Is there a future for exoskeletons in SA mining?
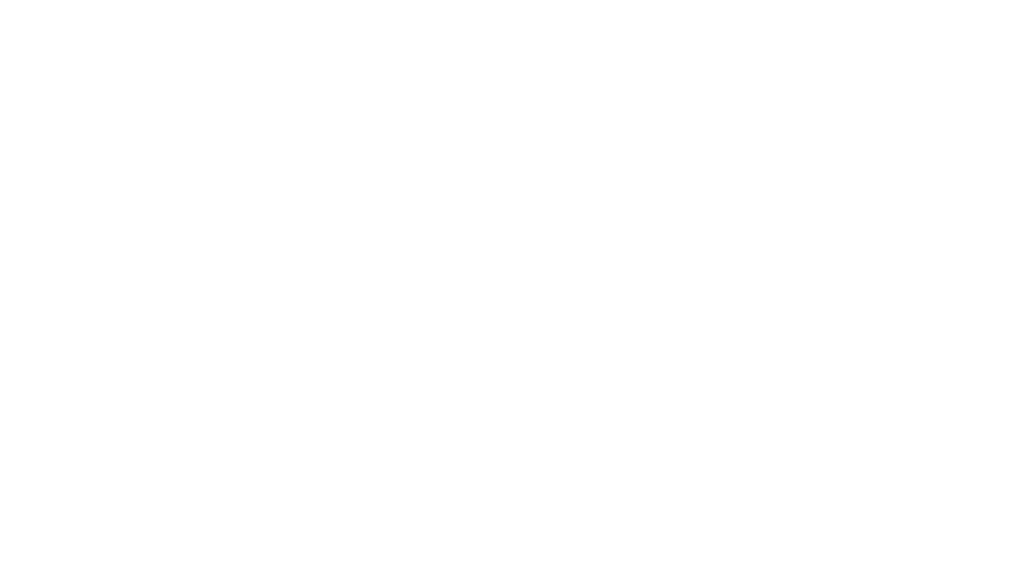
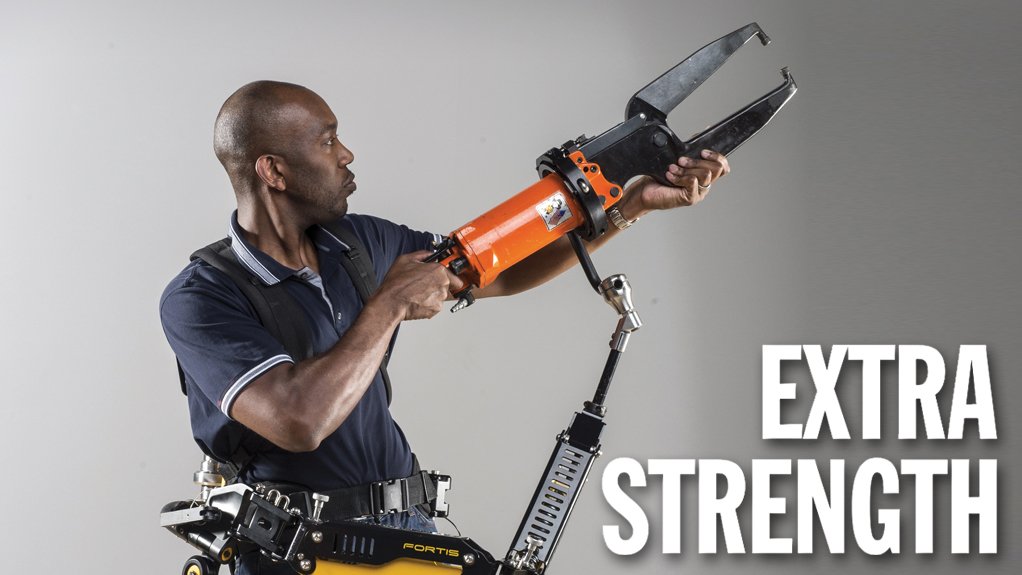
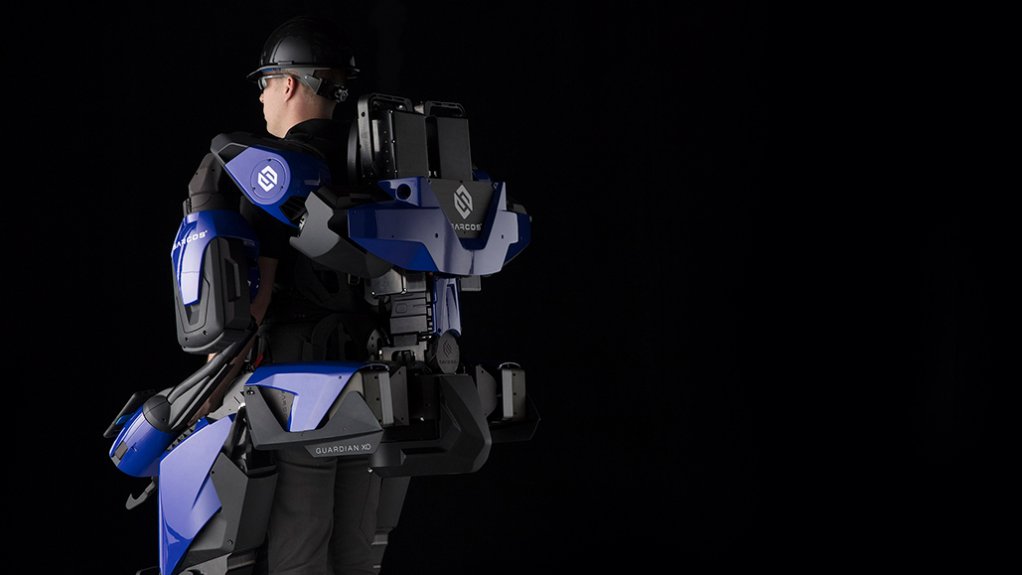
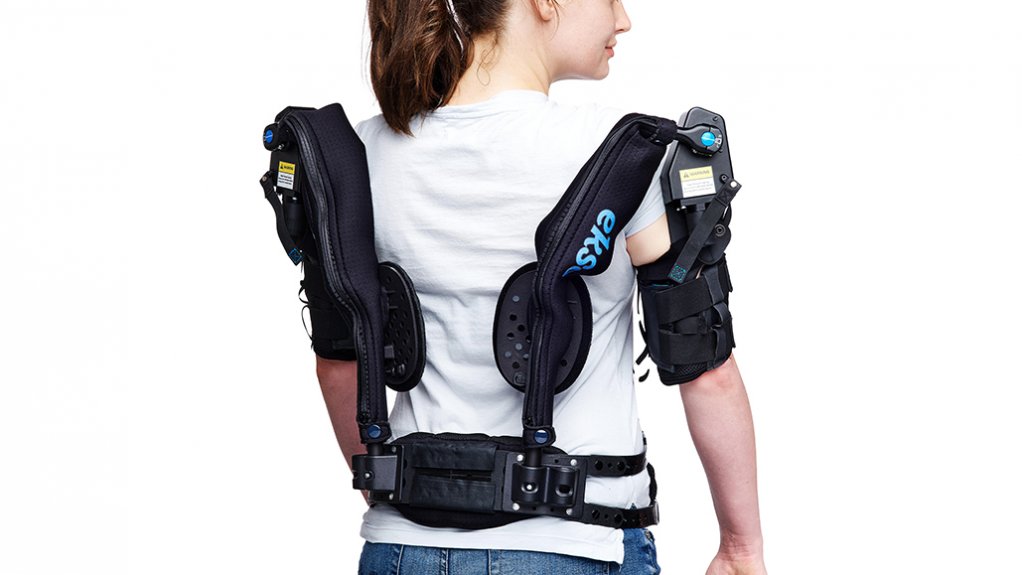

SUPERHUMAN The Sarcos Guardian XO full-body powered exoskeleton can give workers enhanced strength and stamina far beyond their normal ability
Photo by Sarcos Robotics
SUPPORT The Ekso Bionics EVO upper-body passive exoskeleton is designed to provide workers with added stamina in tasks that require the arms to be raised for a long time
Photo by Ekso Bionics
ROBUST The German Bionic Cray X powered upper body exoskeleton is designed to provide added strength to workers and to withstand the harshest conditions
Photo by German Bionic
While the world’s attention has been focused on the exponential advances being made in robotics and artificial intelligence, technological development in mechanical exoskeletons has largely been overlooked.
Exoskeletons are wearable devices designed to bolster human performance in physically demanding tasks by supporting various body parts, including the hands, lower and upper back, legs, shoulders and arms. This reduces the amount of energy required when lifting and carrying heavy objects and holding heavy tools.
