Pump reuse key for circular economy
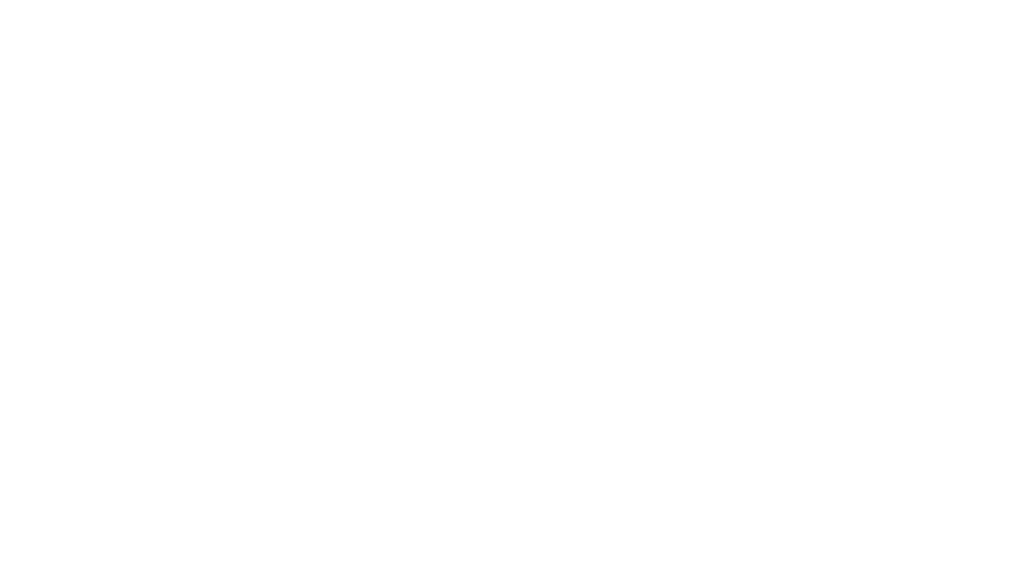
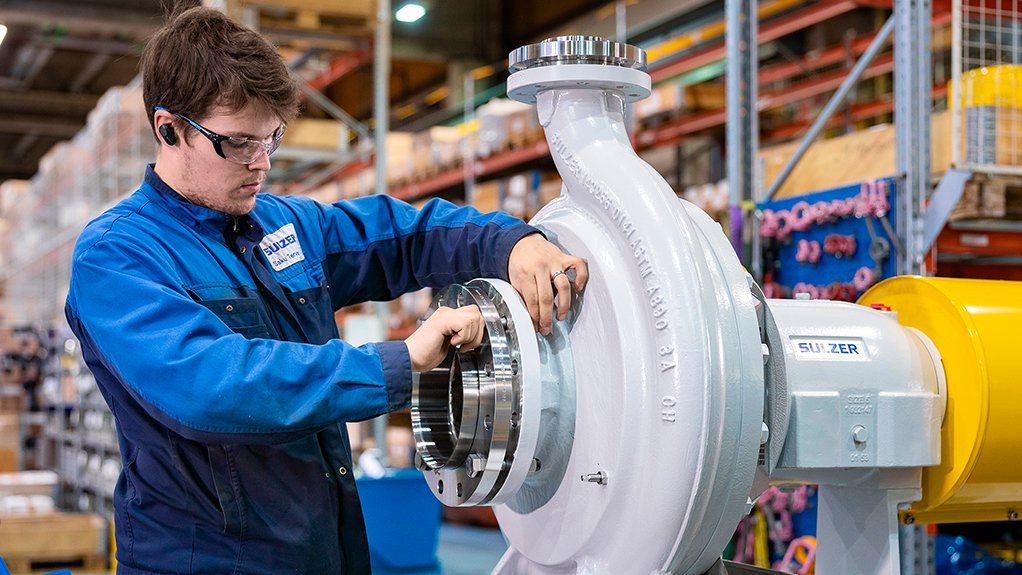
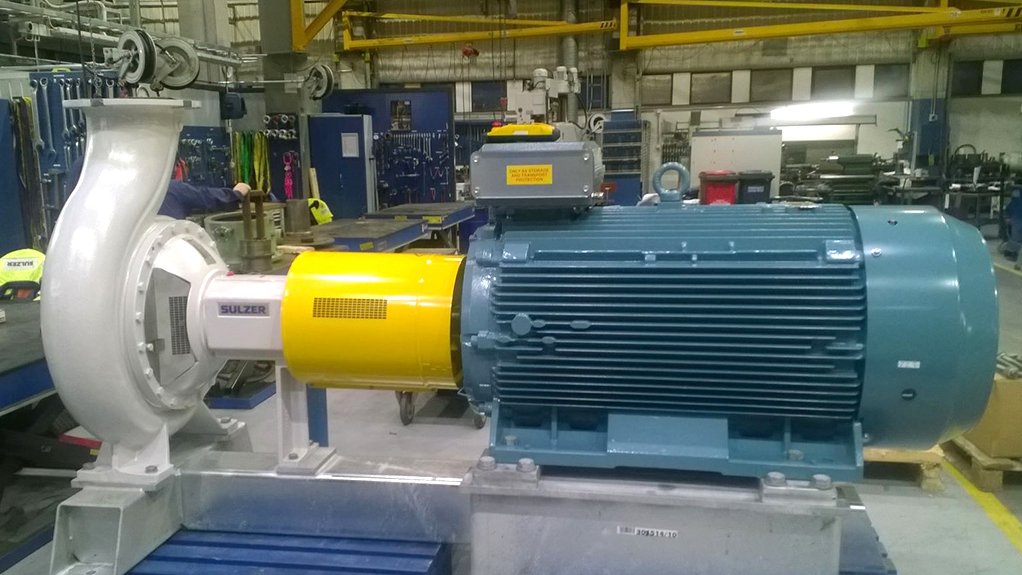
SUSTAINABILITY MATTERS 95% of Sulzer’s pumps are serviceable by design and 95% of the materials used in the pumps are recyclable
ON PURPOSE With repurposed pumps, new customers effectively get a perfect quality pump with a very short lead-time, saving time and money for their project
Pump manufacturers require a large amount of raw materials to create their products and, as such, they have a responsibility to assist the circular economy by recovering, reusing and recycling pumps as far as possible.
