Grout injection plant recognised for safety track record
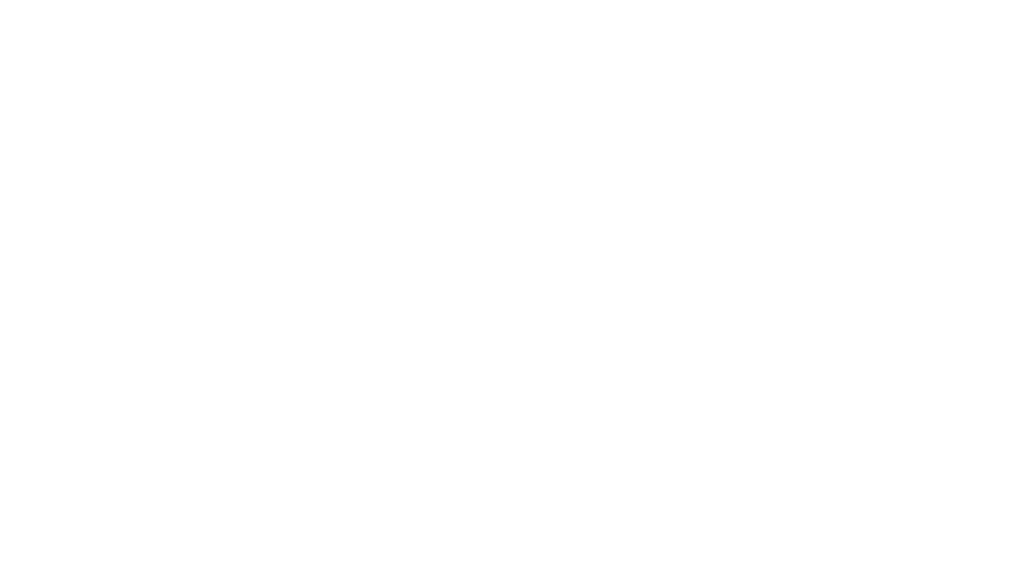
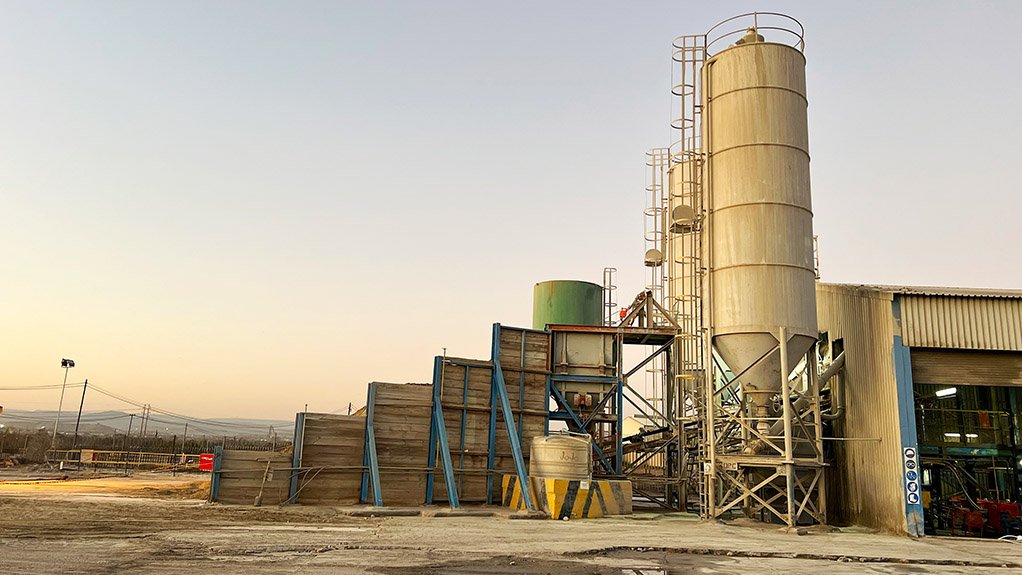
Grout injection plants pump grout mixtures at high pressures to underground workings
A local grout injection plant that includes operations at depths up to 1 600 m below surface has achieved a significant milestone, having operated for 20 years without a single lost-time injury.
