Miner expands renewables uptake
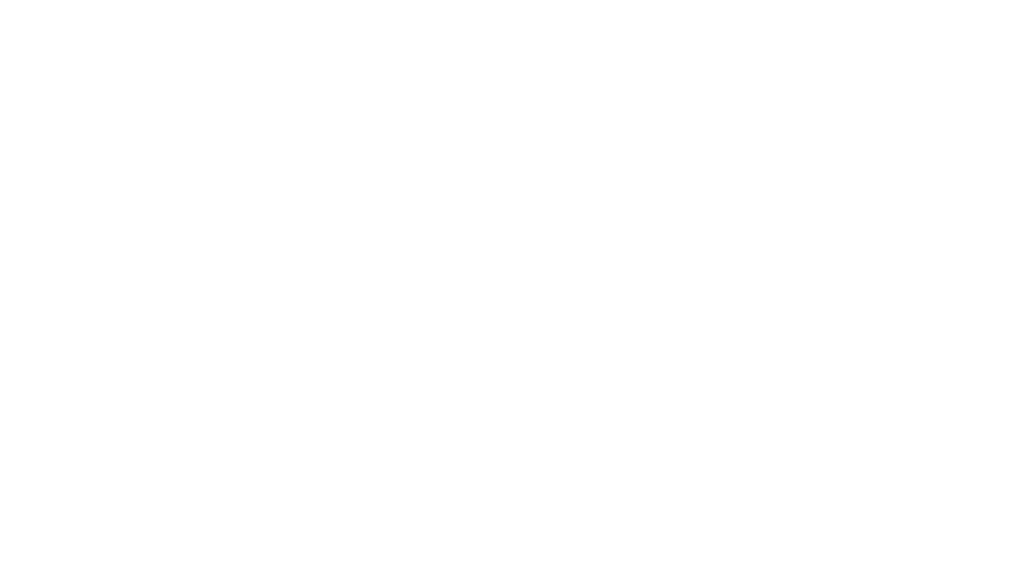
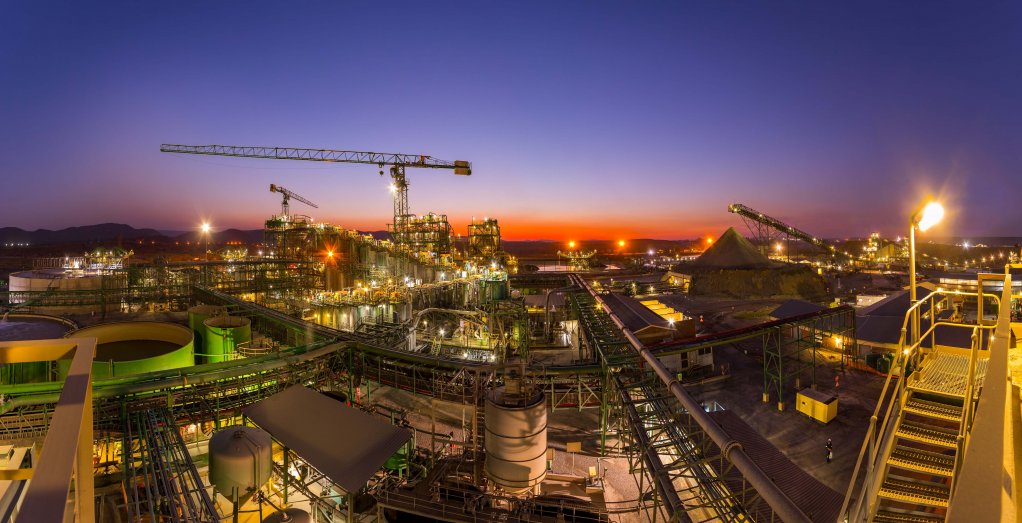
LIGHTING THE WAY The new power purchase agreement signed between Tharisa Minerals and Etana Energy will provide substantial renewable energy to the Tharisa mine
Platinum group metals (PGMs) and chrome co- producer Tharisa Minerals has entered into a long-term power purchase agreement (PPA) for the procurement of wheeled renewable energy for its Tharisa mine, situated on South Africa’s western limb of the Bushveld Complex, in the Northern Cape.
The 15-year agreement signed with National Energy Regulator of South Africa-licensed electricity trader Etana Energy will see the latter providing up to 44% of Tharisa mine’s electricity demand.
This wheeled energy will complement Tharisa mine’s 40 MW solar power plant being developed by integrated energy company TotalEnergies Renewables and transitional energy group Chariot Transitional Power.
Once commissioned, Tharisa’s in-house solar plant will provide 30% of the Tharisa mine’s energy needs.
“The Etana energy will be provided using wheeled energy from wind and solar farms in the Western Cape and Northern Cape, capitalising on the existing electricity transmission grid,” says Tharisa Minerals investor relations and communications head Ilja Graulich.
He adds that the wheeled energy system is scheduled to come on stream in 2026.
The energy trading deal enables the Tharisa mine to better manage its power costs and benefit from associated renewable-energy certificates.
Importantly, the Etana PPA and the solar project will ensure that Tharisa Minerals’ drive to reduce its carbon footprint by 30% by 2030 is well within reach, while simultaneously guaranteeing pre-determined power costs for a portion of the mine’s power expenses.
