a single tool in a consolidated and structurally prepared manner.
Parts identification can be done through the bills of materials logs, or by drawing or on-demand scans. Additional information, such as operating manuals or technical data sheets, can be annexed up to an individual parts level and retrieved on mobile devices.
The technical service is testing new forms of knowledge transfer and active support with regard to the innovative training courses. As part of VR, the course participants are equipped with VR glasses in a virtual plant environment where they gain deep insight into, for example, hydraulic components regarding maintenance and servicing.
With AR, additional information is entered into AR data glasses – when watching a real hydraulic component, the internal structure can be virtually seen or virtual instructions for filter changes can be entered. Maintenance technicians, therefore, receive digital support for their work on a specific component.
Further support informa- tion, such as technical documentation, can be retrieved into the glasses’ projection or real VR questions can be discussed with an SMS group trainer.
SMS group hopes that these initiatives will help stave off challenges such as export market volatility and increased competition from international competitors.
“SMS group hopes to expand on their current support to the South African aluminium market by equipping and providing services to enable local aluminium companies to move out of the low-margin products and into high- margin products,” concludes Bezuidenhout.
Comments
Announcements
What's On
Subscribe to improve your user experience...
Option 1 (equivalent of R125 a month):
Receive a weekly copy of Creamer Media's Engineering News & Mining Weekly magazine
(print copy for those in South Africa and e-magazine for those outside of South Africa)
Receive daily email newsletters
Access to full search results
Access archive of magazine back copies
Access to Projects in Progress
Access to ONE Research Report of your choice in PDF format
Option 2 (equivalent of R375 a month):
All benefits from Option 1
PLUS
Access to Creamer Media's Research Channel Africa for ALL Research Reports, in PDF format, on various industrial and mining sectors
including Electricity; Water; Energy Transition; Hydrogen; Roads, Rail and Ports; Coal; Gold; Platinum; Battery Metals; etc.
Already a subscriber?
Forgotten your password?
Receive weekly copy of Creamer Media's Engineering News & Mining Weekly magazine (print copy for those in South Africa and e-magazine for those outside of South Africa)
➕
Recieve daily email newsletters
➕
Access to full search results
➕
Access archive of magazine back copies
➕
Access to Projects in Progress
➕
Access to ONE Research Report of your choice in PDF format
RESEARCH CHANNEL AFRICA
R4500 (equivalent of R375 a month)
SUBSCRIBEAll benefits from Option 1
➕
Access to Creamer Media's Research Channel Africa for ALL Research Reports on various industrial and mining sectors, in PDF format, including on:
Electricity
➕
Water
➕
Energy Transition
➕
Hydrogen
➕
Roads, Rail and Ports
➕
Coal
➕
Gold
➕
Platinum
➕
Battery Metals
➕
etc.
Receive all benefits from Option 1 or Option 2 delivered to numerous people at your company
➕
Multiple User names and Passwords for simultaneous log-ins
➕
Intranet integration access to all in your organisation