FLS completes major upgrade of Delmas polyurethane facility
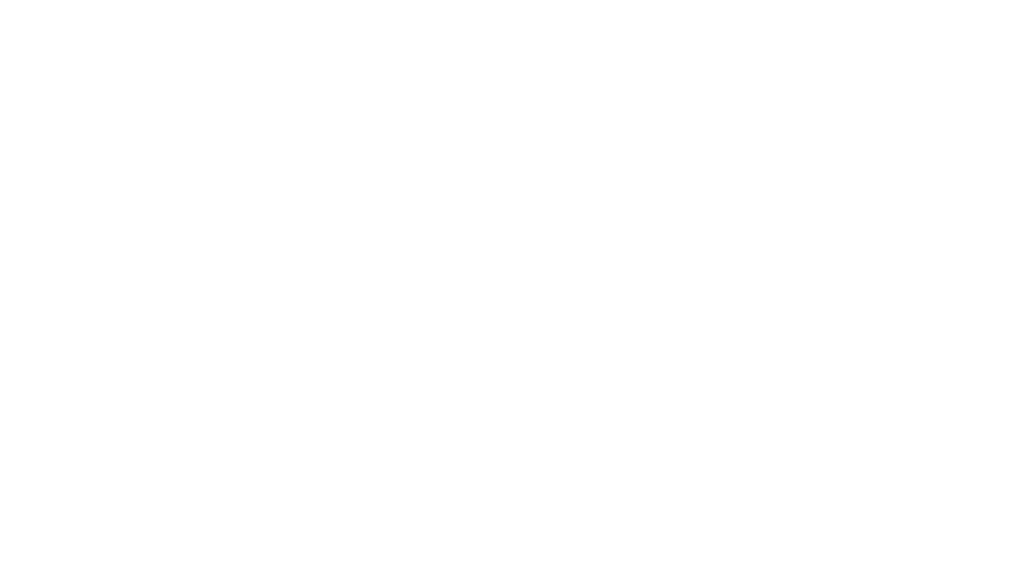
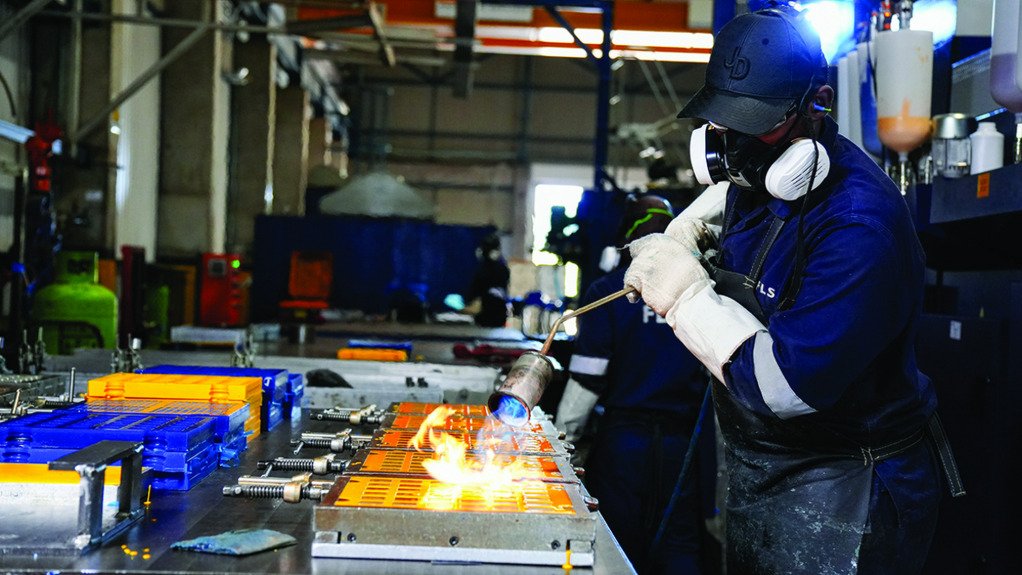
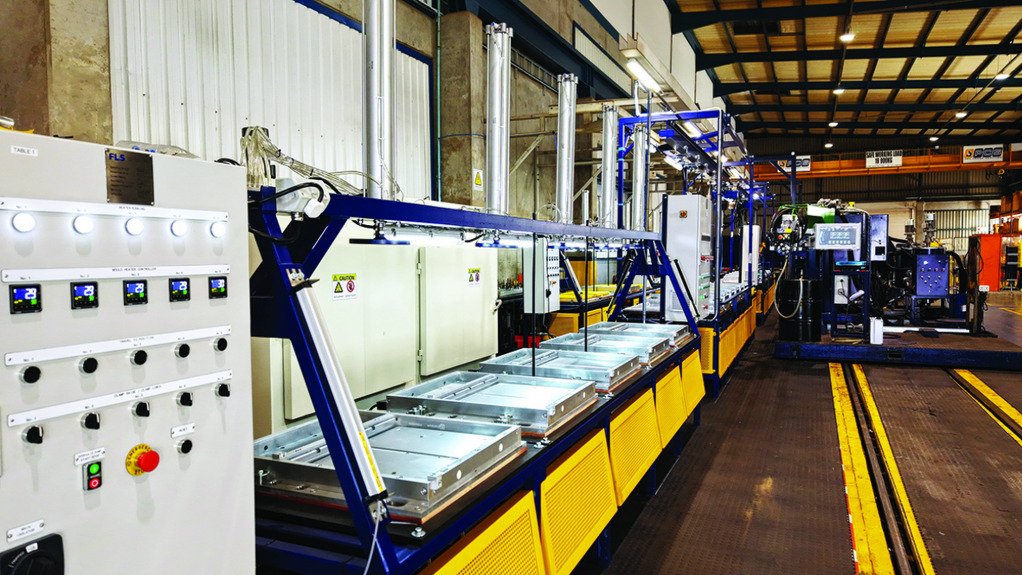
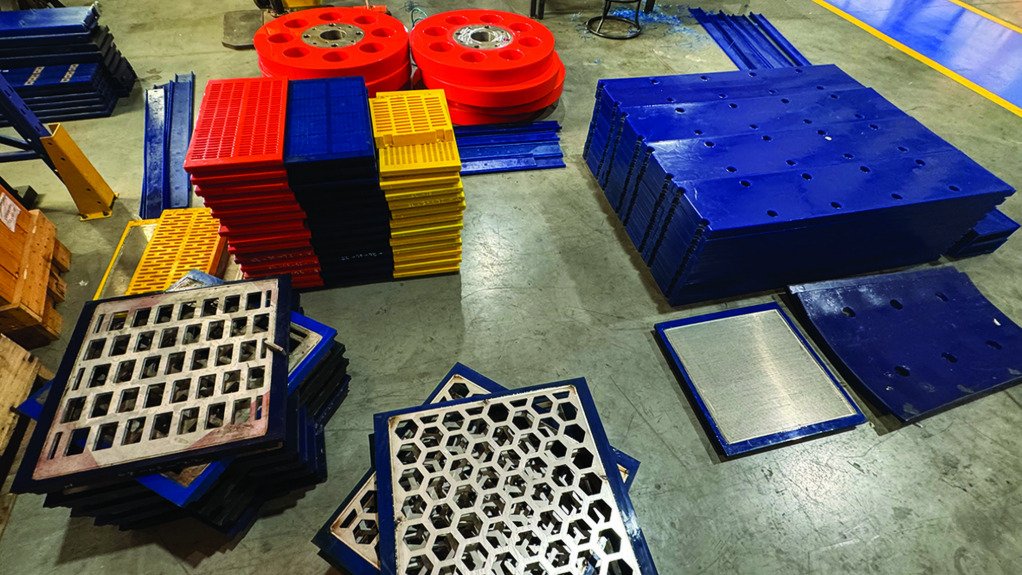
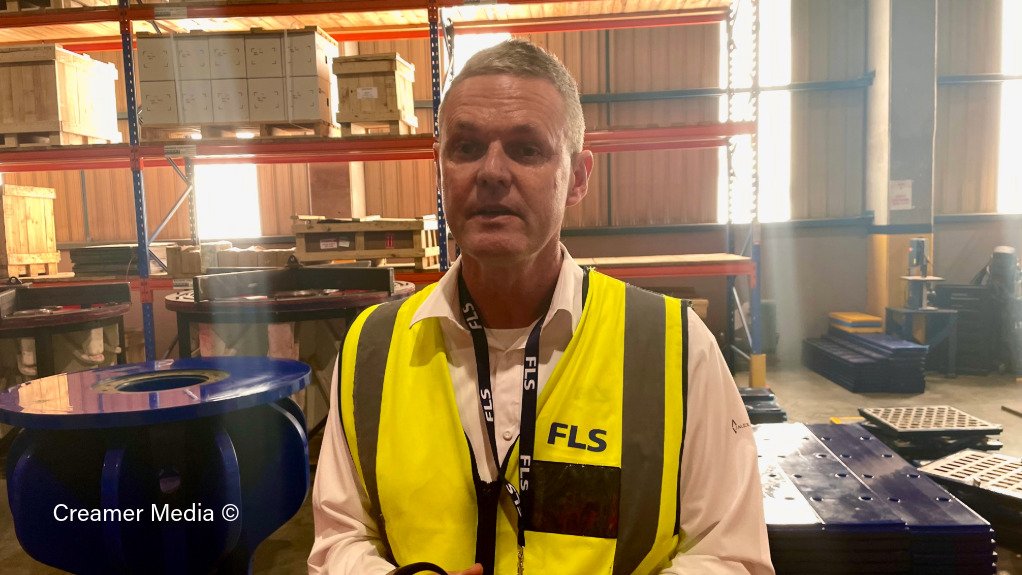
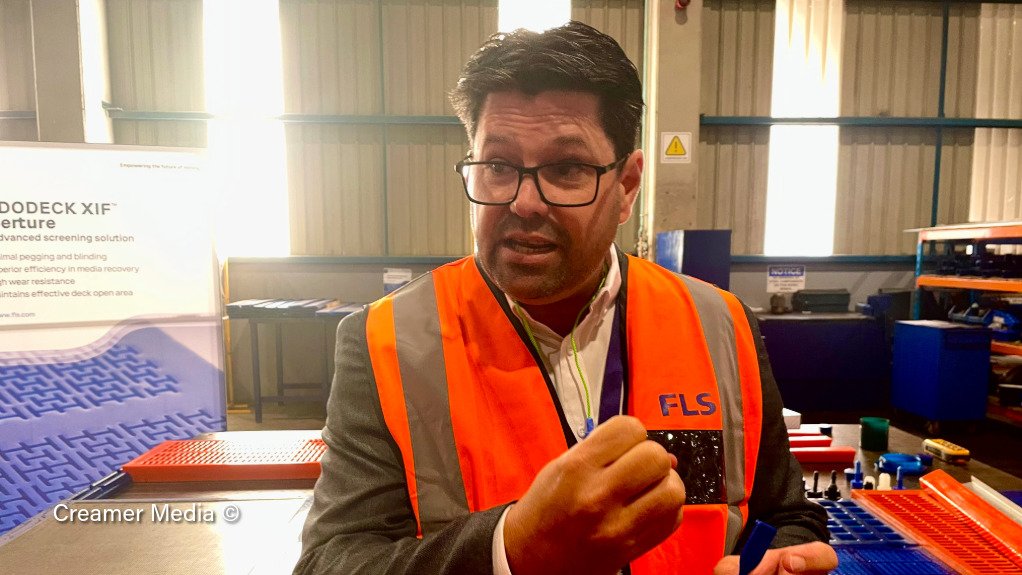
FLS global manufacturing head of polyurethane operations at Warren Walker
Photo by Creamer Media
FLS screen and feeder consumables service line director Brad Shepherd
Photo by Creamer Media
Full flowsheet minerals processing supplier FLS has completed a significant upgrade to its polyurethane manufacturing facility in Delmas, Mpumalanga, to position the site as a key global hub for the production of the company’s advanced NexGen wear-resistant material.
The facility expansion forms part of a wider modernisation programme by FLS, aimed at strengthening its supply chains, increasing manufacturing efficiency and enhancing sustainability across its global footprint.
FLS screen and feeder consumables service line director Brad Shepherd said the investment at Delmas aligned with the company’s global strategy to standardise and optimise production processes.
