Mobile calibration averts excessive downtime
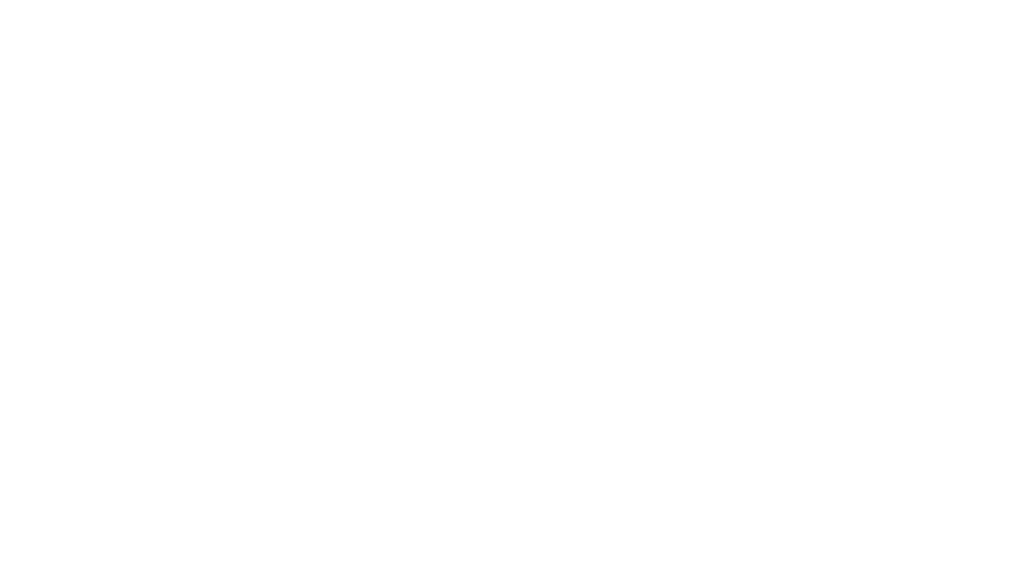
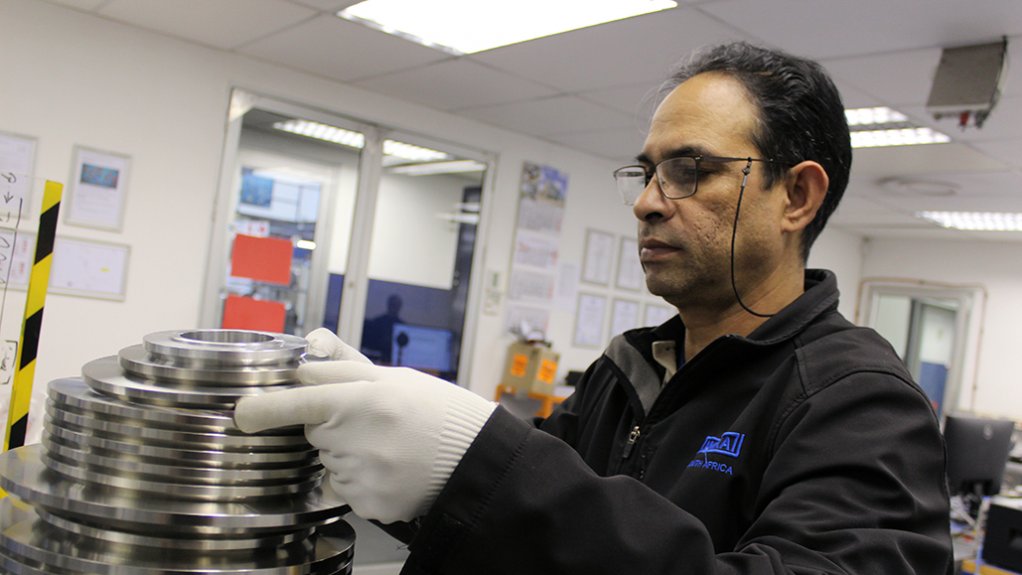
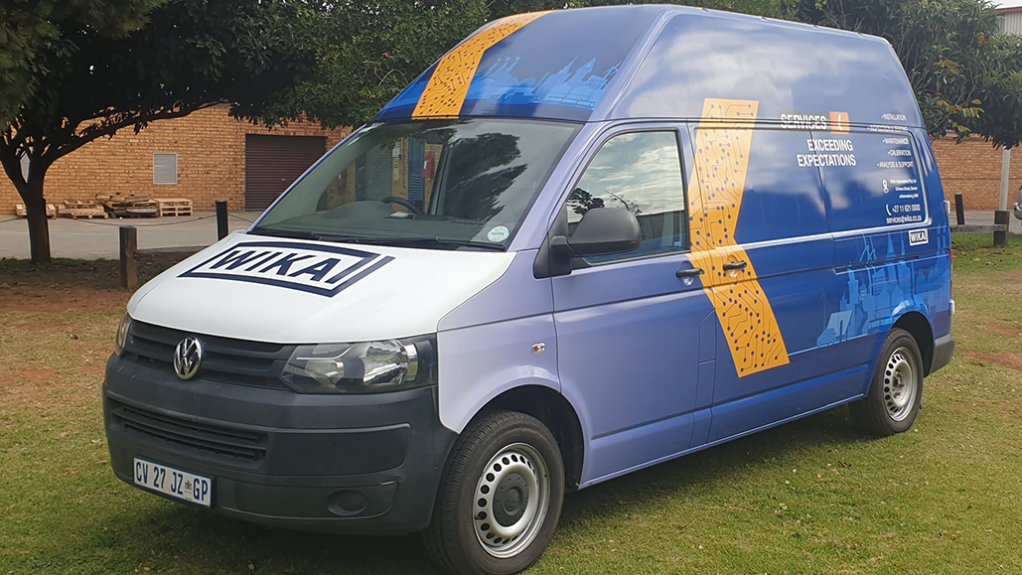
UNDER PRESSURE Interlaboratory comparisons can be time consuming
ON THE MOVE WIKA’s mobile calibration vehicles simplify installed instruments recalibration
Pressure, temperature, level, flow and force measuring technology company
WIKA’s mobile calibration vehicles simplify the recalibration of installed instruments; its mobile calibration team comprises trained personnel who provide a faster turnaround for recalibration on site.
