Modern remining equipment used at MTR
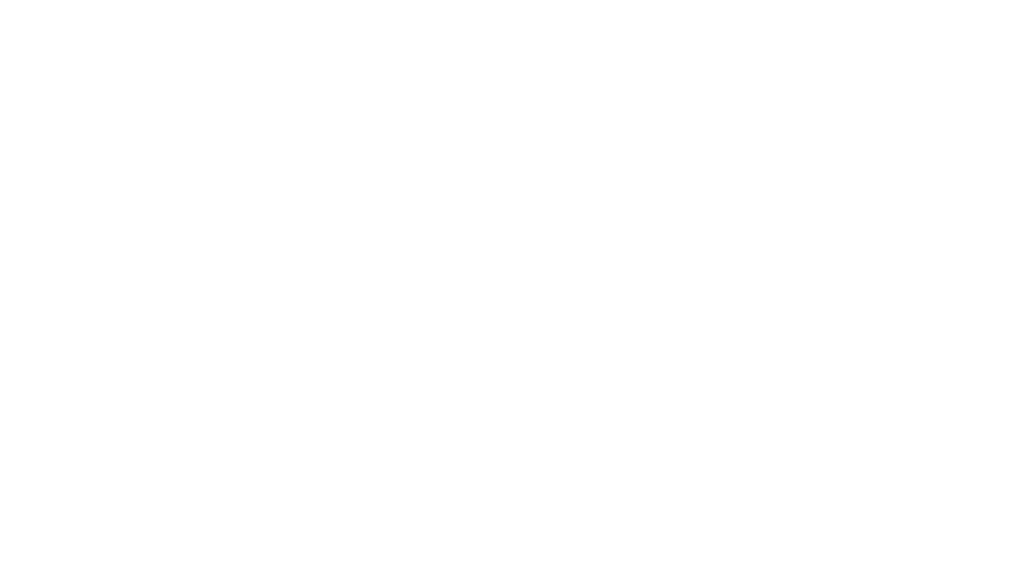
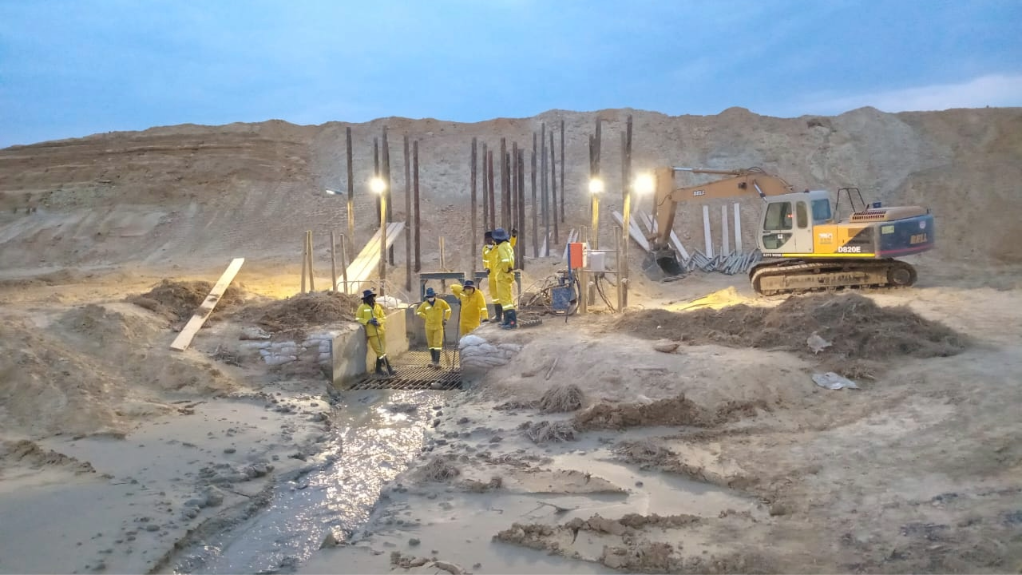
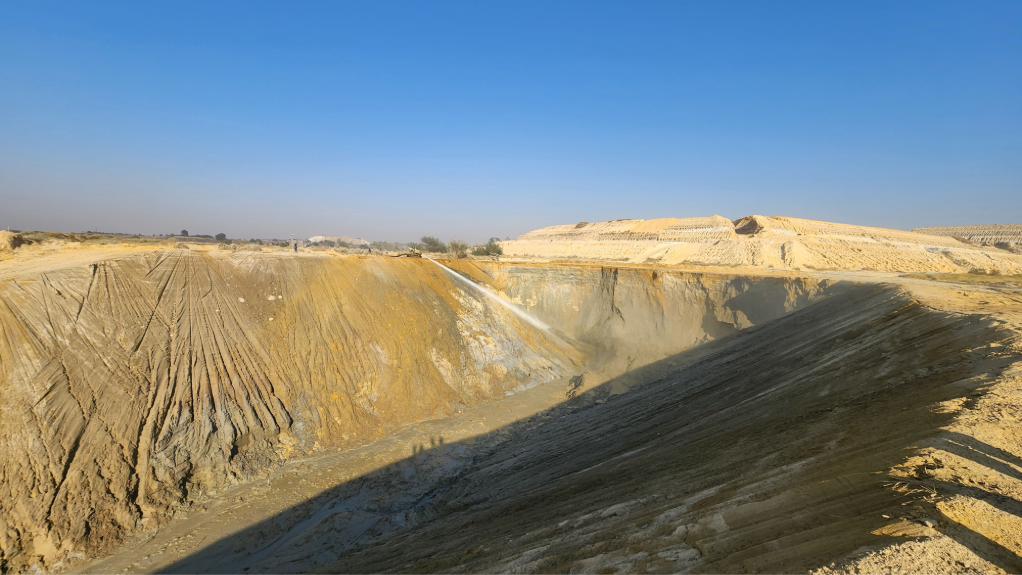
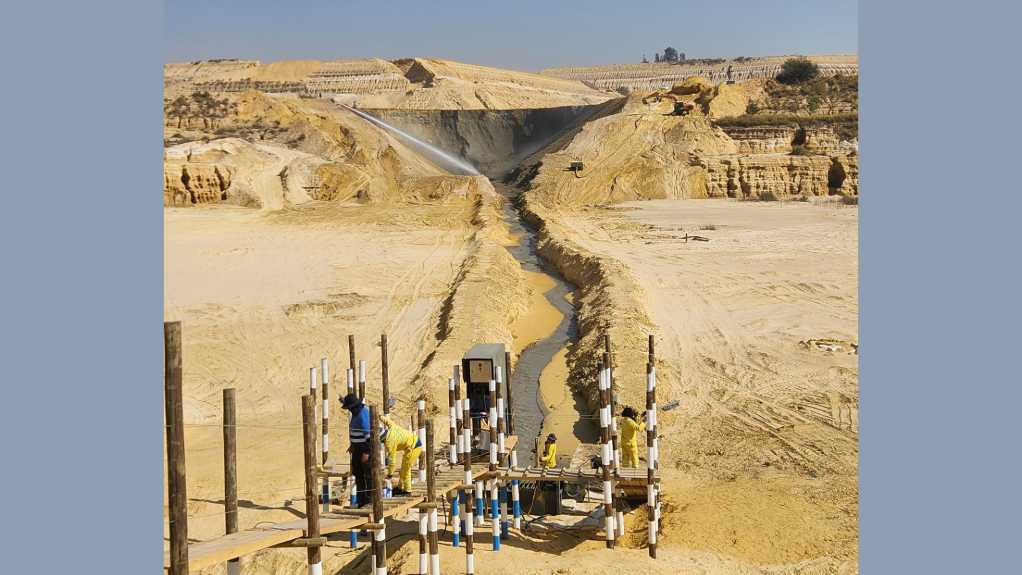
EQUIPMENT PROVISION Paragon provided the in-dam hydraulic tailings remining infrastructure
BALANCED APPROACH The hydraulic remining part of the MTR operation serves as a practical example of how tailings retreatment can balance environmental rehabilitation with resource recovery and economic development
METICULOUS PLANNING The transition from plant construction to production required meticulous planning and preparation
Tailings solutions provider Paragon Tailings’ involvement in gold producer Pan African Resources’ (PAR’s) Mogale Tailings Retreatment (MTR) operation has reinforced the growing importance of hydraulic remining in addressing South Africa’s ongoing environmental challenges in light of its prolific gold mining legacy, says Paragon operations director Donovan Spangenberg.
Paragon provided the in-dam hydraulic tailings remining infrastructure inclusive of five specialised remote-controlled tracked hydro-mining cannons, in-dam screens and decant piping needed to process the tailings material present on legacy tailings storage facilities (TSFs), which PAR has the authority to remine.
Technological advancements play a significant role in improving operational efficiency at MTR. Specifically, remote-controlled tracked hydro-mining cannons were introduced, reducing the frequency of adjustments compared to older manual models.
Drones are also deployed to survey the site, enabling accurate planning and rapid identification of issues.