Fluid engineering specialist Sulzer has a long history of supporting renewable power generation, plastic recycling and sustainable practices as a whole in all its operations – in manufacturing and spare parts and services centres.
“We have also been operating a program that helps operators to improve their sustainability and reduce investment costs by matching unneeded or idle pumps, agitators and high-speed compressors with new applications. “Our technology is helping to recycle clothing, create bioplastics and renewable fuels, as well as repurposing a large number of our pumps. About 95% of Sulzer’s pumps are serviceable by design and 95% of the materials used in our pumps are recyclable,” says Sulzer business development customer support services head Pekka Salmi.
During the last recession, management within Sulzer set aside a budget to buy back some pre-owned process pumps from businesses that no longer needed them or had ceased their operation.
To facilitate a seamless process, the sales, procurement, operations and financial departments joined forces to locate second-hand pumps, purchase them and then find a new purpose for them.
Once a new customer is found, they are taken out of storage, refurbished and sold in as-new condition with a standard one-year guarantee.
The company notes that the process is beneficial for all parties, with the previous owners having now realised some value from an asset that was unused, even if it was a brand-new spare pump.
For Sulzer, it has acquired a pump that it can easily repurpose and refurbish, owing to its extensive in-house pump knowledge and expertise, while the new customer effectively gets a perfect quality pump with a short lead-time, saving time and money for their project.
These pumps can come from several sources. It may be that a plant has changed a process and a number of pumps are no longer required. Some will come from the production line, others may be brand-new spares.
In other cases, upgrading projects may have been put on hold or cancelled after the new process pumps have been delivered. Based on the condition of the pumps, Sulzer will make an offer for these pieces of equipment and work to give it a new lease on life.
Since the scheme was established, Sulzer has recovered pumps from plants that are closing, thereby offering the owners a way to recycle some of their assets rather than scrapping them.
The numbers involved are not insignificant; in one project alone, around 200 pumps have been acquired by Sulzer and they will be relocated with new operators, having been refurbished by the in-house engineering team.
This approach also has advantages for those looking to purchase pumps for their operations. The process for the customer continues to be the same as always, contacting their local sales representative with their requirements.
Sulzer’s worldwide network of pump sales personnel is well-briefed on this scheme, enabling customers to be offered a brand-new product as well as an alternative from the refurbished stock.
Some customers may need their new pump in a shortened timeframe, or the price of the recycled pump may be more appealing. For example, it has even been known for a pump to be available for shipment the day after receiving the specifications.
“Our program has proven to be very successful for all those involved; since 2010 we have supplied more than 700 units made using components that have already lived one life.
As the importance of sustainability continues to grow, manufacturers in general need to take greater responsibility for their products and what happens to them when they are no longer needed,” concludes Salmi.
Comments
Press Office
Announcements
What's On
Subscribe to improve your user experience...
Option 1 (equivalent of R125 a month):
Receive a weekly copy of Creamer Media's Engineering News & Mining Weekly magazine
(print copy for those in South Africa and e-magazine for those outside of South Africa)
Receive daily email newsletters
Access to full search results
Access archive of magazine back copies
Access to Projects in Progress
Access to ONE Research Report of your choice in PDF format
Option 2 (equivalent of R375 a month):
All benefits from Option 1
PLUS
Access to Creamer Media's Research Channel Africa for ALL Research Reports, in PDF format, on various industrial and mining sectors
including Electricity; Water; Energy Transition; Hydrogen; Roads, Rail and Ports; Coal; Gold; Platinum; Battery Metals; etc.
Already a subscriber?
Forgotten your password?
Receive weekly copy of Creamer Media's Engineering News & Mining Weekly magazine (print copy for those in South Africa and e-magazine for those outside of South Africa)
➕
Recieve daily email newsletters
➕
Access to full search results
➕
Access archive of magazine back copies
➕
Access to Projects in Progress
➕
Access to ONE Research Report of your choice in PDF format
RESEARCH CHANNEL AFRICA
R4500 (equivalent of R375 a month)
SUBSCRIBEAll benefits from Option 1
➕
Access to Creamer Media's Research Channel Africa for ALL Research Reports on various industrial and mining sectors, in PDF format, including on:
Electricity
➕
Water
➕
Energy Transition
➕
Hydrogen
➕
Roads, Rail and Ports
➕
Coal
➕
Gold
➕
Platinum
➕
Battery Metals
➕
etc.
Receive all benefits from Option 1 or Option 2 delivered to numerous people at your company
➕
Multiple User names and Passwords for simultaneous log-ins
➕
Intranet integration access to all in your organisation