High-quality seals and correct maintenance critical
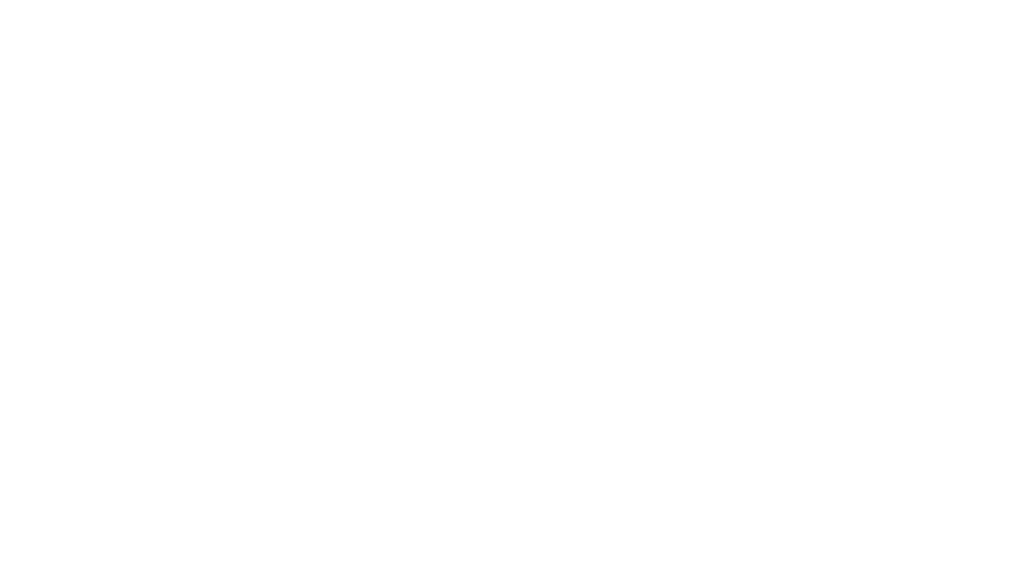
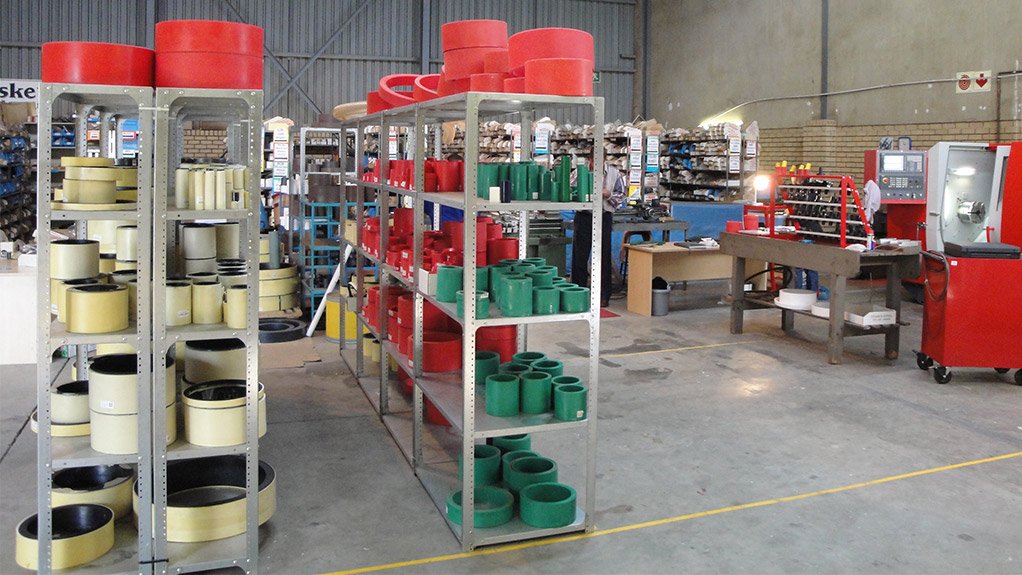
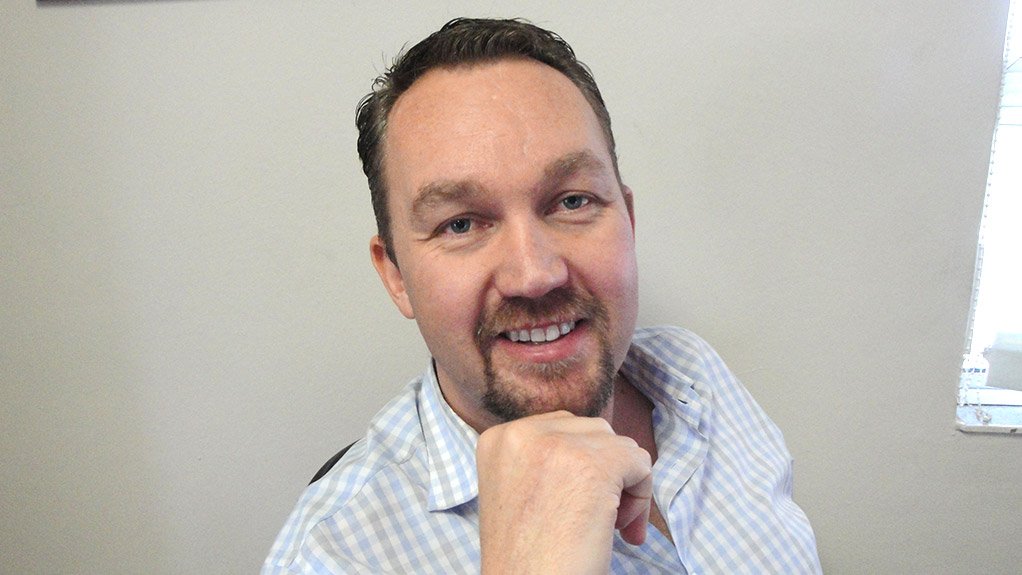
COMPLETE SERVICE Seal & Gasket Supplies’ core strengths are providing technical advice and support for customers before and after buying a product
CHRIS EHINGER One of the major causes of seal failure is a damaged piston rod, which is caused by misalignment
Hydraulic and pneumatic seal supplier Seal & Gasket Supplies stresses that buying substandard components will lead to more frequent breakdowns, resulting in overall work productivity decreasing and ultimately culminating in costly long-term consequences for businesses.
“Companies need to train their operators to identify potential maintenance problems before they transpire. For example, for a seal to operate safely and efficiently, hydraulic equipment needs to operate within a specified maximum speed, temperature and pressure range,” Seal & Gasket Supplies director Chris Ehinger tells Engineering News.
Ehinger says one of Seal & Gasket Supplies’ core strengths is providing technical advice and support for customers before and after buying a product.
“Reliability can be determined not only by the product but also according to the levels of service and support received by suppliers.”
Ehinger stresses the importance of ensuring that seals are well maintained, as this should be a key area of companies’ preventative maintenance policy.
Quality Control
Ehinger says operators should undertake certain quality control methods to avoid rod-seal leaks, subsequently eliminating the need to regularly replace cylinders and rods.
