R3bn Scaw project is South Africa’s first flat-steel investment in decades
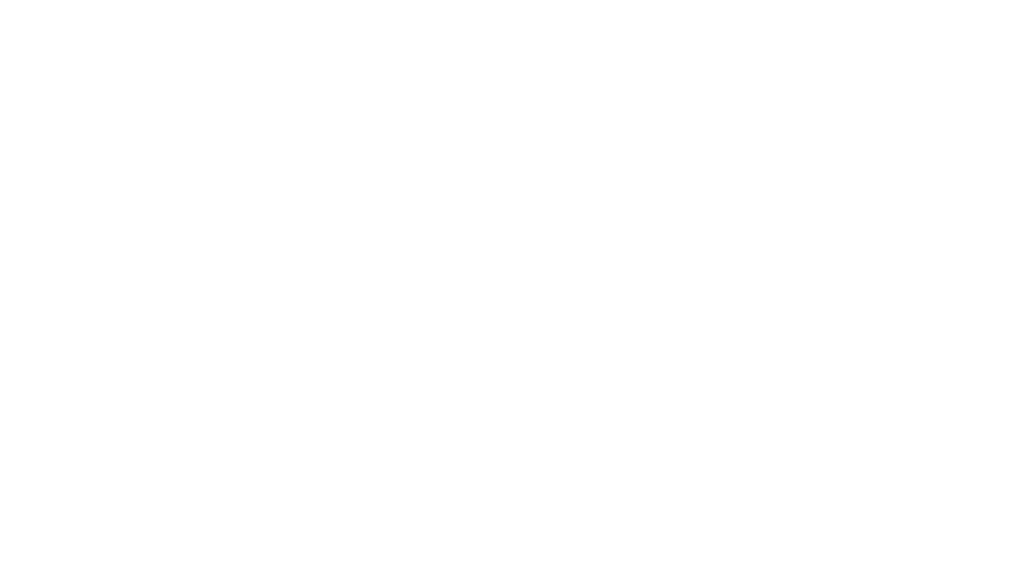
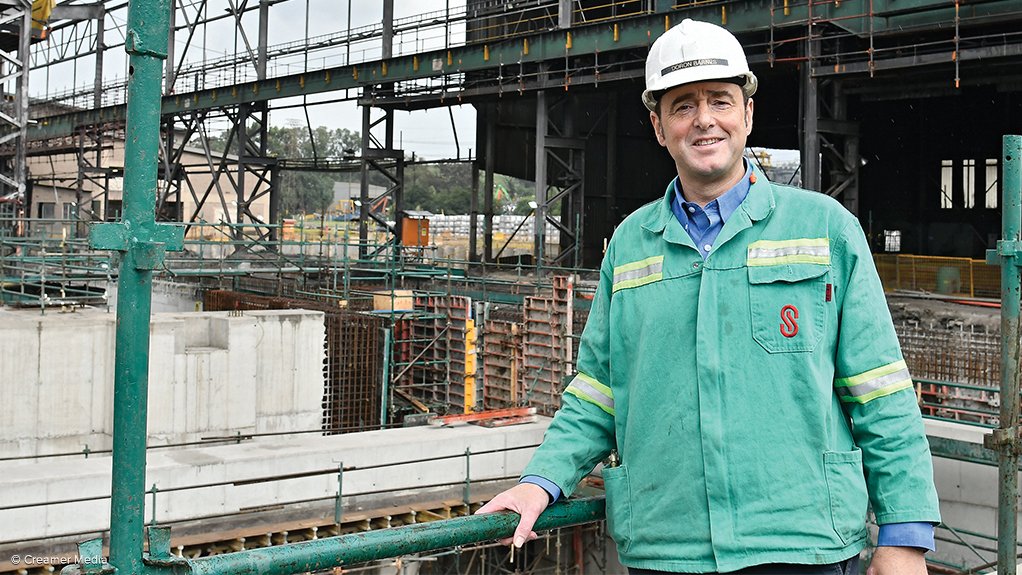
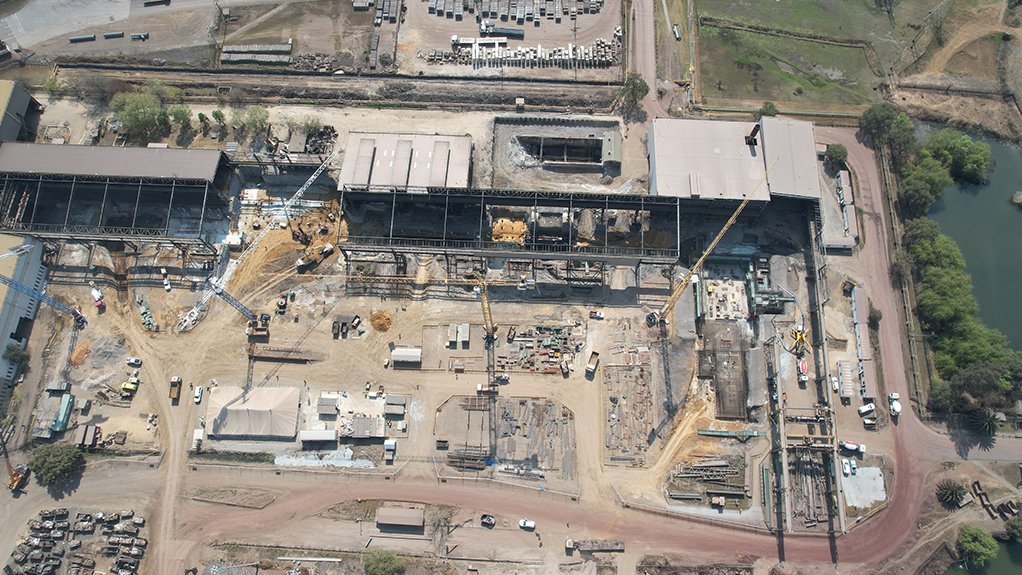
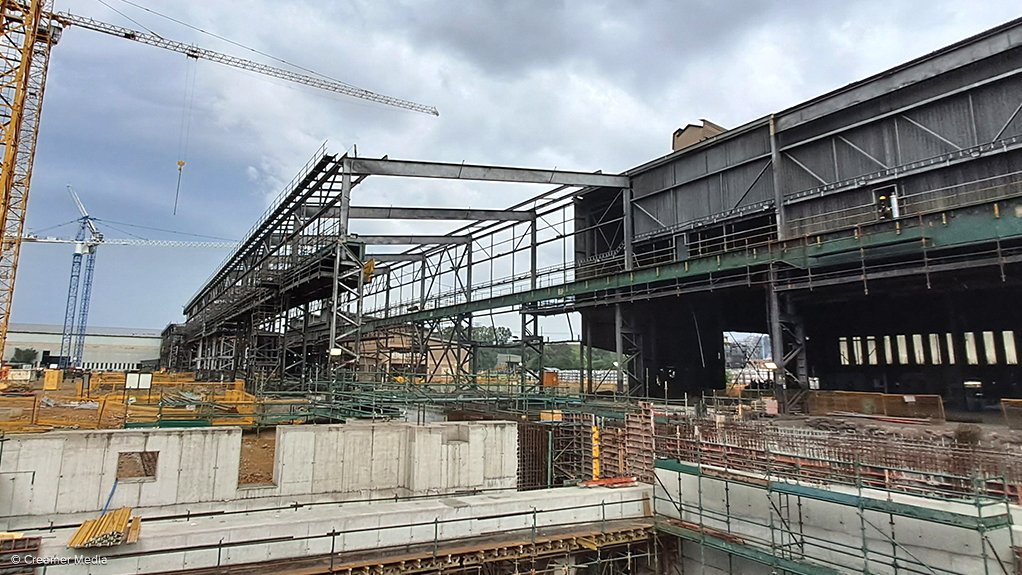
Barnes Group CEO Doron Barnes at the project construction site at Scaw Union Junction
Photo by Creamer Media's Donna Slater
Aerial view of the steel project being developed on a brownfield site in Gauteng
Tower cranes on the Union Junction site where civil works are well under way and where construction-related employment is expected to peak in 2023 at about 1 200 workers
Photo by Creamer Media's Donna Slater
Construction tower cranes have been something of a rare sight on the Germiston skyline over the past few decades as the once-thriving industrial hub has faced severe deindustrialisation headwinds.
