Predictive maintenance can be deployed cost-effectively in manufacturing
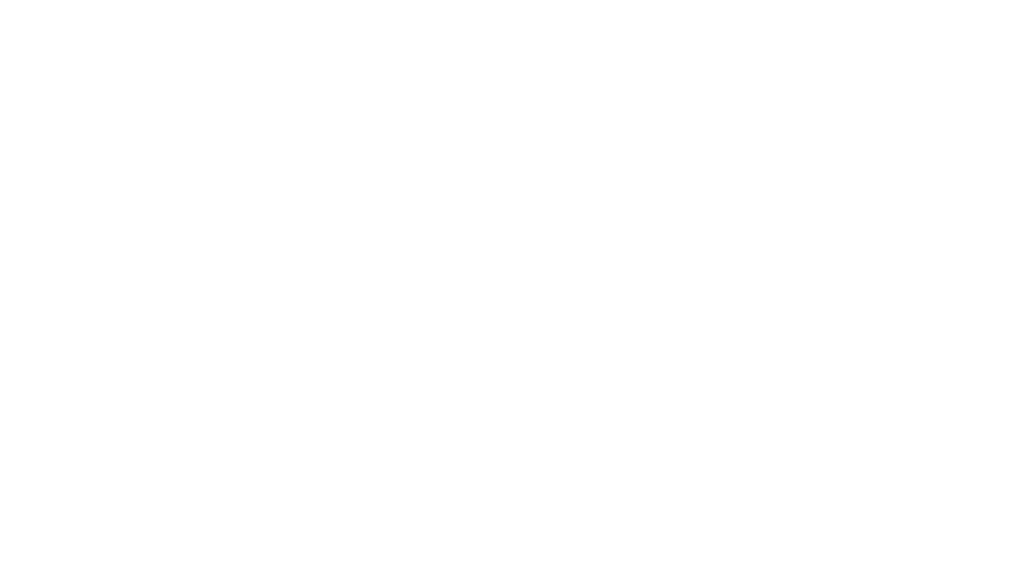
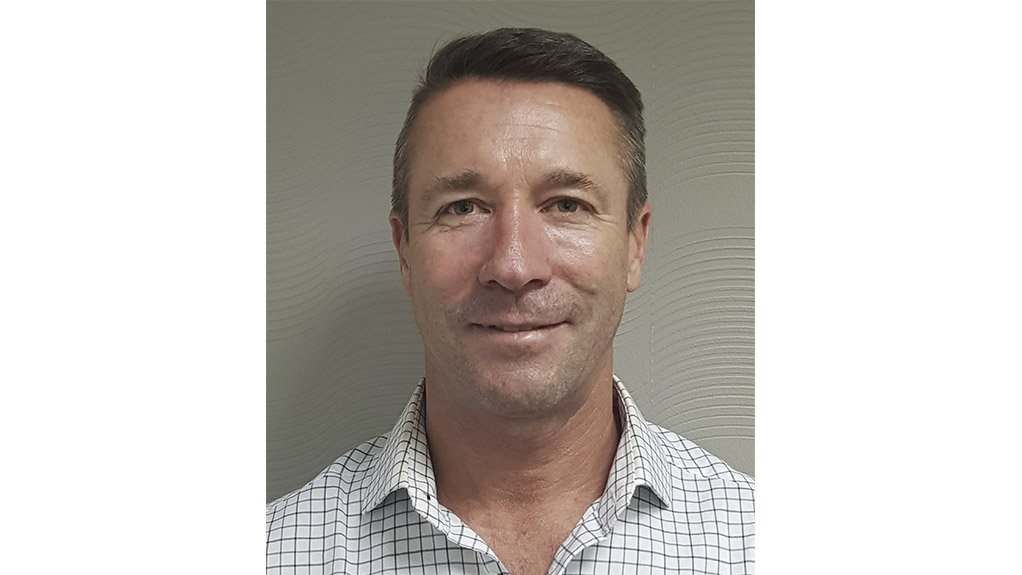
SIMON SHAW Digital twins allow companies to model process and equipment changes and thereby contribute to their business strategy
While it is often more expensive and difficult to implement predictive maintenance regimes in existing legacy factories, there are ways that manufacturing operations can introduce cost-effective predictive maintenance, says information technology multinational Wipro South Africa business development manager Simon Shaw.
