Company supplies single chamber melting, casting furnace
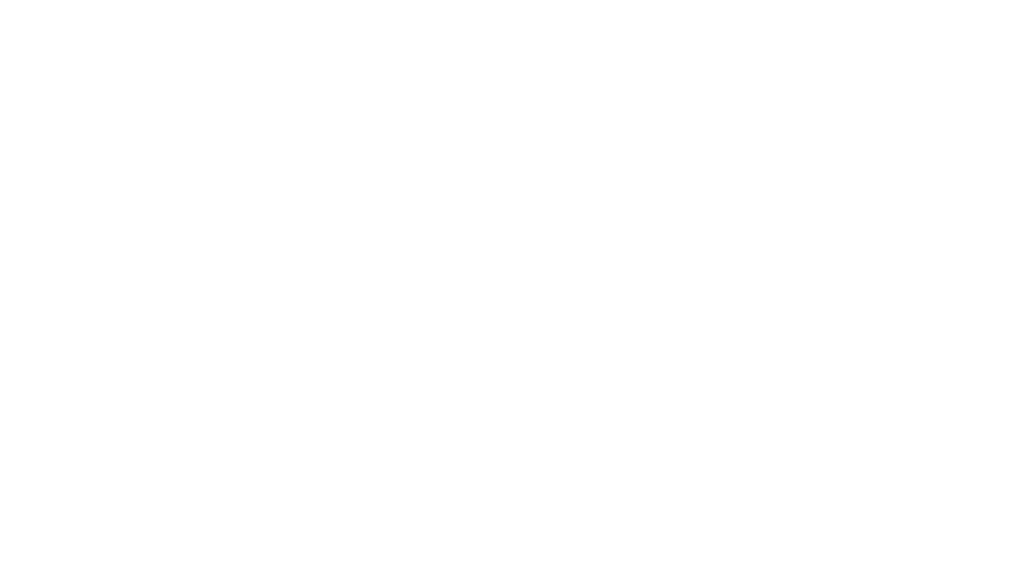
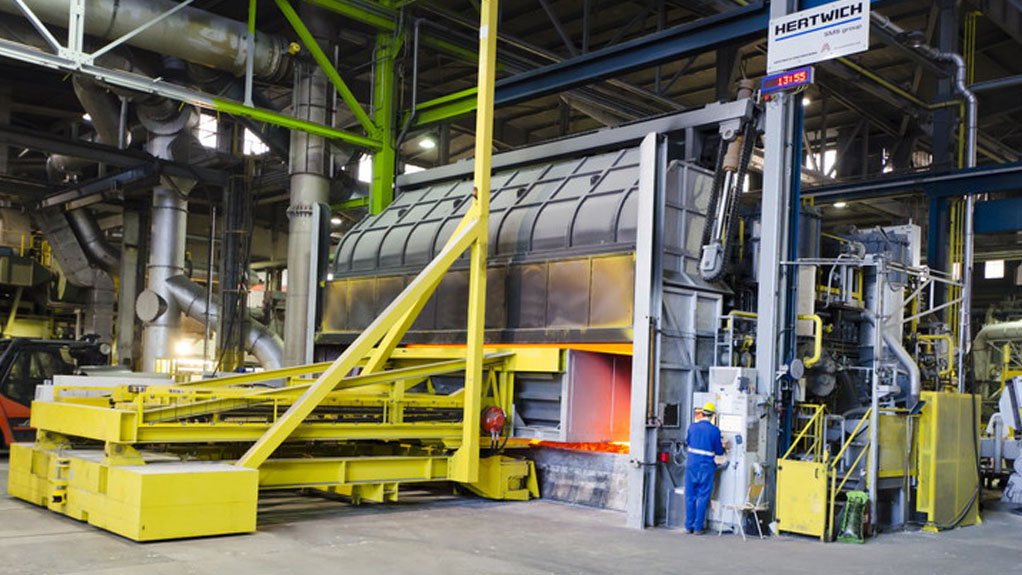
DUAL FURNACE The new aluminum melting and casting furnace will have a capacity of 55 000 t a year
Mechanical engineering company Hertwich Engineering will supply a melting and casting furnace with a capacity of 55 000 t/y of aluminium, as well as a charging machine, to Austrian aluminium product supplier AMAG. Commissioning of the new furnace is scheduled for mid-2017.
The move to increase capacity is based on the assumption in the aluminium industry that worldwide consumption of rolled aluminium products will grow by 70% over the next ten years. Owing to this expected growth in demand, AMAG started an enlargement programme in 2012 with an initial cost of €220-million.
