Orica expands its fragmentation monitoring solution with FRAGTrack™ Crusher
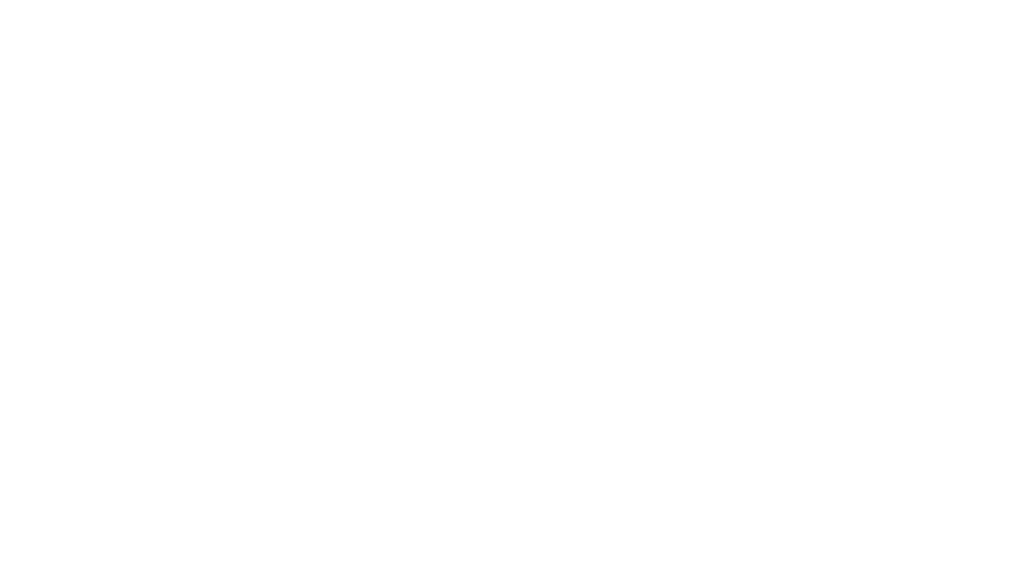
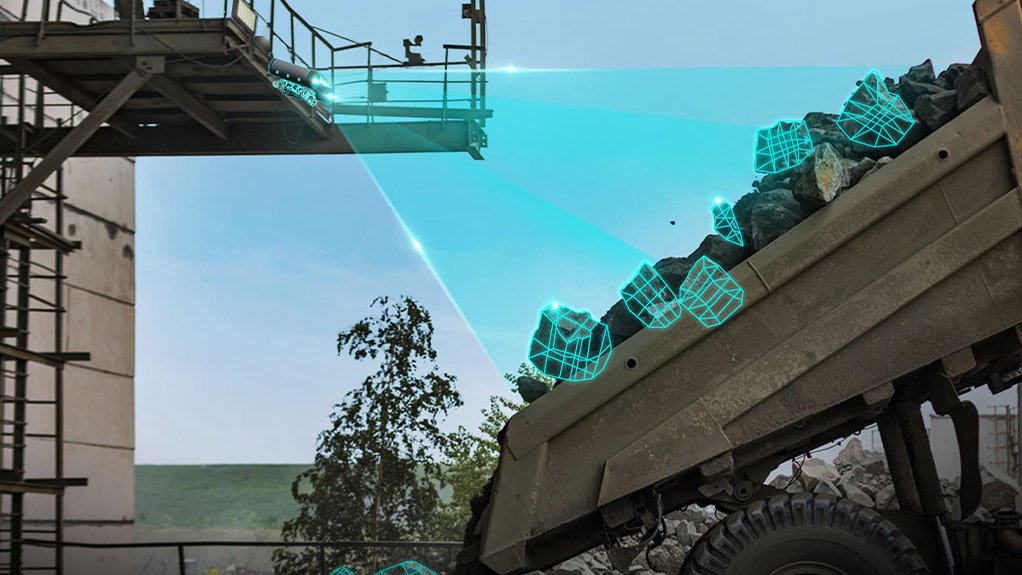
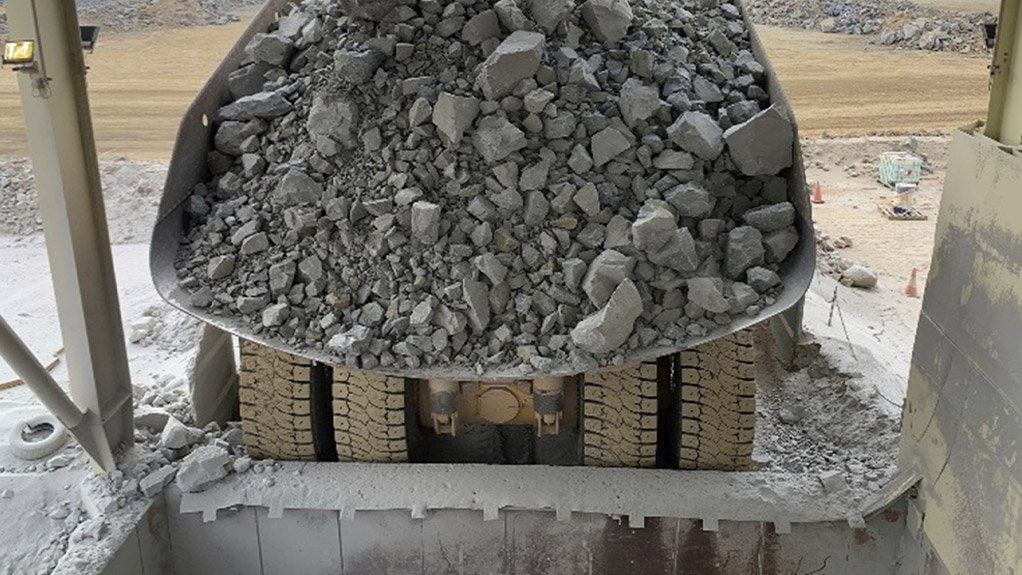
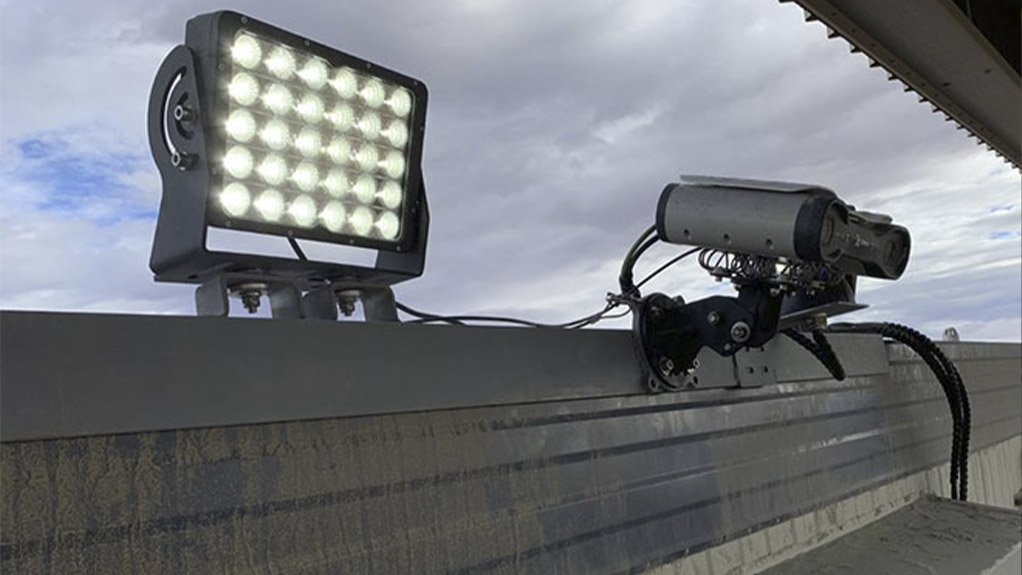
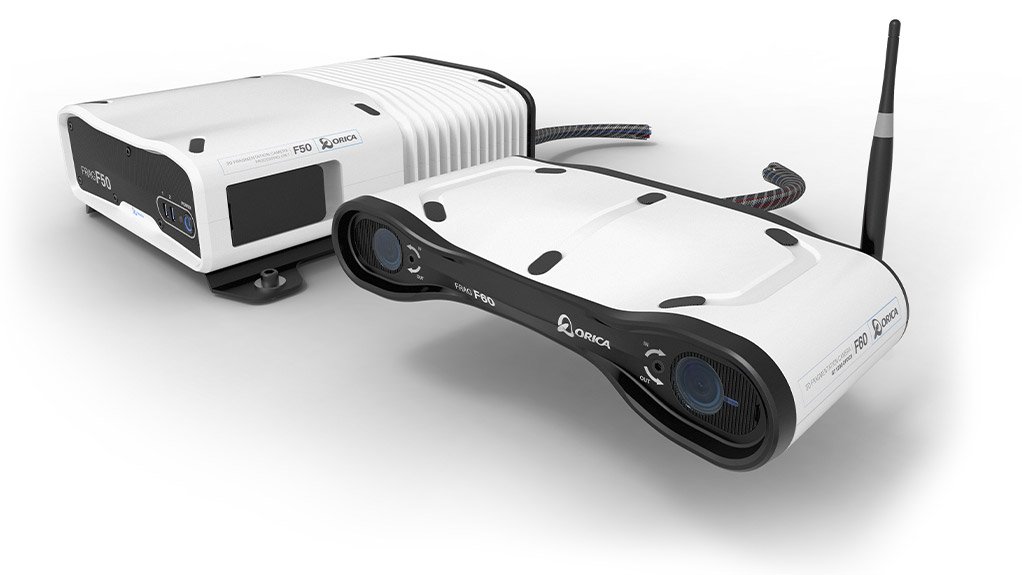
The FRAGTrack™ Crusher mounted installation (Visualisation)
FRAGTrack™ Crusher camera view. Measurements are captured and processed in real-time during the tipping operation
FRAGTrack™ Crusher installation
The Orica FRAGTrack™ system
This article has been supplied.
