PDS efficacy colliding with workforce culture
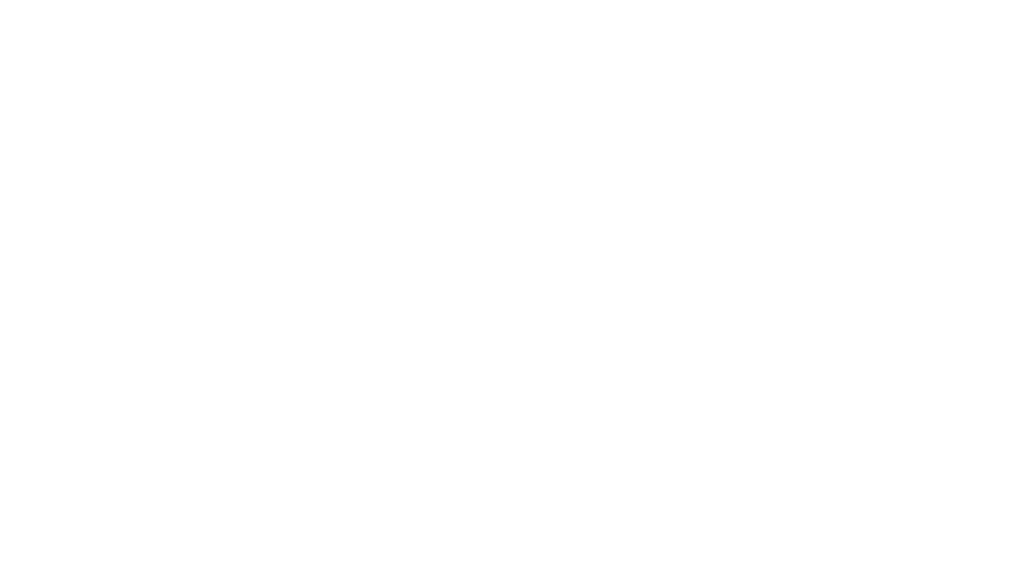
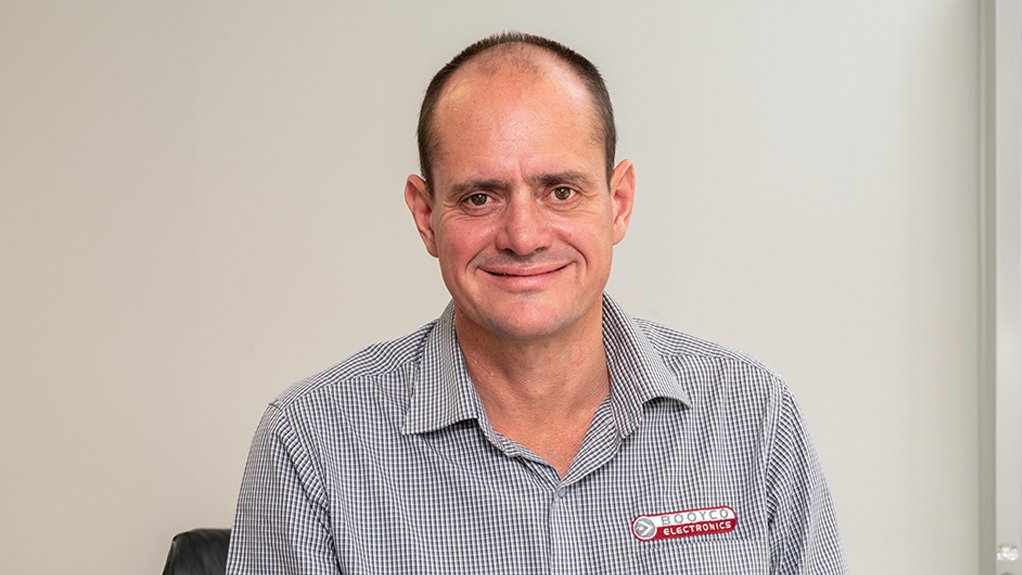
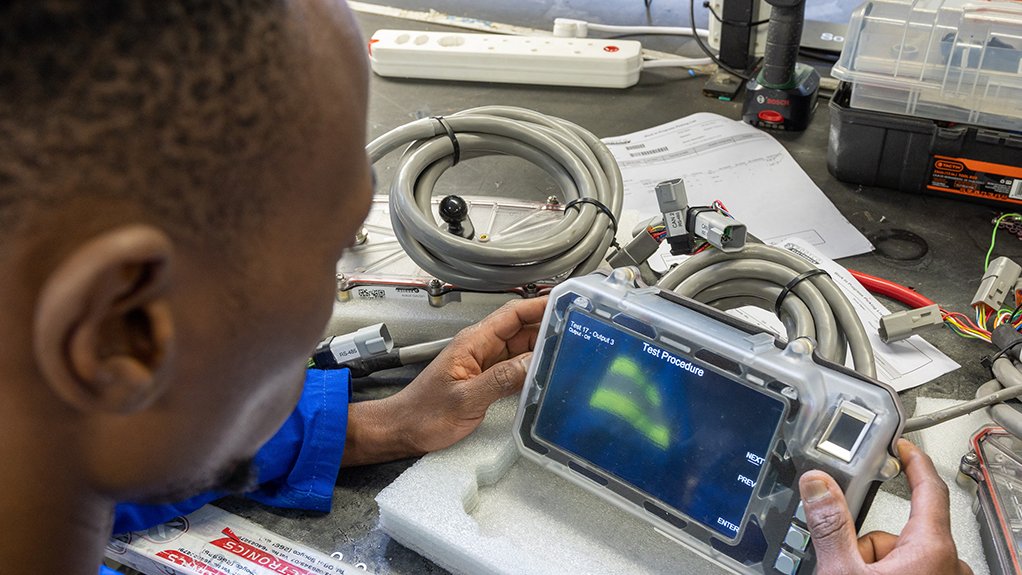
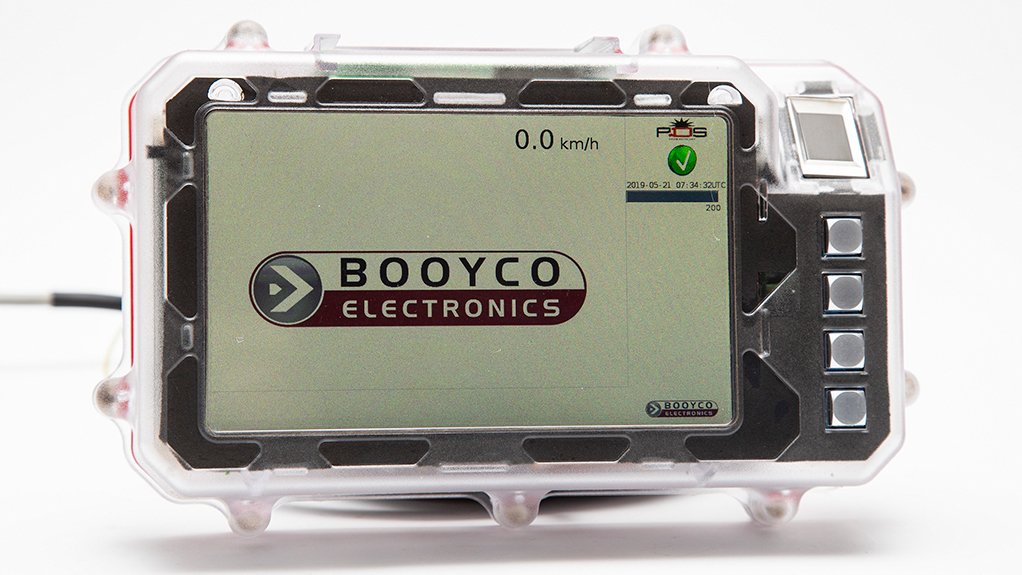
ANTON LOURENS PDS is maturing as a technology and as a solution, specifically in the South African mining space
HUMAN-CENTRED DESGIN Focusing on the human element ensures the PDS solution being implemented is not only technically sound but also practical and user-friendly
SUPPORTING SUCCESS The successful implementation of proximity detection systems in the mining sector hinges on the effective integration of the human factor
Proximity detection systems (PDS) are enablers of health and safety on mine sites but can be rendered less effective should the technology fail to be adopted outright by a mining company’s workforce, says mine safety equipment manufacturer Booyco Electronics CEO Anton Lourens.
It has been almost two years since South Africa’s Mine Health and Safety Act, No 29 of 1996, introduced a regulation that enforces the inclusion of PDS on trackless mobile machinery (TMM) to avoid accidents involving other vehicles, pedestrians and objects. Prior to December 2022, a PDS was generally considered a grudge purchase and not a means to improve safety, reduce downtime and increase productivity at underground and surface mining operations.
“There is a massive upside, but you must get people to understand this. Generally speaking, PDS is maturing as a technology and as a solution, specifically in the South African mining space,” adds Lourens.
With legislation making the inclusion of PDS on TMM mandatory, customers have matured and are progressively understanding the real value proposition of the technology, he advises.
“Nonetheless, people are always resistant to change. The ability of the radio frequency identification tags that enable workers’ and vehicles’ locations to be tracked on site is often used as an excuse to implement.”
Lourens tells Mining Weekly that workers have even gone as far as to sabotage PDS to take unscheduled breaks.