WIKA South Africa maintains three calibration vehicles in Johannesburg, Cape Town and Gqeberha, while WIKA Namibia maintains one calibration vehicle, explains WIKA marketing manager Greg Rusznyak.
He adds that a mobile calibration vehicle assisted WIKA Namibia in meeting the client requirements and overcoming challenges, owing to the large distances between customers.
Traditionally, gauges would have to be removed, packaged and sent to a laboratory for recalibration, resulting in the plant’s remaining idle or the plant incurring high costs, owing to replacement instrumentation.
The mobile calibration team can reduce downtime and, therefore, the impact of interruptions using a mobile calibration vehicle to dismount and calibrate gauges, and return the instruments to the manufacturing process in a fairly short time. If more than ten instruments need to be calibrated, on-site calibration becomes significantly cost effective.
An additional benefit of calibrating on site is having the metrologist available for technical advice and best-practice approaches.
The mobile team also offers small repair services on calibration instruments at customers’ premises upon request.
Under Pressure
An ongoing challenge for WIKA South Africa is finding suitable laboratories where interlaboratory comparisons can be made, says Rusznyak.
Owing to WIKA South Africa’s high scope of accreditation for its pressure laboratory, it is difficult to find laboratories in South Africa that can offer interlaboratory comparisons and cover the pressure range that WIKA requires.
“For example, WIKA South Africa’s pressure calibration range extends to a little over 4 000 bar. There are only two ISO 17 025-accredited labs in South Africa that cover this pressure range, and the standard requires at least three for interlaboratory comparisons,” explains Rusznyak.
As a result, when interlaboratory comparisons are required for that pressure range, WIKA South Africa has to send the test article to a suitable lab overseas.
Further, such testing can be considerably time-consuming, which puts additional pressure on WIKA and the laboratories with which the company liaises.
For instance, laboratories need to work with a dead-weight tester to certify a 4 000 bar pressure transmitter, such as WIKA’s CPB5000HP, which is capable of generating just over 4 000 bar using weight discs.
These discs are added incrementally to simulate the ten required pressure steps. Readings are then taken on rising and falling pressure, with the entire process repeated three times. As a result, collecting readings for the calibration of one transmitter takes more than five hours, while the subsequent certificate preparation can take one to two hours to finalise.
SANAS
WIKA South Africa operates two calibration laboratories that are South African National Accreditation System- (SANAS-) accredited, in line with ISO 17 025 standards. One laboratory focuses on pressure calibration and the other on temperature calibration.
The company’s laboratories are audited by SANAS to ensure conformity to the international standard. During this audit, measurement capability is verified to national and international standards, and the document management system is reviewed.
Rusznyak notes that the regular audits address any changes in the standards.
When documentation or process changes occur, the changes are planned and incorporated into the local procedures and work instructions, he concludes.
Comments
Press Office
Announcements
What's On
Subscribe to improve your user experience...
Option 1 (equivalent of R125 a month):
Receive a weekly copy of Creamer Media's Engineering News & Mining Weekly magazine
(print copy for those in South Africa and e-magazine for those outside of South Africa)
Receive daily email newsletters
Access to full search results
Access archive of magazine back copies
Access to Projects in Progress
Access to ONE Research Report of your choice in PDF format
Option 2 (equivalent of R375 a month):
All benefits from Option 1
PLUS
Access to Creamer Media's Research Channel Africa for ALL Research Reports, in PDF format, on various industrial and mining sectors
including Electricity; Water; Energy Transition; Hydrogen; Roads, Rail and Ports; Coal; Gold; Platinum; Battery Metals; etc.
Already a subscriber?
Forgotten your password?
Receive weekly copy of Creamer Media's Engineering News & Mining Weekly magazine (print copy for those in South Africa and e-magazine for those outside of South Africa)
➕
Recieve daily email newsletters
➕
Access to full search results
➕
Access archive of magazine back copies
➕
Access to Projects in Progress
➕
Access to ONE Research Report of your choice in PDF format
RESEARCH CHANNEL AFRICA
R4500 (equivalent of R375 a month)
SUBSCRIBEAll benefits from Option 1
➕
Access to Creamer Media's Research Channel Africa for ALL Research Reports on various industrial and mining sectors, in PDF format, including on:
Electricity
➕
Water
➕
Energy Transition
➕
Hydrogen
➕
Roads, Rail and Ports
➕
Coal
➕
Gold
➕
Platinum
➕
Battery Metals
➕
etc.
Receive all benefits from Option 1 or Option 2 delivered to numerous people at your company
➕
Multiple User names and Passwords for simultaneous log-ins
➕
Intranet integration access to all in your organisation