“One of the major causes of seal failure is a damaged piston rod, which is caused by misalignment. Poor alignment between the cylinder and the load will cause piston and gland bearings to be exposed to side loading, causing damage to the rod or the surface of the tube and, therefore, the seal.”
Ehinger stresses that cylinder and rod replacements can be extremely costly. A new piston rod is a customised part that is made to order; it cannot be repaired and will need to be replaced after a complete strip down and rebuild of the cylinder.
“While there are not any real solutions, other than cylinder review and accuracy in machine alignment, it is important to ensure that piston and gland bearings are correctly proportioned to support the cylinder loads and handle the thrust forces created by the application,” he says.
Moreover, Ehinger highlights the importance of customers’ understanding that cylinders are designed to provide linear force and that the maximum thrust of this force is limited by its rod diameter and overall length.
“In cases where clients have requested a sealing solution to prevent the occurrence of misalignments, we have identified and manufactured a profile ideally suited for heavy-duty mobile and stationary service, which is highly resistant to side loading and insensitive to pressure spikes.”
Further, he says that operators must ensure the seal housing is free from any damage that could possibly harm the seal.
“It is important to remove all sharp edges and burrs from metal parts, especially ports, grooves and threads over or through which the seal passes during assembly.
“All seal housing areas and surfaces adjacent to the passage of the seal must be cleaned to ensure that all metallic bits and other dirt particles have been removed,” Ehinger notes.