“Identifying critical components and the associated cost of failure, including the impact on production processes, provides a baseline to calculate the return on investment of predictive maintenance. Not every piece of equipment needs to be monitored and understanding where the main losses or most significant halts to processes are underpins predictive maintenance,” he says.
Predictive maintenance is typically more cost effective than routine, corrective or preventive maintenance, but requires constant monitoring and data flows to drive analytical models to detect anomalies that would indicate the need for maintenance and prevent equipment breakdowns.
Additionally, these monitoring and analysis systems can also indicate when equipment starts to deteriorate, which may have implications for manufacturing processes and/or quality, as well as costs and downtime.
A commonly used architecture of predictive maintenance systems is to have equipment and process data sent to a cloud-hosted analytics platform. This is due to the significant amounts of data that is collected while the efficiency of analytics models is improved by having ready access to the data streams.
“However, companies can still opt to use home-grown solutions, including systems hosted on-premise.”
Wipro provides clients with a fit-for-purpose version of its Holmes smart, machine-learning system to enable them to implement predictive maintenance systems quickly in their manufacturing operations, says Shaw.
“Modern machinery in manufacturing operations generate significant amounts of data that can be analysed. More information and data outputs lead to more accurate predictions. Further, analytics platforms can also prepare a manufacturer to adopt other modern technologies, such as virtual and augmented reality systems.”
He highlights the rise of digital twins in manufacturing, which are virtual models of physical systems that are based on data generated by the physical equipment and which are used to improve predictions, fault, anomaly or error detection.
Digital twins allow companies to model process and equipment changes, outages, downtime and disruptions to assess their impacts, determine bottlenecks or critical elements and, thereby, contribute to their business strategy.
Additionally, as manufacturing operations become more automated, predictive maintenance becomes key, adds Shaw.
Machine learning systems can compare equipment and whole process flows against various performance parameters. They are required to ensure that notifications do not depend on people reacting by ensuring that action can be taken as quickly as possible, and to ensure that the equipment is run at peak performance as much as possible.
Shaw advises that predictive maintenance, machine learning systems and the triggers for alerts be designed on the basis of the policies and processes required to meet quality and safety standards.
Greater automation of industrial operations, which is one of the hallmarks of modern industry, including manufacturing, will reduce the work required for the normal operations of industrial facilities, and enable engineers and managers to focus on the more strategic needs of their facilities and businesses.
“Minimising mundane tasks, including a reduction in corrective and preventive maintenance, will give specialists more scope to focus on safety, quality and the future of their operations,” he concludes.
Comments
Press Office
Announcements
What's On
Subscribe to improve your user experience...
Option 1 (equivalent of R125 a month):
Receive a weekly copy of Creamer Media's Engineering News & Mining Weekly magazine
(print copy for those in South Africa and e-magazine for those outside of South Africa)
Receive daily email newsletters
Access to full search results
Access archive of magazine back copies
Access to Projects in Progress
Access to ONE Research Report of your choice in PDF format
Option 2 (equivalent of R375 a month):
All benefits from Option 1
PLUS
Access to Creamer Media's Research Channel Africa for ALL Research Reports, in PDF format, on various industrial and mining sectors
including Electricity; Water; Energy Transition; Hydrogen; Roads, Rail and Ports; Coal; Gold; Platinum; Battery Metals; etc.
Already a subscriber?
Forgotten your password?
Receive weekly copy of Creamer Media's Engineering News & Mining Weekly magazine (print copy for those in South Africa and e-magazine for those outside of South Africa)
➕
Recieve daily email newsletters
➕
Access to full search results
➕
Access archive of magazine back copies
➕
Access to Projects in Progress
➕
Access to ONE Research Report of your choice in PDF format
RESEARCH CHANNEL AFRICA
R4500 (equivalent of R375 a month)
SUBSCRIBEAll benefits from Option 1
➕
Access to Creamer Media's Research Channel Africa for ALL Research Reports on various industrial and mining sectors, in PDF format, including on:
Electricity
➕
Water
➕
Energy Transition
➕
Hydrogen
➕
Roads, Rail and Ports
➕
Coal
➕
Gold
➕
Platinum
➕
Battery Metals
➕
etc.
Receive all benefits from Option 1 or Option 2 delivered to numerous people at your company
➕
Multiple User names and Passwords for simultaneous log-ins
➕
Intranet integration access to all in your organisation