Pneumatic robot welding-gun solution a solid seller
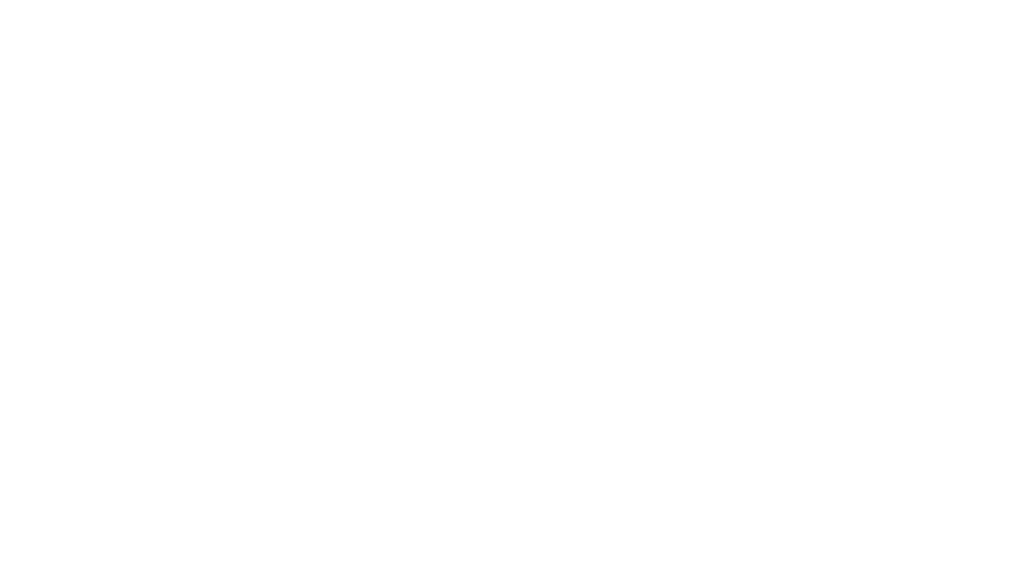
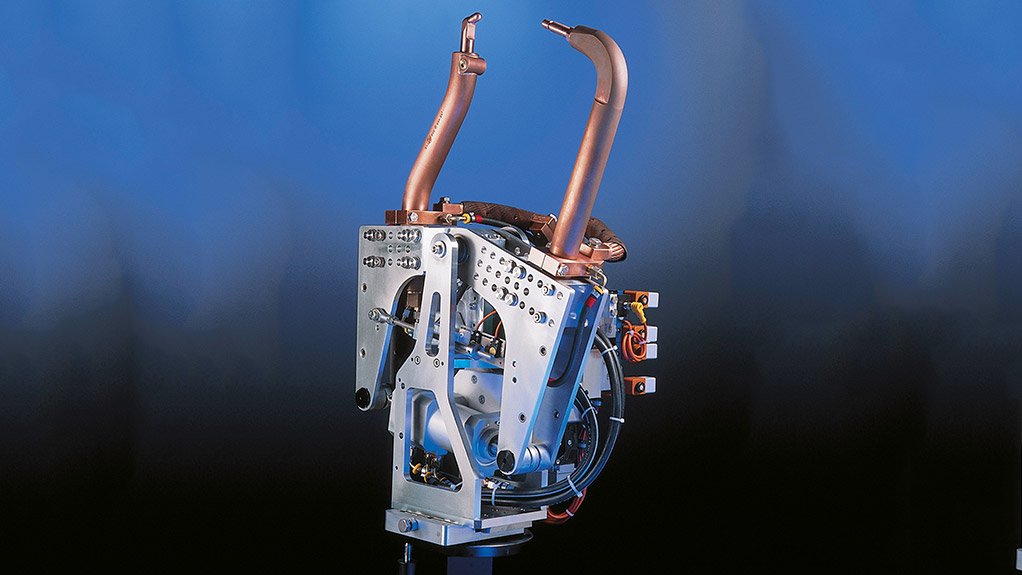
SERVO-PNEUMATIC SOLUTION Festo's Servo-Pneumatic system controls the welding gun mounted on a welding robot
Pneumatic and electric automation solutions provider Festo has sold about 450 Servo-Pneumatic robot welding-gun solution systems in South Africa since the product was launched in February 2012, Festo automotive industry head Charles Hulme tells Engineering News.