He advises that, to avoid premature rod-seal failure, all seals and components should be lubricated with clean operating fluid, as “fluid contamination is often the result of water or air suspended in the fluid”.
Ehinger notes that water affects the lubricity of the fluid and causes many seal materials to harden, crumble or disintegrate.
“In these instances, we offer a hydrolysis-resistant polyurethane seal, as this material is more resilient to high water-based fluids at higher temperatures.
“
Heated air bubbles, commonly caused by a rapid increase in hydraulic pressure, are also a common problem when dealing with hydraulic applications. The intensely heated bubbles sit at the lip of the seal and cause small, damaging marks on the inner surface of the seal.”
He says it is important for the seal to be the correct size, type and material.
“The choice of seal material is extremely important in eliminating problems caused by extreme temperature applications or where the seals may be damaged by chemicals. “While a static seal, such as a cylinder body O-ring, can tolerate swelling to a degree, the same cannot be said for a dynamic seal, which will cause friction and faster wear if swelling occurs,” Ehinger warns.
He says the best solution to this problem is for customers to ask their seal supplier for a material recommendation based on a particular fluid.
Further, Ehinger highlights that seals must be stored – distortion free – in a cool, dry and dark place prior to fitting.
“Where the difference between a thread diameter, over which the seal must pass, and the seal diameter is small, an operator must use some form of protection over the thread. For example, a fitting sleeve made out of hard plastic.”
Ehinger says where seals are fitted to pistons that are awaiting further fitting, the seals must not be subjected to misaligned or localised loading, as this will cause deformation.
He urges operators to “remember to flush the hydraulic system carefully before connecting the cylinder to the system”.
“Special seal designs should be considered when a severe flow restriction at the head end of the cylinder is accompanied by accidental pressure increases. “This, together with an oversized rod, can cause high-pressure leakages and rapid wear,” states Ehinger.
He adds that Seal & Gasket Supplies most commonly recommends polyurethane seals as being one of the most effective materials to withstand this high-pressure leakage.
Ehinger states that the company emphasises the importance of understanding how the application works and the pressure required to improve operational efficiencies.
“For example, the cylinder may not work to its full capacity because some elastomer lipseals require a minimum pressure level to be fully energised, which is why companies must consult with a sealing specialist who will recommend the required seal, based on the amount of pressure being applied,” he states.
“It is important that any innovations undertaken on an application provide improved levels of service efficiency and productivity,” Ehinger concludes.
Comments
Press Office
Announcements
What's On
Subscribe to improve your user experience...
Option 1 (equivalent of R125 a month):
Receive a weekly copy of Creamer Media's Engineering News & Mining Weekly magazine
(print copy for those in South Africa and e-magazine for those outside of South Africa)
Receive daily email newsletters
Access to full search results
Access archive of magazine back copies
Access to Projects in Progress
Access to ONE Research Report of your choice in PDF format
Option 2 (equivalent of R375 a month):
All benefits from Option 1
PLUS
Access to Creamer Media's Research Channel Africa for ALL Research Reports, in PDF format, on various industrial and mining sectors
including Electricity; Water; Energy Transition; Hydrogen; Roads, Rail and Ports; Coal; Gold; Platinum; Battery Metals; etc.
Already a subscriber?
Forgotten your password?
Receive weekly copy of Creamer Media's Engineering News & Mining Weekly magazine (print copy for those in South Africa and e-magazine for those outside of South Africa)
➕
Recieve daily email newsletters
➕
Access to full search results
➕
Access archive of magazine back copies
➕
Access to Projects in Progress
➕
Access to ONE Research Report of your choice in PDF format
RESEARCH CHANNEL AFRICA
R4500 (equivalent of R375 a month)
SUBSCRIBEAll benefits from Option 1
➕
Access to Creamer Media's Research Channel Africa for ALL Research Reports on various industrial and mining sectors, in PDF format, including on:
Electricity
➕
Water
➕
Energy Transition
➕
Hydrogen
➕
Roads, Rail and Ports
➕
Coal
➕
Gold
➕
Platinum
➕
Battery Metals
➕
etc.
Receive all benefits from Option 1 or Option 2 delivered to numerous people at your company
➕
Multiple User names and Passwords for simultaneous log-ins
➕
Intranet integration access to all in your organisation