“This is a milestone for us. We are integrating cutting-edge technology and modern manufacturing methodologies across all our polyurethane plants, and Delmas is leading the way.
“The upgrade enables us to respond more quickly and reliably to customer needs across Africa, the Middle East and Europe,” he said on July 18 during a site visit, which Engineering News attended.
The centrepiece of the upgrade is the introduction of purpose-built infrastructure to produce NexGen screen media, which is a polyurethane material developed by FLS to deliver extended wear life, reduced maintenance and improved operational efficiency.
In on-site trials, screen panels made from NexGen demonstrated up to three times the wear life of conventional rubber and polyurethane products, making it an attractive option for industries that rely on high performance screening solutions.
“Rubber has been the go-to in that really high impact, high abrasion situation for many years. But what we've been able to do through extensive research and development is design polymers that surpass the outcomes of rubber by a factor of three.
“This means really big upgrades for our customers in the way that they think about and interact with screen media,” he told Engineering News.
Shepherd said the NextGen material has a very high tensile strength and a very high abrasion loss index. It also has extremely high impact resistance properties.
“So all those physical properties enable it to perform much better in service. It also enables us to construct polyurethane media in a way that allows for a much larger open area, without compromising maintainability,” he explained.
FLS global manufacturing head of polyurethane operations Warren Walker noted that the Delmas facility was the first of the company’s five global polyurethane plants to complete this transition.
“We have installed new, latest-generation polyurethane machines, precision tooling and dedicated preheating ovens for inserts. This allows us to significantly increase our output while ensuring consistent quality,” he said.
The facility now includes two trommel screen media stations and three screen media stations, each tailored to produce NexGen products.
