Pumps range enjoys success in local market
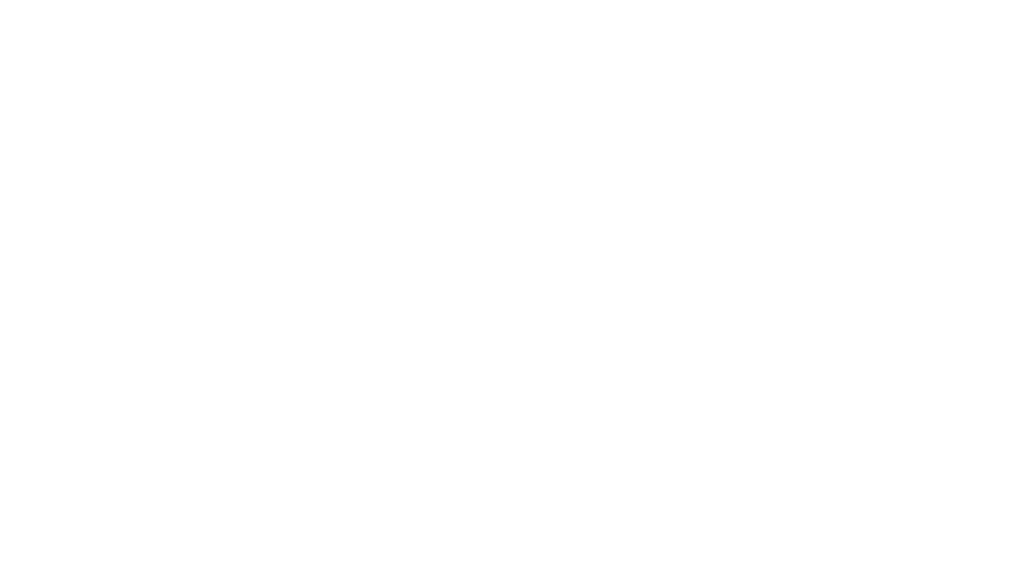
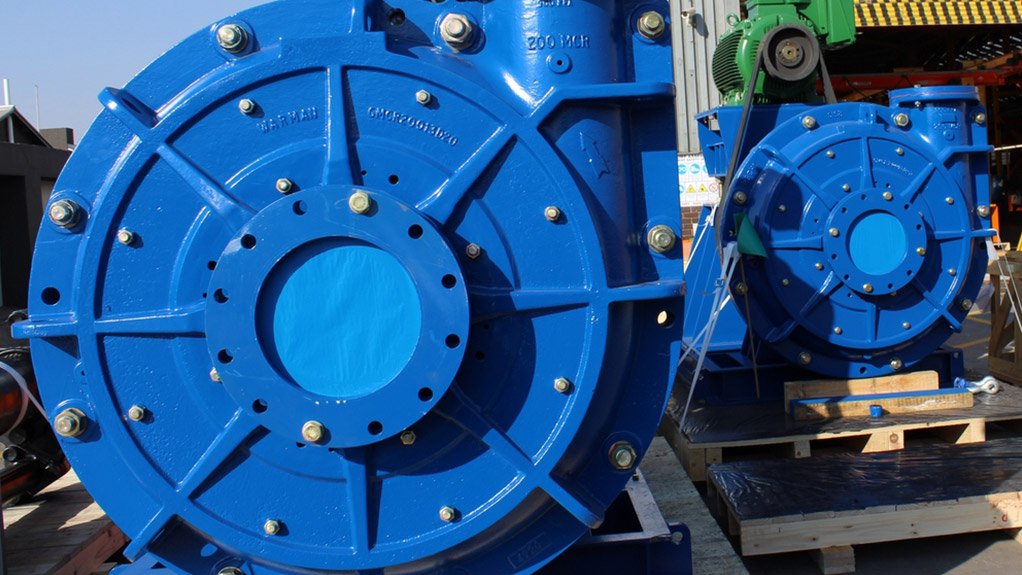
SUCCESSFUL RANGE The 200 MCR is one of six sizes of mill circuit pump that is fully manufactured in South Africa by Weir Minerals Africa
While many South African plants still run on the Warman AH series slurry pumps for highly abrasive mill duties, which are supplied by minerals sol-utions company Weir Minerals Africa, an increasing number of plant operators in other parts of Africa are recognising that the latest-generation Warman MCR rubber-lined centrifugal slurry pump offers various other advantages, states company slurry pumps products manager Rui Gomes.
Advantages of the new-generation slurry pump include superior safety and low ownership costs, as well as outstanding performance and reliability, Gomes notes.
“These pumps are recording major successes globally across a broad range of commodities and, in Africa, we are looking at a number of additional new MCR pumps going into operation this year alone – so this technology is clearly generating a substantial amount of market confidence,” he says.
The MCR pump is specifi- cally designed for mill discharge and cyclone feed duties, incorporating a number of elements that enhance performance in the most aggressive wear applications, he notes.
Features of the pump, such as impeller design, liner material, specific speed and bearing assembly, allow the pump to easily manage large-size particles in dense abrasive slurries and offer the right combination of ruggedness, durability, hydraulics and materials.
“A big advantage is the full front throat bush adjustment that aids pump efficiency and performance, and is critical to the efficient operation of the pump, while a quick-change feature allows technicians to replace the wet end of the pump on site,” Gomes says.