This year, the company introduced a new rolling plant project, called AMAG 2020 strategy project, which should boost the company’s capacity more than 300 000 t/y by 2017. The new furnace is part of this enlargement programme. Its design also allows for the remelting of scrap, which is expected to increase along with rolling production.
The melting and casting furnace is a joint development by AMAG and Hertwich. The first unit of this type started operation at AMAG in 2013. With a holding capacity of 70 t, this furnace was already of impressive size. The new furnace unit exceeds the size of the existing unit, with a liquid metal volume of 110 t.
The single-chamber furnace used for melting is able to also take over the function of a casting furnace, if necessary. For heating, two pairs of regenerative burners are installed above the melting bath level. It has a specific maximum gas consumption of 500 kWh for each ton of aluminium, ensuring that the plant satisfies the strictest requirements, both in economic terms and also in terms of environmental impact.
To ensure clean combustion, an oxygen regulation system and separate regulating systems for natural gas and combustion air are provided. An electromagnetic pump ensures thorough metal circulation, constantly high melting performance and homogeneous temperature distribution in the furnace.
The scope of supply also includes a rail-guided, pusher-type charging machine enabling the furnace to be efficiently charged in just a few charging cycles.
Another facet of its rolling mill extension includes AMAG’s increasing its homogenising capacity. In the last two years, three new Hertwich batch homogenising furnaces have been commissioned.
As of last month, two more furnaces have been ordered and will be commissioned at the end of this year, or early next year.
The batch homogenising unit, designed and supplied by Hertwich, is notable for its integrated data processing and its fully automated operation. The five new homo- genising furnaces, each with a capacity of 200 t, will be combined together at one complex.
On the support table of the rolling slab, each rolling slab is identified by storing its batch and rolling slab number to the system. All other information is provided by data processing software Hertwich MES. A stacking crane transports the slabs to a weighing station where they are measured and weighed.
In accordance with the production programme specified by MES, the stacking crane fully automatically transports the slabs from the store to the central stacking machine.
For the best heat transfer, the individual layers are separated by spacers. These are taken from a magazine and positioned individually on the slab surfaces by the automatic spacer handling system.
A charging car takes up the stack, moves it in front of whichever unit has been chosen and transports the complete stack into the furnace. The individual heat treatment parameters are stored in the control system.
At the end of the holding time, the charging car transfers the homogenised material directly to the air-cooling station. Depending on the alloy range processed, some of these are made in an open, and some in a closed design. The closed cooling stations are particularly required for high-alloyed materials, for which a low cooling rate or a complex cooling regime is required.
After the cooling process, the stacks are discharged by the charging car and transferred back into store. Using the stacking crane they are destacked and either returned to the store or sent ahead for further processing.
Hertwich forms part of the SMS group of companies, which is internationally active in plant construction and mechanical engineering for the steel and nonferrous metals industry. The SMS group has over 14 000 employees and generate sales of over €3.3-billion.
Comments
Announcements
What's On
Subscribe to improve your user experience...
Option 1 (equivalent of R125 a month):
Receive a weekly copy of Creamer Media's Engineering News & Mining Weekly magazine
(print copy for those in South Africa and e-magazine for those outside of South Africa)
Receive daily email newsletters
Access to full search results
Access archive of magazine back copies
Access to Projects in Progress
Access to ONE Research Report of your choice in PDF format
Option 2 (equivalent of R375 a month):
All benefits from Option 1
PLUS
Access to Creamer Media's Research Channel Africa for ALL Research Reports, in PDF format, on various industrial and mining sectors
including Electricity; Water; Energy Transition; Hydrogen; Roads, Rail and Ports; Coal; Gold; Platinum; Battery Metals; etc.
Already a subscriber?
Forgotten your password?
Receive weekly copy of Creamer Media's Engineering News & Mining Weekly magazine (print copy for those in South Africa and e-magazine for those outside of South Africa)
➕
Recieve daily email newsletters
➕
Access to full search results
➕
Access archive of magazine back copies
➕
Access to Projects in Progress
➕
Access to ONE Research Report of your choice in PDF format
RESEARCH CHANNEL AFRICA
R4500 (equivalent of R375 a month)
SUBSCRIBEAll benefits from Option 1
➕
Access to Creamer Media's Research Channel Africa for ALL Research Reports on various industrial and mining sectors, in PDF format, including on:
Electricity
➕
Water
➕
Energy Transition
➕
Hydrogen
➕
Roads, Rail and Ports
➕
Coal
➕
Gold
➕
Platinum
➕
Battery Metals
➕
etc.
Receive all benefits from Option 1 or Option 2 delivered to numerous people at your company
➕
Multiple User names and Passwords for simultaneous log-ins
➕
Intranet integration access to all in your organisation