Fabricator completes maintenance project at PetroSA refinery
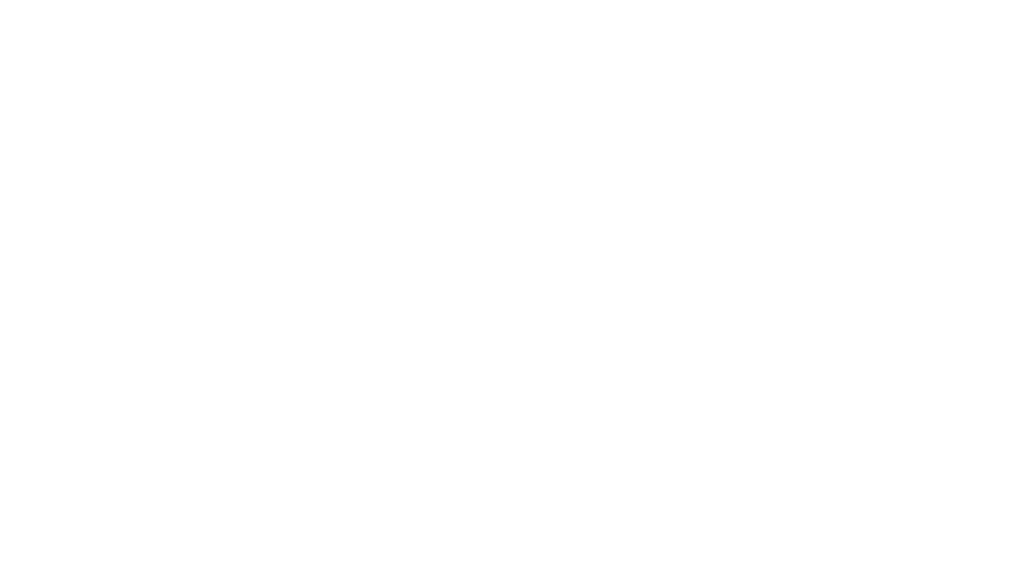
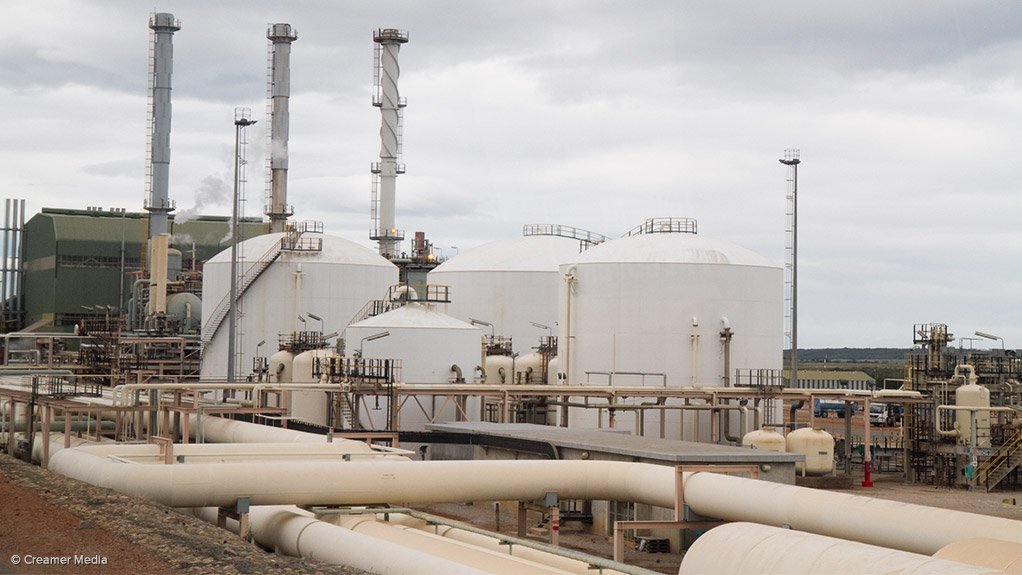
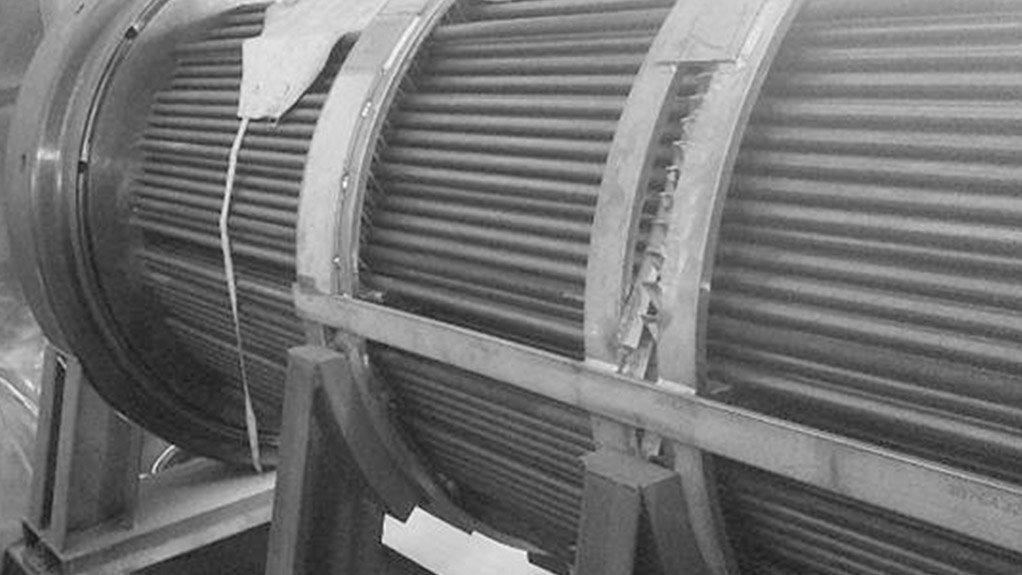
PLANNED MAINTENANCE Steinmüller Africa replaced the Synthol Reactor internal coil U section and structurally replaced and welded the pipe components at PetroSA's GTL refinery, in Mossel Bay
Photo by Duane Daws
SOUND WELD Explosive welding used to fuse tubes to tube plates or headers in high-pressure heat exchangers reduces welding time, plant downtime and relative repair costs
Engineering company Steinmüller Africa, a subsidiary of Germany-based international engineering and services group Bilfinger, completed a planned maintenance project in March for State-owned national oil company PetroSA’s Mossel Bay-based gas-to-liquids refinery, in the Western Cape.
