Heat transfer tech offers more bang for buck
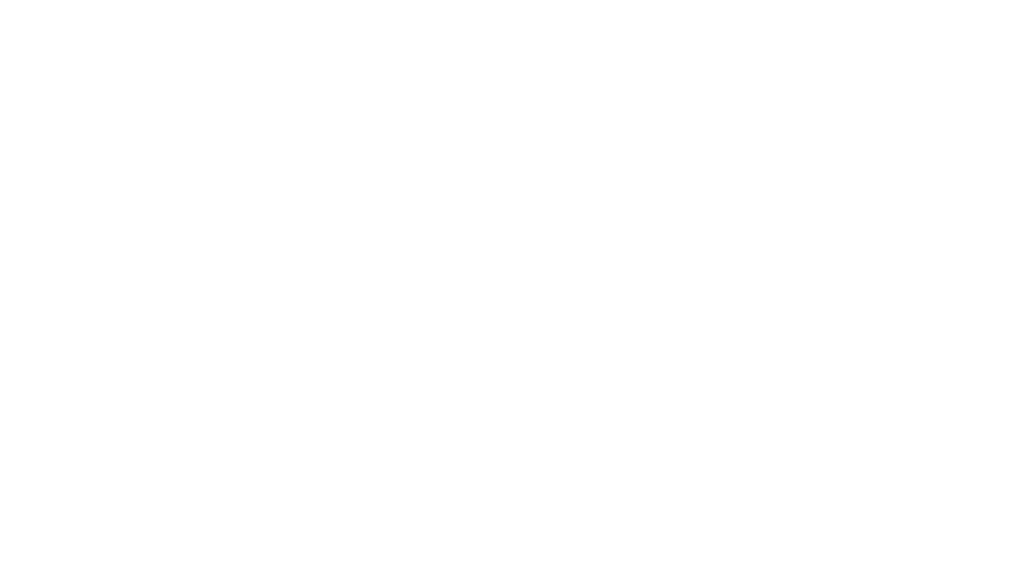
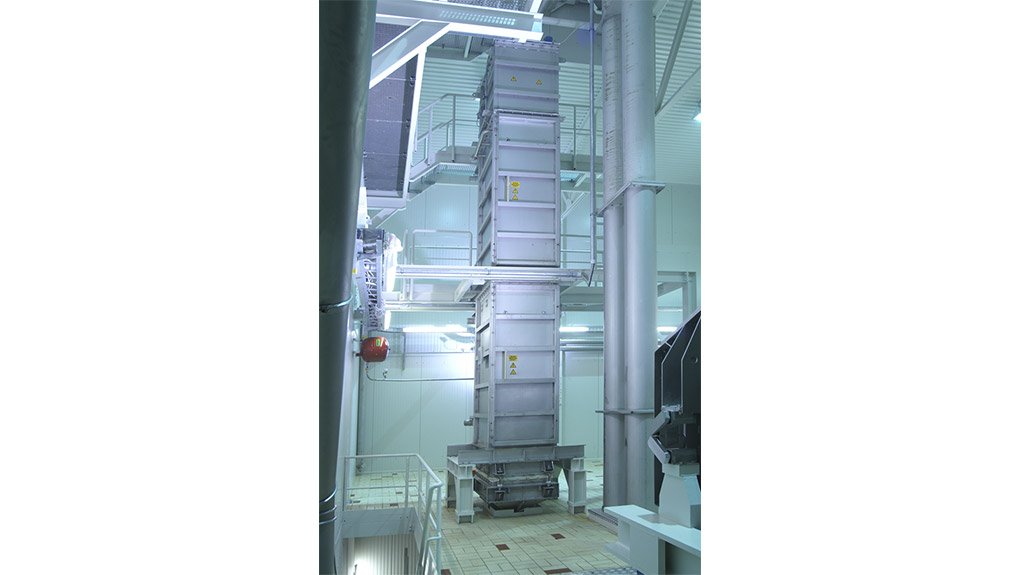
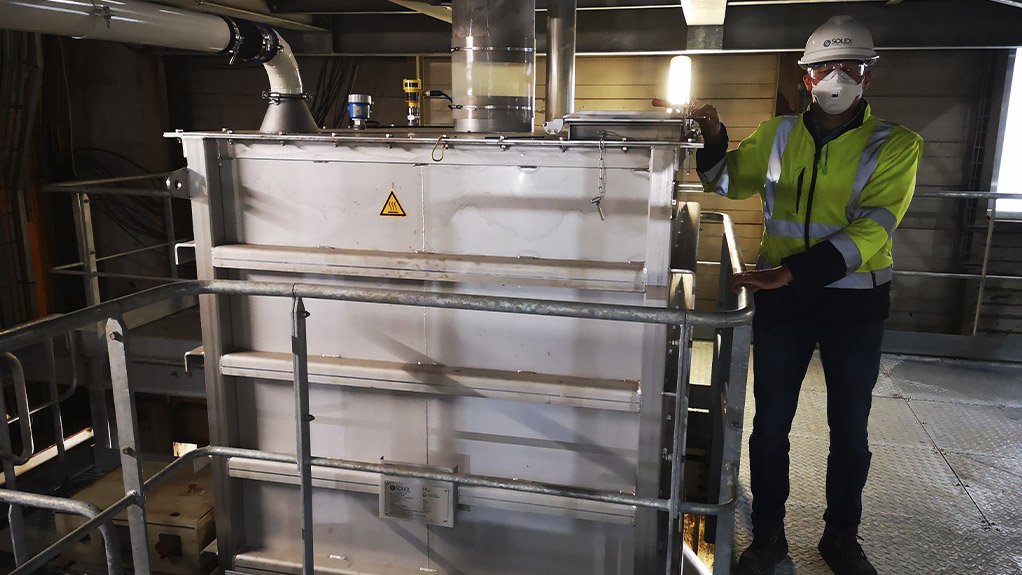
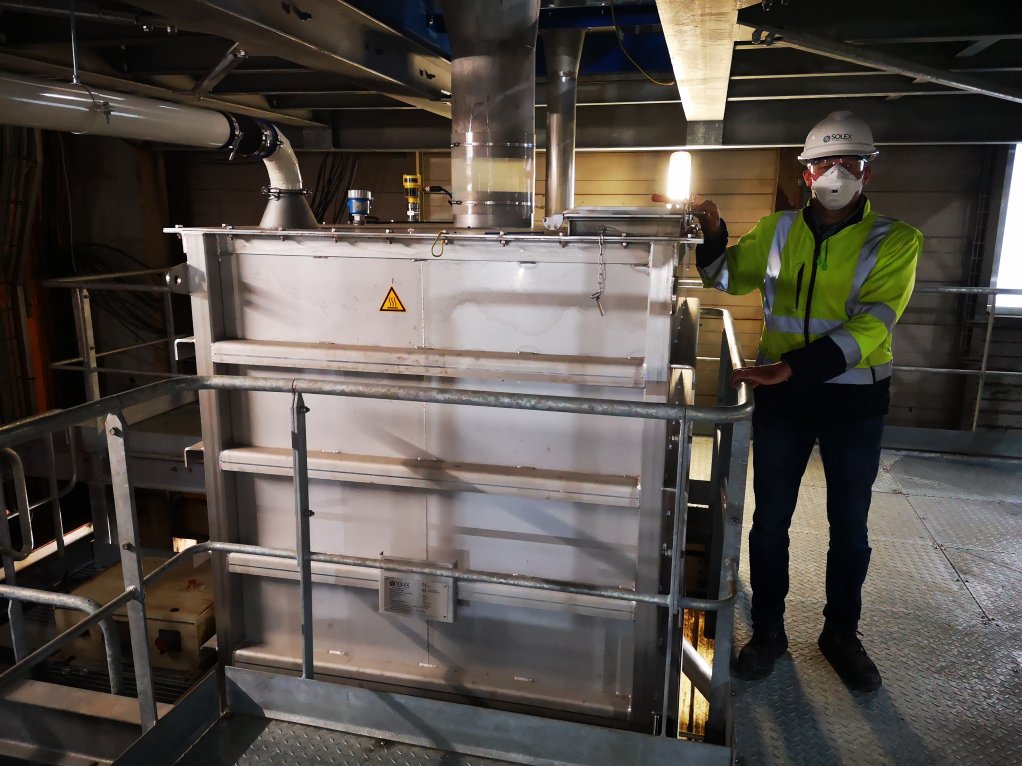
COOLING DOWN IWC has partnered with Solex to distribute heat transfer technology
SOLEX SUGAR COOLER UNIT Sugar processing plants can increase capacity easily with SOlex's products
SOLEX SUGAR COOLER UNIT Sugar processing plants can increase capacity easily with SOlex's products
Thermal engineering solutions company Industrial Water Cooling (IWC) has partnered with Canada-based developer, designer and manufacturer Solex Thermal Science to distribute Solex’s technology to Southern Africa to cool, heat or condition bulk solid products, for example sugar.