One of the key technologies introduced is a programmable auto-calibrating polyurethane machine capable of adjusting material hardness to suit specific applications.
“The flexibility to produce varying hardness levels is critical. It means we can tailor our screen media precisely to the customer’s application, ensuring optimum performance and longevity,” Walker said.
To complement this, a high capacity polyurethane machine capable of pouring up to 42 kg/m is now in operation at the facility. This system is particularly suited to applications requiring large volume pours, such as flotation spare parts and vertical mill components.
The Delmas facility previously received a significant upgrade in 2019, when a six-axis machining centre was introduced for tooling precision, along with robotic welding systems for manufacturing screen media panel inserts, and a computer numerical control controlled spiral welding machine to produce wedge wire products.
The latest round of investments improved energy efficiency in the layout and equipment design.
“We have incorporated smart energy-saving features like individual temperature control on each casting table station. This avoids the need to heat large surface areas unnecessarily and contributes to our carbon reduction goals,” Walker said.
In support of FLS’s energy efficiency efforts, the company installed 300 kW of solar generation capacity at the Delmas site in 2024. Plans are now in place to expand this by another 500 kW in 2026, along with the integration of a battery energy storage system.
The Delmas plant is also equipped to handle the complete fabrication of vibrating screens, from raw material processing and in-house machining to assembly and factory acceptance testing.
This vertical integration allows the company to customise its solutions for customers, with tighter control over the quality and lead times.
Shepherd explained that FLS operates both as an original-equipment manufacturer and a screen media specialist, supplying screen panels for all types and brands of vibrating screens, feeders and trommel screens.
“We don’t just supply products. We work closely with our customers through our network of on-the-ground specialists to assess site conditions and select the best screening media for their specific needs,” he said.
Shepherd noted that many older processing plants treat materials that differ from their original design specifications. In these cases, screen efficiency can often only be improved by optimising the screen media.
“This is where NexGen makes a real difference. Combined with the correct aperture design, it allows customers to get more life and better performance from their screens,” he said.
Unlike injection-moulded polyurethane, which can compromise the structural integrity of screen panels, FLS’s proprietary process retains its superior mechanical properties, resulting in a tougher and more durable product Shepherd explained.
“We have never used injection moulding because it reduces the quality of the end product. Our process delivers a product that stands up to the toughest operating conditions and offers lasting value,” he said.
Walker added that the expansion at Delmas supported FLS’s global operations while also contributing to the local economy.
“Our commitment to local manufacturing is evident in the scale of our investment and the jobs we have created. We have expanded our workforce, prioritised local recruitment and significantly grown our apprenticeship programme,” he said.
“We've had a good base of individuals who have been with us for a long time, working in the polyurethane shop that existed previously. This capacity upgrade meant a lot more training and more people.
“At the end of the day, it is going to bring about a lot more opportunity for the local people with respect to employment, because what we're looking for here is enablement through throughput capacity and high-quality products. That means more people are going to be needed to help us do that,” Shepherd said.
Comments
Press Office
Announcements
What's On
Subscribe to improve your user experience...
Option 1 (equivalent of R125 a month):
Receive a weekly copy of Creamer Media's Engineering News & Mining Weekly magazine
(print copy for those in South Africa and e-magazine for those outside of South Africa)
Receive daily email newsletters
Access to full search results
Access archive of magazine back copies
Access to Projects in Progress
Access to ONE Research Report of your choice in PDF format
Option 2 (equivalent of R375 a month):
All benefits from Option 1
PLUS
Access to Creamer Media's Research Channel Africa for ALL Research Reports, in PDF format, on various industrial and mining sectors
including Electricity; Water; Energy Transition; Hydrogen; Roads, Rail and Ports; Coal; Gold; Platinum; Battery Metals; etc.
Already a subscriber?
Forgotten your password?
Receive weekly copy of Creamer Media's Engineering News & Mining Weekly magazine (print copy for those in South Africa and e-magazine for those outside of South Africa)
➕
Recieve daily email newsletters
➕
Access to full search results
➕
Access archive of magazine back copies
➕
Access to Projects in Progress
➕
Access to ONE Research Report of your choice in PDF format
RESEARCH CHANNEL AFRICA
R4500 (equivalent of R375 a month)
SUBSCRIBEAll benefits from Option 1
➕
Access to Creamer Media's Research Channel Africa for ALL Research Reports on various industrial and mining sectors, in PDF format, including on:
Electricity
➕
Water
➕
Energy Transition
➕
Hydrogen
➕
Roads, Rail and Ports
➕
Coal
➕
Gold
➕
Platinum
➕
Battery Metals
➕
etc.
Receive all benefits from Option 1 or Option 2 delivered to numerous people at your company
➕
Multiple User names and Passwords for simultaneous log-ins
➕
Intranet integration access to all in your organisation