Several such cranes have made a reappearance at Scaw Metals’ Union Junction complex in Ekurhuleni in recent months, however, in support of a R3-billion steel investment to increase Scaw’s steelmaking capacity from about 500 000 t/y to 650 000 t/y.
This seemingly modest capacity increase somewhat belies the significance of the project, which is South Africa’s first flat-steel investment since the Saldanha Steel project was initiated by then Iscor (now ArcelorMittal South Africa, or AMSA) and the Industrial Development Corporation (IDC) in the 1990s.
Barnes Group CEO Doron Barnes – whose company acquired Scaw Metals, together with its Haggie and McKinnon Chain units, in May 2018 – tells Engineering News that the investment has been informed primarily by the current domestic manufacturing imbalance between flat and long steel.
There is sufficient long-product capacity, which is reflected in the price, while AMSA is currently the only remaining producer of flat-steel products after the closure of Highveld Steel.
Scaw has hitherto produced only long-steel products, but the investment under way will position it to produce both long and flat products, with a 50/50 mix envisaged currently.
In addition, AMSA’s mothballing of the Saldanha Steel mill, in the Western Cape, has resulted in the closure of significant local capacity to produce thin-gauge hot rolled coil (HRC), on which some domestic re-rollers previously relied.
Barnes says the intention is to position Scaw Union Junction to produce both long and flat steel, using an advanced solution that is being supplied by Danieli, of Italy, which also supplied substantial portions of Scaw’s current steelmaking and rolling plant units, installed when the company was still owned by Anglo American.
Half of the investment cost is being funded from internal Barnes Group resources, with the balance arising from a club loan that has been extended, in equal portions, by Absa, Investec and the IDC, which continues to hold a 26% equity position in Scaw Metals.
Under the contract, which was signed with Danieli in August 2021, Scaw will build a new flat-steel complex on the brownfield site in Gauteng for narrow- and medium-width HRC, at gauges of between 1.2 mm and 8.0 mm.
The Barnes Group will absorb a portion of the output itself for further downstream processing at its Barnes Tubing operation in Isando and Hall Longmore operation in Wadeville, both also in Gauteng, where steel piping is manufactured. The balance will be sold into the merchant steel market or to re-rollers, which currently have no domestic flat-steel alternative to AMSA.
The contract with Danieli includes several components, including a medium-slab continuous caster and semi-continuous hot-strip mill, a reheating furnace, and a brownfield water-treatment plant.
It also involves the revamping of Scaw’s existing meltshop, which includes a new-generation electric arc furnace.
The meltshop will be fed using a combination of scrap and direct reduced iron (DRI), produced using the mill’s existing kilns onsite.
COGENERATION POTENTIAL
Scaw has three kilns to produce DRI, not all of which have been restarted, and Barnes reports that investigations are advancing, using initial Anglo concepts, into the prospect of fitting two of the kilns with cogeneration plants to produce about 60 MW.
No final investment decision has been made, but Barnes believes the project is likely to be developed in the coming two years, given South Africa’s electricity crisis and the fact that tariffs are rising steeply, which has improved the economics of cogenerated electricity.
At 60 MW, Scaw expects to be able to meet about 60% of its needs and buffer itself from Eskom’s load-curtailment requirements.
In addition, the new facility is significantly more energy efficient than existing plants in South Africa, which will help reduce how much electricity it will consume for every ton of steel produced even if Scaw’s overall power requirement stays flat.