“Up to 76% of Tharisa Minerals’ energy needs will be provided by renewable energy from 2026 onwards under these agreements,” enthuses Graulich.
Branching Out
Tharisa Minerals has also invested significantly in its new research arm Redox One, which is dedicated to pioneering a sustainable energy future by delivering safe, reliable, cost-effective and large-scale energy storage solutions to industries and communities.
“Redox One is a wholly-owned subsidiary of Tharisa, and both Tharisa and Redox One are headquartered in Cyprus, with laboratory facilities in Germany,” he adds.
“Through our unwavering commitment to technological innovation and excellence, environmental stewardship and customer collaboration, we strive to revolutionise the global energy landscape,” says Graulich.
In addition to Redox One, Tharisa’s beneficiation, and research and development (R&D) arm Arxo Metals conducts extensive research into technologies and downstream beneficiation opportunities that can potentially improve yields and recoveries at the Tharisa mine.
“Its core focus is to create increased-value PGM and chrome products through expanding and optimising the group’s processing operations,” he says, adding that Arxo Metals has already made significant strides in furthering its objectives of finding opportunities in the energy space.
“As such, the Arxo Metals Renewable Energy Centre was established as an independent unit of Arxo Metals, focusing on energy storage solutions using our commodities, including long- duration scalable storage solutions,” points out Graulich.
Local Operations
Tharisa Minerals’ two separate processing plants are designed to treat the PGM and chromitite layers of the Bushveld Complex.
“Our smaller-volume Genesis plant was commissioned in August 2011, with the PGM circuit starting up in December 2011, with our larger-volume Voyager plant being commissioned in December 2012,” says Graulich.
Following a number of recent upgrades, both plants currently operate above designed nameplate capacity.
“The plants have a similar process flow that includes crushing and grinding, primary removal of chrome concentrate by spirals, followed by PGM flotation from the chrome tails and a second spiral recovery of chrome from PGM tails,” he says.
Operating in parallel, the separate plants provide processing flexibility and production stability by enabling one plant to be shut down without affecting the production of the other.
The modular design of the processing circuits will enable sections of the plant to be stopped without affecting the rest of the operation, such as the crushing circuit which can be stopped independently of the milling, spiral and flotation circuits.
Using off-the-shelf technology, the Genesis and Voyager processing plants are uniquely engineered to produce both PGM and chrome concentrates.
“This innovative approach to production has made Tharisa a world-class PGM and chrome concentrate co-producer,” enthuses Graulich.
Further, a third high-volume plant – the Vulcan Plant, was commissioned in Tharisa’s 2021 financial year.
He points out that the plant, which processes live tailings produced by the Voyager and Genesis plants, ensures further beneficiation of the company’s chrome production at the Tharisa mine while reducing carbon emissions.
“The Vulcan Plant is the first large-scale plant to produce chrome concentrates from ultrafines, consolidating Tharisa’s position as a key chrome producer,” he explains.
The concept of Vulcan was developed entirely inhouse by the R&D team to extract ultrafine chrome from tailings.
Specialty chrome recovery circuits are integrated into the feed circuit of the Genesis plant, known as the Challenger plant.
“The Challenger plant, owned by Arxo Metals, was commissioned in July 2013 and produces chemical- and foundry-grade chrome concentrates, significantly adding to the revenue diversification strategy of Tharisa,” concludes Graulich.
Comments
Press Office
Announcements
What's On
Subscribe to improve your user experience...
Option 1 (equivalent of R125 a month):
Receive a weekly copy of Creamer Media's Engineering News & Mining Weekly magazine
(print copy for those in South Africa and e-magazine for those outside of South Africa)
Receive daily email newsletters
Access to full search results
Access archive of magazine back copies
Access to Projects in Progress
Access to ONE Research Report of your choice in PDF format
Option 2 (equivalent of R375 a month):
All benefits from Option 1
PLUS
Access to Creamer Media's Research Channel Africa for ALL Research Reports, in PDF format, on various industrial and mining sectors
including Electricity; Water; Energy Transition; Hydrogen; Roads, Rail and Ports; Coal; Gold; Platinum; Battery Metals; etc.
Already a subscriber?
Forgotten your password?
Receive weekly copy of Creamer Media's Engineering News & Mining Weekly magazine (print copy for those in South Africa and e-magazine for those outside of South Africa)
➕
Recieve daily email newsletters
➕
Access to full search results
➕
Access archive of magazine back copies
➕
Access to Projects in Progress
➕
Access to ONE Research Report of your choice in PDF format
RESEARCH CHANNEL AFRICA
R4500 (equivalent of R375 a month)
SUBSCRIBEAll benefits from Option 1
➕
Access to Creamer Media's Research Channel Africa for ALL Research Reports on various industrial and mining sectors, in PDF format, including on:
Electricity
➕
Water
➕
Energy Transition
➕
Hydrogen
➕
Roads, Rail and Ports
➕
Coal
➕
Gold
➕
Platinum
➕
Battery Metals
➕
etc.
Receive all benefits from Option 1 or Option 2 delivered to numerous people at your company
➕
Multiple User names and Passwords for simultaneous log-ins
➕
Intranet integration access to all in your organisation