Using fluid bed coolers, which use large fans to fluidise the sugar and another large fan to extract the air, is the traditional way of cooling sugar. A plant then treats the extracted air with expensive equipment such as a bag filter. This installation takes up a lot of space, owing to its air pipes and auxiliary equipment.
IWC heat exchanger division manager Carl van Maanen says a medium-capacity sugar plant usually uses a combined drum dryer cooler to process the sugar crystals before storage.
Often, the plant starts to use the equipment over the design capacity, consequently resulting in the sugar crystals not having the appropriate moisture content and the sugar being too hot for optimal storage, he explains.
However, by transforming a combined drum dryer and cooler into a one-drum dryer and adding a Solex heat exchanger, the plant can provide the required cooling capacity.
This retrofit allows for increased sugar production capacity and a higher quality of finished sugar using limited investment.
The exchanger can operate as a secondary cooler after an existing fluid bed or drum cooler when cooling capacity becomes a constraint.
As an alternative, the Solex heat exchanger uses cold water as cooling medium in an indirect mode, which reduces the risk of contamination, bad odours or bacteria.
“Solex’s technology fits well in IWC’s portfolio. IWC has experience in the design and supply of cooling towers, plate and frame heat exchangers, dry coolers and chillers,” explains Van Maanen.
The heat exchanger uses cold water to cool the sugar in a closed loop and, therefore, this cold water needs to be cooled before it enters the sugar cooler. Through IWC’s expertise, it is equipped to recommend the most appropriate technology based on a customer’s site conditions to ensure customers have the appropriate equipment to work alongside the heat exchanger. Through Solex and IWC’s partnership, customers can be provided with a complete turnkey solution.
Further, some of heat exchanger’s benefits include low energy consumption and a small installation footprint, as well as a modular design that allows for additional units to be added to increase capacity.
It is installed vertically and can be retrofitted into existing sugar processing facilities.
It can also be designed for a wide capacity range, which can vary from between 10 tph to 100 tph and 250 tph. It does not use air or air treatment and ensures no external contamination. The Solex heat exchanger is also operator friendly, with the process conditions easily set up for optimal storage conditions of the sugar.
The heat exchanger cools the sugar using only 0.4 kWh/t, compared to fluid bed and rotary drum coolers, which have an energy requirement of about 5.0 kWh/t.
“This is a 90% reduction in the energy required for cooling. In addition to substantial cost savings, this also supports a reduction in the greenhouse-gas footprint of sugar production when fossil fuels are used to produce energy,” adds Van Maanen.
The technology can be applied in many industries, and in applications used for heating, cooling or conditioning of solid products, such as sugar crystals, cement, oil seeds, polymer pellets, foundry sands, slag and coffee beans, he concludes.
Comments
Press Office
Announcements
What's On
Subscribe to improve your user experience...
Option 1 (equivalent of R125 a month):
Receive a weekly copy of Creamer Media's Engineering News & Mining Weekly magazine
(print copy for those in South Africa and e-magazine for those outside of South Africa)
Receive daily email newsletters
Access to full search results
Access archive of magazine back copies
Access to Projects in Progress
Access to ONE Research Report of your choice in PDF format
Option 2 (equivalent of R375 a month):
All benefits from Option 1
PLUS
Access to Creamer Media's Research Channel Africa for ALL Research Reports, in PDF format, on various industrial and mining sectors
including Electricity; Water; Energy Transition; Hydrogen; Roads, Rail and Ports; Coal; Gold; Platinum; Battery Metals; etc.
Already a subscriber?
Forgotten your password?
Receive weekly copy of Creamer Media's Engineering News & Mining Weekly magazine (print copy for those in South Africa and e-magazine for those outside of South Africa)
➕
Recieve daily email newsletters
➕
Access to full search results
➕
Access archive of magazine back copies
➕
Access to Projects in Progress
➕
Access to ONE Research Report of your choice in PDF format
RESEARCH CHANNEL AFRICA
R4500 (equivalent of R375 a month)
SUBSCRIBEAll benefits from Option 1
➕
Access to Creamer Media's Research Channel Africa for ALL Research Reports on various industrial and mining sectors, in PDF format, including on:
Electricity
➕
Water
➕
Energy Transition
➕
Hydrogen
➕
Roads, Rail and Ports
➕
Coal
➕
Gold
➕
Platinum
➕
Battery Metals
➕
etc.
Receive all benefits from Option 1 or Option 2 delivered to numerous people at your company
➕
Multiple User names and Passwords for simultaneous log-ins
➕
Intranet integration access to all in your organisation