Although many pundits agree that increased automation is, indeed, the future, plenty of human workers are still required.
According to market research company ABI, the emerging market for exoskeletons – particularly in labour-intensive industrial applications – is forecast to grow significantly over the next few years, with global revenues expected to reach more than $7-billion by 2030.
ABI expects that exoskeletons will drastically reduce the incidence of musculoskeletal disorders, thereby reducing the costs associated with absenteeism and workplace injuries.
While exoskeletons are already being used to help workers in a range of industrial applications globally, ranging from painting buildings to warehousing and car manufacturing, not much has been said about how they might be used in mining – one of the most dangerous and labour-intensive industries.
With South Africa’s mining industry being particularly dependent on human labour, combined with the ever-present need to reduce injuries and fatalities, and considering the generally negative perception among unions towards increased automation in the sector, local mines are under pressure to find ways of improving worker safety – especially underground – while retaining jobs.
Against this backdrop, Minerals Council South Africa is actively exploring how mechanical exoskeletons could be used in underground mining, specifically to assist workers in the physically demanding and dangerous task of barring.
Barring, which is the removal of loose rocks from the walls and ceiling of an underground mine using a long steel pole, is notoriously risky work, with many fall-of-ground (FoG) deaths being attributed to this process over the years.
Unfortunately, it is a very necessary part of underground mining, with no safer technological alternative currently available that is effective and affordable, according to Minerals Council rock engineering programme manager Duncan Adams.
Moreover, barring causes significant strain on the back, shoulders and arms of even the strongest and most physically fit mineworkers. This makes them unable to do the job effectively for more than a few minutes at a time, after which they become too tired to continue. This can negatively affect the barring and, consequently, put other workers in jeopardy.
Recognising this as an area of concern, the Mandela Mining Precinct (MMP) and the Minerals Council organised a Rock Hazard Identification and Safe Removal Innovation Challenge.
The challenge, in partnership with mining companies Sibanye-Stillwater and Impala Platinum, was aimed at finding novel solutions for rock hazard identification and safe rock removal to reduce FoG incidents and improve safety underground.
Mining technology company Reutech Mining was the winner of the first part of the challenge – rock hazard identification. However, Adams says the second part of the challenge – safe rock removal – was not a success, as no suitable technology was suggested.
As such, the search for a suitable solution for safe rock removal continues.
Remote-controlled tracked robots were investigated, but Adams tells Engineering News & Mining Weekly that the cost per unit would have been much too high to be economically viable.
However, exoskeletons, which could cost a fraction of such machines, piqued the interest of the MMP and Minerals Council team as a potential solution for enhancing the safety and effectiveness of barring underground.
Adams explains that exoskeletons could provide physical support for workers performing barring, reducing fatigue and, consequently, enabling them to carry out the task for longer and with greater consistency, thereby improving the quality of the work and increasing the level of safety for all.
Moreover, an exoskeleton could provide the necessary strength and stamina for workers to hold the bar from further back, reducing the risk of rock falls.
“Insofar as safe rock removal is concerned, there is great enthusiasm from the rock engineering technical committee of the Minerals Council to pursue research on exoskeletons,” he adds.
Further, there are many other potential uses for exoskeletons in mining aside from barring, however, such as the replacement of large and heavy haul truck tyres in opencast mining, and the lifting and holding of pneumatic drills for long periods in underground stopes.
Adams notes that there have been instances where exoskeletons were tested in South African mining – although not for barring – but they did not work as hoped. However, he believes that the technology has advanced significantly since then and is, therefore, worth reassessing.
“I see a huge use for them in the South African mining industry. There are many instances of mineworkers needing to lift and manipulate heavy equipment, and an exoskeleton is perfect for providing the strength to do it,” he says.
Types of Exoskeletons
Several types of exoskeletons are commercially available globally, each with its own unique design and intended use.
However, Adams says the Minerals Council could not find any South African exoskeleton manufacturers or suppliers.
The bulk of exoskeleton technology development is taking place in the US, Germany and Japan.
Full-body-powered exoskeletons are the most expensive, but they also provide the most support. They use electric motors to assist with movement, enabling the user to lift heavier loads than would otherwise be possible and to move more easily.