Murray & Roberts Cementation project manager Andre van Buuren emphasises the company’s depth of experience as the basis for its grout injection plant’s safety accolade. Located between Northam and Thabazimbi in South Africa’s Limpopo province, the grout plant consists of a 36-person team that oversees the logistics of mixing on surface, managing over 5 km of pipeline to underground destinations, and injecting grout at the workface to prevent inundation where water is intersected during mine development.
“Achieving 20 years without an injury is a real testament to the collective effort of our team, applying our corporate strategies and taking personal accountability for everything that happens on site,” says Van Buuren.
The Northam grout injection plant regularly pumps specialised grout mixtures at pressures of up to 10 MPa to underground workings. Over 20 t of cementitious material are commonly injected into designated areas over a three- to four-day period, according to Murray & Roberts Cementation senior project manager Pieter Oosthuysen. A recent water intersection incident required as much as 56 t- to be injected at high pressure to stem the flow of groundwater at a single point.
“A compact surface team oversees the running of the plant, which includes two 100 t silos among a range of equipment and backup units,” says Oosthuysen. “Most are part of the underground teams, working in day shifts and night shifts. They follow the mining teams as the mine deepens, extending the grout range to allow injection to be conducted whenever necessary.”
Safety is also a key aspect of the training that injection plant staff receive at the company’s training academy, which includes a mock-up of a grout plant as part of the experiential training.
Van Buuren highlights the importance of engaging every member of the team in the safety strategies employed, including the selection and adoption of the most appropriate personal protective equipment such as boots or glasses to ensure these are fit for purpose.
Grout plant foreman Louis Neethling emphasises the culture of care within each team, where every member is expected to look after not only themselves but those around them.
“We recognise that promoting safety is rather like sweeping water uphill,” says Neethling. “If you stop sweeping, the water will run back again; it is an ongoing task to ensure safe behaviour, and to find ways of improving safety performance.”
Comments
Press Office
Announcements
What's On
Subscribe to improve your user experience...
Option 1 (equivalent of R125 a month):
Receive a weekly copy of Creamer Media's Engineering News & Mining Weekly magazine
(print copy for those in South Africa and e-magazine for those outside of South Africa)
Receive daily email newsletters
Access to full search results
Access archive of magazine back copies
Access to Projects in Progress
Access to ONE Research Report of your choice in PDF format
Option 2 (equivalent of R375 a month):
All benefits from Option 1
PLUS
Access to Creamer Media's Research Channel Africa for ALL Research Reports, in PDF format, on various industrial and mining sectors
including Electricity; Water; Energy Transition; Hydrogen; Roads, Rail and Ports; Coal; Gold; Platinum; Battery Metals; etc.
Already a subscriber?
Forgotten your password?
Receive weekly copy of Creamer Media's Engineering News & Mining Weekly magazine (print copy for those in South Africa and e-magazine for those outside of South Africa)
➕
Recieve daily email newsletters
➕
Access to full search results
➕
Access archive of magazine back copies
➕
Access to Projects in Progress
➕
Access to ONE Research Report of your choice in PDF format
RESEARCH CHANNEL AFRICA
R4500 (equivalent of R375 a month)
SUBSCRIBEAll benefits from Option 1
➕
Access to Creamer Media's Research Channel Africa for ALL Research Reports on various industrial and mining sectors, in PDF format, including on:
Electricity
➕
Water
➕
Energy Transition
➕
Hydrogen
➕
Roads, Rail and Ports
➕
Coal
➕
Gold
➕
Platinum
➕
Battery Metals
➕
etc.
Receive all benefits from Option 1 or Option 2 delivered to numerous people at your company
➕
Multiple User names and Passwords for simultaneous log-ins
➕
Intranet integration access to all in your organisation