Orica (ASX: ORI), today announced the release of its latest fragmentation monitoring solution enabled by FRAGTrack™ Crusher, an automated pre-crusher fragmentation measurement tool delivering operational continuity in a safe and reliable way.
Based on the success of the existing suite of automated post-blast fragmentation monitoring solutions, Orica has developed FRAGTrack™ Crusher to meet growing demand from customers for downstream monitoring and optimisation solutions at every stage of the mining value chain. The technology leverages the latest deep neural network artificial intelligence (AI) framework along with the industry-proven hybrid 2D and 3D particle size distribution (PSD) processing methods to deliver a fully autonomous adaptive fragmentation monitoring solution at the crusher dump pocket, enabling customers to measure material on the truck during the tipping operations.
FRAGTrack™ Crusher provides truck by truck PSD analysis of rock fragments during the dumping operation with unmatched accuracy and without impacting operations or productivity. The technology delivers constant performance tracking for both the drill and blast operations and the downstream processing functions, driving continuous improvements end-to-end in the mining value chain. When bundled with Orica’s FRAGTrack™ Conveyor technology in a fragmentation monitoring solution, it enables further analysis of the crusher’s performance and the impact of blasting parameters in a production workflow in real-time.
Orica Vice President - Digital Solutions, Raj Mathiravedu, said: ”The full adoption of AI technology into our architecture, coupled with our strategic partnership with Microsoft, allows us to expedite the delivery of capabilities that were not previously possible, and FRAGTrack™ Crusher is an example of how we leverage AI to help deliver intelligence and value to our customers.”
PSD data is provided via a real-time application programming interface (API) and industrial open platform communication unified architecture (OPC UA) protocol to drill and blast software and crusher distributed control systems (DCS), allowing seamless integration into the existing site operation workflows.
FRAGTrack™ Crusher has already been gaining traction globally in the mining and quarry markets, where it is being utilised as a critical enabler of blasting optimisation and mine to mill initiatives. This signals a significant transformation from the subjective nature of existing manual PSD analysis methods while eliminating the safety concerns of on-bench photography and the extensive time required to manually process and correlate to relevant data sets, including fleet management data to determine the material’s blast of origin.
In the most recent application of FRAGTrack™ Crusher in a Tier I low-cost gold operation in Western Australia, it successfully delivered an automated blasting optimisation workflow on site leveraging PSD as a primary KPI to throughput and overall mill performance. The project included installation of a FRAGTrack™ Conveyor system post crusher, allowing pre and post crusher PSD to be monitored. When combined with a fragmentation improvement process, the FRAGTrack™ solution enabled a continuous feedback loop that enabled the operation to rapidly optimise blast designs that drive overall project profitability.
Comments
Press Office
Announcements
What's On
Subscribe to improve your user experience...
Option 1 (equivalent of R125 a month):
Receive a weekly copy of Creamer Media's Engineering News & Mining Weekly magazine
(print copy for those in South Africa and e-magazine for those outside of South Africa)
Receive daily email newsletters
Access to full search results
Access archive of magazine back copies
Access to Projects in Progress
Access to ONE Research Report of your choice in PDF format
Option 2 (equivalent of R375 a month):
All benefits from Option 1
PLUS
Access to Creamer Media's Research Channel Africa for ALL Research Reports, in PDF format, on various industrial and mining sectors
including Electricity; Water; Energy Transition; Hydrogen; Roads, Rail and Ports; Coal; Gold; Platinum; Battery Metals; etc.
Already a subscriber?
Forgotten your password?
Receive weekly copy of Creamer Media's Engineering News & Mining Weekly magazine (print copy for those in South Africa and e-magazine for those outside of South Africa)
➕
Recieve daily email newsletters
➕
Access to full search results
➕
Access archive of magazine back copies
➕
Access to Projects in Progress
➕
Access to ONE Research Report of your choice in PDF format
RESEARCH CHANNEL AFRICA
R4500 (equivalent of R375 a month)
SUBSCRIBEAll benefits from Option 1
➕
Access to Creamer Media's Research Channel Africa for ALL Research Reports on various industrial and mining sectors, in PDF format, including on:
Electricity
➕
Water
➕
Energy Transition
➕
Hydrogen
➕
Roads, Rail and Ports
➕
Coal
➕
Gold
➕
Platinum
➕
Battery Metals
➕
etc.
Receive all benefits from Option 1 or Option 2 delivered to numerous people at your company
➕
Multiple User names and Passwords for simultaneous log-ins
➕
Intranet integration access to all in your organisation