US-based exoskeleton developer Sarcos has developed the Guardian XO full-body- powered exoskeleton, which is designed to assist workers with heavy-duty tasks, empowering them to safely lift and manipulate up to 90 kg without fatigue or strain, amplifying the lifting strength 20 times over.
According to ABI, the average selling price for a full-body-powered exoskeleton is about $133 700, although it expects the cost to drop by about 7% by 2030, owing to greater economies of scale, quantum improvements in technology, improved manufacturing methodologies and increased competition as more developers enter the market.
Passive exoskeletons are significantly less costly, as they do not have any motors or electronics but instead rely on smartly engineered mechanical designs to provide support and mobility assistance. They also enable users to lift and move heavy objects more easily, although not to the same extent as powered exoskeletons.
The aim of passive exoskeletons is to provide support, rather than enhancement, providing workers with greater stamina so that they can perform their tasks for longer without experiencing crippling fatigue or injury.
Passive exoskeletons might be the most viable for use in barring, in Adams’ opinion, as they can provide workers with the necessary support and strength to perform tasks at a more reasonable price.
ABI research shows that the average selling price for a full-body passive exoskeleton is significantly less than powered exoskeletons, at about $45 078. Using passive upper-body-only exoskeletons could result in the costs being reduced further, to about $20 086.
An example of a viable passive upper-body exoskeleton for use in barring could be the EVO from US-based exoskeleton developer Ekso Bionics.
Resembling a wearable vest, the EVO supports the weight of a worker’s arms, which takes the load off the worker’s shoulders and arms when lifting something overhead.
Another option is the Cray X upper-body-powered exoskeleton from developer German Bionics, owing to its capability to withstand the harsh underground mining environment, owing to its moisture- and dust-proof design. It can provide workers with an additional 30 kg of lifting strength.
Another promising option that the Minerals Council is investigating is the Fortis tool-holding exoskeleton – manufactured by aerospace company Lockheed Martin – which sends the weight of a heavy tool directly into the ground, bypassing the user’s body and providing them with significantly enhanced stamina.
The Fortis – a passive lower-body exoskeleton – uses a gimbal, which is connected to a spring-loaded arm to allow for rotation and flexibility. This arm is connected to the exoskeleton at the waist, with a set of counterweights at the back keeping the operator steady.
With options available, and rapid developments and enhancements, Adams believes that the incorporation of exoskeletons – into not only mining but also other industries in South Africa – is increasingly likely in the near future.
“As long as we’re going to need human beings to carry out certain tasks, there remains a market for exoskeletons,” Adams concludes.
Comments
Press Office
Announcements
What's On
Subscribe to improve your user experience...
Option 1 (equivalent of R125 a month):
Receive a weekly copy of Creamer Media's Engineering News & Mining Weekly magazine
(print copy for those in South Africa and e-magazine for those outside of South Africa)
Receive daily email newsletters
Access to full search results
Access archive of magazine back copies
Access to Projects in Progress
Access to ONE Research Report of your choice in PDF format
Option 2 (equivalent of R375 a month):
All benefits from Option 1
PLUS
Access to Creamer Media's Research Channel Africa for ALL Research Reports, in PDF format, on various industrial and mining sectors
including Electricity; Water; Energy Transition; Hydrogen; Roads, Rail and Ports; Coal; Gold; Platinum; Battery Metals; etc.
Already a subscriber?
Forgotten your password?
Receive weekly copy of Creamer Media's Engineering News & Mining Weekly magazine (print copy for those in South Africa and e-magazine for those outside of South Africa)
➕
Recieve daily email newsletters
➕
Access to full search results
➕
Access archive of magazine back copies
➕
Access to Projects in Progress
➕
Access to ONE Research Report of your choice in PDF format
RESEARCH CHANNEL AFRICA
R4500 (equivalent of R375 a month)
SUBSCRIBEAll benefits from Option 1
➕
Access to Creamer Media's Research Channel Africa for ALL Research Reports on various industrial and mining sectors, in PDF format, including on:
Electricity
➕
Water
➕
Energy Transition
➕
Hydrogen
➕
Roads, Rail and Ports
➕
Coal
➕
Gold
➕
Platinum
➕
Battery Metals
➕
etc.
Receive all benefits from Option 1 or Option 2 delivered to numerous people at your company
➕
Multiple User names and Passwords for simultaneous log-ins
➕
Intranet integration access to all in your organisation