In the meantime, priority is being given to the steel project, project managed by ECS Associates, where civil works are well under way with the Enza Construction and Trencon Construction teams on site and with construction-related employment expected to peak in 2023 at about 1 200 workers.
The project is also expected to generate a further 300 direct permanent jobs at Scaw and the Barnes Group, which already employs about 5 000 people.
Besides the market gap that Barnes believes has opened up to supply flat steel domestically, he says the investment has been supported by some other significant “tailwinds”.
The first is the price preference system (PPS) and scrap export tax that has been put in place by government to ensure domestic consumers of scrap secure material at a discount before any exports take place.
This benefit is likely to be amplified further by the recent decision to ban the export of nonferrous and ferrous scrap in an effort to dampen demand for metals and copper being stolen from public infrastructure assets.
“I realise there is some negativity about the banning of scrap exports and the PPS, but without these interventions we would struggle to access affordable material and there would be no advantage to manufacturing scrap-based steel in South Africa,” Barnes states.
He notes that various other markets, including China and, more recently, the European Union are imposing restrictions on scrap exports, with the European Parliament voting in early December to impose restrictions on scrap exports in the interest of boosting Europe’s “circular economy” and its decarbonisation efforts.
Likewise, favourable steel market conditions in recent years have enabled the Barnes Group to generate the cash resources required to support such a large capital investment.
Thirdly, a combination of technological innovation and a global trend towards local production had prompted Danieli to consider a project that would previously have been considered too small to be feasible.
The Italian original equipment manufacturer is reportedly treating the Scaw project as a benchmark for a flat products mini-mill concept, which is viewed as a potential new niche market in the steel sector.
Another advantage for Scaw is it proximity to markets, with the Gauteng province remaining by far the largest steel-consuming province in South Africa. This materially reduces the logistics-cost component for Scaw.
Barnes reports the project remains on track for the commissioning of the continuous caster by the end of 2023 and for the hot-strip mill to begin ramping up to full production by April 2024.
“We are fully committed to building a sustainable steel business, but to fulfil that ambition we have to invest, which is what we are doing,” Barnes concludes.
Comments
Press Office
Announcements
What's On
Subscribe to improve your user experience...
Option 1 (equivalent of R125 a month):
Receive a weekly copy of Creamer Media's Engineering News & Mining Weekly magazine
(print copy for those in South Africa and e-magazine for those outside of South Africa)
Receive daily email newsletters
Access to full search results
Access archive of magazine back copies
Access to Projects in Progress
Access to ONE Research Report of your choice in PDF format
Option 2 (equivalent of R375 a month):
All benefits from Option 1
PLUS
Access to Creamer Media's Research Channel Africa for ALL Research Reports, in PDF format, on various industrial and mining sectors
including Electricity; Water; Energy Transition; Hydrogen; Roads, Rail and Ports; Coal; Gold; Platinum; Battery Metals; etc.
Already a subscriber?
Forgotten your password?
Receive weekly copy of Creamer Media's Engineering News & Mining Weekly magazine (print copy for those in South Africa and e-magazine for those outside of South Africa)
➕
Recieve daily email newsletters
➕
Access to full search results
➕
Access archive of magazine back copies
➕
Access to Projects in Progress
➕
Access to ONE Research Report of your choice in PDF format
RESEARCH CHANNEL AFRICA
R4500 (equivalent of R375 a month)
SUBSCRIBEAll benefits from Option 1
➕
Access to Creamer Media's Research Channel Africa for ALL Research Reports on various industrial and mining sectors, in PDF format, including on:
Electricity
➕
Water
➕
Energy Transition
➕
Hydrogen
➕
Roads, Rail and Ports
➕
Coal
➕
Gold
➕
Platinum
➕
Battery Metals
➕
etc.
Receive all benefits from Option 1 or Option 2 delivered to numerous people at your company
➕
Multiple User names and Passwords for simultaneous log-ins
➕
Intranet integration access to all in your organisation