Lafarge launches ECOPact cement with as much as 100% less embodied carbon emissions
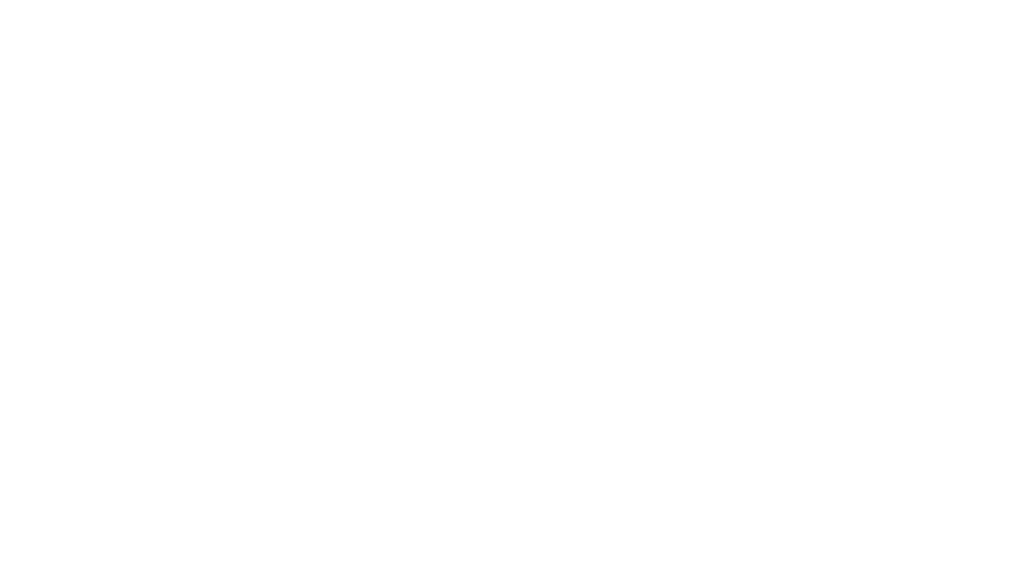
Lafarge South Africa launches lower carbon emissions cement ECOPact in efforts to reduce construction industry’s environmental impact.
Following the successful take-up in markets where building materials company Holcim is present, local subsidiary Lafarge South Africa (SA) on July 18 launched its lower-carbon cement ECOPact to the domestic market.
Compared with CEM I – Portland cement containing a maximum of 5% of other materials – ECOPact is available in products containing between 30% and 100% less carbon emissions.
Lafarge is able to lower its carbon emissions in the manufacturing process by replacing clinker with fly ash and other upcycled construction materials.
Where regulatory conditions permit, ECOPact products integrate fly ash and other upcycled construction materials, thereby making use of materials readily available from the construction and power generation industries which might have otherwise been disposed of.
In terms of using recycled materials, Lafarge uses its co-located Kempton Park-based Geocycle business to obtain relevant materials. Geocycle co-processes more than 100 000 t/y of waste from the industrial sector, municipalities, the agricultural sector and other waste management companies.
As for getting fly ash to use in ECOPact, Lafarge SA relies on its subsidiary Ash Resources to source ash materials – a by-product of coal-fired power stations.
Lafarge developed ECOPact as part of its endeavours to create a sustainable and circular construction ecosystem.
In addition, with its research and development laboratory and equipment, Lafarge is enhancing its innovation and continuous improvement towards its sustainability goals.
GREEN BUILDING
The Green Building Council South Africa (GBCSA) launched its net-zero green building rating tools in 2017, which considers the carbon, water, waste and ecology of buildings.
However, as technologies evolve and engineers and building materials producers develop new and green methods and products, the GBCSA is refining its ratings tools and methodologies to cater for an industry that is making it easier to build greener.
As such, GBCSA CEO Lisa Reynolds says rating buildings on their carbon, water, waste and ecology is the first step in the GBCSA’s journey to helping the construction industry realise its net-zero goals.
In this regard, the first steps towards net-zero carbon takes into account the base levels of carbon that go into a building and the operational energy within buildings. These form GBCSA’s Levels 1 and 2 of net-zero ratings criteria; while Level 3 takes into account the embodied energy and carbon of building materials used to construct a building.
A Level 3 score can, therefore, be improved by using a product like ECOPact.
“[The] GBCSA has commenced with the base work to include Level 3 into our net-zero carbon tool as well,” Reynolds says.
Level 4, meanwhile, involves consideration of the carbon intensity of renovating a green building in the future, while Level 5 takes deconstruction into account.
Reynolds says ECOPact has a role to play in levels 4 and 5 as well.
She notes that, in terms of closing the gap in a circular economy, it is important to prioritise the reduction, reuse and recycling of materials.
“Where we cannot reduce, and where we cannot reuse, recycling is a vital part of the circular economy. Within this space, I love the concept of upcycling as opposed to merely recycling. The initiatives within Lafarge tick both boxes of upcycling and recycling.”
Comments
Press Office
Announcements
What's On
Subscribe to improve your user experience...
Option 1 (equivalent of R125 a month):
Receive a weekly copy of Creamer Media's Engineering News & Mining Weekly magazine
(print copy for those in South Africa and e-magazine for those outside of South Africa)
Receive daily email newsletters
Access to full search results
Access archive of magazine back copies
Access to Projects in Progress
Access to ONE Research Report of your choice in PDF format
Option 2 (equivalent of R375 a month):
All benefits from Option 1
PLUS
Access to Creamer Media's Research Channel Africa for ALL Research Reports, in PDF format, on various industrial and mining sectors
including Electricity; Water; Energy Transition; Hydrogen; Roads, Rail and Ports; Coal; Gold; Platinum; Battery Metals; etc.
Already a subscriber?
Forgotten your password?
Receive weekly copy of Creamer Media's Engineering News & Mining Weekly magazine (print copy for those in South Africa and e-magazine for those outside of South Africa)
➕
Recieve daily email newsletters
➕
Access to full search results
➕
Access archive of magazine back copies
➕
Access to Projects in Progress
➕
Access to ONE Research Report of your choice in PDF format
RESEARCH CHANNEL AFRICA
R4500 (equivalent of R375 a month)
SUBSCRIBEAll benefits from Option 1
➕
Access to Creamer Media's Research Channel Africa for ALL Research Reports on various industrial and mining sectors, in PDF format, including on:
Electricity
➕
Water
➕
Energy Transition
➕
Hydrogen
➕
Roads, Rail and Ports
➕
Coal
➕
Gold
➕
Platinum
➕
Battery Metals
➕
etc.
Receive all benefits from Option 1 or Option 2 delivered to numerous people at your company
➕
Multiple User names and Passwords for simultaneous log-ins
➕
Intranet integration access to all in your organisation