Further, he notes that a recent case study trialled the performance and wear life of an exist- ing Warman 14/12 AH metal pump and a competitor’s 16/14 primary mill discharge pump at a gold mine in south-western Ghana. The trial also sought to determine whether a Warman 350MCR pump could handle the mill’s tonnage, Gomes notes.
“The initial milestone of matching or improving on the 2 100 t/h, achieved by the original pumps, was quickly achieved,” Gomes says, adding that the second and more critical goal was to increase the wear life of the pumps, for which the target of 1 000 hours of operation without failure was also achieved. In addition, the impeller lasted about 1 900 hours before requiring replacement, while the R55 rubber liners continued without needing replacement, he notes.
“A number of factors drove the success of this trial. Firstly, the pump design was ideally suited to the application, compared to the pumps previously installed – notably the contribution of the MCR’s rubber lining to the substantial increase in its wear life and the consequent improved mill availability,” he says, noting that the company was astounded by the performance of the rubber liners, compared with the metal volute originally in place.
“At the four-month inspection, there was still a substantial amount of residual value on the liners and we estimate getting to about 6 000 hours – six times as long as the life of the metal volute.”
In another successful installation in the West African gold industry, a Warman 350MCR was installed to be compared with a Warman 16/14 AH metal pump. The mill was operating at flows of about 2 000 m3/h to a head of 38 m and the Weir Minerals Africa team had to install the MCR pump to fit in with existing pipework and foundations. The complete wet-end was retrofitted after about 1 400 hours, which more than doubled the life of the metal volute of the 16/14 pump, and effectively improved plant availability, Gomes notes.
“This particular site was experiencing the fairly common problem of mill balls coming through the system and cracking the metal volutes,” he says, but notes that the R55 rubber liner offered an indirect but immediate solution to this operational issue.
“The customer was also impressed by the quick and easy adjustment capability, the reduced cost of replacement spares and the improved safety levels. This MCR was installed in 2012 and we’re receiving similar feedback after 18 months of operation,” he says.
Meanwhile, a third gold mine in West Africa agreed to trial a MCR pump against its existing 14/12 AH pump. A full technical team from Weir Minerals Africa designed, supplied and fitted a retrofit base. This plant was poised to increase its tonnage to 3 000 m3/h to a head of 39 m to boost output, he points out.
“The throatbush ran for about 2 000 hours – far more than what was being achieved with the 14/12 metal throatbush,” Gomes says, noting that both the impeller and the liners were intact and are still running at the moment, after about 3 000 hours without replacement.
Further, he notes that the burgeoning interest in the Warman MCR pumps is primarily driven by the improved total cost-of-ownership being achieved, and adds that the company also experienced positive spin-offs from greenfield projects in Central Africa, Zambia and the Democratic Republic of Congo (DRC).
“Most recently, a project house, which manages a recently commissioned greenfield copper plant expansion in the DRC, opted for MCR pumps, based on the increasing number of impressive case studies being rec- orded for this particular pump,” Gomes says.
Meanwhile, he notes that, in terms of brownfield applications, tonnages and requirements change over the years, but the pumps rarely change.
“This could be detrimental if the pump becomes too big for the duty, impacting on efficiencies and pump life, or too small, affecting wear life. We’ve now proven that we’re able to retrofit MCR pumps into existing piping and foundations to achieve significant improvements with little or no downtime,” he comments, adding that the company had started to focus on a variety of commodity plants where there is pressure to drive costs down and improve processes.
He concludes that, from a manu- facturing perspective, the company has improved availability of the MCR pumps by manufacturing many of the MCR components locally over the last three years.
“This has enhanced our offering through improved lead times and route to market. We started out with three pump sizes in 2008 and we now offer six sizes, with various com-binations for each size,” he adds.
Comments
Press Office
Announcements
What's On
Subscribe to improve your user experience...
Option 1 (equivalent of R125 a month):
Receive a weekly copy of Creamer Media's Engineering News & Mining Weekly magazine
(print copy for those in South Africa and e-magazine for those outside of South Africa)
Receive daily email newsletters
Access to full search results
Access archive of magazine back copies
Access to Projects in Progress
Access to ONE Research Report of your choice in PDF format
Option 2 (equivalent of R375 a month):
All benefits from Option 1
PLUS
Access to Creamer Media's Research Channel Africa for ALL Research Reports, in PDF format, on various industrial and mining sectors
including Electricity; Water; Energy Transition; Hydrogen; Roads, Rail and Ports; Coal; Gold; Platinum; Battery Metals; etc.
Already a subscriber?
Forgotten your password?
Receive weekly copy of Creamer Media's Engineering News & Mining Weekly magazine (print copy for those in South Africa and e-magazine for those outside of South Africa)
➕
Recieve daily email newsletters
➕
Access to full search results
➕
Access archive of magazine back copies
➕
Access to Projects in Progress
➕
Access to ONE Research Report of your choice in PDF format
RESEARCH CHANNEL AFRICA
R4500 (equivalent of R375 a month)
SUBSCRIBEAll benefits from Option 1
➕
Access to Creamer Media's Research Channel Africa for ALL Research Reports on various industrial and mining sectors, in PDF format, including on:
Electricity
➕
Water
➕
Energy Transition
➕
Hydrogen
➕
Roads, Rail and Ports
➕
Coal
➕
Gold
➕
Platinum
➕
Battery Metals
➕
etc.
Receive all benefits from Option 1 or Option 2 delivered to numerous people at your company
➕
Multiple User names and Passwords for simultaneous log-ins
➕
Intranet integration access to all in your organisation