New pump bearing decreases maintenance at treatment plants
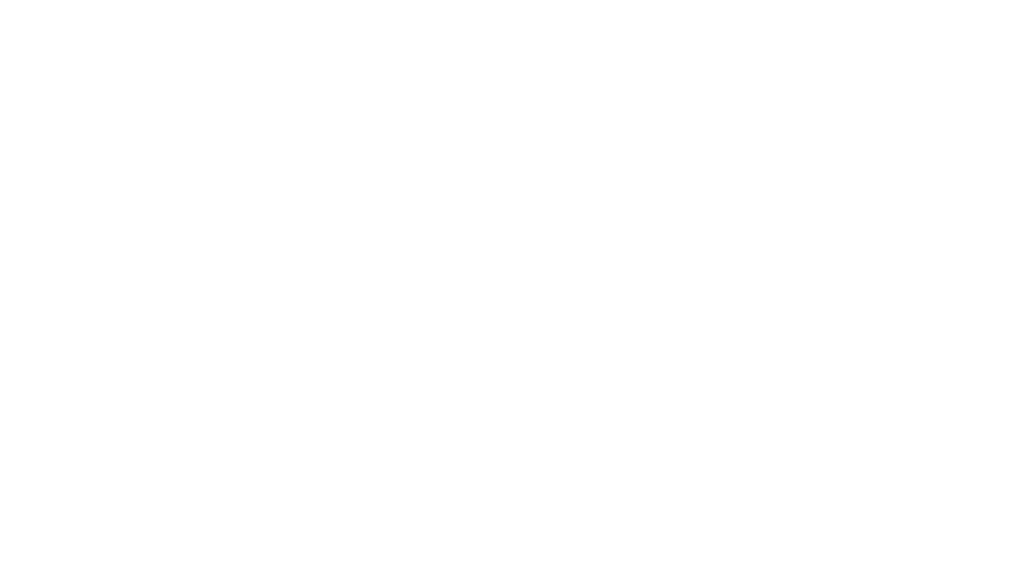
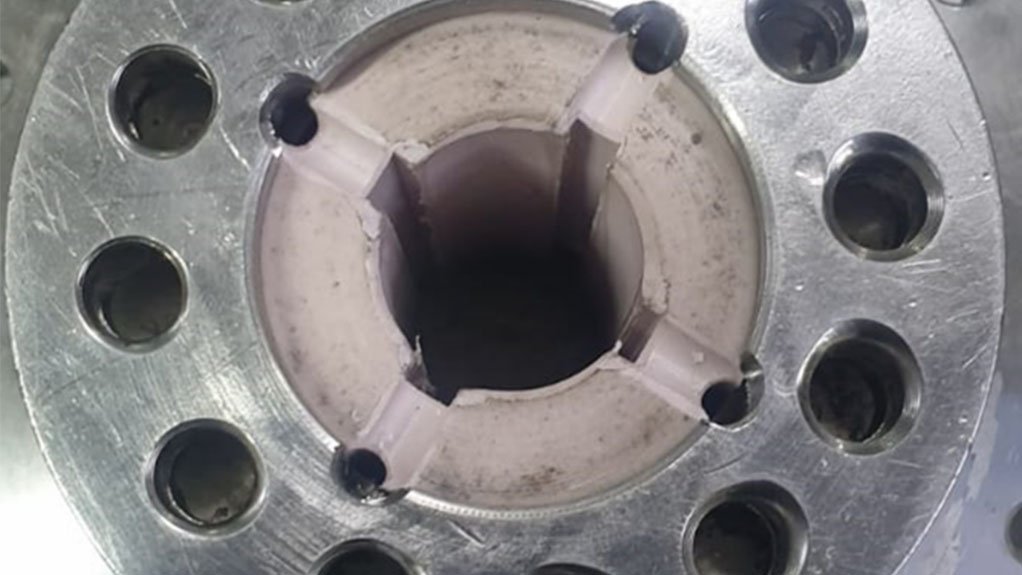
BEARING THE BRUNT The bearings being used in aeration pumps at a number of wastewater plants kept failing until Vesconite Bearings developed an alternative, more robust bearing
A local wastewater plant operator recently approached polymer bushings and bearings manufacturer Vesconite Bearings in search of a solution to a reoccurring bearing failure on its aeration pumps at a number of the plants it maintains in South Africa.
The plant operator was being called in every couple of weeks to remove, disassemble and clean wastewater pumps, to prevent any failures at the plant.
The pump design that was in place was a standard vertical shaft pump design with an output of between 5 kW and 10 kW; however, the bearing design was complex and prone to failure.
Aeration pumps float on wastewater treatment dams and ensure that chemical decomposition of the dirty water occurs before the wastewater gets treated further.
“Vesconite Bearings and the pump original-equipment manufacturer (OEM) went through several design iterations before an appropriate and effective design was finalised,” says Vesconite Bearings engineer Petrus Fourie.