Steinmüller Africa welding operations manager Morne Kidson tells Engineering News that the scope of work involved replacing the Synthol Reactor internal coil U-section and structurally replacing and welding the pipe components. The outside diameters of the pipes varied from 40 mm to 90 mm, with the wall thickness varying between 3 mm and 25 mm.
Additionally, he notes that Steinmüller Africa is an original-equipment manufacturer for various State-owned power utility Eskom’s boilers and has ongoing boiler and high-pressure piping maintenance service contracts at 11 coal-fired power stations.
Further, to assist the power generation sector with skills development, Steinmüller is involved in a training programme for the power utility’s Skills Development and Localisation initiative, says Steinmüller group training administration manager Sonet Jordaan. The company is training ten riggers, ten pipe fitters, ten boilermakers and ten welders through this programme.
Explosive Welding
Kidson highlights the increasing demand for explosive welding technology applications during the maintenance of high-pressure heat exchangers at power stations.
Explosive welding is used to fuse tubes to tube plates or headers in high-pressure heat exchangers. It is performed when a tube is impelled against the tube plate material using the energy from an explosive discharge. In the process, expansion and fusion occur in a high- energy rate impact, Kidson explains.
The ageing coal-fired power stations, such as Kriel and Arnot, in Mpumalanga, have several heat exchangers that need to be refurbished or replaced. They weigh several tons and have up to several thousand tubes that need to be either plugged during maintenance or totally replaced during refurbishment.
“Since the traditional welding methods are time consuming, explosive welding, with a weld metal travel speed of more than 200 000 km/h, reduces welding time, plant downtime and relative repair costs. It also achieves a weld that is expanded, fused and sound,” he says.
Explosive welding is also suitable for the welding of components made from different metals, as well as for welding dissimilar metals, such as carbon steel to stainless steel and stainless steel to titanium. “Steinmüller can apply the process to manufacturing in workshops, or in situ at the power stations,” Kidson emphasises.
He explains that explosive welding technology existed for a while and was mostly applied to on-site heat exchanger tube plugging. “Steinmüller is the first in the world to manufacture a brand new heat exchanger from scratch making use of the explosive technology. It is important to note that the process actually fuses the two mate- rials into one homogenous material. “The fusion line is not detectable through a microscope or etching.”
Although Steinmüller Africa originally introduced explosive welding to Eskom in 2010 under licence from UK-based engineering and maintenance company TEi/Yimpact, it remains the only company in South Africa qualified and approved to perform explosive welding for the power generation sector, he adds.
“Innovation is one of Stein-müller’s values and we are constantly evaluating the market for opportunities. The company is 52 years old and, therefore, has to continually evolve. It is vital to keep abreast of new innovations and technologies, as this allows for the company to anticipate end-user needs.”
Comments
Press Office
Announcements
What's On
Subscribe to improve your user experience...
Option 1 (equivalent of R125 a month):
Receive a weekly copy of Creamer Media's Engineering News & Mining Weekly magazine
(print copy for those in South Africa and e-magazine for those outside of South Africa)
Receive daily email newsletters
Access to full search results
Access archive of magazine back copies
Access to Projects in Progress
Access to ONE Research Report of your choice in PDF format
Option 2 (equivalent of R375 a month):
All benefits from Option 1
PLUS
Access to Creamer Media's Research Channel Africa for ALL Research Reports, in PDF format, on various industrial and mining sectors
including Electricity; Water; Energy Transition; Hydrogen; Roads, Rail and Ports; Coal; Gold; Platinum; Battery Metals; etc.
Already a subscriber?
Forgotten your password?
Receive weekly copy of Creamer Media's Engineering News & Mining Weekly magazine (print copy for those in South Africa and e-magazine for those outside of South Africa)
➕
Recieve daily email newsletters
➕
Access to full search results
➕
Access archive of magazine back copies
➕
Access to Projects in Progress
➕
Access to ONE Research Report of your choice in PDF format
RESEARCH CHANNEL AFRICA
R4500 (equivalent of R375 a month)
SUBSCRIBEAll benefits from Option 1
➕
Access to Creamer Media's Research Channel Africa for ALL Research Reports on various industrial and mining sectors, in PDF format, including on:
Electricity
➕
Water
➕
Energy Transition
➕
Hydrogen
➕
Roads, Rail and Ports
➕
Coal
➕
Gold
➕
Platinum
➕
Battery Metals
➕
etc.
Receive all benefits from Option 1 or Option 2 delivered to numerous people at your company
➕
Multiple User names and Passwords for simultaneous log-ins
➕
Intranet integration access to all in your organisation