However, in one instance, where a PDS has truly been accepted and adopted at a local underground platinum mine, the data generated has been used by workers to hold others accountable when those pedestrians’ actions impact on their productivity.
These operators fully understand the technology and know when a specific individual is causing stoppages or delays on site. Similarly, that operator is aware when they are affecting other vehicles. This, ultimately, results in increased productivity. There is a better understanding that the cost of downtime when equipment has failed is a negative and, thereby, workers take greater care when operating equipment, elaborates Lourens.
Culture is Critical
Culture is always the biggest challenge faced by Booyco Electronics when implementing PDS at a new mining operation. While some customers have fostered a good company culture at their mines where workers care about equipment and their personal safety, others have a “very hostile” culture, he notes.
“Every excuse is found against the deployment of PDS, unless workers understand that the system has been implemented for their safety.”
Since the Covid-19 pandemic, Booyco Electronics’ deployment strategy has evolved to have a more people-centric approach.
“We take an inclusive approach that encompasses engagement with everyone on site, from the coalface up to the mine manager. The feedback received through collaboration with our customers during the change management process and the journey of inclusion has helped us to improve the user experience and enable a higher level of adoption and acceptance,” explains Lourens.
By ensuring that everyone understands the value-add of PDS adoption, as well as its capabilities and limitations, Booyco Electronics also shapes and manages expectations to avoid misconceptions.
This approach includes taking new customers to visit one of the numerous sites where Booyco Electronics has already deployed PDS.
Informed Decision-making
Established in 2006, the company has multiple deployments across various mineral types and mining methods. Therefore, through Booyco Electronics’ 18 years of experience, it can offer solutions that it knows have been effective at hard rock, soft rock, low seam or surface mines and plant operations, for example.
Using a baseline informed by this experience, the initial solution offered by the company generally covers 80% of a customer’s requirements.
“If one mining operation has a problem, the likelihood is that a similar mine has the same problem. Therefore, we are open to feedback, positive or negative, as it enables continuous improvement and the development of a more mature and effective solution as we go forward,” elaborates Lourens.
The initial solution recommended by Booyco Electronics is customised during the commissioning phase. The workforce is engaged on site to gain a greater understanding of the specific operation to develop a solution that is 100% aligned to the particular needs of the site.
Booyco Electronics’ PDS has been developed to include a one-size-fits-all hardware platform that offers software customisation that is compatible with a mine’s preferred original-equipment manufacturer, as well as vehicle type and size.
“We try and achieve 99% of customisation through software updates and configurations, rather than different sets of hardware platforms,” says Lourens.
While the efficacy of PDS is largely dependent on adoption by the workforce, procuring the correct technology that enables people to perform better is also vital.
“Some mining operations are choosing technology without necessarily understanding its capabilities and limitations. There’s not one single technology out there that is the silver bullet. Creating a near-perfect PDS involves combining sensor technologies in a way that provides multiple and redundant sensing technology while considering the type of mining operation and the transportation methods and strategies employed,” he concludes.
Comments
Press Office
Announcements
What's On
Subscribe to improve your user experience...
Option 1 (equivalent of R125 a month):
Receive a weekly copy of Creamer Media's Engineering News & Mining Weekly magazine
(print copy for those in South Africa and e-magazine for those outside of South Africa)
Receive daily email newsletters
Access to full search results
Access archive of magazine back copies
Access to Projects in Progress
Access to ONE Research Report of your choice in PDF format
Option 2 (equivalent of R375 a month):
All benefits from Option 1
PLUS
Access to Creamer Media's Research Channel Africa for ALL Research Reports, in PDF format, on various industrial and mining sectors
including Electricity; Water; Energy Transition; Hydrogen; Roads, Rail and Ports; Coal; Gold; Platinum; Battery Metals; etc.
Already a subscriber?
Forgotten your password?
Receive weekly copy of Creamer Media's Engineering News & Mining Weekly magazine (print copy for those in South Africa and e-magazine for those outside of South Africa)
➕
Recieve daily email newsletters
➕
Access to full search results
➕
Access archive of magazine back copies
➕
Access to Projects in Progress
➕
Access to ONE Research Report of your choice in PDF format
RESEARCH CHANNEL AFRICA
R4500 (equivalent of R375 a month)
SUBSCRIBEAll benefits from Option 1
➕
Access to Creamer Media's Research Channel Africa for ALL Research Reports on various industrial and mining sectors, in PDF format, including on:
Electricity
➕
Water
➕
Energy Transition
➕
Hydrogen
➕
Roads, Rail and Ports
➕
Coal
➕
Gold
➕
Platinum
➕
Battery Metals
➕
etc.
Receive all benefits from Option 1 or Option 2 delivered to numerous people at your company
➕
Multiple User names and Passwords for simultaneous log-ins
➕
Intranet integration access to all in your organisation