“These innovations reduced downtime and helped us stay aligned with the mining plan,” says Spangenberg, adding that the use of standby equipment added flexibility, ensuring production could continue uninterrupted during equipment maintenance.
Developed in partnership with PAR, he says the hydraulic remining part of the MTR operation serves as a practical example of how tailings retreatment can balance environmental rehabilitation with resource recovery and economic development.
According to Spangenberg, the alignment of goals and clear communication between the two entities were essential for the success of the overall project commissioning.
“A detailed mining plan, developed collaboratively, ensured all aspects – from grade-tonnage profiles to practical mining techniques – were addressed,” he says, noting that this cohesive approach enabled the project to meet its deadlines while adhering to stringent operational and safety requirements.
Paragon Tailings projects entity manager Hannes Meyer, who oversaw project management and engineering, procurement and construction management, elaborates that Paragon’s focus was on applying lessons learned from PAR’s similar previous successful projects, which were also completed safely, on schedule and under budget.
While the core vision remained intact, challenges with undertaking work for the MTR project, such as supply chain disruptions and design modifications, required the team to adapt quickly, he adds.
“The dynamic nature of the project forced us to be flexible, and we worked closely with the PAR project team to make informed decisions,” states Meyer.
Spangenberg highlights that the transition from plant construction to production required meticulous planning and preparation, explaining that the team started with early works, such as building access roads, removal of vegetation and installing hydraulic mining equipment within the TSF to be mined, in the first phase.
Safety remained a top priority, particularly given the high-risk nature of remining operations using high-pressure water cannons.
“Training was central to minimising risks during this phase. We also focused on steady-state operations – balancing water pressures, flow volumes and material transfer to the processing plant,” says Spangenberg.
He adds that effective communication among the in-dam operations, transfer pump station and processing plant teams ensured the operation remained safe and efficient.
Further, Meyer notes that several challenges were encountered during the construction phase, including security risks posed by illegal miners and the logistical difficulties of managing multiple contractors in a restricted area.
“Security was a significant concern, but coordination between the MTR security team and the local South African Police Service ensured that the area was monitored effectively,” he says.
Resource allocation was also carefully planned to address accessibility issues for different contractors working simultaneously in close proximity.
In this regard, daily meetings were held with contractors to monitor progress and address potential delays, complemented by weekly schedule reviews. This level of coordination helped keep the project on track and under budget, notes Meyer.
According to Spangenberg and Meyer, the MTR project offers valuable insights for similar initiatives.
They note that key lessons include the importance of prioritising safety, maintaining clear communication across all levels, and fostering close supplier relationships to ensure timely delivery of resources.
Looking ahead, Paragon Tailings is aiming to become PAR’s preferred supplier for hydraulic remining.
Comments
Press Office
Announcements
What's On
Subscribe to improve your user experience...
Option 1 (equivalent of R125 a month):
Receive a weekly copy of Creamer Media's Engineering News & Mining Weekly magazine
(print copy for those in South Africa and e-magazine for those outside of South Africa)
Receive daily email newsletters
Access to full search results
Access archive of magazine back copies
Access to Projects in Progress
Access to ONE Research Report of your choice in PDF format
Option 2 (equivalent of R375 a month):
All benefits from Option 1
PLUS
Access to Creamer Media's Research Channel Africa for ALL Research Reports, in PDF format, on various industrial and mining sectors
including Electricity; Water; Energy Transition; Hydrogen; Roads, Rail and Ports; Coal; Gold; Platinum; Battery Metals; etc.
Already a subscriber?
Forgotten your password?
Receive weekly copy of Creamer Media's Engineering News & Mining Weekly magazine (print copy for those in South Africa and e-magazine for those outside of South Africa)
➕
Recieve daily email newsletters
➕
Access to full search results
➕
Access archive of magazine back copies
➕
Access to Projects in Progress
➕
Access to ONE Research Report of your choice in PDF format
RESEARCH CHANNEL AFRICA
R4500 (equivalent of R375 a month)
SUBSCRIBEAll benefits from Option 1
➕
Access to Creamer Media's Research Channel Africa for ALL Research Reports on various industrial and mining sectors, in PDF format, including on:
Electricity
➕
Water
➕
Energy Transition
➕
Hydrogen
➕
Roads, Rail and Ports
➕
Coal
➕
Gold
➕
Platinum
➕
Battery Metals
➕
etc.
Receive all benefits from Option 1 or Option 2 delivered to numerous people at your company
➕
Multiple User names and Passwords for simultaneous log-ins
➕
Intranet integration access to all in your organisation