“The first local use of the Servo-Pneumatic system was at vehicle manufacturer BMW South Africa’s Rosslyn plant, in Pretoria, in February 2012, on BMW’s new F30 3-Series line,” he states, adding that it was also the first time that the customised Servo-Pneumatic control technology was used on robotic welding systems in South Africa.
He explains that Festo’s Servo-Pneumatic system controls the welding gun mounted on a welding robot.
“The product has also had international success, as Festo has, to date, sold about 9 000 units to carmakers and automotive component producers, such as BMW, Volkswagen, MA Automotive and Linde + Wiemann,” Hulme points out.
Hulme says the requirements for customised welding-gun control solutions are constantly increasing.
“It is not just the quality of spot welds that play an important role. Equally important is the flexibility and speed of the welding gun. Festo has developed the Servo-Pneumatic drive and controller system to meet these specific customer requirements,” he states.
He adds that the Servo- Pneumatic system offers more than precision control and regulation of welding guns. “Each spot weld from the welding gun, can be set to an individual force and the opening gap of the welding arms can be controlled proportionally. The freely programmable opening width means that the welding gun no longer has to be fully opened when moving around disruptive edges.”
Hulme notes that the opening width of the welding arm can be freely programmed using the Servo-Pneumatic cylinder and that the pressure level in the compensation cylinder can be adapted depending on the welding gun’s position.
Further, he highlights that Festo developed a controller software program specifically for the Servo-Pneumatic welding guns.
“The ability to control the welding force results in a significant improvement in the quality of the spot welds. The commissioning software is required during initial startup in the welding-gun workshop to calibrate the gun. The software ceases to be required once the welding gun is attached to the robot arm. All application data, such as electrode position, welding force and compensating pressure, are controlled by the higher-level controller by fieldbus communication,” he notes.
He adds that the controller can monitor the welding process through the feedback of the current sensor values.
“Different interface capabilities also facilitate high levels of communication flexibility. Communication can take place through various bus systems such as Interbus, Profibus and Profinet. A computer can also be connected through a serial interface with the system,” Hulme points out.
He notes that better control means the welding gun is not subjected to the rebound impact of the electrodes, which, therefore, results in noise reduction in the factory, better quality workmanship and less breakdowns, thereby ensuring improved production volumes and no lead time.
Comments
Press Office
Announcements
What's On
Subscribe to improve your user experience...
Option 1 (equivalent of R125 a month):
Receive a weekly copy of Creamer Media's Engineering News & Mining Weekly magazine
(print copy for those in South Africa and e-magazine for those outside of South Africa)
Receive daily email newsletters
Access to full search results
Access archive of magazine back copies
Access to Projects in Progress
Access to ONE Research Report of your choice in PDF format
Option 2 (equivalent of R375 a month):
All benefits from Option 1
PLUS
Access to Creamer Media's Research Channel Africa for ALL Research Reports, in PDF format, on various industrial and mining sectors
including Electricity; Water; Energy Transition; Hydrogen; Roads, Rail and Ports; Coal; Gold; Platinum; Battery Metals; etc.
Already a subscriber?
Forgotten your password?
Receive weekly copy of Creamer Media's Engineering News & Mining Weekly magazine (print copy for those in South Africa and e-magazine for those outside of South Africa)
➕
Recieve daily email newsletters
➕
Access to full search results
➕
Access archive of magazine back copies
➕
Access to Projects in Progress
➕
Access to ONE Research Report of your choice in PDF format
RESEARCH CHANNEL AFRICA
R4500 (equivalent of R375 a month)
SUBSCRIBEAll benefits from Option 1
➕
Access to Creamer Media's Research Channel Africa for ALL Research Reports on various industrial and mining sectors, in PDF format, including on:
Electricity
➕
Water
➕
Energy Transition
➕
Hydrogen
➕
Roads, Rail and Ports
➕
Coal
➕
Gold
➕
Platinum
➕
Battery Metals
➕
etc.
Receive all benefits from Option 1 or Option 2 delivered to numerous people at your company
➕
Multiple User names and Passwords for simultaneous log-ins
➕
Intranet integration access to all in your organisation