Modern materials handling systems support operational improvements
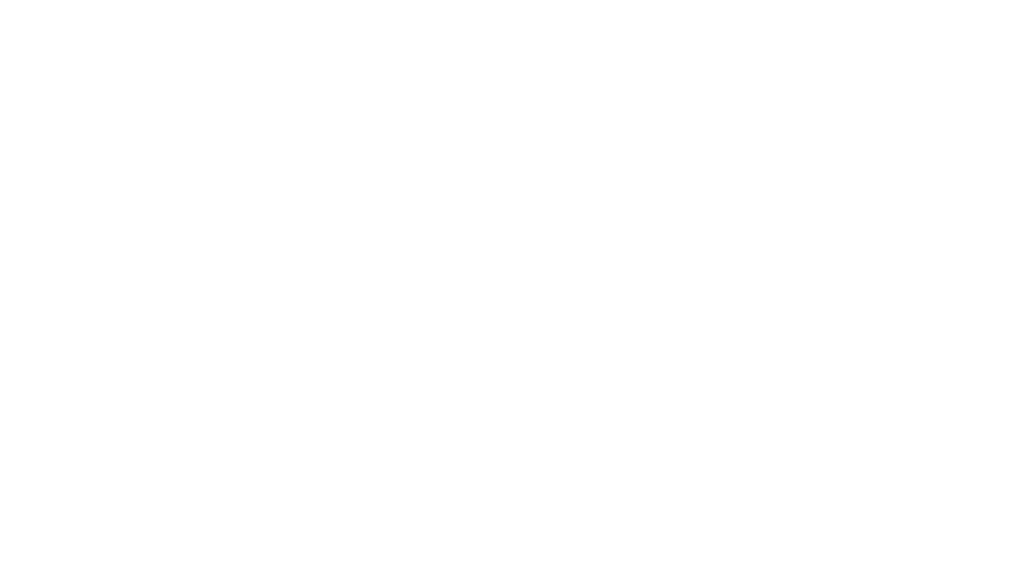
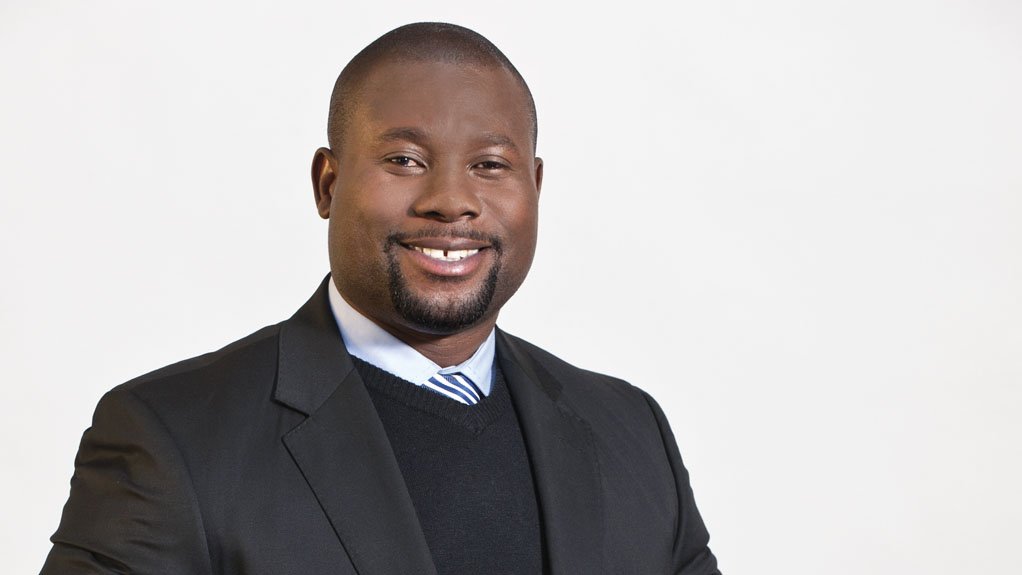
NORMAN MALEKA Technologies like SEW-EURODRIVE’s MOVITRANS are paving the way to the fully integrated and automated future of materials handling
With the Internet of Things driving large-scale automation and data exchange in manufacturing technologies, drive engineering company SEWEurodrive South Africa national sales manager Norman Maleka says that materials handling systems will become increasingly integral to improving manufacturing efficiencies, reducing costs and tracking products.