He explains that the main shaft bearing design consisted of a ball bearing with carbon mechanical seals on either side of it and the ball bearing was lubricated by oil that was pressure fed into the system, so the pressure of the oil was higher than the pressure of the water on either side of the carbon seals.
The first design involved the replacement of the ball bearing, two carbon seals and the lubrication system with a no-swell wear- resistant Vesconite Hilube bushing in the existing housing.
The design was a combined thrust bearing and radial guide bearing — a combined main shaft bearing and thrust bearing, so it has both axial and radial running faces.
“We proposed a flange bearing design, where basically a step on the shaft would sit on the flange,” states Fourie.
He adds that the vertical shaft sat on top of the flange to absorb the vertical forces, the axial forces, and then the bushing absorbed the lateral forces, or radial forces.
“In a pump that uses plain bearings from the start, you have a separate thrust washer or wear ring and a main shaft bearing,” Fourie notes.
“But here we hybridised the two parts,” he says, noting that, as the ball bearings absorbed the axial force, Vesconite Bearings designed a plain bushing as well, to take on the axial force.
However, the first design proved inadequate in testing on a test bench with dirty water in the OEM company’s workshop.
None of the water that flowed through the pump got to the flange face and this resulted in that particular face overheating and melting.
Fourie then suggested that the pumps company cut some grooves on the flange face to allow the water to flush through.
Further suggestions included adding a stainless steel collar to the shaft, which would increase the area on to which the axial force applied, which would consequently increase the area, therefore decreasing the pressure and decreasing the overall load on the bearing so it was less likely that it would overheat.
This second design worked better, but a couple of the grooves got blocked up on the axial face because of the dirty water and, again, that resulted in the bearing overheating.
Fourie further altered the design and suggested that the pump OEM switch its bearing material to Vesconite Bearings’ highest-grade bearing material, Vesconite Superlube, which is known for its ultra-low friction and extreme wear resistance.
His design also included additional grooves, increased groove sizes and holes through the stainless steel flange that rests on the axial face of the bearing, to allow more water to flow through the bearing.
The third design iteration has proven to be the most effective and the wastewater company is happy with its pump’s performance.
Other advantages include that the company has reduced oil lubrication, which, prior to the introduction of Vesconite Superlube, took place every four to six weeks depending on the water quality.
The timeframe between oil lubrication is now between four to six months with Vesconite Superlube, says the wastewater company’s operations director, who adds that the company is still deciding on a final acceptable maintenance schedule for the Vesconite Superlube application.
In addition, Vesconite Bearings’ solution resulted in the elimination of the carbon seals and the ball bearings, making the system much less complex and allowing for fewer problem areas while making the bearing system cheaper, owing to the reduction in the number of components.
The wastewater company’s operations director says that he estimates that the Vesconite Superlube solution costs two-thirds that of the replaced bearings and seals, with additional savings for the end-user, owing to reduced downtime, labour and service costs.
“The company has also indicated it is easier to do maintenance because it is simpler to replace a plain bushing than to replace the carbon seals and ball bearings that were present in the earlier design,” concludes Fourie.
Comments
Press Office
Announcements
What's On
Subscribe to improve your user experience...
Option 1 (equivalent of R125 a month):
Receive a weekly copy of Creamer Media's Engineering News & Mining Weekly magazine
(print copy for those in South Africa and e-magazine for those outside of South Africa)
Receive daily email newsletters
Access to full search results
Access archive of magazine back copies
Access to Projects in Progress
Access to ONE Research Report of your choice in PDF format
Option 2 (equivalent of R375 a month):
All benefits from Option 1
PLUS
Access to Creamer Media's Research Channel Africa for ALL Research Reports, in PDF format, on various industrial and mining sectors
including Electricity; Water; Energy Transition; Hydrogen; Roads, Rail and Ports; Coal; Gold; Platinum; Battery Metals; etc.
Already a subscriber?
Forgotten your password?
Receive weekly copy of Creamer Media's Engineering News & Mining Weekly magazine (print copy for those in South Africa and e-magazine for those outside of South Africa)
➕
Recieve daily email newsletters
➕
Access to full search results
➕
Access archive of magazine back copies
➕
Access to Projects in Progress
➕
Access to ONE Research Report of your choice in PDF format
RESEARCH CHANNEL AFRICA
R4500 (equivalent of R375 a month)
SUBSCRIBEAll benefits from Option 1
➕
Access to Creamer Media's Research Channel Africa for ALL Research Reports on various industrial and mining sectors, in PDF format, including on:
Electricity
➕
Water
➕
Energy Transition
➕
Hydrogen
➕
Roads, Rail and Ports
➕
Coal
➕
Gold
➕
Platinum
➕
Battery Metals
➕
etc.
Receive all benefits from Option 1 or Option 2 delivered to numerous people at your company
➕
Multiple User names and Passwords for simultaneous log-ins
➕
Intranet integration access to all in your organisation