He notes that, globally, discussions on the future of materials handling are focused on increasing automation and variety, improving system performance and integration, and optimising efficiency and flexibility, while reducing costs.
“The main objectives are to improve material flow control, promote safe and hazard-free work conditions and increase productivity through the improved management of time and equipment.”
As such, robotics and automation are garnering much attention, with systems being developed that will facilitate the movement of materials through production and loading lines without any human intervention. Sensors are also increasing the communication potential of materials handling systems, with tracking, maintenance and decision- making increasingly digitised when it comes to product orders and shipments.
“This technology will ensure that products are tracked in real time, in transit and at the various facilities the products pass through, from the instant an order is placed, during production and to the point of delivery.”
He notes that technologies – such as SEWEurodrive’s Movitrans, a contactless energy transfer system – are paving the way to the fully integrated and automated future of materials handling. The system functions according to the principle of inductive energy transfer, with electrical energy transferred without contact from a fixed conductor to one or more mobile consumers.
The electromagnetic connection is made by means of an air gap and is, thus, not subject to wear – eliminating the cost and time of maintenance. The power supply is also emission-free and resistant to contamination from external sources.
“Movitrans is an ideal power supply system for all mobile applications, especially where equipment needs to cover long distances at high speeds, or if maintenance-free operation is required. It is also suited to applications in sensitive environments where outside contaminants are not permitted, and in wet and damp environments,” says Maleka.
He adds that fixed conveyors are limited in terms of their flexibility, but Movitrans allows for materials and products to be moved quickly, safely and reliably in a facility. The system can be programmed to move material in any format using the cable loop buried underneath the surface, which further allows for the layout to be manipulated.
Common applications of the system include conveyor trolleys, transport systems in logistics centres, linear-motion platforms with elevating tables or battery-charging supply units and overhead trolley systems, as well as storage and retrieval systems. The system can also be applied to floor conveyors, such as automated guided vehicles, to transport materials in a self-guided mode using sensor-based technology.
Maleka notes that, through the reliability of the system, Movitrans has been operating for two years at a wax plant in the Free State without any problems or need for replacement parts, thus boosting the plant’s productivity and reducing operating costs.
Movitrans replaced the drag chains that used to power two transverse trolleys, each servicing conveyor lines from one of the packing robots. Maleka explains that the transverse pallet trolleys each had two motors: one to drive the conveyor rollers and another to move the trolley along the rails. These were used to power the drag chain, which carried the power and communication cables.
“Wax would often clog the chain links, impeding free movement, and operators would have to step into the cell to align the trolleys properly. “During this process, there was a high risk of standing on the chain, causing it to break – and resulting in costly production stoppages for repair or replacement.”
Comments
Press Office
Announcements
What's On
Subscribe to improve your user experience...
Option 1 (equivalent of R125 a month):
Receive a weekly copy of Creamer Media's Engineering News & Mining Weekly magazine
(print copy for those in South Africa and e-magazine for those outside of South Africa)
Receive daily email newsletters
Access to full search results
Access archive of magazine back copies
Access to Projects in Progress
Access to ONE Research Report of your choice in PDF format
Option 2 (equivalent of R375 a month):
All benefits from Option 1
PLUS
Access to Creamer Media's Research Channel Africa for ALL Research Reports, in PDF format, on various industrial and mining sectors
including Electricity; Water; Energy Transition; Hydrogen; Roads, Rail and Ports; Coal; Gold; Platinum; Battery Metals; etc.
Already a subscriber?
Forgotten your password?
Receive weekly copy of Creamer Media's Engineering News & Mining Weekly magazine (print copy for those in South Africa and e-magazine for those outside of South Africa)
➕
Recieve daily email newsletters
➕
Access to full search results
➕
Access archive of magazine back copies
➕
Access to Projects in Progress
➕
Access to ONE Research Report of your choice in PDF format
RESEARCH CHANNEL AFRICA
R4500 (equivalent of R375 a month)
SUBSCRIBEAll benefits from Option 1
➕
Access to Creamer Media's Research Channel Africa for ALL Research Reports on various industrial and mining sectors, in PDF format, including on:
Electricity
➕
Water
➕
Energy Transition
➕
Hydrogen
➕
Roads, Rail and Ports
➕
Coal
➕
Gold
➕
Platinum
➕
Battery Metals
➕
etc.
Receive all benefits from Option 1 or Option 2 delivered to numerous people at your company
➕
Multiple User names and Passwords for simultaneous log-ins
➕
Intranet integration access to all in your organisation